Manual Sheet Metal Bender
Manual Sheet Metal Bender
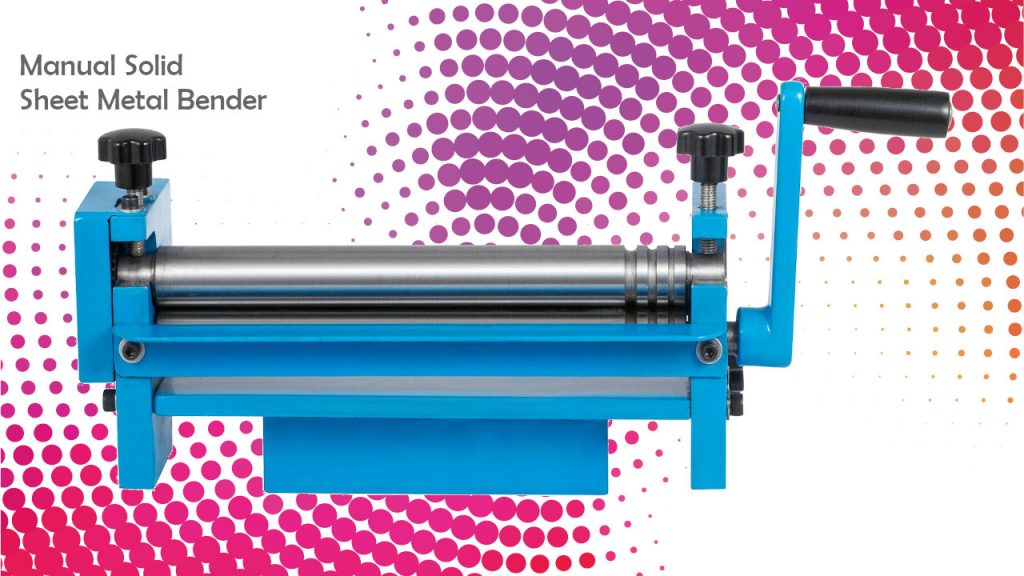
A manual sheet metal bender, also commonly known as a metal brake, is an essential and surprising versatile piece of machinery and pretty much a must for most metal shops but also incredibly useful machine to have in a home / DIY workshop.
Bending is one of the most common sheet metal fabrication operations. Also known as press braking or flanging, this method is used to transform the metal to an angular shape.
This is done through the application of force to the work-piece. The force has to be greater than the material’s yield strength to achieve a the change in shape. Only when this occurs can you get a lasting result in the form of a bend. A manual sheet metal bender makes this a fairly simple task.
The advantages of using a manual sheet metal bender
There are several things to consider when bending sheet metal. Firstly, what constitutes a good bend? A good Bend is defined by the radius of the bend, how straight it is, and if it meets the required angle.
If you were going to bend the sheet metal by hand you need to achieve a bend that’s as tight and sharp as possible, you need to look at the radius of the bend, the bend is always rounded edge of the outside of the bend with this radius being the determining factor of how tight or sharp the bend is.
Thus, your choice of clamping material (former) is critical. For example, a wood former would likely result in a poor bend. Using a manual sheet metal bender alleviates this as the former that the metal is bent around ensures crisp sharp bend.
Additional uses of a manual sheet metal bender
A manual sheet metal bender is more versatile than given credit for. As well as being able to bend metal to virtually any angle it can also be use to apply a hem (folded back upon itself to create a flat bend and can be used to cut sheet metal. This can be achieve through scoring the metal. The cuts are clean sharp and straight.
Types of Metal Bend
There’s quite a few different bending methods available. Each has their own advantages. The dilemma is usually between going for accuracy or simplicity, while the latter gets more usage. Simpler methods are more flexible and most importantly, need less different tools for getting a result.
V-Bending
V-bending is the most common bending method using a punch and die. It has three subgroups – bottoming, air bending and coining. Air bending and bottoming account for around 90% of all bending jobs.
Bottoming
Bottoming is also known as bottom pressing or bottom striking. As the name “bottom pressing” suggests, the punch presses the metal sheet onto the surface of the die, so the die’s angle determines the final angle of the workpiece. With bottoming, the inner radius of the angled sheet depends on the die’s radius.
As the inner line gets compressed, it needs more and more force to further manipulate it. Bottoming makes exerting this force possible, as the final angle is preset. The possibility to use more force lessens the springback effect and provides good precision.
Coining
Coining used to be far more widely spread. It was pretty much the only way to get accurate results. Today, machinery is so well controllable and precise, that such methods are not widely used any more.
The metal is given the die’s exact shape by applying great weight. The name coining comes from the fact that this method that when making counterfeit coins each had to be identical and thus indistinguishable from a real one. Coining, in bending, allows similarly precise results.
This is because the die penetrates into the sheet, pressing a dent into the work-piece. This, along with the high forces used (about 5-8 times as much as in partial bending), guarantee high precision. The penetrating effect also ensures a very small inside radius for the bend.
Step Bending
Whilst the above video uses an automated brake similar results can be achieved with a manual sheet metal bender.
Step bending is, in essence, repetitive V-bending. Also called bump bending, this method uses many V-bends in succession to get a large radius for your workpiece. The final quality depends on the number of bends and the step between them. The more you have them, the smoother the outcome. Step bending has many use case scenarios. For example a conical hoppers or a snow-plough shovel . It makes large radius bending possible with regular tools. The easier setup makes for a cheaper price, especially with small batches.
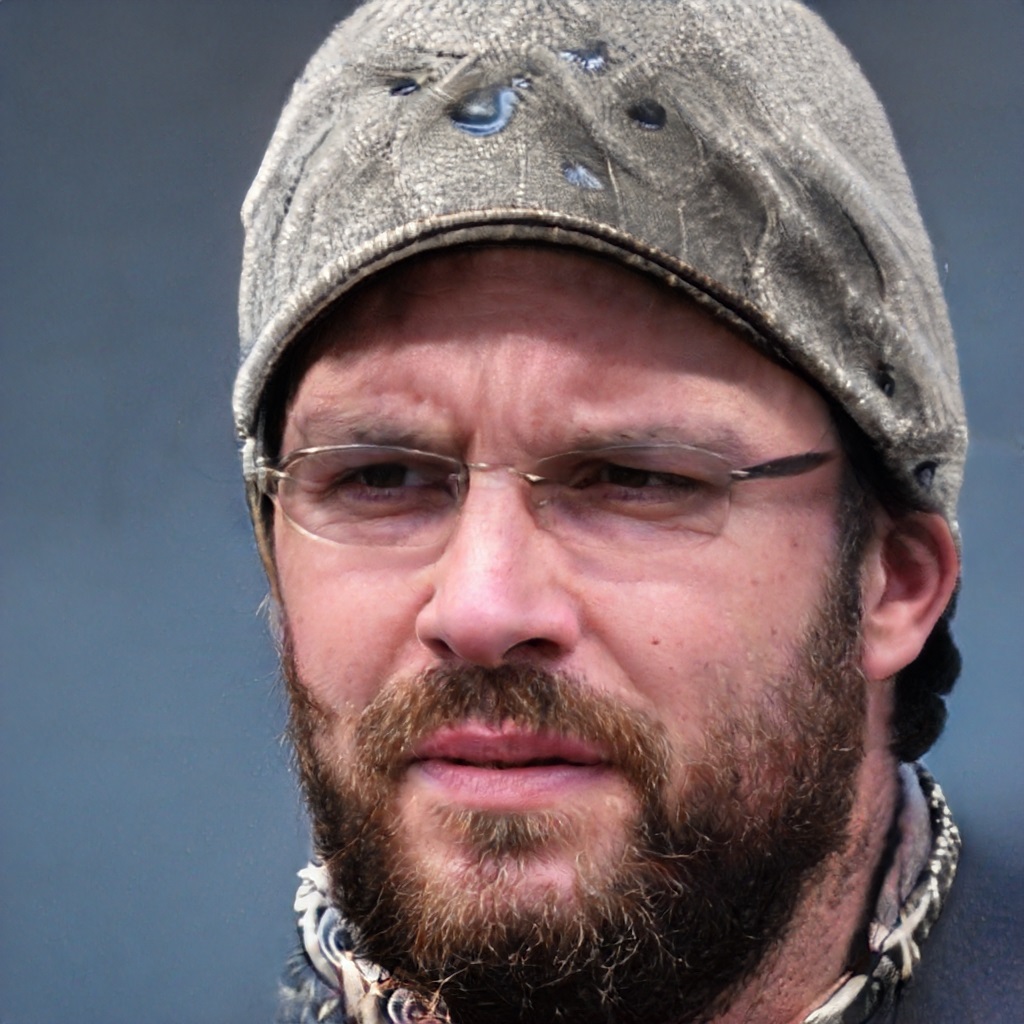
I’ve been involved in the welding industry for over twenty years. I trained in various engineering shops working on various projects from small fabrication and repairs through to industrial projects.I specialize in welding aluminum and food grade stainless steel and an now run an engineering shop fabricating equipment for the food industry.