Mig Welding Gases | Using the Right Gas for the Welding Task
MIG welding gases. The choice of shielding gas is crucial in Gas Metal Arc Welding (GMAW), more commonly known as MIG welding. Discover how to choose the best shielding gas for your task.
Shielded gas-assisted MIG welding delivers cleaner and quicker welds, eliminating the need to constantly change electrodes just like you would with stick welding. There are several benefits to employing shielding gases in welding that include less clean-up and better efficiency, but understanding how these MIG welding gases work and the various types available is essential.
In order to keep the molten weld pool from being exposed to the oxygen, hydrogen, and nitrogen in the air around you, shielding gas is used. In the weld pool, the response of these constituents, including excessive spatter and holes in the bead known as porosity, may cause weaker welds as a consequence of these reactions.
We will discuss the various MIG welding gases options available but as a side note Metal Inert Gas welding is technically no longer MIG welding if carbon dioxide or oxygen are utilised. MAG, or Metal-Activated Gas, welding, is the method of choice for this kind of welding. The reason for this is because neither carbon dioxide nor oxygen are inert gases also referred to as noble gases. Helium or argon are used as shielding gases in MIG welding, whereas MAG employs active gases.
Shielding Gas for MIG Welding: The Fundamentals
Choosing a welding gas can be confusing, but it doesn’t have to be. Learn about the different types of gases and what they are used for. This guide will help you understand the basics of MIG welding (GMAW).
Choosing The Right Shielding Gas
A wide range of shielding gas options are available as MIG welding gases for MIG welding applications. Your welding aims and applications must be taken into consideration before deciding on a welding machine.
Each gas has a specific function in the weld process, ranging from arc stability through weld penetration to the final weld. MIG welds may benefit greatly from using consumables that produce a steady supply of gas, therefore this is an essential consideration.
Make sure you know what you want to achieve with the weld before selecting the correct gas for the job at hand. Cost, preparation, base material to be welded, completed weld qualities, and what has to be done during post-weld clean up should all be considered when making your choice of welding procedure.
However, it is always a good idea to seek out the advice of your supplier for MIG welding gases that are compatible with the welding wire you want to use. Consult the wire maker for more advice as well. Most likely, they’ll provide a variety of gas selections, ranging from the greatest to the least acceptable, along with their pricing. A suggestion guide on the inner panel of your MIG welder may present you with a list of many possibilities.
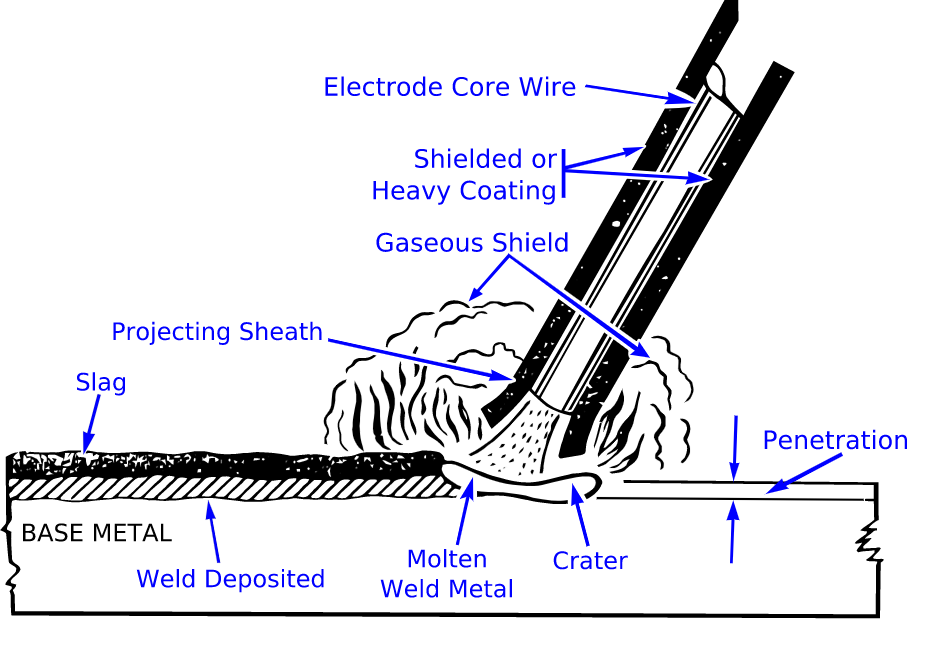
When making your final decision on which gas to use, keep the following factors in mind.
The price of the MIG welding gases
The properties of the finished weld
Required work preparation and post-weld clean up
The base metal material
The nature of the weld transfer process
The time it will take for the job
Inert Gases (Noble Gases) for MIG Welding
The use of Inert gases is often preferred when MIG welding because weld spatter is reduced with noble gases like helium which in turn prevents chemical reactions from occurring. For MIG welding, generally argon and helium are often utilised, despite the fact that there are six noble gases to choose from. The six noble gases that occur naturally are helium (He), Neon (Ne), Argon (Ar), Krypton (Kr), Xenon (Xe), and Radon (Rn).
The usage of pure argon/helium combinations would usually only be employed for nonferrous metals, such as copper and aluminium. Below are more detailed analysis of most inert MIG welding gases used:
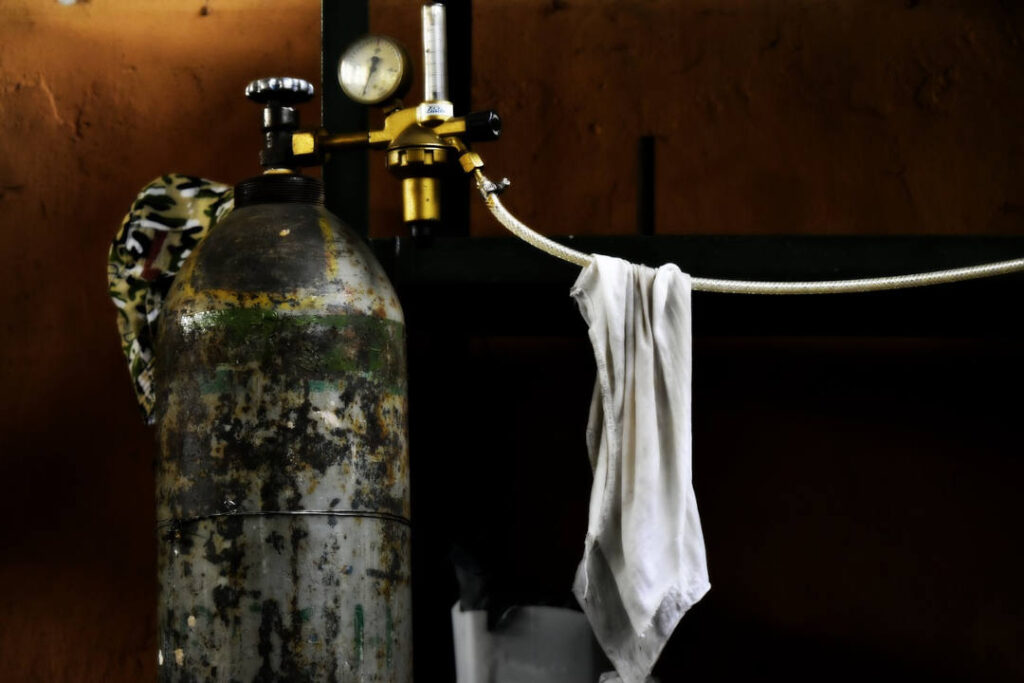
Argon
Argon as a MIG welding gas. Argon has several benefits for use as a shielding gas particularly for butt and fillet welds because of its limited penetration. It also has a pretty smooth and easy-to-follow trajectory. When welding non-ferrous metals like titanium, aluminium, or magnesium, you must use pure argon. Hydrogen, helium, or oxygen are common additions to argon mixtures. Arc characteristics and metal transfer may be improved by enhancing the arc characteristics.
Using mixed gases is a viable option if weld quality and aesthetics are crucial. Many variations are available, ranging from 75% to 95% argon to a maximum of 5% CO2. They have superior arc stability and less splatter than pure CO2. As a result, more aesthetically pleasing welds and greater productivity may be achieved via the employment of mixed gases in the spray transfer process. Some stainless steels and carbon metals may be welded using a combination of argon and CO2. Remember that greater quantities of carbon dioxide might lead to more splatter.
Helium
Helium as a MIG welding gas. When welding non-ferrous metals helium is often employed although is possible to utilise helium on stainless steels, despite the fact that it is a ferrous metals. Its broad and deep penetrating qualities make it ideal for working with heavy metals. 25-75 percent helium to 75-25 percent argon is typical. You may change the penetration and bead profile by altering these ratios.
Helium, CO2 and argon are often utilised as a tri-mix gas combination while working with stainless steels. Metals like stainless steel, aluminium, magnesium and copper alloys are also welded using helium to avoid oxidation.
Faster arc speeds and higher productivity may be achieved by using helium. While helium is more costly than argon, it does have a faster flow rate. When deciding whether or not to use helium, it is vital to examine the cost of the gas in relation to productivity rates.
Argon/Helium Mix
Argon/Helium mix as MIG welding gases. Because of there different properties when welding finer control can be gained by mixing argon and helium. This is especially useful when welding non-ferrous metals.
The mix can range from around 25% to 75% helium, depending on the application, for GMAW. We can control how much heat is transferred to the weld by altering the shielding gas composition. The form of the weld metal cross section and the welding speed might be affected by this.
As generally labour expenses account for a large portion of our total welding expenditures, an increase in welding speed has the potential to save us a significant amount of money. In rare cases, the cross section of the weld metal might have an impact.
Adding helium to pure argon increases the arc voltage by 2 or 3 volts for a given arc length. GMAW can achieve its widest penetration shape with a helium/argon mixture of around 75% to a 25%. Double-sided groove welds in heavy plate benefit from the wider penetration form and reduced porosity levels of these gas mixes. Weld bead profiles’ ability to provide a broader target during back chipping can assist lessen the chance of incomplete joint penetration associated with this type of weld joint.
Active Gases
Non-inert or active gases are also commonly used as MIG welding gases. Active gases interact with the puddle and/or melting drop wire. The two most commonly used active gases are carbon dioxide and oxygen.
Carbon Dioxide (CO2)
Carbon dioxide as a MIG welding gas. Carbon dioxide or CO2 is a “semi-inert” gas, meaning it is resistant to chemical change to a lesser degree than inert gases such as argon and helium.
Carbon dioxide is the most prevalent active gas used and is one of the few gases that may be utilised in its pure form without the addition of an inert gas like argon or helium. As a result, CO2 is often considered the least expensive solution and an excellent choice if project budgets are a top concern.
Pure carbon dioxide , also referred to as 100 percent CO2, has a deep weld penetration, which is useful for welding thick materials. However, pure carbon dioxide is confined to short circuit welding and generates a less stable arc as well as more spatter than when coupled with additional gases (also known as’mixed gases’).
Pure carbon dioxide is appropriate for tasks where the aesthetics of the weld are either unimportant or cannot be seen, such as the underbelly of an automobile. Another thing to bear in mind is that cleaning up after a weld is also a bit more complex.
When dealing with ferrous metals such as mild steel, carbon dioxide comes in handy. For speciality wires, 100 percent CO2 is occasionally used; for regular MIG welding, 72/25 Argon/CO2 or a tri-mix of CO2, argon, and helium is considerably more frequent.
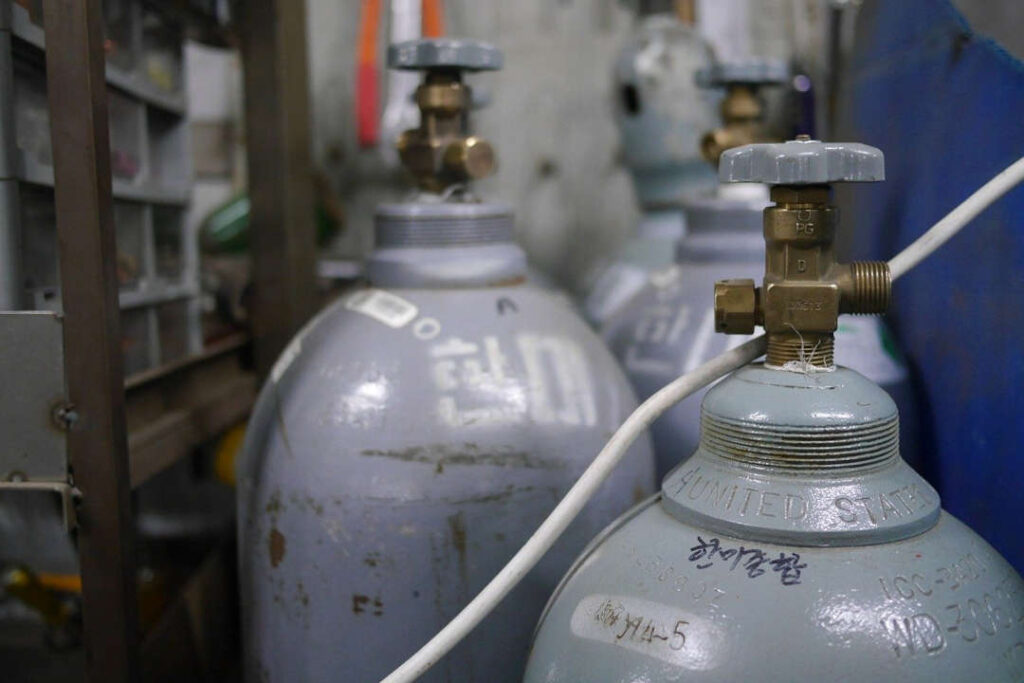
Oxygen
Oxygen as a MIG welding gas. As a reactive gas, oxygen is frequently added in modest quantities when combined with other shielding gases, typically ranging from 1 to 9 percent. In stainless steel, mild carbon, and low alloy metals, this enhances weld pool flow as well as arc stability and penetration. Because oxygen may induce oxidation, it is not suggested for use with aluminium, copper, magnesium, or other unusual metals.
On stainless steel and simple carbon metals, oxygen/argon mixes are often utilised. It creates a steady arc with little splatter. Higher quantities of oxygen, on the other hand, may make out-of-position welding difficult owing to increased puddle flow.
Other MIG Welding Gases
Hydrogen as a MIG welding gas: In high-temperature applications, such as stainless steels, hydrogen acts as a shielding gas. For usage on austenitic stainless steel, it is often combined with argon.
Nitrogen as a MIG welding gas : When welding stainless steel tubes, nitrogen is utilised as a purging gas. It may also be used as a shielding gas for stainless steels when mixed with argon in tiny volumes.
Propane as a MIG welding gas : Propane is often used in scrap yards to cut carbon steel when cut quality is not critical. If your application does not need exceptional cut quality, propane is a relatively inexpensive solution.
What’s the Best Gas for MIG Welding Different Metals?
When looking for a shielding gas for MIG welding, 75/25 argon and CO2 mixtures are the most common. It’s possible to utilise Vern Lewis Welding Supply’s argon and CO2 mix 75/25 to weld a wide range of metals, including mild steel and nonferrous metals. Contact us immediately if you have any queries or need help selecting the finest MIG welding gas.
MIG Welding: What Is the Best Gas for Mild Steel?
Many welders choose MIG welding for mild steel welding because it produces a cleaner finish. When it comes to welding, MIG is the most common method used by artists, amateurs, farmers, racing fanatics, and DIY welders.
A shielding gas is used to protect the arc and weld puddle throughout the procedure. CO2, argon, or a combination of these two gases are commonly used by welders to shield their projects when welding mild steel since they give the finest protection for the material.
Nonetheless, what is the ideal gas for MIG welding purposes? There are two ideal gas mixtures for MIG welding of mild steel; a 100% CO2 and a 25-75 Carbon-Argon mixture.
Welders at home and in garages often utilise a shielding gas consisting of 25 percent carbon dioxide with 75 percent Argon. Welders use this combination because it provides a good balance between cost and end weld quality.
Local welding supply businesses have this shielding gas mixture. It comes in a variety of sizes and may be stored in the trunk of your car. If you plan to weld at home or on the ranch sometimes, this gas mixture is ideal.
However, before we get into the specifics of this and other common gases, there are a few things you should be aware of. More on shielding gases for welding mild steel can be found here.
MIG Welding Gases: What is the Best Gas for Carbon Steel?
Carbon steel has a much higher content of carbon in it compared to mild steel which can change the gas you might want to use.
As a result, many welders employ the C25 combination, which consists of 25% CO2 and 75% Argon gas, because CO2 cannot be used alone because it causes a deeper penetration and a lot of smoke, and it may even cause a rough-looking weld. That’s also why Argon gas is so commonly used for welding carbon steel. It’s best to consult the user handbook or the inscription on the welding equipment to discover what alternative mixes are recommended by other welders.
Welding thin sheet metal and producing a lot of spatter might be tough and time-consuming, but if you’re solely welding carbon steel, Co2 is a great option for a hobby welder.
What is the best gas for MIG welding aluminum?
The most effective shielding gas to use when welding aluminum is either argon or a combination of both argon and helium. This is because both of the above are inert MIG welding gases and prevent oxidization taking place.
Pure argon is frequently used as a shielding gas to achieve excellent aluminium welds. As such it is the most common shielding gas for aluminium welding, .
We must take into account the distinctions between argon and argon helium mixtures when deciding on a shielding gas for welding aluminium.
Helium shielding gas has a substantially greater ionisation potential and thermal conductivity than argon. When welding with the inclusion of helium in the shielding gas, these properties result in a higher heat output.
With pure argon shielding gas, the finished weld usually has a brighter and shinier look to it. It is common practise to do post-weld wire brushing on a helium/argon mixture weld in order to get a comparable surface look and finish. It is possible that aluminum’s strong heat conductivity will result in an unsatisfactory fuse. Using helium shielding gas combinations can assist avoid partial fusion and incomplete penetration due to the additional heat potential of these MIG welding gases . Click here for a more detailed analysis of the correct shielding gas to use for welding aluminum.
The best gas for MIG welding stainless steel?
Because of the make up of stainless steel, an iron-chromium alloy made up of at least
at least 11% chromium and also containing silicon, nickel, manganese, titanium among other elements. Because of this, it usually requires a slightly more complicated mix of MIG welding gases in order to produce the best results.
As we have seen argon or argon/helium-based combinations are commonly used in MIG welding, which uses a solid wire.These gases also need to contain a small amount of an oxidising gas, such as oxygen or carbon dioxide, in order to regulate the arc.
Low carbon stainless steels (sometimes referred to as “L” grade stainless steels) may only be used with around 3% of the permitted carbon dioxide for burning.
More on shielding gases for welding stainless steel can be found here.
When MIG Welding, what is the proper gas pressure?
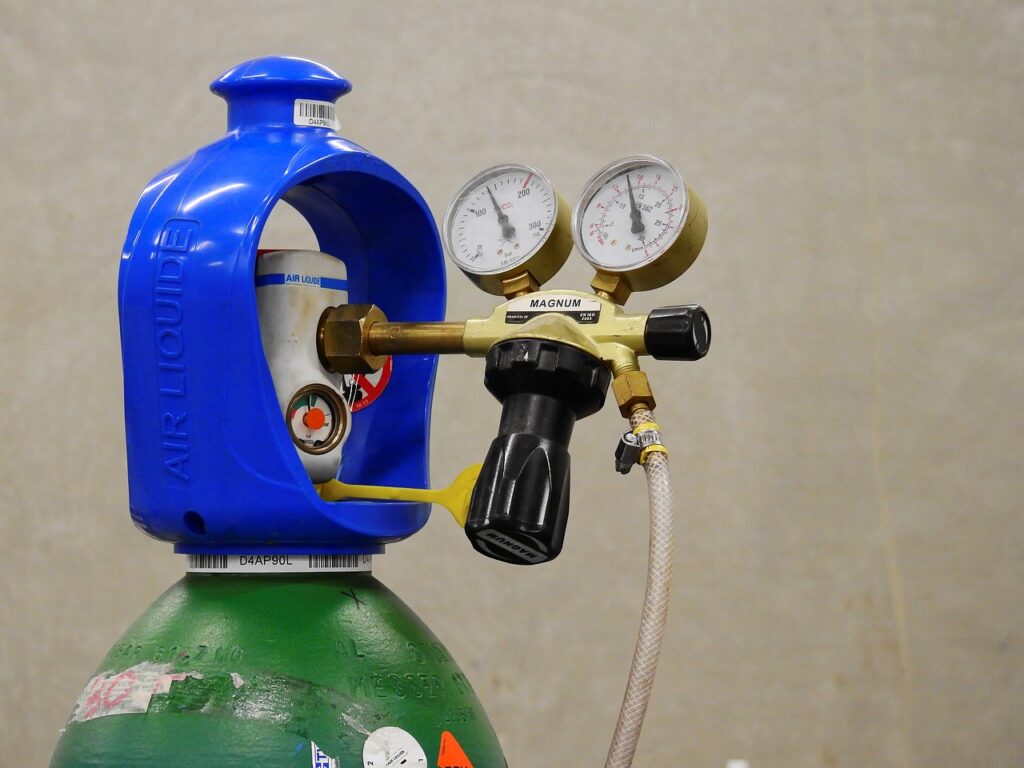
With MIG welding gases gas pressure or flow are two phrases that are sometimes misunderstood, is the most important factor in your weld.
The first thing you need to know about welding is that there is a right level of pressure and a wrong level of pressure. If you have too little pressure, then the arc will be unstable and it won’t stay on long enough to melt the metal. Too much pressure can cause the wire to burn through before the molten metal has time to cool.
In general, we recommend using at least 1/2 inch of pressure when welding with MIG welding equipment. This means that the gas should be flowing at a rate of at least 500 cubic inches per minute . For example, if you use an air-operated gun with a 4 CPM fan, you’ll get 3/4 inch of pressure. A 5 CPM fan gives you 1 inch of pressure.
If you’re welding aluminum, stainless steel or other metals that require higher temperatures than those used by MIG welding, you may want to increase the pressure even more. You might consider using as high as 2 inches of pressure.
How Much Gas Should I Use When Welding With MIG Equipment?
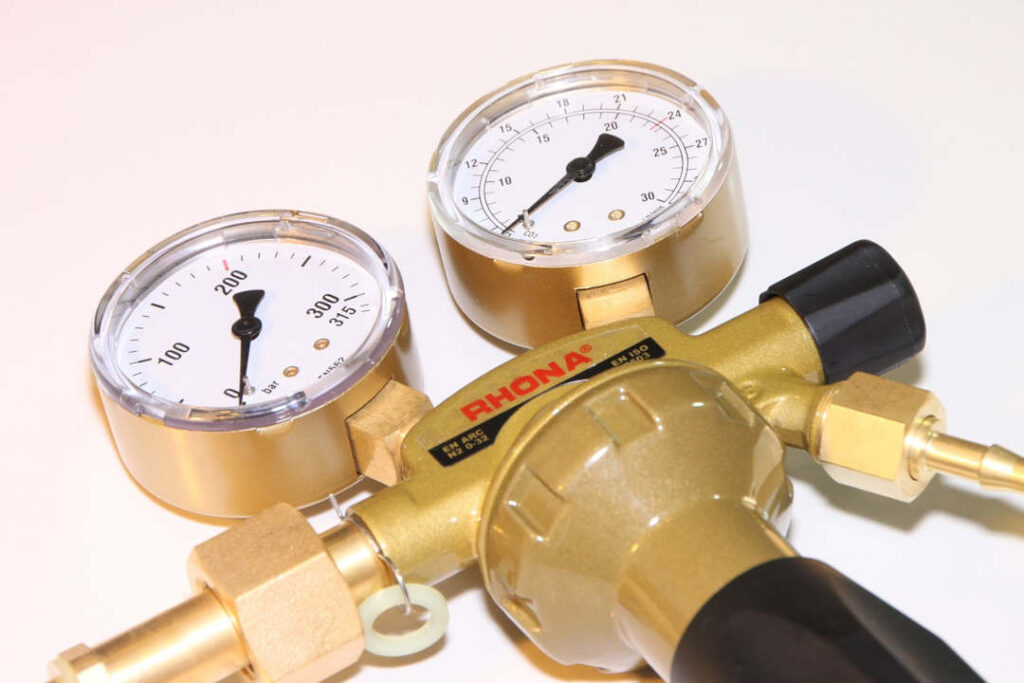
There are several factors to consider when determining how much MIG welding gases you should use.
- First, you must determine whether you’re working with thin materials such as sheet metal or thick materials like pipes. Thin materials need less gas because they don’t take up as much space. Thick materials need more gas because they take up more room.
- Second, you must decide whether you’re working with a single pass or multiple passes. Single-pass welding uses less gas than multi-pass welding because you only heat one side of the material.
- Third, you must decide whether the weld area is large or small. Large areas need more because they cover larger amounts of surface area. Small areas need less gas because they are smaller and therefore take up less space.
- Fourth, you must decide whether or not you’re using filler rod. Filler rod adds weight to the weld puddle and increases the amount of gas needed.
- Finally, you must decide whether your workpiece is hot or cold. Hot workpieces need more gas because they absorb more energy from the arc. Cold workpieces need less gas because they absorb less energy from the arc.
Following are some guidelines that should help in your ability to determine how much MIG welding gases you should be using when welding with MIG equipment.
Single Pass vs Multiple Passes
A single pass is when you weld all of the pieces together in one go. In this case, you’d use the same amount of MIG welding gases regardless of the size of the weld area. However, you would need to adjust the gas flow accordingly so that the weld doesn’t blow out.
Multiple passes are where you make multiple passes over the same spot. Each pass covers a different part of the weld area. In this case, the amount of gas you use depends on the size of the weld.
For example, let’s say you’re making a 10 foot pipe. To do this, you would start at one end of the pipe and move along the length of the pipe. As you approach the end of the pipe, you would stop and begin again at the beginning. The first time through, you would use half the amount of gas you would normally use for a single pass. Then, as you come back around to the beginning, you would use twice the normal amount of gas. By doing this, you would have covered 50% of the weld area. Next, you would repeat the process until you had completed the entire weld area.
The total amount of MIG welding gases you would use for a 10 foot pipe would be:
10 feet x 0.5 5 gallons
10 feet x 1 15 gallons
10 feet x 2 30 gallons
Total 55 gallons
This is an average of about 11/2 gallons per foot. This number can vary depending on the type of material being welded, the thickness of the material and the size of the weld joint.
How to Get Shielding Gas to the Weld Pool
Choosing the correct shielding gas might be a waste of time if you can’t get the gas to the weld area. Protecting the weld pool is dependent on the consumables for MIG guns (diffuser, contact tip, and nozzle).
The contact tip is positioned in the diffuser and kept in place by the splatter guard inside the nozzle in this cutaway view of a consumable system.
It’s possible that too little shielding gas will reach the weld pool when you use a nozzle that’s too small or when the diffuser is clogged with spatter. Additionally, a poorly built diffuser might result in a turbulence and imbalanced gas flow. Excessive spatter, porous welds, and contamination are all possible outcomes of each of these situations.
Consumables for MIG guns should be resistant to spatter buildup and have a wide enough nozzle diameter to give appropriate shielding gas coverage, therefore look for them while shopping. It is possible to buy spray guns that include both a built-in splatter guard and additional shielding gas diffusion. This improves shielding gas flow even further, making it much more constant.
The sort of welding you undertake and your operational priorities must be carefully analysed in order to select the best shielding gas for your particular application. Learning may get off to a good start by following the suggestions provided above. Before making a final selection, speak with your local MIG welding gases supply distributor.
MIG Welding Gases: Conclusion
With a variety of MIG welding gases and gas combinations, it is possible to weld aluminium. The decision is generally made depending on the unique use case. Helium-rich gases are often utilised for MIG (GMAW) welding on thicker materials. Pure argon is the most often utilised shielding gas for non ferrous welding. MIG welding gases with higher concentrations of helium tend to be more costly.
Higher flow rates are required when welding with Helium because of its lower density than argon. Helium and/or helium/argon mixes can be used to speed up welding in particular situations. Helium mixes are more expensive, but your increased production may make up for the additional expense.
In terms of ferrous metals carbon dioxide or an argon carbon dioxide mix are the most common gases used. Much of course will depend on the actual material being welded. Although cheaper than pure argon or argon helium mix the addition of carbon dioxide produces more splatter and could depending on the finish required add to post weld clean up time, slowing down productivity.
You should experiment with the various MIG welding gases to find the one that best suits your needs.
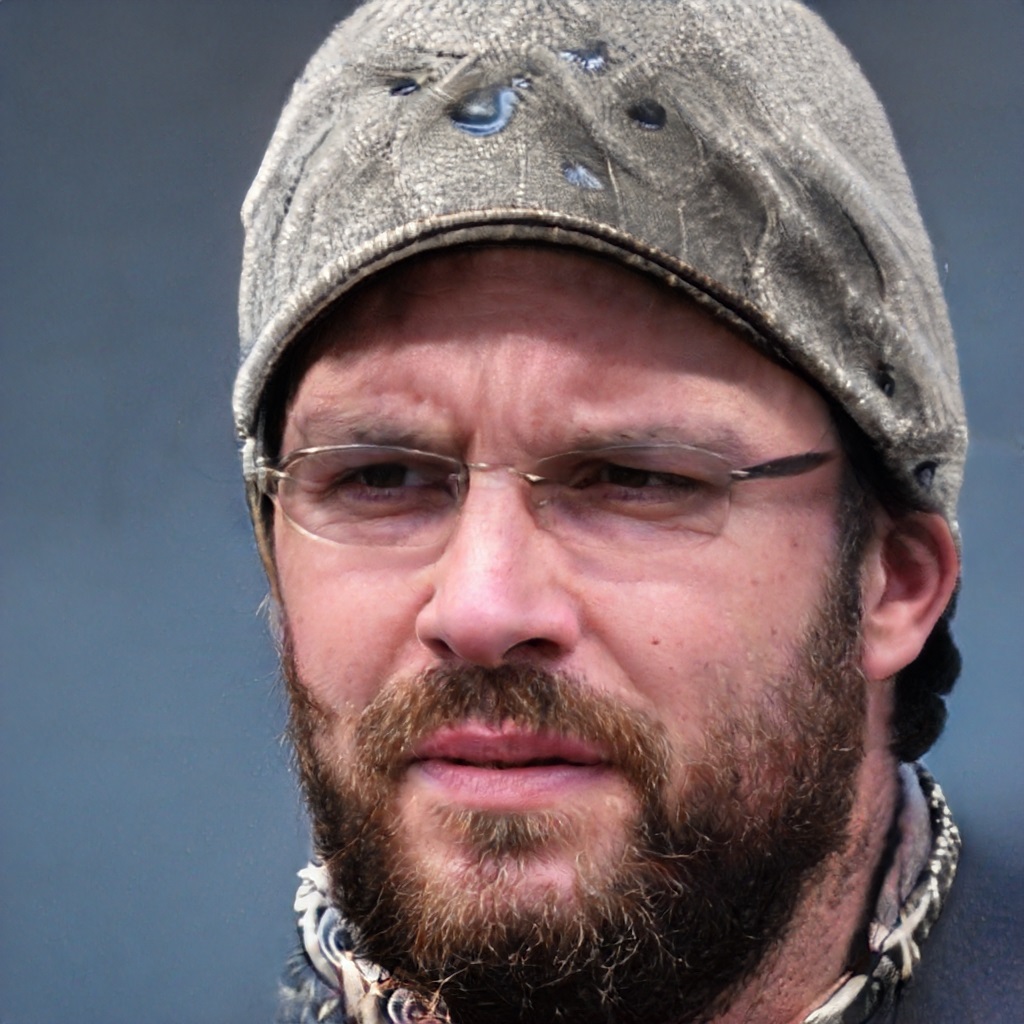
I’ve been involved in the welding industry for over twenty years. I trained in various engineering shops working on various projects from small fabrication and repairs through to industrial projects.I specialize in welding aluminum and food grade stainless steel and an now run an engineering shop fabricating equipment for the food industry.