MIG Welding Nozzles Everything You Need to Know
americanindustrialsupl and its partners may earn a commission if you purchase a product through one of our links.
MIG welding nozzles, everything you need to know – In this article we will look to explain the intricacies of MIG welding nozzles and show you how to choose the right nozzle for the welding task at hand.
MIG Welding also called gas metal arc welding, or GMAW for short.
MIG Welding Nozzles – Introduction
To successfully weld metals together, a welder requires the right equipment. The maker needs to be able to apply heat, pressure, and filler material during the process to create the desired shape. The welder also needs high-quality tools that can handle the job at hand.
A welding torch for a MIG machine is composed of several consumable parts. One such part is the welding nozzle. The end of a welding torch, is one of these, and is something that a welder cannot be without. The welding nozzle directs gas into the weld puddle and also protects the contact tip from molten metal. Different nozzles exist and a torch can be fitted for certain types to accomplish desired results and effects.
The design of welding nozzles is important, because it determines how the shielding gas will be directed into the weld puddle. The best nozzle choice will depend on your application, joint access and the process. The gas coverage, the access and the reamers efficiency vary according to the nozzle design.
The type of welding process you employ will affect the type of nozzle you should use. Whether you weld in spray, pulse, or short circuit will largely influence the nozzle design you should use for your process.
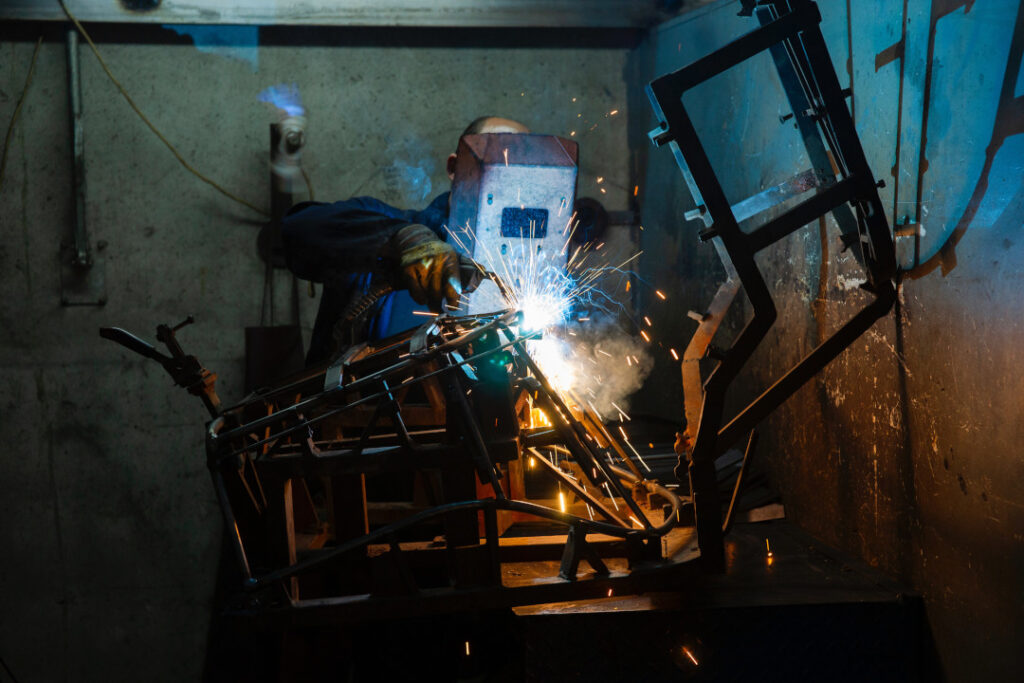
MIG Welding Nozzle Types
Unfortunately, the necessity of choosing the proper nozzle, like other MIG welding consumables, is frequently ignored. The correct form and style of nozzle, in any welding application, may have a major influence on the quality, productivity, and total cost of the welding process. Knowing how to store and use nozzles correctly will also help them work better.
When considering welding nozzle, it is important to think about the joint needing to be welded. That’s because different types of weld require different gas coverage. With MIG welding, a shielding gas is used. MIG nozzles pushes the shielding gas into the weld puddle in order to prevent the puddle from being contaminated.
The construction of MIG welding nozzles
The majority of your MIG gun welding nozzles will be made of brass or copper. Brass welding nozzles offer superior spatter resistance than copper welding nozzles in lower amperage applications, but typically lack that superiority in higher amperage uses and can break if they fail. At higher temperatures, copper welding nozzles offer greater general spatter resistance and heat control.
Nickel-plated welding nozzles (shown separately) have greater endurance and spatter resistance than ordinary copper and brass nozzles. You should always anticipate nickel-plated welding nozzles to be plated on a copper nozzle, so you get all the good durability properties of copper as well as outstanding spatter resistance. Nickel-plated welding nozzles last longer than ordinary copper nozzles because nickel’s characteristics deflect rather than absorb heat, allowing the interior and outside of your welding nozzle to stay cooler while your MIG gun is running. This causes less splatter to adhere to the nozzle, extending its life.
Finally there are ceramic welding nozzles. These are a more recent development and less frequently used than brass, copper, or nickel-plated nozzles. There main benefit is that they are designed to be more resistant to intense heat and protracted use.
Nozzles come in a variety of types, including heavy-duty and regular versions. Heavy-duty nozzles feature stronger walls and insulators, and are suitable for applications with currents ranging from 400 to 600 amps. These nozzles are more heat resistant than regular types due to their heavier structure. Regular nozzles have a narrower wall and are ideal for applications requiring 100 to 300 amps.
MIG welding nozzles – slip-on and thread-on connection type
When it comes to deciding whether to use threaded or slip-on nozzles, it will most likely be determined by the type of MIG welding gun you have, since some can only accommodate one or the other. Threaded nozzles that must be twisted to install but will attach more firmly to the torch, reducing gas leakage. The downside is that they sometimes might be difficult to take off.
Slip-on welding nozzles easily slip on to the front end of the MIG gun , as the name indicates . They are also more suited for overhead welding applications since they create significantly more spatter, notably at the base of the MIG gun’s neck. As they are simpler to remove a slip-on nozzle protects your other consumables such as your diffuser during replacement.
Slip-on nozzles are also generally less expensive than threaded nozzles, owing to their single-piece design as opposed to threaded, which are typically two-piece structure and require additional machining for the threads.
To keep the welding nozzle or tip holder tight to the torch when welding, a tension band of some kind is usually placed at the base. These rings can sometimes become loose, causing the nozzle to shift which means that the nozzle might become dislodged at times, causing objects to sit off-center.
Slip-on nozzles are usually not a suggested consumable for robotic welding applications since they do not work well with reamers . This is because the nozzle can rotate with the reamer blade when in cleaning phase.
MIG Welding Nozzle Shapes
Irrespective of whether the welding nozzle is slip-on or threaded there are several nozzle shapes to select from, each of which will have an effect on the welds being worked on.
Conical MIG Welding Nozzles
In hand welding, a conical-shaped welding nozzle provides excellent gas coverage while yet giving enough vision. The shielding gas covers a somewhat larger area surrounding the weld puddle due to the (inner) conical shape than other nozzle designs. The shape also accelerates gas into the weld puddle, which helps to minimise disturbance and ambient factors from influencing the weld.
Conical welding nozzles are the preferred nozzle form when welding zinc or zinc-coated metals. Because zinc produces very big and violent spatter when welded, and the space given by the base of the conical welding nozzle enables it to be reamed more efficiently than some other nozzle shapes presuming a two-stroke reaming procedure with air blast.
A disadvantage of conical-shaped welding nozzles is that they are less accessible around tools than bottleform welding nozzles. A further issue that might arise is a decreased reamer cleaning efficiency when utilising a torch cleaning station in robotic welding. Because the nozzle’s inner wall is cone-shaped and the reamer blade is straight, weld spatter can accumulate on the inner wall and limit gas coverage. This may be handled with adequate anti-spatter coating and a one-piece conical nozzle design.
Another essential factor to consider with your nozzle is the contact tip outer diameter in relation to the inner diameter of your welding nozzle. If you’re using a 12mm inner diameter nozzle, for example, you may safely utilise an 8mm outer diameter contact tip since you’ll have sufficient gas space to adequately fully cover your weld. If you utilise a big contact tip, such as an M10 or M12, you risk decreasing your gas flow and, as a result, porosity in your welds, as well as spatter bridging.
Bottleform MIG Welding Nozzles
This type of nozzles has a smaller exterior diameter on the work end stepping in like the neck on a bottle. Bottleform Nozzles provide for easy view and access to the work item. When compared to other nozzle designs, gas coverage is narrower, which puts them at a larger risk of contamination.
In robotic applications, the bottle neck part of the nozzle is generally a straight bore, allowing for efficient and effective cleaning using a torch cleaning station. This is why, despite their difficulty in reaming due to the tiny aperture, bottleform nozzles are frequently utilised in robotic applications.
When employing bottleform nozzles, the possibility of splatter bridging rises. As a basic guideline, the tighter the front end of the welding nozzle is around the tip and tip holder, the more likely it is to experience quicker spatter accumulation.
You can also get Tapered Nozzles. These nozzles work on the same principle as the Bottleform Nozzle but with a lower bore size, are also available. These are designed for exceptionally tight access applications such as pipe welding or exceedingly tight corners.
Cylindrical MIG Welding Nozzles
Because of its huge, straight bore, a cylindrical welding nozzle is also known as a straight nozzle. Because they can withstand surges in gas flow, these nozzles are often employed on higher-amp welds. They do have some accessibility limitations. They are often the go to option if welding with large contact tips like M10 or M12 heavy duty size.
When welding at high parameters with an M10 contact tip, you want as much space between the contact tip and the nozzle wall as feasible to fit the contact tip while also allowing as much gas to flow in as possible. Because they can sustain huge spikes in gas flow without producing porosity, cylindrical welding nozzles are also ideal for high amperage applications.
As cylindrical welding nozzles have a wider straight bore, they produce the finest nozzle reamer cleaning results around the tip, tip adapter, and internal gas nozzle parts.
The main issues with cylindrical MIG welding nozzles is in terms of accessibility as well as contact tip selection. M6 and M8 type contact tips are generally not recommended for use with cylindrical nozzles. Using a tiny contact tip with a nozzle that offers so much space might result in too much gas entering the weld puddle and causing porosity.
Contact Tip Placement
Generally, the tip location is determined by the nozzle used by some manufacturers. The tip placement on the welding nozzle you select should be appropriate for the welding type of your project. When MIG welding in spray, short circuit or pulse modified pulse modes can have a significant impact on the nozzle design suggested for your operation.
Recessed Contact Tips
Recessed contact tips are designed to be used with wires that have a longer stick-out. When utilising a recessed welding nozzle, you will typically be welding in spray or pulse mode – in other words, whenever you are welding at higher amperages.
The reasoning for this is that a recessed nozzle allows the contact tip to lie further within the nozzle, providing more gas cover to the weld.
A recessed nozzle allows gas to encompass the contact tip and flow to the weld piece while MIG welding at high current. This ensures that the correct quantity of gas is applied to the weld and prevents porosity.
Flush Contact Tips
MIG welding in short circuit mode is generally done with a flush welding contact tip. As a result, you don’t need while much wire stick-out, which helps you to see where the wire is going as you weld. Using a flush nozzle means you have improved visibility on your component, which is very useful for hand MIG welding.
One of the few disadvantages of a flush nozzle is that because the contact tip is in direct touch with the bore of the welding nozzle, it can cause spatter bridging if not cleaned periodically or treated with an anti-spatter solution.
Protruding Contact Tips
Protruding contact tips are welding nozzles that let the contact tip to extend from the nozzle exit point, allowing the contact tip to reach or even touch the work-piece before the nozzle. This sort of welding nozzle should only be used when you need to go from your flame to your weld piece.
In general, you’d use a Protruding nozzle if you were MIG welding in a tight corner or deep down into a section that you couldn’t reach otherwise. Because of the openness of the contact tip, gas coverage with stick-out nozzles is reduced, therefore stick-out nozzles actually only operate as designed when welding in an area where gas may pool.
Storage, Handling and Maintenance of MIG Welding Nozzles
To achieve constant welding performance and avoid early failure, nozzles must be handled, stored, and maintained correctly. Choosing high-quality nozzles can also allows the welding nozzle to have an extended life.
Opt for nozzles with a smooth surface finish and edges, since they will withstand spatter build-up better than nozzles with an irregular surface or burrs on the edges. Nozzles with considerable bulk are also preferred over lighter or thinner ones because they tolerate heat better. Consider getting nozzles with a brass insert as well. This component assists the nozzle in maintaining its inner diameter and prevents the nozzle from swaying and excessively wearing.
Storage of MIG Welding Nozzles
It is always best when storing your welding nozzles to keep nozzles them in their original packaging, which is generally a tiny plastic bag. Removing them from their box and storing them with other items might cause scratches or dents that enable splatter to attach and, as a result, reduce the life of the nozzle. When handling or replacing nozzles, use gloves to avoid dirt, oil, or other pollutants from clinging to them and unintentionally infiltrating the weld puddle.
Maintenance of MIG Welding Nozzles
Ensuring that your MIG welding nozzles clean will prevent dirt and other foreign bodies from entering the weld puddle by accident. Examining nozzles for spatter accumulation and cleaning them with approved equipment or anti-spatter solution is the best method to keep them appearing and working to the highest of standards.
Nozzles, like any other front-end consumable, are critical to maintaining excellent weld quality and may have a quantifiable influence on productivity and costs. Take the effort to choose the best ones for each purpose and to properly maintain them. In the long term, careful selection and maintenance may save downtime and keep your welding process operating more smoothly.
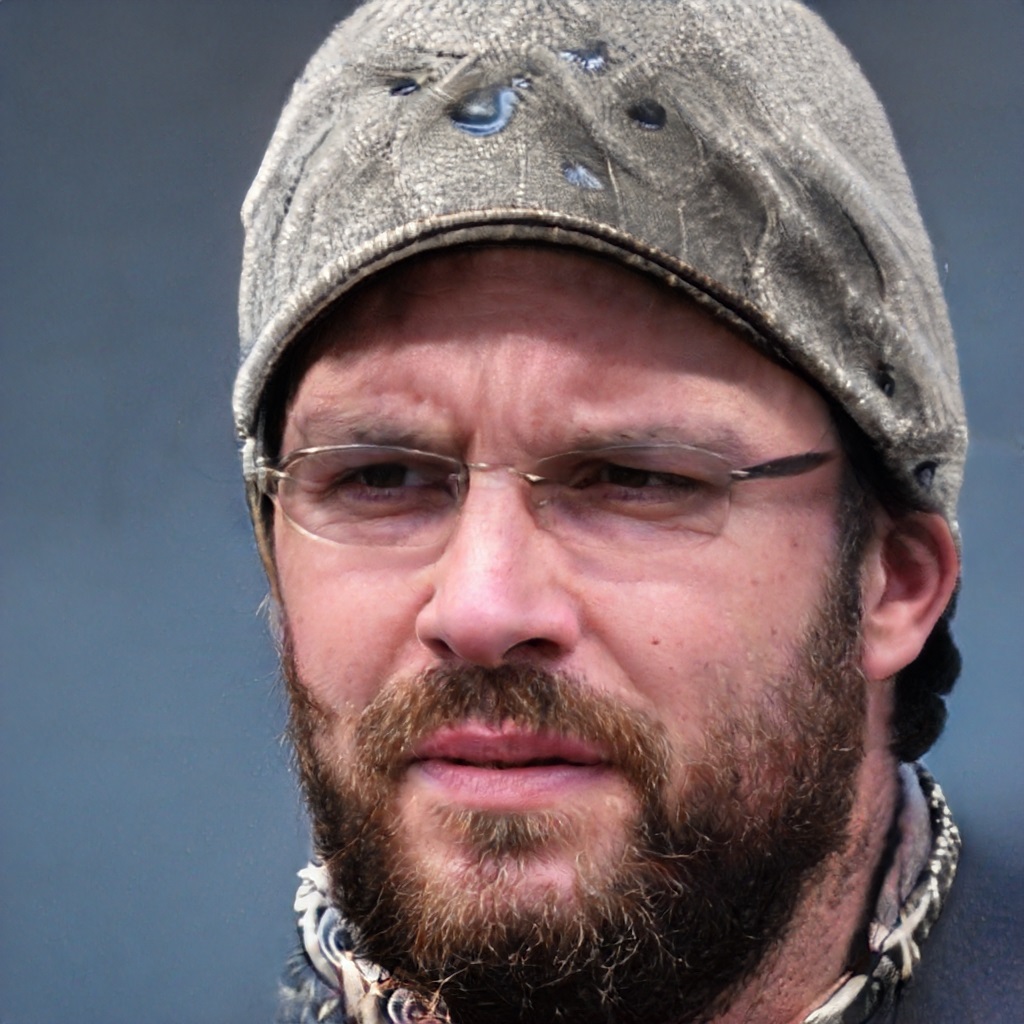
I’ve been involved in the welding industry for over twenty years. I trained in various engineering shops working on various projects from small fabrication and repairs through to industrial projects.I specialize in welding aluminum and food grade stainless steel and an now run an engineering shop fabricating equipment for the food industry.