What is the Best Shielding Gas for Welding Stainless Steel?
What is the best shielding gas for welding stainless steel? Welding stainless steel may be accomplished in a variety of methods, each requiring a particular shielding gas. We will examine the most popular stainless steel welding methods and determine which gas types is best for each.
Properties of Stainless Steel
Stainless steel has been used since the early 1900’s as an alternative to iron and other metals because it does not rust or corrode. It is also resistant to corrosion by acids and alkalis. The main difference between stainless steel and carbon steel is that stainless steel contains chromium, nickel, molybdenum, manganese and sometimes vanadium. These elements are added to make the metal more durable and less susceptible to corrosion.
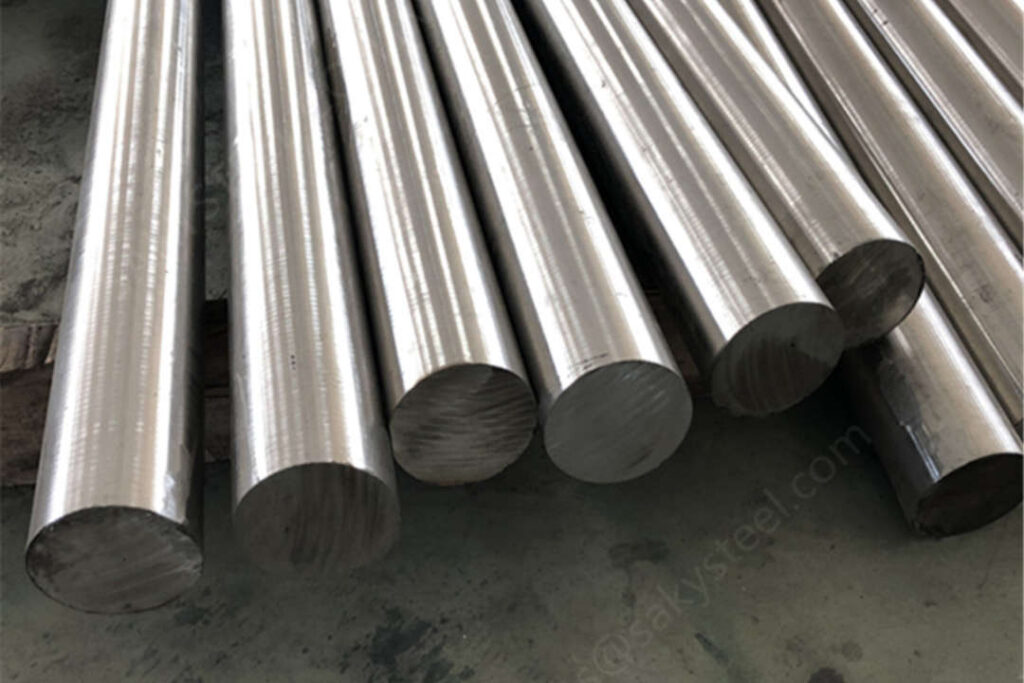
Stainless steel is usually selected because of not only its corrosion resistance but ability to withstand high temperatures as well as its strength. There are several kinds of stainless steel and welding procedures and techniques that may be used to fabricate stainless steel components without compromising corrosion, oxidation, or mechanical qualities or introducing faults into the weld.
As a result of its wide range of applications, stainless steel is found in many different of fields from construction to automobiles to aircraft to petrochemicals to electronic equipment to power plants to ships. Depending on the application, these sectors demand a wide range of welds.
The two main grades of stainless are austenitic and ferritic. The corrosion resistance of nickel-based alloys is superior than that of 300-series chromium alloys. As compared to austenitic chrome alloy, ferritic 400-series chromium alloy is less costly.
Selecting a Shielding Gas for Welding Stainless Steel
As each metal has different properties the shielding gas used for welding stainless steel will be different to the shielding gas used for welding mild steel or aluminium and different depending on welding method used.
Argon gas is used as a shielding gas during welding to protect the molten weld pool from oxidation. Helium gas is often added to reduce porosity and promote better wetting of base metals by filler metal. These gases are added to the welding process to control the amount of heat transferred to the base material being joined.
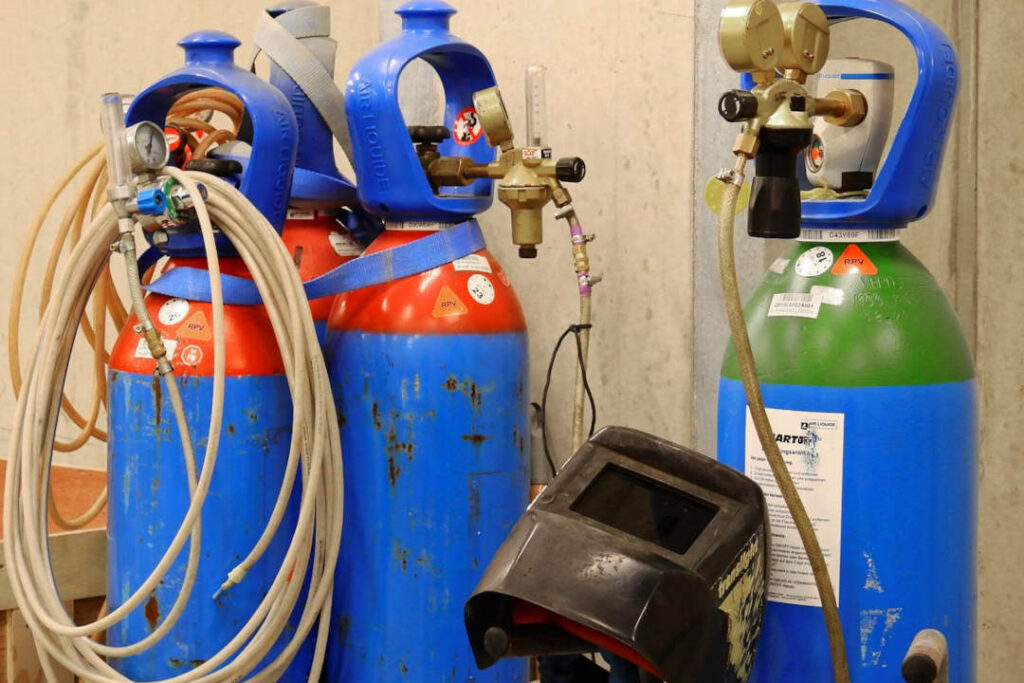
In gas metal arc welding GMAW (MIG), oxygen is added to the shielding gases. The addition of oxygen improves the arc stability and weld puddles.
In flux cored arc welding FCAW, arc stability is improved by include CO2 in the shield gas. Nitrogen and hydrogen may also be introduced in regulated proportions in both processes. For specific stainless steel welding applications, these three-part combinations are the optimum option.
In gas tungsten arc welding GTAW (TIG) the predominant shielding gas used is argon or argon and helium gas mixes.
Before deciding on a shielding gas, it’s necessary to determine the property of the materials will be weded and then decide on the best welding procedure for the task. This will to a large extent dictate the shielding gas used.
MIG Welding Stainless Steel
Metalographic tests have shown that differing shielding gas mixtures may significantly alter the mechanical and microstructural properties and characteristics of 316 austenitic stainless steel when welded using the GMAW (MIG) process, and these findings have been substantiated.
Thus with MIG welding, choosing the correct gas is important. Your stainless steel MIG procedure should not use shielding gases that are fully inert,such as 100% argon or helium.
This is because in MIG, the arc uses a filler material, unlike other processes such as TIG, which do not. As the surface tension of stainless steel droplet and pool causes low liquid metal fluidity, it makes it difficult to distribute and wet the welding surface, and the weld pass is not created properly when using pure argon as the shielding gas because materials a high surface tension.
As a result if you were to employ fully inert gas such as argon as your shielding gas in the welding process it is likely to result in a poor weld.
Gas combinations like these should be chosen:
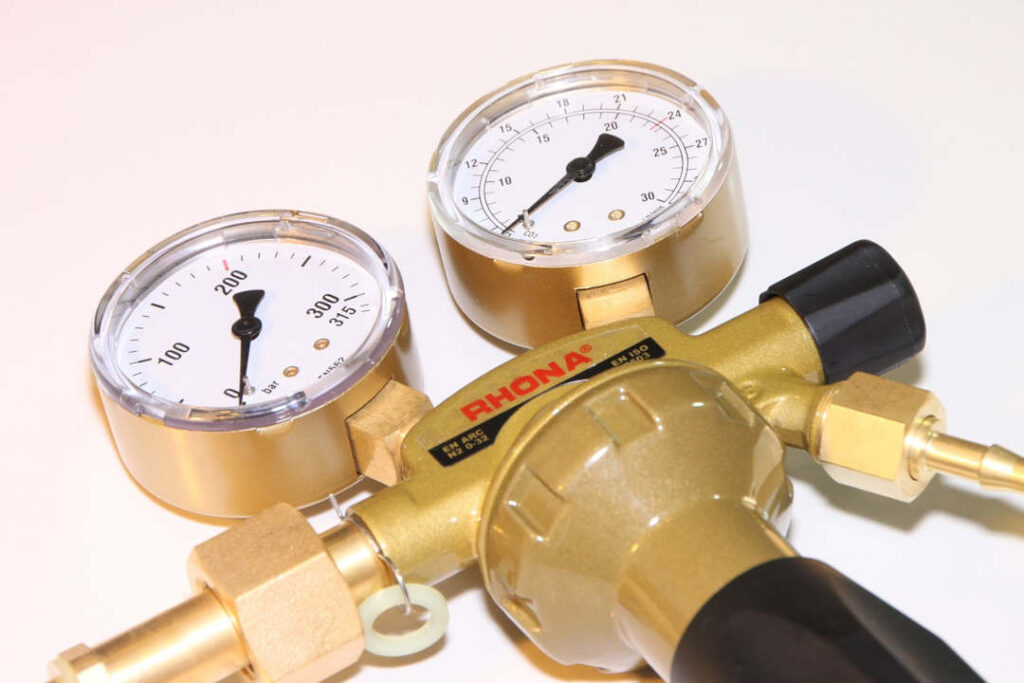
Ar plus 1-2% O2
By adding oxygen Both stainless steel droplets and molten pools have lower surface tensions, which improves their fluidity and spreadability, as well as their wettability on the weld surface. Beautiful weld bead formation due to proper weld depth and breadth.
Ar plus 2-5% CO2
By adding 2 to 5% carbon dioxide although there can be risk of carburizing the stability of the arc is excellent and oxidation is much reduced. In addition the alloying element burns less, this mix can be used in wire welding for jet transition, pulse transition and short circuit transition.
Ar plus 25% CO2
This gas mix is probably the most common shielding gas for MIG welding stainless steel and can be used with jet transition, pulse transition and short circuit transition.
Ar plus 5% CO2 plus 2% O2
Adding 5% carbon dioxide and 2% oxygen to argon is excellent for stainless steel welding with higher technical requirements because of its good single welding seam and double forming properties of the three part blend gas arc concentration.
Ar plus 30% He plus 2% CO2
To maximise welding depth, speed, and decrease weldment deformation, 30% helium and 2% carbon dioxide is added to argon. This is often used when welding austenitic and high alloy austenitic stainless steel. This three part blend works well with both short- circuiting, spray, or pulsed spray transfer. For welding 304 stainless steel to carbon steel, this combination is a great option.
Other Gas Blends
You may achieve better bead form and colour with the correct gas combination than with pure argon or pure CO. More than 90% of the mixture consists of argon and CO, with 2% to 5% each of nitrogen and hydrogen.
With caution, nitrogen mixtures may be used to weld stainless steel to other metals, but they must be utilised carefully. To ensure a high strength and corrosion resistance, a suitable microstructure is required.
MIG Welding Ferritic Stainless Steels
Steels with no nickel or chromium were developed to save money on production. Steels such as ferritic and martensitic stainless fit within this category. Both are very resistant to corrosion. They are, however, less durable than nickel and chromium alloys.
As a consequence, weld travel speeds may be reduced when shielded arc welding is used instead of traditional GMAW. SAW, on the other hand, may produce more weld spatter because to its lower weld puddle energy flux density. The usage of this kind of welding to connect ferritic stainless steel is rather common.
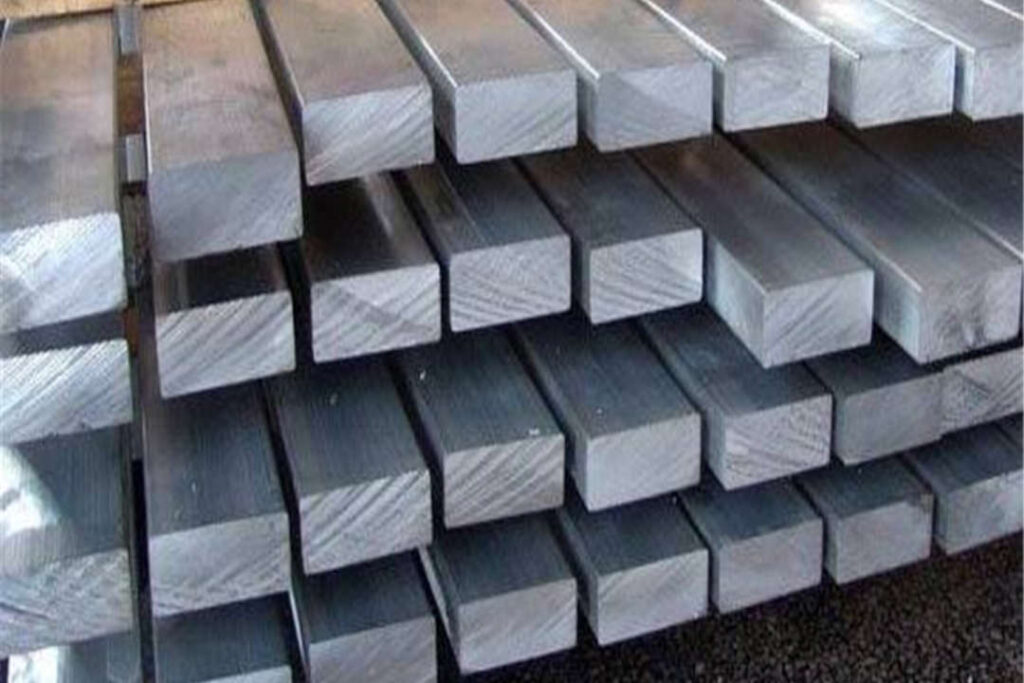
In ferritic stainless steel joints, argon mixtures with 5 to 10 percent CO typically provide acceptable weld chemistries and microstructures. Weld chemistries may be changed to match individual demands by employing metal-cored wire with these mixes, which can speed up and increase productivity in most applications.
The most cost-effective approach was developed using the following shielding gases and wires: MIGS uses 4% carbon steel wire and 12% argon shield gas;
Standard copper and silver wires demonstrated lower deposition rates than metal-cored wires at the same current levels. So flat beads might be used instead of filaments to deposit more diverse forms. Because the metal-cored wire requires no extra processing after welding, the amount of post weld machining that is necessary is reduced.
FCAW Welding Austenitic and Ferritic Stainless Steels
When using flux core arc welding (FCAW)to weld austenitic stainless steel, flux-cored wire is produced for use with specific shielding gases. Often 100% CO is used for welding austenitic stainless steel where as argon/CO mixtures are used for welding ferritic and martensitic stainless steels.
TIG Welding Stainless Steel
When it comes to welding stainless steel, TIG welding is one of the most used procedures.
There are more shielding gas mixtures that can be used for TIG welding stainless steel than for steel, but not all gas mixtures are appropriate for all types of material. For example hydrogen mixes are only suitable for austenitic stainless steel while nitrogen blends are only suitable for duplex stainless steel.

Pure argon, may be used to weld stainless steels and nickel alloys using TIG welding. It has a consistent welding arc and can be used with any kind of stainless steel. However, thicker material can cause the arc need to be more viscous and it becomes harder to control causing fusion issues
Should it be necessary, argon may also be utilised to purge the air of any contaminants.
Argon is a superior shielding gas to either helium or hydrogen, although it is more costly. Argon/helium mixes are less effective in shielding than pure argon, but they are less expensive and produce more. Mixtures of argon and hydrogen are less effective than pure argon and need greater operating voltages.
Faster welding rates and increased productivity may be achieved by adding helium and hydrogen to the shielding gas argon. Distortion is also reduced if the speed of travel is increased. An argon/hydrocarbon mix should also reduce the amount of oxide left on the weld deposit if colour match between the base metal and filler material is required.
Summary: What is the best shielding gas for welding stainless steel
So, what is the best shielding gas for welding stainless steel? Determining this is clearly dependent on a number of criteria. The main ones, though, is the welding method to be employed and the type of stainless steel to be welded.
Although you can use MIG generally speaking it is better to use TIG when welding stainless steel as the weld quality tends to be better, although in terms of productivity MIG is likely to be better.
For TIG pure argon is the most common gas but if you are looking to weld thick materials then an argon helium blend is better.
For MIG an argon and carbon dioxide blend is probably the most efficient. Although you can go as low a 2% many welder will often prefer to use a 25% carbon dioxide content.
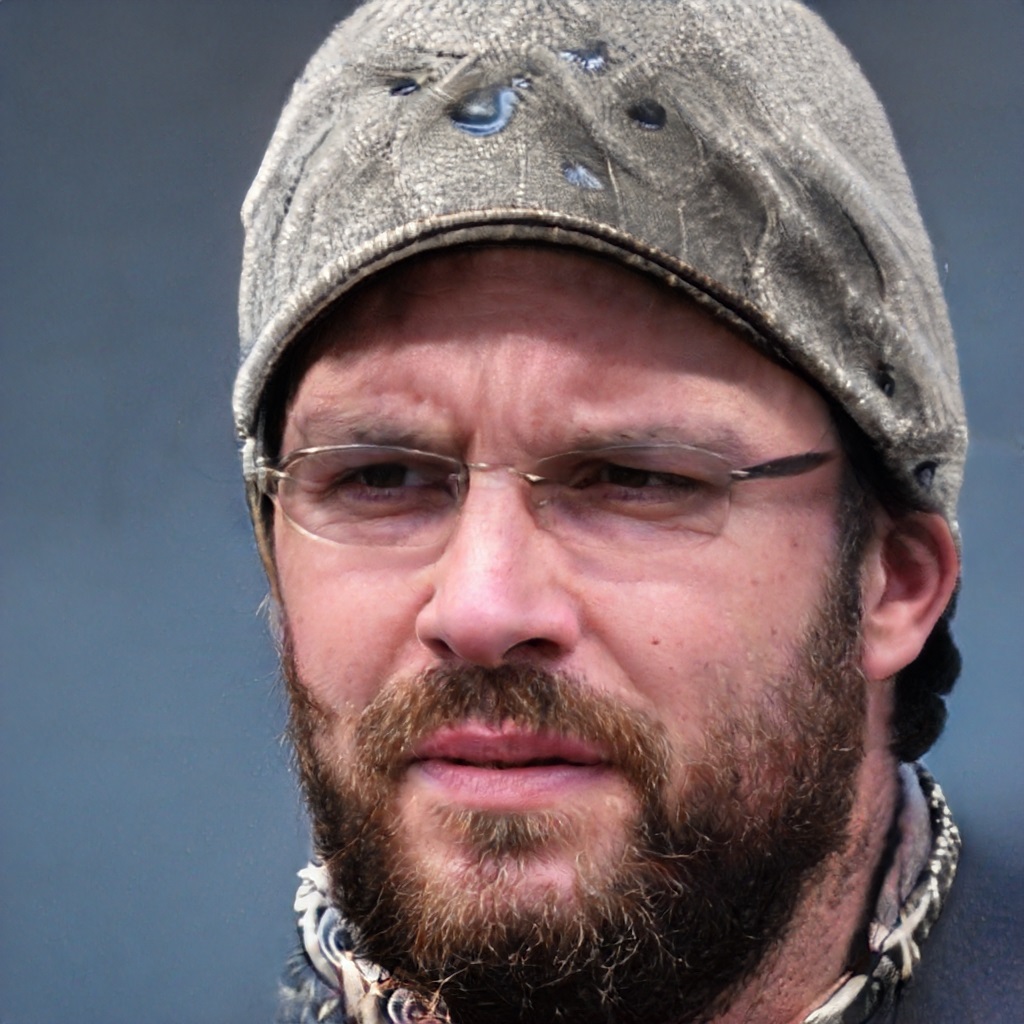
I’ve been involved in the welding industry for over twenty years. I trained in various engineering shops working on various projects from small fabrication and repairs through to industrial projects.I specialize in welding aluminum and food grade stainless steel and an now run an engineering shop fabricating equipment for the food industry.