Safety Guidelines for Using Air Hose Quick Connect Couplers
Quick connect fittings used in compressed air systems must comply with specific regulations and standards to ensure both safety and operational efficiency. These rules require that both fittings and hoses are appropriately matched to the air system’s demands, minimizing the risk of leaks and guaranteeing optimal performance. Compliance with these standards protects the system’s integrity and user safety, making it essential to select and use pneumatic couplers that meet the required specifications for a particular compressed air application.
Understanding Quick Connect Couplers
Quick connect couplers are innovative devices designed to easily connect and disconnect air hoses in pneumatic systems without the need for tools.
Types and Applications
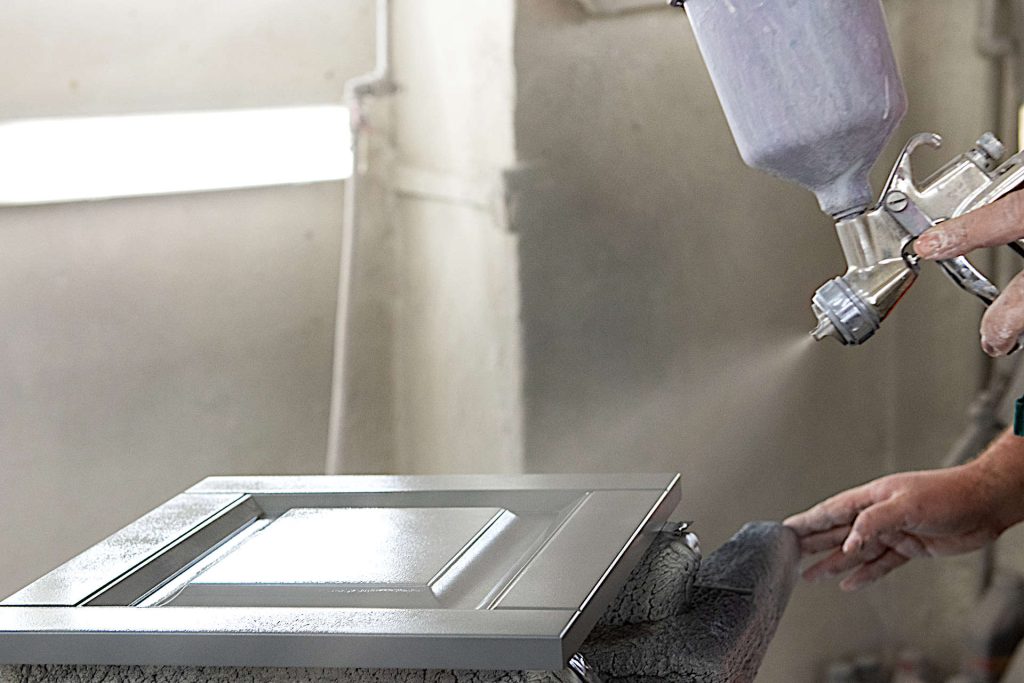
There are several types of quick connect couplers, each designed for specific applications and pressures. The most common types include:
- Industrial Interchange: Widely used in manufacturing, automotive, and construction, compatible with a variety of tools and equipment.
- Automotive: Specifically designed for automotive applications, these couplers have a unique profile to prevent accidental interchange with industrial types.
- Aro: Common in industrial settings, known for their distinct shape and reliable performance under varying pressures.
- European High Flow: Offers higher flow rates, suitable for applications requiring maximum air flow, such as in certain manufacturing processes.
Safety Regulations and Best Practices
Overview of OSHA Regulations for Securing Pneumatic Power Tools and Hoses
OSHA regulations emphasize the safety of pneumatic systems. Key points include securely fastening all pneumatic power tools and hoses to prevent accidental disconnection. This involves using retainers and safety clips where necessary to ensure a secure connection. These regulations are designed to protect workers from potential hazards caused by flying hoses or disengaged tools.
General Safety Requirements for Compressed Air and Gas Systems
Essentials of Compressed Air and Gas Equipment Safety (1910.132):
- All systems for compressed air and other gases must be safely designed, installed, operated, and maintained to avert accidents.
- Employers are tasked with training employees on these systems’ safe usage.
Lockout/Tagout Procedures (1910.147):
- A program to prevent accidental machine energization, startup, or stored energy release during maintenance or servicing is mandatory.
- This includes cutting off quick connect couplers (QCCs) from pressure sources beforehand.
Electrical Safety for Work Tasks (1920.110):
- Protection against electrical hazards for employees is required, ensuring QCCs for electrical connections meet safety ratings and insulation standards.
Industry-Specific Standards
Safety in Oxy-Acetylene Welding and Cutting (1915.71):
- QCCs must be designed to prevent disconnection through a straight pull without a rotational movement.
Gas Welding and Cutting in Construction (1926.350):
- Echoes the requirements for QCCs in oxy-acetylene setups, adding that QCCs must be inspected for damage prior to use.
Powered Industrial Trucks (1926.650):
- For hydraulic attachments on industrial trucks, QCCs must be designed and maintained to avoid accidental disconnections.
These essential safety standards for using quick connect couplers across different applications, emphasizing the necessity for proper design, maintenance, and training to ensure a safe working environment.
Not Exceeding Safe Operating Pressure
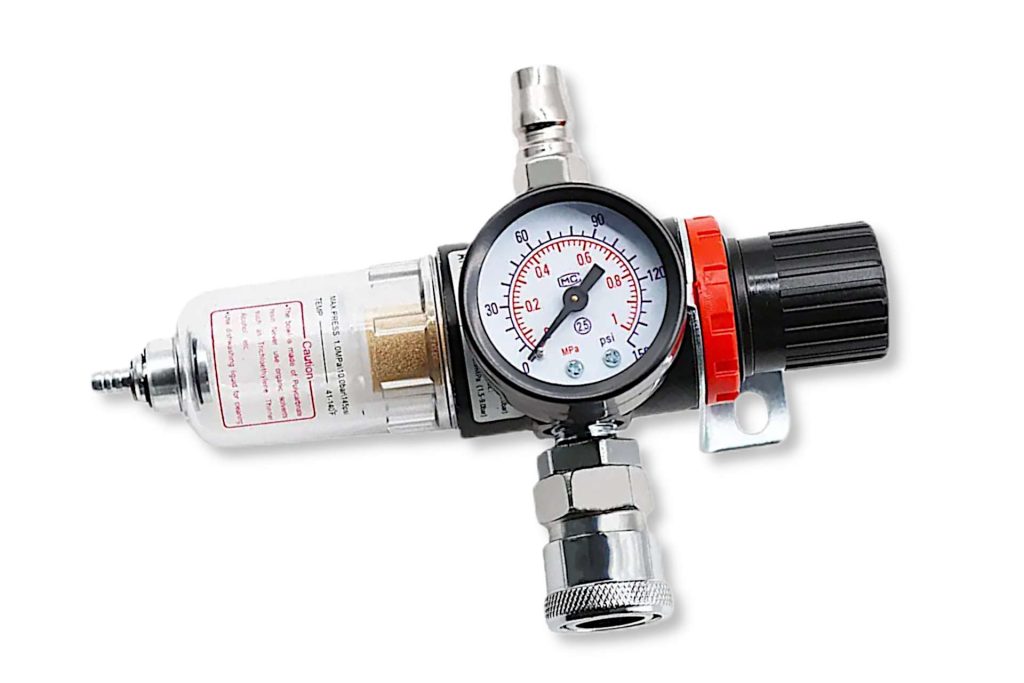
The importance of not exceeding the manufacturer’s safe operating pressure in pneumatic systems cannot be overstated. Operating within specified pressure limits ensures the longevity and reliability of pneumatic tools and hoses, preventing wear and tear from excessive force.
Exceeding these limits can lead to equipment failure, posing serious risks to users, including potential injuries from hose bursts or tool malfunctions. Adhering to these guidelines is crucial for maintaining a safe working environment and ensuring the efficient operation of pneumatic systems.
For hoses with an inside diameter exceeding ½”, safety devices are mandated to prevent hazardous situations. These precautions are vital for several reasons:
- Prevent Whip Accidents: In case of disconnection or failure, a safety device stops the hose from whipping uncontrollably, which can cause injury or damage.
- Reduce Hazard Potential: By controlling the movement of a failed hose, these devices minimize the risk of hitting operators or damaging equipment.
- Compliance with Regulations: Adhering to safety standards and regulations, including OSHA guidelines, is crucial to maintaining a safe work environment and avoiding legal issues.
Implementing safety devices on larger hoses is a proactive step towards ensuring workplace safety and maintaining operational integrity in pneumatic systems.
Guidelines for Preventing Accidental Disengagement of Quick Connect Couplers
To prevent accidental disengagement:
- Regular Inspection: Check couplers for signs of wear or damage before use.
- Correct Connection: Ensure that the coupler and plug are correctly matched and securely connected.
- Use of Safety Locks: Employ couplers equipped with safety locks to prevent unintended disconnections.
- Training: Provide adequate training for operators on the proper use and handling of quick connect couplers.
- Pressure Check: Verify that the system’s pressure is within the coupler’s rated capacity to avoid disengagement caused by excessive pressure.
These practices safeguard against unexpected disconnections, maintaining system integrity and protecting users from potential hazards.
Other Key Safety Guidelines
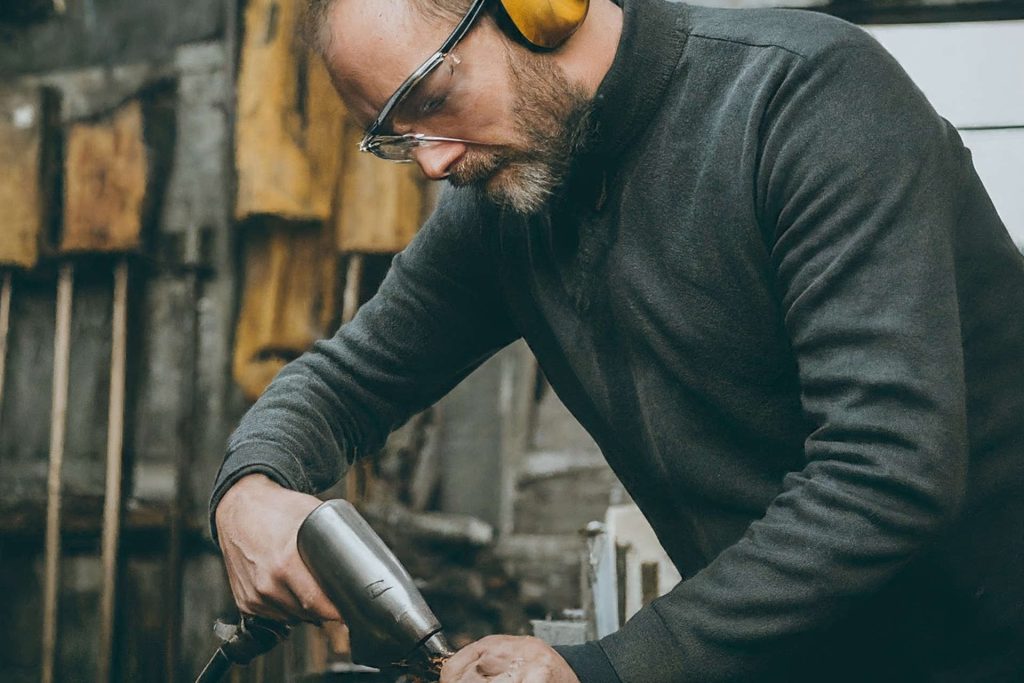
Securing Pneumatic Tools
OSHA regulations, specifically 29 CFR 1926.302, emphasize the need for securing pneumatic power tools to hoses or whips to prevent accidental disengagement. This rule is vital to avoid unexpected disconnections that could lead to injuries or equipment damage.
Operating Pressure Limits
It’s crucial not to exceed the manufacturer’s recommended safe operating pressure for hoses, pipes, valves, filters, and other fittings. Operating within these limits ensures the longevity and safety of the pneumatic system components.
Safety Devices for Hoses
For hoses exceeding ½” inside diameter, safety devices at the source of supply or branch line are mandated to prevent the hose from thrashing if quick disconnect couplings fail. This guideline aims to mitigate the risk of injuries and damage from uncontrolled hose movements.
High-Pressure Hose Connections
To prevent accidental disengagement, high-pressure hose connections must be secured with safety chains or other suitable locking devices. This measure, guided by both OSHA and MSHA regulations, is essential for maintaining secure and stable connections in high-pressure environments.
Consequences of Non-Compliance
Not following safety guidelines in pneumatic systems can lead to various negative outcomes:
- Injuries: Ignoring safety protocols can result in accidents, causing serious injuries to operators or bystanders. This includes injuries from flying debris or the violent whipping of a disconnected hose.
- Equipment Damage: Failure to adhere to recommended pressures and connections can cause premature wear or catastrophic failure of pneumatic tools and machinery.
- Environmental Impact: Leaks or spills from improperly secured systems can contribute to environmental pollution, affecting soil and water quality.
- Legal and Financial Repercussions: Non-compliance with safety standards can lead to fines, legal actions, and increased insurance costs.
Compliance is not only a legal obligation but also a moral one, ensuring the safety and well-being of all personnel and the protection of assets and the surrounding environment.
High-Pressure Environment Safety
In high-pressure environments, ensuring the safety of quick connect fittings involves comprehensive steps beyond basic inspections and secure connections. It includes adopting advanced safety protocols tailored to high-pressure risks, implementing specialized equipment designed for high-pressure scenarios, and enforcing stringent safety standards to mitigate the risks associated with high-pressure pneumatic systems.
Regular training for personnel on handling high-pressure equipment safely and emergency response procedures also forms a critical part of maintaining safety in these environments. These expanded measures are essential for preventing accidents and ensuring a safe working area in high-pressure settings.
- Comprehensive Inspection: Conduct thorough inspections of quick connect fittings, hoses, and tools before each use to identify wear, damage, or any signs of fatigue.
- Pressure Rating Awareness: Only use components that meet or exceed the maximum pressure rating of the pneumatic system to ensure compatibility and safety.
- Leak Prevention: Apply thread sealants or tape as recommended by manufacturers to prevent leaks at connection points.
- Emergency Preparedness: Establish clear procedures for dealing with equipment failure or sudden pressure release incidents, including emergency shutdowns.
- Safety Training: Provide regular safety training sessions for all personnel, focusing on the correct handling of high-pressure equipment and emergency response actions.
- Use of Safety Equipment: Employ safety devices such as whip checks, safety chains, or hose restraints to prevent whipping if a disconnection occurs.
- Regulatory Compliance: Adhere to local and international safety standards and regulations governing the use of high-pressure pneumatic systems.
- Environmental Considerations: Ensure that all safety measures take into account the potential environmental impact of the pneumatic systems, including noise and emissions control.
Based on industry standards and best practices, the above points will help create safer working environment when dealing with high-pressure pneumatic systems, reducing the risk of accidents and enhancing operational safety.
Pressure Limits and Compatibility
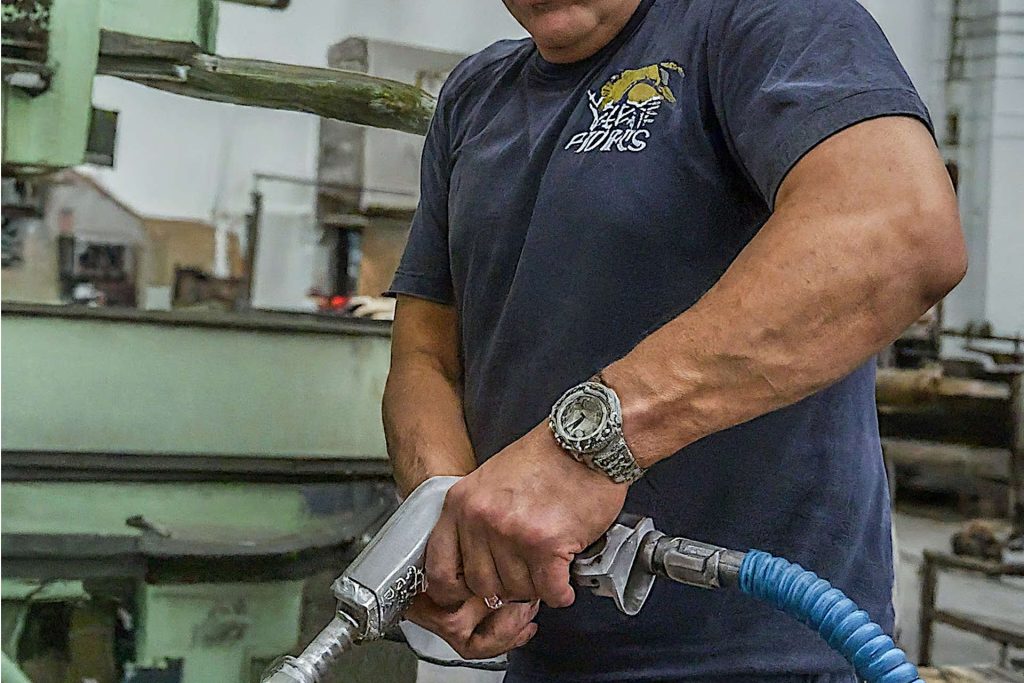
Adhering to the recommended pressure limits for quick connect fittings is crucial to maintain system integrity and safety. Each fitting is designed to handle a specific maximum pressure; exceeding this limit can cause failure, resulting in leaks or bursts.
Compatibility between fittings and hoses is equally important to prevent leaks and ensure efficient operation. Using incompatible components can lead to poor connections, increased wear, and eventual failure. Regularly checking for compatibility and adhering to pressure guidelines helps in maintaining a safe and efficient pneumatic system, avoiding potential hazards and downtime.
Table of recommended pressure limits for various types of quick connect fittings:
Quick Connect Fitting Type | Recommended Pressure Limit (PSI) | Material | Compatible Hose Types |
---|---|---|---|
Industrial Interchange | 300 PSI | Steel or brass | Type A, Type B, etc. |
Automotive | 150 PSI | Nylon or other plastic materials | Type C, Type D, etc. |
Aro | 150 to 300 PSI Depending on the specific mode | Steel or brass | Type E, Type F, etc. |
European High Flow | 300-600 PSI Depending on the specific model and size | Steel or brass | Type G, Type H, etc. |
It should be noted that pneumatic couplers are engineered to specific pressure ratings, often denoted in PSI (pounds per square inch). These ratings must align with the pneumatic system’s operating pressure to ensure safety and functionality. When we talk of compatibility, it not only relates to pressure but also to material, size, and design, ensuring a leak-proof seal and optimal flow. Misalignment in these factors can lead to decreased performance, increased wear, and even catastrophic system failures, highlighting the critical nature of selecting the appropriate fittings for each application.
Identifying and Preventing Accidents
To enhance safety and prevent accidents in pneumatic systems, it’s crucial to understand the causes and prevention strategies for common injuries.
Common Injuries Caused by Air Hose Accidents
- Whiplash Injuries: Sudden disconnection can cause hoses to whip dangerously.
- Impact Injuries: Flying debris or disengaged fittings can strike workers.
- Hearing Loss: Excessive noise from air leaks or bursts.
Prevention Strategies
- Regular Inspections: Check hoses and fittings for wear and damage.
- Correct Usage: Follow manufacturer guidelines for pressure and compatibility.
- Safety Training: Educate employees on proper handling and emergency procedures.
Signs of Issues
- Exceeding Pressure Limits: Unusual noises, hose expansion, or fittings showing signs of stress.
- Incompatible Fittings: Leaks at connection points, difficulty connecting or disconnecting fittings.
Education on these signs and implementing routine safety checks can significantly lower accident risks., ensuring a safer working environment.
Emergency Response Procedures
To effectively manage emergencies involving quick connect couplers, it’s essential to have clear procedures. These should include immediate isolation of the affected area, shutting down the air supply to prevent further pressure buildup, and assessing the situation for potential hazards.
In case of injury, provide first aid as required and notify emergency services promptly. Document the incident thoroughly for future reference and review safety protocols to prevent recurrence. This proactive approach ensures rapid response, minimizing risks and damages.
FAQ: Safe Use of Quick Connect Couplers
How often should quick connect couplers be inspected?
Regular inspections before each use are recommended to check for wear, damage, or compatibility issues.
Can I use any quick connect coupler with my air hose?
No, it’s crucial to use couplers that are compatible with your hose in terms of size, pressure rating, and material to ensure safety and efficiency.
What should I do if a quick connect coupler fails during use?
Immediately shut off the air supply, evacuate the area if necessary, and follow established emergency response procedures.
How do I prevent accidental disconnection of couplers?
Use couplers with safety locks and ensure they are correctly engaged. Also, regular training on proper connection techniques is vital.
Are there specific safety devices recommended for hoses over ½” diameter?
Yes, safety devices like hose safety cables or whip checks are recommended to prevent whipping in case of disconnection.
What are the consequences of using incompatible fittings?
Using incompatible fittings can lead to leaks, reduced system efficiency, and potentially hazardous situations due to improper sealing or disconnection.
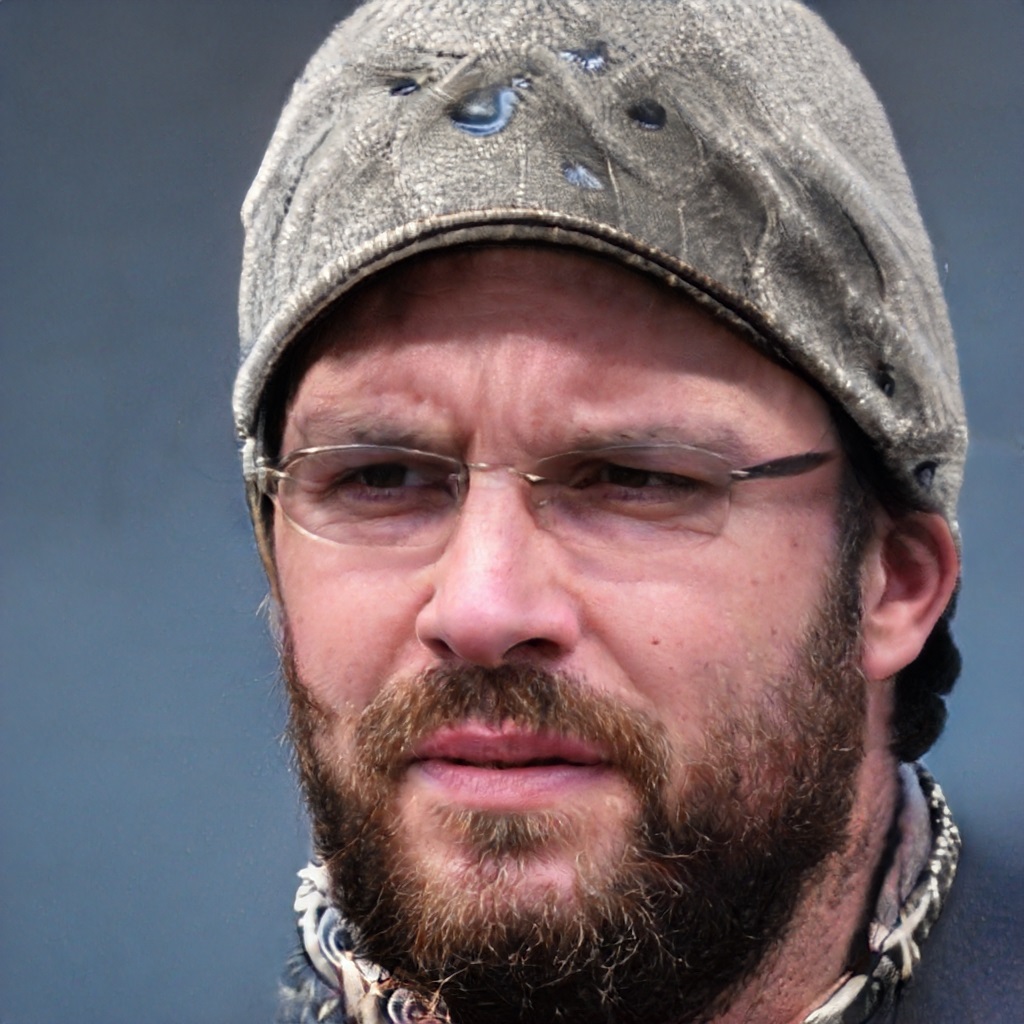
I’ve been involved in the welding industry for over twenty years. I trained in various engineering shops working on various projects from small fabrication and repairs through to industrial projects.I specialize in welding aluminum and food grade stainless steel and an now run an engineering shop fabricating equipment for the food industry.