Soldering Iron Station
Soldering Iron Station
A soldering station provides the heating system to allow the high temperatures required for the soldering process to be produced. This means that the soldering iron itself that is attached to the station only needs a power source in order to heat and apply the solder wire to the place where an electrical join is required.
Soldering Iron Station Features
For soldering on larger work pieces, sophisticated soldering stations are often required. These stations need to be temperature-controlled and therefore will include temperature sensors and regulating components to ensure the temperature of the soldering tip remains at a constant level. They are programmed to automatically increase the power when the work pieces they are soldering to is big. Many newer types of soldering iron stations include a visual display of the temperature at the irons tip.
- A digital Front-panel – Helps by displaying readily readable information
- Hot air pencil – Removal of SMD chips
- SMD tweezers – Specifically designed for use with SMD chips
- Energy saving mode – Energy saving feature automatically powers off the station if left idle
- Delayed suction – This stops the problem of solder clogging up around the tip
- ESD safe – Helps protects current sensitive components
- Temperature lockout feature – A password code can be set to lock the temperature
- Heater/sensor failed detection – If the event a sensor fails the heater power will switch off
- Programming – Selection of exact temperatures that can be applied by pushing a button, i.e. able to select pre-set fixed temperatures
The common aspects of a soldering stations are:
Uses
Soldering irons are perfect for soldering together transistor leads, pads or wires on printed circuit boards (PCBs). Soldering stations are also often used for fabrication work in electronic assembly, for making repairs and completing installations. They are used less often in plastic welding which melts plastic work pieces together at the join instead of applying a separate solder material. You can sometimes see them used for burning designs into wood but this is far from the best way of applying the process.
Soldering Guns VS Soldering Irons
The next question often ask is should I get a new soldering gun or possibly a soldering iron? Generally, operated with just using one hand, a new soldering gun will be shaped like a gun and is used for the connecting of metal surfaces. The soldering iron, which used for joining 2 pieces of metal as well, will be caduceus-shaped device that utilises a heated metallic tip. While each device are used for soldering, both has its advantages and disadvantages in terms of application.
Soldering Guns
Soldering guns generally are more powerful than soldering iron (from 100 to 240 watts). A soldering gun provides you with greater versatility while working too. Capable of working in restricted spaces, which is a lot more difficult with a soldering iron, a solder gun has a tip molded like a loop of wire. Soldering guns are useful to join both heavy electrical power connections as well as light-weight metalwork.
For the reason that guns have a specific step-down transformer which converts power from mains to a very low voltage with an large amperage current. Soldering gun gets hotter considerably faster than a iron: the tip can be warm enough to be able to solder seconds following plugging in your soldering gun. A soldering gun is more cost effective as a result of its capacity to quickly heat and also cool. In addition , soldering guns provide far better visibility since, after you depress the gun’s trigger, a low brightness lights up the area that you are working on.
The main disadvantage of using a soldering gun is that the wire loop that creates the gun’s tip dissolves with use and needs to be replaced fairly often. This can lengthen the time required to complete a soldering project. A further limitation of soldering guns is that they tend to be a lot heavier than soldering irons. This has the propensity to cause repetitive-strain injuries and can prevent clean solders. Another issue is their larger bulk. This can result in difficulties when soldering on smaller jobs. Finally, soldering guns are probably best used for intermittent work. This is largely due to the way the transformer works in that it can disrupt your work flow when soldering.
Soldering Irons
Soldering irons are a not as weighty as soldering guns and as such makes them easier to work particularly over long periods. A soldering iron provides much flexibility as there are a much wider selection of sizes to choose from; small irons tend to be best for light electronics while bigger soldering irons are more useful for heavy-duty jobs. Most soldering irons have a variety of different tips that means that you can use them for diverse types of projects, and this variety of tips also helps you to be more efficient when using an iron. In addition, whereas a gun needs to be disconnected when not in use a soldering iron doesn’t need to be turned off on on repeatedly as it retains its heat much longer. This contributes to a vastly smoother workflow.
Soldering irons, are though less effective when using on heavier jobs. Soldering irons have considerably less poser than soldering guns, making them more useful for lighter, less power intensive work. Since soldering irons heat more slowly they subsequently consume more energy, therefore less energy efficient than soldering guns.
Advantages of a Soldering Iron Station
However some of the disadvantages of a soldering iron can be overcome if the iron is connected to a soldering iron station. This helps increase the size of the work pieces that can be worked on and regulate power and temperature of the soldering iron.
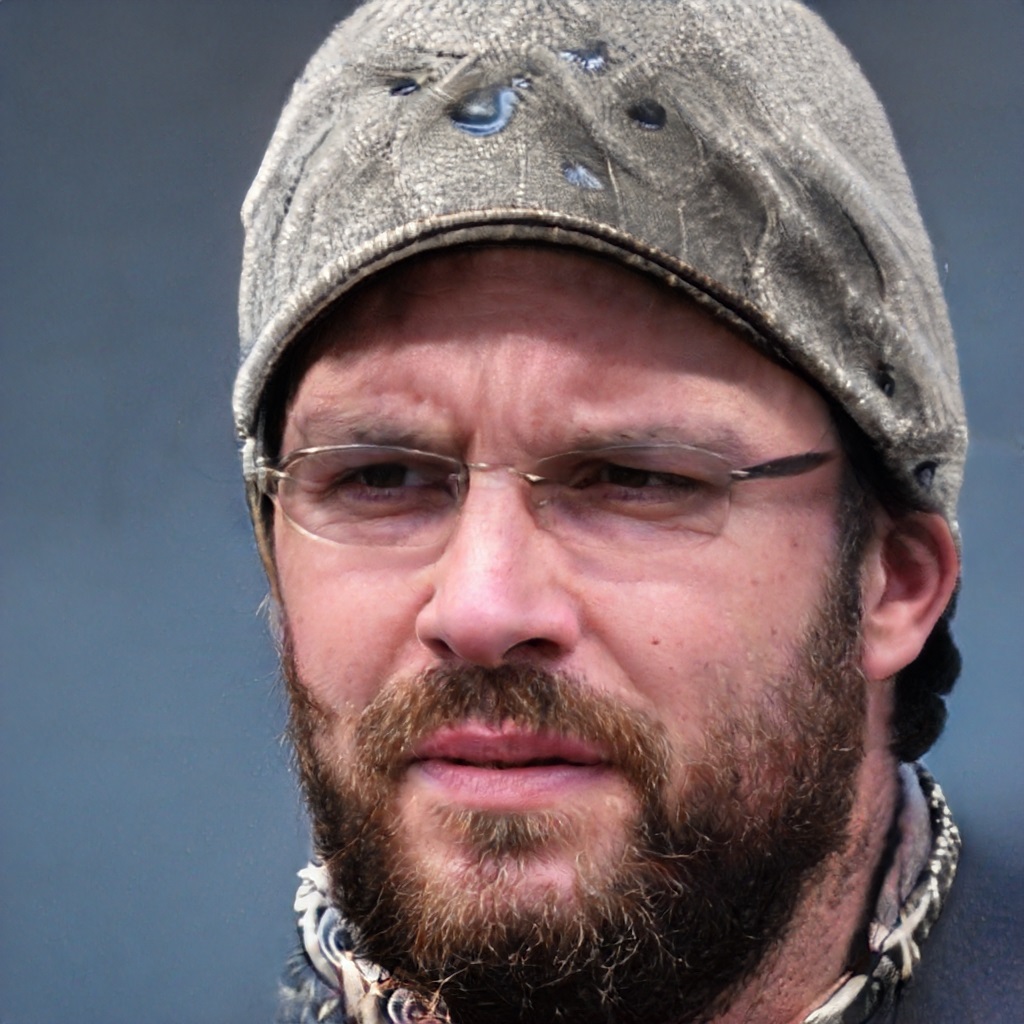
I’ve been involved in the welding industry for over twenty years. I trained in various engineering shops working on various projects from small fabrication and repairs through to industrial projects.I specialize in welding aluminum and food grade stainless steel and an now run an engineering shop fabricating equipment for the food industry.