24v DC Motor
24v dc motor can come in various specifications. You can find a wide selection of motors on the market that can be used for varying applications that require different power delivery. The two principle types of 24v dc motor are brushless and brushed. Although they are based on the same mechanical principles, their build, performance and control ability differ substantially.
24v DC Motor Brushed vs Brushless
The below video gives a good explanation of the difference between a brushed and brushless motor. Whilst it emphasizes it use of a 24v dc motor in terms of a cordless drill the principle of the difference between the motors is largely the same for most applications.
Up until the 1980s the main dc motor was a brushed motor. Then in 1962 T. G. Wilson and P. H. Trickey published an article demonstrating a brushless motor design that operated on direct current (dc). The motors were built with technology that utilised magnetism and successively opposed by an electric device. The breakthrough underpinning the concept of the brushless motor was the ability to do away with physical switch to transmit the current.
The new technology was slow to take off and up until the 1980’s the main 24v dc motor was still a brushed motor. At was at this point though that things began to change. With the wider availability of permanent magnets together better and cheaper high-voltage transistors brushless motors started to be able to produce a equivalent power output to their brushed counterpart at similar or lower cost. Since then improvements to the brushless motor have continued which has transformed the the market place to make the brushless motors the dominant dc motor particularly in the small appliance market as it allow manufacturers to develop more efficient appliances with reduced maintenance requirements.
What are the Advantages of Each Type of 24v DC Motors?
Despite the greater efficiency and other advantages of the the brushless motor there are still advantages to be had in deploying brushed motors into your appliance / machime.
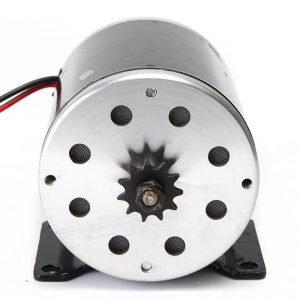
Brushed
- Low overall building costs;
- Can usually be refurbished to extend life;
- Simple and less expensive controller;
- No controller not needed for single speed motor;
- Excellent for use in extreme operating environments.
Brushless
- Less overall maintenance due to lack of brushes;
- Operates more effectively at all speeds with rated load;
- High efficiency and high output power to size ratio meaning smaller motors;
- Reduced size with far less heat produced;
- Wider speed range and less noise.
What Applications are Brushed and Brushless DC Motors Used In?
Today, the brushless 24v dc motor is used far more often then its brushed counterpart. However, both can be found in a wide range of applications.
Brushed DC motors are still used frequently in household appliances and in automobiles. They also maintain a strong industrial niche because of the ability to change the torque to speed ratio which is exclusive to brushed motors.
Because of their reliability and lifespan, the brushless 24v dc DC motor has found its way into numerous applications. It is common throughout a wide range of industries: Manufacturing, computing, and as we have seen many household appliance such as power tools. The next generation electric vehicles is also being built around brushless motors.
In an motion control project because of the enormously differing needs and environmental concerns, most projects could benefit from either motor.
Brushed vs Brushless Motors: Why the Extra Cost?
In a conventional brushed 24v dc motor, the rotor (rotating part) is driven inside of the stator (the fixed part). They are joined via an electrical connection called the collector or commutator, which is in contact with the carbon brushes.
In a brushless24v dc motor, the rotor is made up of magnets and the stator of coils that are charged alternately positive then negative. Because of this the poles attract and repel causing the motor to turn. The significance of this is that there is no actual physical contact between the rotor and stator. The energy passes from one to the other via the magnetic field created between electromagnets.
Powered by a direct current, the motor works with an alternating current produced via an electronic card that changes the direct current to three-phase variable frequency. This means that the coils are powered alternately to create a rotating field and thus generate the rotation. An electronic module is built directly into the motor or into a housing allowing it to continually regulate the current so that the motor operates with maximum efficiency. The result is an improved overall efficiency and thus reduced cost.
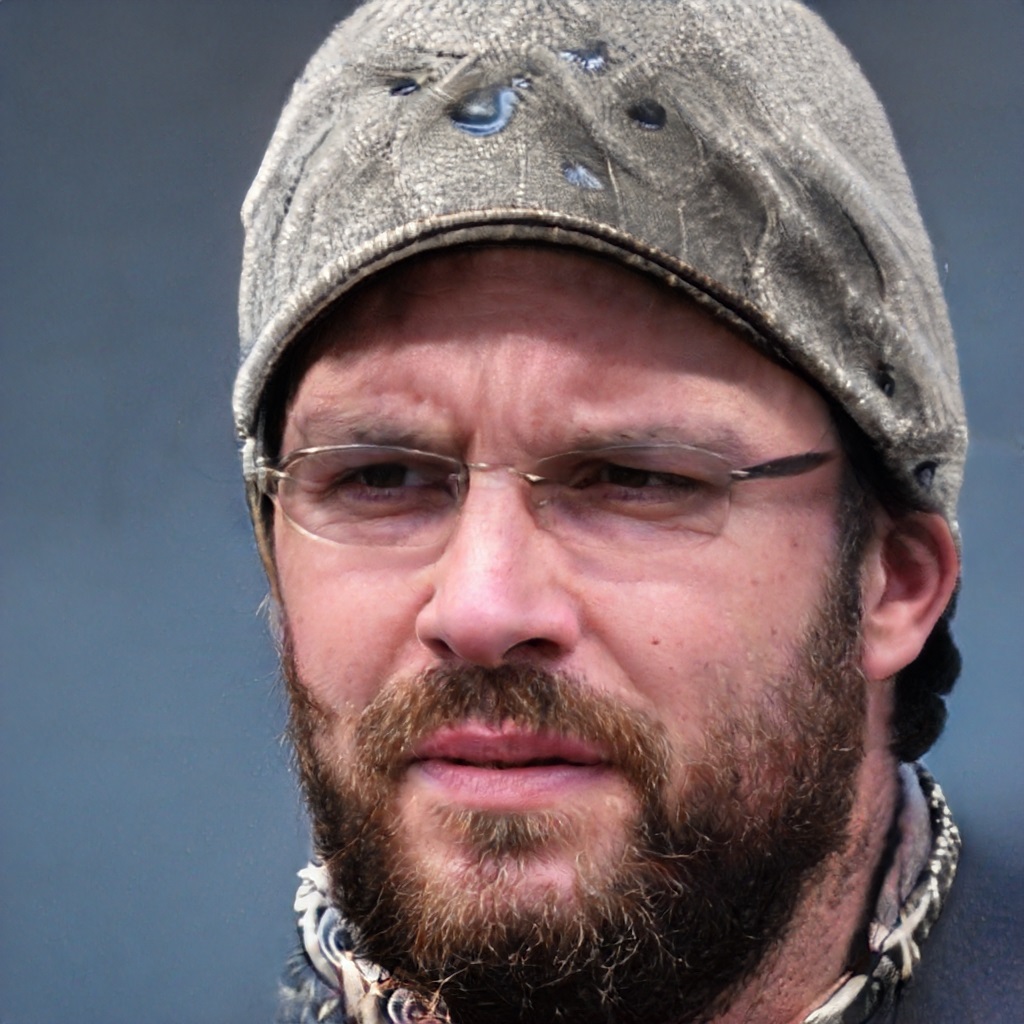
I’ve been involved in the welding industry for over twenty years. I trained in various engineering shops working on various projects from small fabrication and repairs through to industrial projects.I specialize in welding aluminum and food grade stainless steel and an now run an engineering shop fabricating equipment for the food industry.