Best Welding Gloves
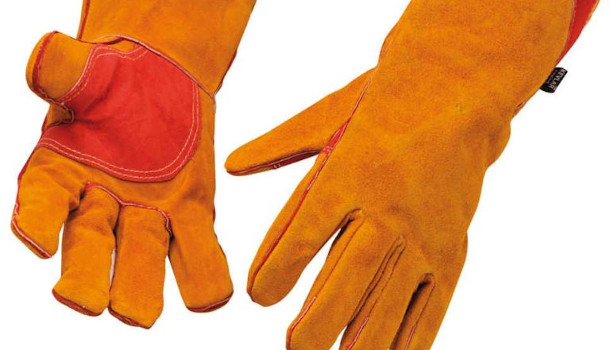
Choosing the correct welding glove / welding gauntlets can make a big difference both to the quality of the weld that you produce and the safty of the welder. Not all welding gloves are equal. You need different welding gloves for different types of welding. In this article we will look at choose the correct gloves and what your best options are.
Safety, comfort, speed and accuracy in doing work, are some of the essential elements, that are required by a good and competent welder for success in welding metals. Safety, because industry statistics show there is a very high injury rate amongst welder operatives, when this precaution is not taken into serious consideration. The injuries are often on the operatives hands or arms, and they are unable to use welding tools until the injuries are cured. Comfort of the welder is achieved when he or she feels protected and safe. Speed and a high productivity rate of excellent quality can then be achieved. As we all know, when everything is in place and working correctly a high standard and a profitable outcome is the result.
When choosing gloves for welding metals, one must consider the environment in which the welder is working. If the welder is working outside in the open air during winter, when the air temperature is low then the welder will require a glove that will keep his hands warm, but without the glove being so stuffed with insulation, that the welding work being carried out is impaired.
Leather Welding Gloves – Are They The Best Option?
It is also necessary to consider the external material from which the gloves are made. Leather is the usual choice of gloves for welding work. It is chosen in many instances because the operatives have always used leather gloves. There are alternatives to leather but these are mainly used for specialist undertakings. The advantage of a leather glove is that it is flame resistant and generally has a good grip particularly when the operative is working on heavy duty applications. Generally the best leather to use that is cost-effectiveis, hard wearing, durable, thin and abrasion resistant, is goatskin or cowhide. Horse hide and buffalo hide would be the next choices. When one is looking from ultrafine material sheep’s hide would be a suitable choice. The problem with sheep’s hide is its durability for all-round work, although it is excellent for light craftwork. It is possible to purchase or have welding gloves made in various styles. Do make sure you choose the style suitable for the work that is needed to be carried out. Generally, welding gloves for metals are divided into 4 categories.
- TIG welding Gloves
- MIG welding Gloves
- VR welding: These are gloves specially made to minimise vibration in the object being welded.
- HH welding: These are gloves that are specially made to be used in high heat conditions.
Getting The Right Glove For Your Hand Size
When selecting a glove, it is necessary to know ones hand measurements. This is taken by measuring across the base of the knuckles on the palm side of the hand to find the width, and then the measurement from the top of the longest finger to the wrist on the palm side of the hand. It is always useful to try on individual manufacturers products. Not all manufacturers make their gloves the same way, and therefore although they may be generally sized the same way according to the label. Each manufacturers glove has a different feel.
Welding Sleeves
The 1st question you should be asking yourself is: ‘Does this type of welding cause burns to arms? If the answer is: ‘Yes’, then one has to decide whether the protection from the arm is an extended sleeve from the glove, or a separate sleeve with special arrangements for holding it in place from the shoulder. Economically, when the protection is made in 2 pieces i.e. a glove separate from the sleeve, one does not have to purchase a new sleeve when the glove wears out. Statistics show that arm injury from sparks and burns etc. are not as frequent as injuries to the hand. If one is working around welding splatter, you are most probably going to want a flame resistant sleeve. There are various materials on the market such as Kevlar or Protex which are manufactured to meet a flame resistant requirement.
Some General Considerations.
Grain leather, comes from the outer skin of the animal. That means that the grain gives an extra durability to the surface and is water and oil repellent. Leather can be split, and you can often see a cheap work glove which is rough exterior, this is because the leather has been split across its thickness enabling the manufacturer to make more products from thinner skins, as what was once one skin now becomes 2 or 3 skins. The number of the skins depends on the thickness of the leather being sliced. This of course has a bearing on the length of the life of the product being manufactured. It is also worth considering as to whether you require the glove that needs cut resistant liners. It is worth noting that special resistant linings can add, for example arc flash protection lining. A further consideration is the laundering of gloves. Many people don’t even think about laundering leather gloves. Clean leather well cared for gloves have a psychological effect on the operator generally and produce a higher quality end product.
Conclusion
In welding make sure you provide the operative with the best equipment, and you will be rewarded with the best work.
Questions About Welding Gloves
Below are some common questions asked about welding gloves.
What are the similarities between MIG and TIG welding gloves?
Apart from the obvious answer they’re both welding gloves, it’s probably easier to answer this as what is the difference between the gloves.
MIG gloves are thicker and have a better heat resistance, they must also resist welding sparks and spatter which are produced during the welding process.
TIG gloves are thinner and have more manoeuvrability. This is crucial for TIG welding due to having to feed the filler material with one hand into the weld pool. A thick MIG gauntlet would hinder the welders ability.
Personally, when I am MIG welding I will use a heavy duty MIG gauntlet on my left hand (closest to the weld pool therefore the heat) then a TIG glove on my right hand, allowing a better feel of the MIG torch trigger and handling the torch.
What is the difference in MIG and TIG welding gloves?
MIG gloves generally include a thick pad at the back of the hand. This provides protection for a common MIG hand position wherein the weldor will rest the edge of the non-dominant hand against the workpiece, thumb-up. The torch is then placed across the index finger of that hand. This provides a solid brace for the torch which enables fine control of the torch tip, and makes it easy to locate the plane of the workpiece (which is often hard to see through the shade).
MIG gloves also generally have a loose fit. This is handy for quickly removing them if they overheat–a glove can be flung off with one hand. Since most of the dexterity required in MIG welding comes from the wrist, the reduced finger mobility isn’t a problem.
TIG gloves, on the other hand, are generally made of much thinner, softer leather, or sometimes a mixture of leather and fire-resistant fabric. They fit more snugly, and allow easy finger mobility. The TIG hand position has both palms facing the weld pool, so the back-pad would be mostly useless. Much more precise control of the torch and filler are required for TIG. I can generally type (poorly) while wearing TIG gloves, but wouldn’t even attempt it in MIG gloves.
TIG gloves are fine for very low-power MIG welding, and when running very short beads, but the backs of them quickly overheat. I sometimes wear TIG gloves when MIG welding very small parts because of the added precision they allow.
Secondary Answer
TIG gloves are generally thinner, allowing more dexterous movement. This is because the real danger in TIG is the light radiation, not the sparks. In MIG, there are many more sparks, and the process is less delicate, so you sacrifice some fine control for thicker, more protective gloves.
You can use them interchangeably, but it is not always a good idea. In very high powered TIG welding, you may want to use MIG gloves to shield from the heat, but in MIG, TIG gloves will be damaged too easily for anything but simple tack welding.
Other Answers
MIG
MIG welding uses electricity to join the metal by forming an arc between the electrode and the metal. When compared to TIG, this style of welding is less precise but works well for longer runs. This means there will be more sparks flying and could mean more of a mess to clean up when grinding down the weld.
STICK
This style of welding is one of the most popular and is used in the construction of heavy steel structures. Like MIG welding, stick welding uses electricity to create an arc to fuse the metals together, so expect high heat and a lot of sparks.
TIG
Tungsten Inert Gas welding (now do you get the reference from above?) is a highly technical style of welding requiring a lot of precision. If welding was karate, TIG welding would be Mr. Miyagi. To master TIG requires a lot of practice to produce a top notch weld.
Which are the international standards for MIG welding gloves?
I’m a big fan of light weight soft leather tight fitted gloves. Having had a number of injuries to my hands I simply like the dexterity they offer. I’ve never had a wire go through my glove in all the time I’ve been welding. Mind you I’ve never stuck my finger in the end of a loaded handgun either. If you are referring to the short circuited stubs sticking up from a bad start,these can be easily wire buffed off. I know of no statute that standardized the gloves industry. I really have done a ton of so called MIG welding since 1980. Best advice is don’t run ones had over a weld to check it and dress it up after completion. Wire buff and grind smooth the rough spots. Maybe there’s a bit of adjustment required for amp and wire feed speed to tune out the cold starts. If you are doing mostly structural stuff,I tend to favour close to a spray transfer weld anyway and that will help eliminate issues as well as a quick back step before progressing. Any time the skin gets compromised there is a risk of infection and these days this is a big issue with WCB claims.
This was work related where a brown recluse got into my welding glove overnight and stung me as soon as I put my gloves on. I eventually lost the finger due to infection. So it’s honestly not oh boohoo and all that tough guy bull shit. Today’s welder has to be a professional in every aspect of how he or she conducts themselves. In order to become treated how they want to be regarded and respected.
Secondary Answer
Aw, boohoo. Maybe they should stop trying to weld their own finger?!
Another source of prickly wires come from “porcupine” welding technique. IF your welders sputter a lot, short segments of wire will bond and stick up from the weld zone. After they are forgotten, your workers may brush the bit of wire and get impaled, or worse, your customers may get stuck. I once worked for a place that had this problem so bad they were fined $500 for every wire remnant their customer found.
The fact is, your workers only need their gloves to do two things: protect against radiation/ the occasional slag, and allow them to handle metal all day long without absorbing metal through their skin. I have learned to weld using woven nitrile gloves, and even very thin black rubber gloves are great for radiation shielding. (i tend to do fine fitting work between welding passes, but have different leather gloves for sessions mostly welding.)
If you want puncture resistance, you will need wire mesh gloves, which are rather expensive, dangerously conductive, and will quickly destruct when contacted with slag. Wire mesh gloves are used by clumsy butchers and other users of knives.
You don’t need international standards to save fingers. You need better training!
However, if you insist that the world needs better gloves, by all means go into the gloves business.
Other Answers
Your workers need retrained. Been around a LOT of Mig – GMAW/ MAG – welding, never seen a glove puncture. They need a light leather glove on the ‘gun hand’ and a heavy leather welding gauntlet on the ‘off hand’ to protect from the weld spatter.
You could try a kevlar inner glove. What I suggest is to observe the welding process to determine what part of the welding process produces the punctures. This may result in rewriting your Hazard Safety Analysis and upgrading your training of the welding procedures.
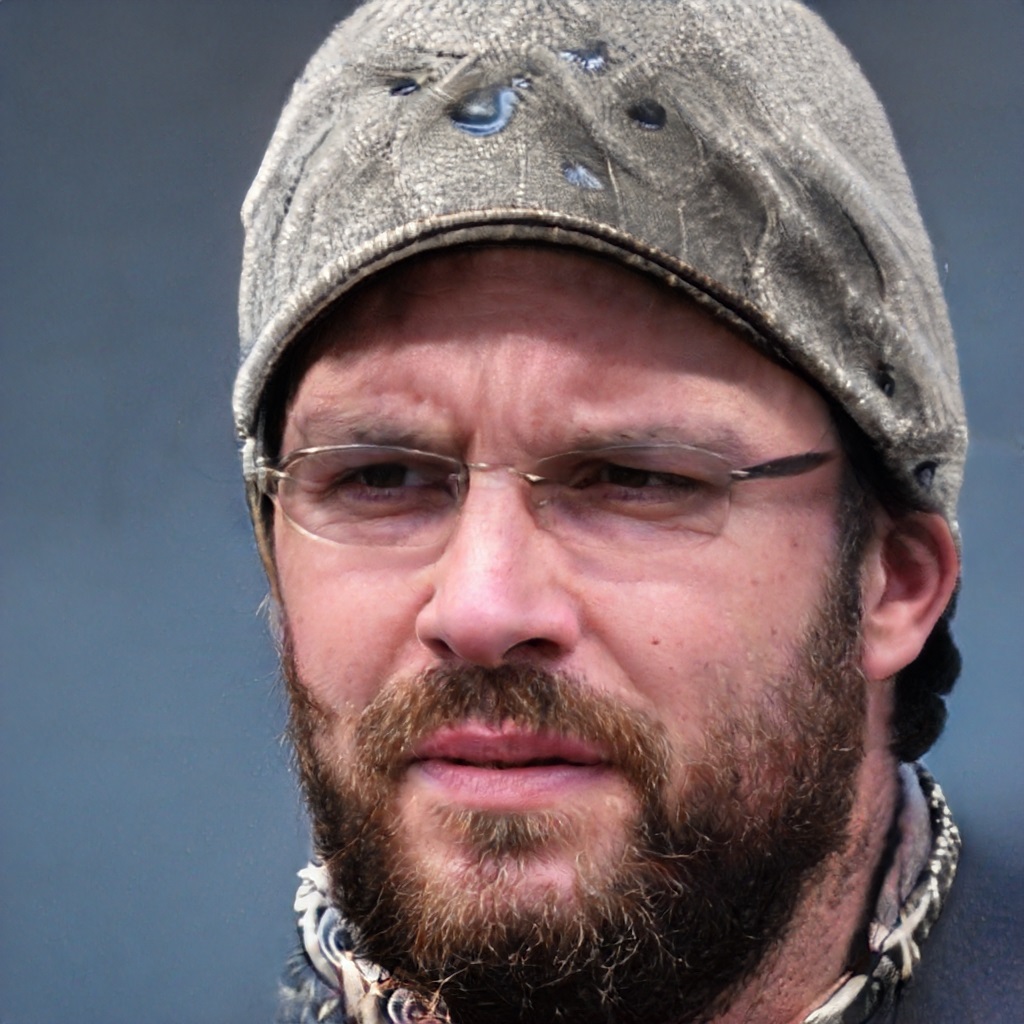
I’ve been involved in the welding industry for over twenty years. I trained in various engineering shops working on various projects from small fabrication and repairs through to industrial projects.I specialize in welding aluminum and food grade stainless steel and an now run an engineering shop fabricating equipment for the food industry.