How to MIG Weld Without Gas (Flux Core MIG Welding)
Whether you’re a homeowner trying to repair your roof or a professional steelworker trying to get your job done there are going to be times when you might need to weld without using gas. There are various different ways of welding with the use if a shielding gas and each has its own drawbacks.
Generally speaking, you are probably going to have to utilize the equipment at hand and with MIG being the most commonly used welding method knowing how to MIG weld without gas is going to be useful.
The good news is that it is eminently doable, however it does takes a level of skill to execute well. Following, we will explore how to MIG weld without gas, look at the equipment required and techniques for achieving the best results.
Reasons to Consider Welding Without Gas
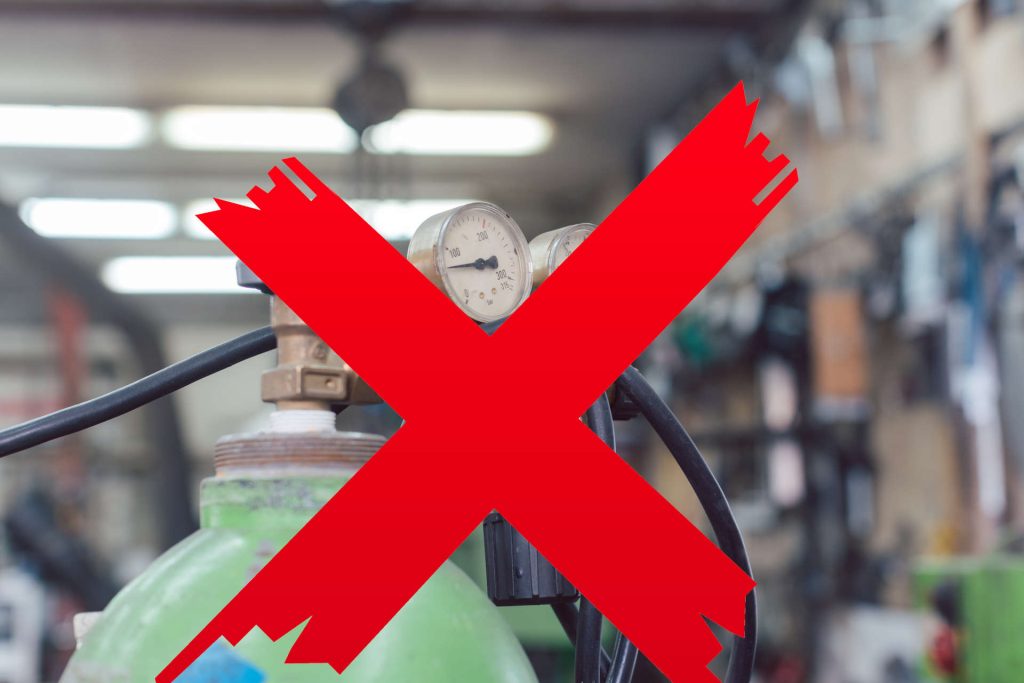
If just starting out the cost of gas bottles can be prohibitive so the question is are there a welding process that you can use that eliminates the need for gas?
It’s a question that many new welders wonder: how can I get started welding without the use of gas? The answer is, there are actually different types of welding that you can use, and different versions of those types of welding.
For example, if you are looking for an alternative to gas welding then you could try flux cored arc welding (FCAW) where a wire element is used instead of a coiled electrode. This type of welding can also be done on aluminum, stainless steel and cast iron with very little change in heat treatments.
Types of Welding
MIG welding is widely used in the manufacturing industry, especially with metals like steel. In fact, it’s the most commonly used method of welding at industrial plants and shipyards around the world. But what if you’re not able to get access to gas?
MIG welding without gas is called flux cored MIG welding. In essence though it is no longer MIG welding but lux-cored arc welding. We refer to it as such because your are using the same equipment just different polarity settings and flu cored wire.
Probably the most common method is welding without gas with stick welding. Stick welding is a gasless welding process which uses a flux coated electrode to shield the the weld from contamination.
A TIG (tungsten inert gas) welding machine can also be used and TIG welding without gas is often referred to as flux cored TIG welding. The main difference between these two methods is the machines used. While TIG welders generally require a shielding gases, flux cored wire can be used. The process is slight more difficult using a TIG machine .
Does MIG Welding Require Gas?
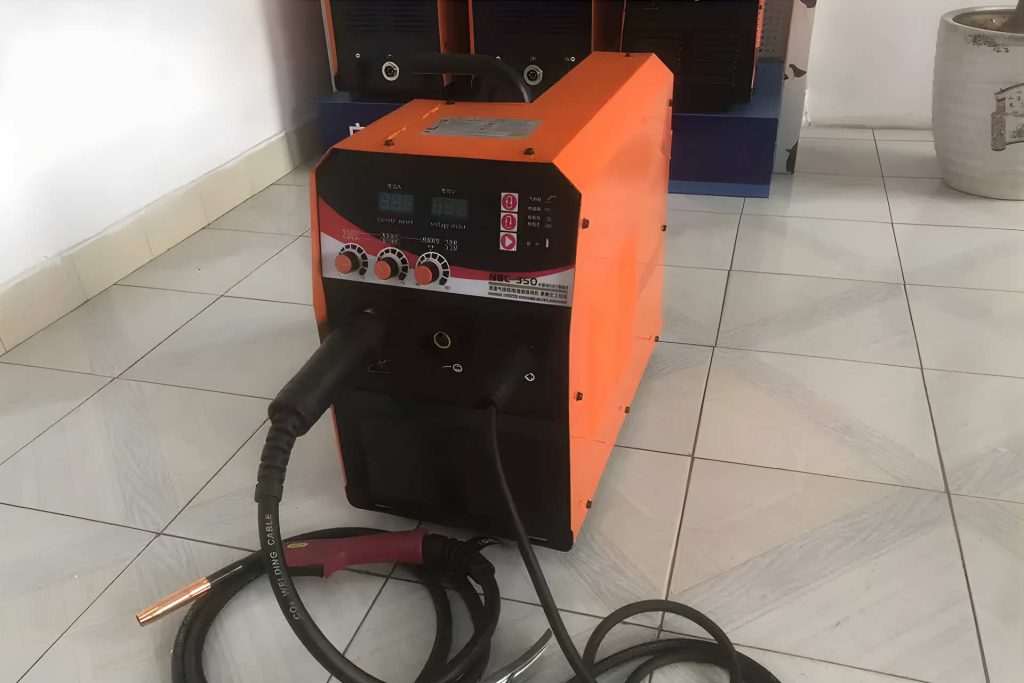
MIG welding without gas is possible, but you will need to use a different method. The solution is known as flux core MIG welding.
Flux core welding, also known as gasless MIG welding, is a process that allows welders to weld without using any external shielding gas. This is achieved through the use of a flux-cored wire, which creates a protective gas while the wire is melting.
Flux core welding can be used on a variety of metal types and thicknesses, such as welding galvanized steel, although it is not suitable for all welding applications. In comparison to MIG welding with gas shielding, flux core welding may produce more spatter and result in a rougher looking weld. However, flux core welding is generally easier to learn and use, and it can be a cost-effective option for those just starting out in welding or for those who do not have access to a gas cylinder.
It should be noted that while flux core welding does not require the use of an external shielding gas, it is possible to use Argon or a combination of Argon and carbon dioxide with flux core wire for improved results. However, this may not be necessary for all applications and can add additional cost.
Selecting the Correct Flux Core MIG Welding Wire
When selecting a flux core MIG welding wire, it is important to consider the specific needs of the project. Different types of flux core wire are available for welding a variety of materials, including mild steel, stainless steel, and aluminum. Additionally, different wire diameters and flux compositions can be used to achieve different welding characteristics, such as increased penetration or reduced spatter.
Safety Equipment When MIG Welding Without Gas
- Fire Retardant Clothing, welding jacket, gloves and a hat are essential to prevent burns from touching the hot metal.
- Make sure you use a welding shield to protect yourself from flying debris when welding without gas. The protection offered by shields can be quite important when working with flammable materials such as aluminum or magnesium. A good shield should also protect against radiation exposure so that you don’t get burned by electromagnetic fields during your welding process.
- Always wear eye protection when using MIG equipment because it may produce sparks or splatters of molten metal which could burn your eyesight if they come into contact with them during any part of this process.* Respiratory Protection – wear a respirator! Don’t forget it!
Preparing the Metal Before Welding
When you’re welding, your finished quality of the weld is never going to be perfect unless you take some steps to prepare. First, clean the metal by removing all rust and dirt with a wire brush or other suitable tool. Sand and grind away any surface oxides that might be present on the metal. Remove any oil or grease from the surface of your work piece by wiping it with an oily rag until everything has been removed from its surface.
Next, smooth out any uneven areas with a file or sandpaper before proceeding with welding operations; this will help prevent tearing in your final product!
Preparing Your MIG Welder
Before you start welding without the use of gas, there are a few things that you need to do. First off, make sure your welder is set up for gasless welding. It can be difficult to tell if your welder is set up correctly or not.
It is essential to check the voltage setting on your welder’s control box and make sure it reads between 120VAC-240VAC (50/60 Hz). Next stop by getting some scrap material from another project or even spare material from yours! This will help you practice before starting on the main project so when it comes time for actual welding with an actual dollar amount attached…you’ll be ready!
Following this, check out what type of tip contacts are available for use in this machine; if none exist then look into buying one separately though these may be fairly expensive depending on which brand they come from so shop around first before making any decisions toward purchasing anything specific here – especially since this might take place several months down line after purchasing said item(s).
Where Flux Core MIG Welding is Commonly Used
Flux core MIG welding has a wide range of applications across different industries, owing to its versatility and cost-effectiveness. Here are some of the best applications for flux core MIG welding:
- Structural Steel Welding: Flux core MIG welding is commonly used for welding structural steel, including beams, columns, and trusses. The high deposition rates and deep penetration of flux core wire make it ideal for welding thick sections of steel, which are common in structural applications.
- Shipbuilding: Flux core MIG welding is also popular in shipbuilding and other marine applications. The high deposition rates of flux core wire can help reduce welding time and increase productivity. Additionally, the ability to weld in windy or outdoor conditions makes flux core MIG welding a preferred method for shipbuilding and repair.
- Automotive and Trailer Manufacturing: Flux core MIG welding is widely used in automotive and trailer manufacturing, particularly for welding chassis and frames. The high deposition rates and deep penetration of flux core wire can help reduce welding time and increase productivity, making it a cost-effective option for high-volume production.
- Oil and Gas Pipeline Welding: Flux core MIG welding is also used in oil and gas pipeline welding, particularly for welding high-strength materials such as X80 and X100. The deep penetration and high deposition rates of flux core wire can help produce strong and reliable welds on thick-walled pipes.
- Repair and Maintenance: Flux core MIG welding is also popular for repair and maintenance work, particularly in outdoor or windy conditions. The ability to weld without an external shielding gas can be particularly useful for on-site repairs and maintenance, where access to a gas supply may be limited.
Flux core MIG welding is particularly useful in outdoor or windy conditions, where a traditional MIG welder may struggle to maintain a consistent gas shield. Additionally, flux core MIG welding can be more cost-effective than traditional MIG welding because it eliminates the need for an external gas supply.
Common Problems When Welding Without Gas
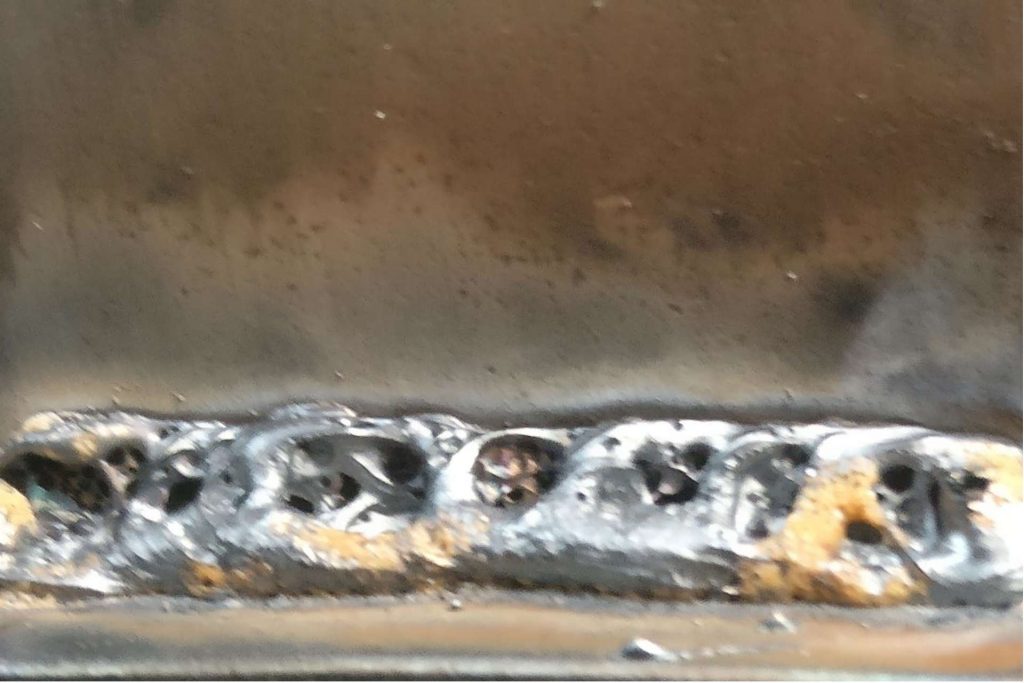
- Porosity or Worm Holes
- Slag Inclusion
- Undercut Along the Toe of the Weld
- The arc length is too short
There are several issues that can occur when welding without gas. One problem, porosity or worm holes, occurs when there’s not enough penetration into the material being welded. This can be caused by a lack of arc length or insufficient heat transfer to fuse two pieces together properly.
If you’re having trouble achieving good fusion across your joint and you’re using an oxyfuel torch instead of an MIG welder, try increasing your setting on your torch to increase its duration so that more heat gets transferred from it into your work piece before it begins melting through them (this will require more oxygen).
Another common issue with welding without gas is slag inclusion within the joint itself; this occurs when there isn’t enough fluxing agent in between plates being joined together during their fusion process as well as following removal from each other once done which results in smaller particles being left behind after cooling down again later down further still due again mostly because there wasn’t enough time spent letting things cool off before removing them again..
Summary – How to Weld Without Gas Using MIG
While MIG welding can be done without gas. In essence though it is no longer MIG welding but lux-cored arc welding. We refer to it as such because your are using the same equipment just different polarity settings and flu cored wire.
There are some important things to keep in mind to ensure it’s safe and successful. We’ve talked about what you need to know about safety equipment and preparing your metal before welding with this method, but the most important thing is getting proper training from a shop that specializes in MIG welding without gas. Once you have that down, you’re all set!
FAQs
What welding does not require gas?
The most common method of welding without gas is stick welding. Flux core welding (also known as gasless MIG welding) is another welding method that does not require the use of an external shielding gas. You can also use flux-cored TIG Welding as an alternate process but this can require more experience as it requires a reasonable skill level to accomplish well.
Can you weld with just electricity?
No, welding requires both electricity and a source of heat (such as an electric arc or a gas flame).
Are gasless welders any good?
Gasless welders can be a good option for certain applications, but they may produce more weld spatter and result in a rougher looking weld compared to MIG welding with gas shielding.
Can you use solid core wire without gas?
No, solid core wire requires the use of an external shielding gas.
Can you MIG weld with just oxygen?
No, MIG welding requires a shielding gas in order to protect the weld pool from contamination. Oxygen cannot be used as a shielding gas.
Is gasless MIG easier than stick welding?
It is subjective whether gasless MIG welding is easier than stick welding. Gasless MIG welding may be easier to set up and use, but stick welding can be more forgiving of operator error and may be more suitable for certain applications.
Is stick welding stronger than MIG?
It is also subjective whether stick welding is stronger than MIG welding. Both methods have their own strengths and limitations, and the choice of which one to use will depend on the specific requirements of the application.
Can you cold weld without gas?
Cold welding does not require the use of heat or electricity, but it can only be performed on certain types of metal with close-fitting, clean surfaces. It is not a welding method that is commonly used in industrial or commercial applications.
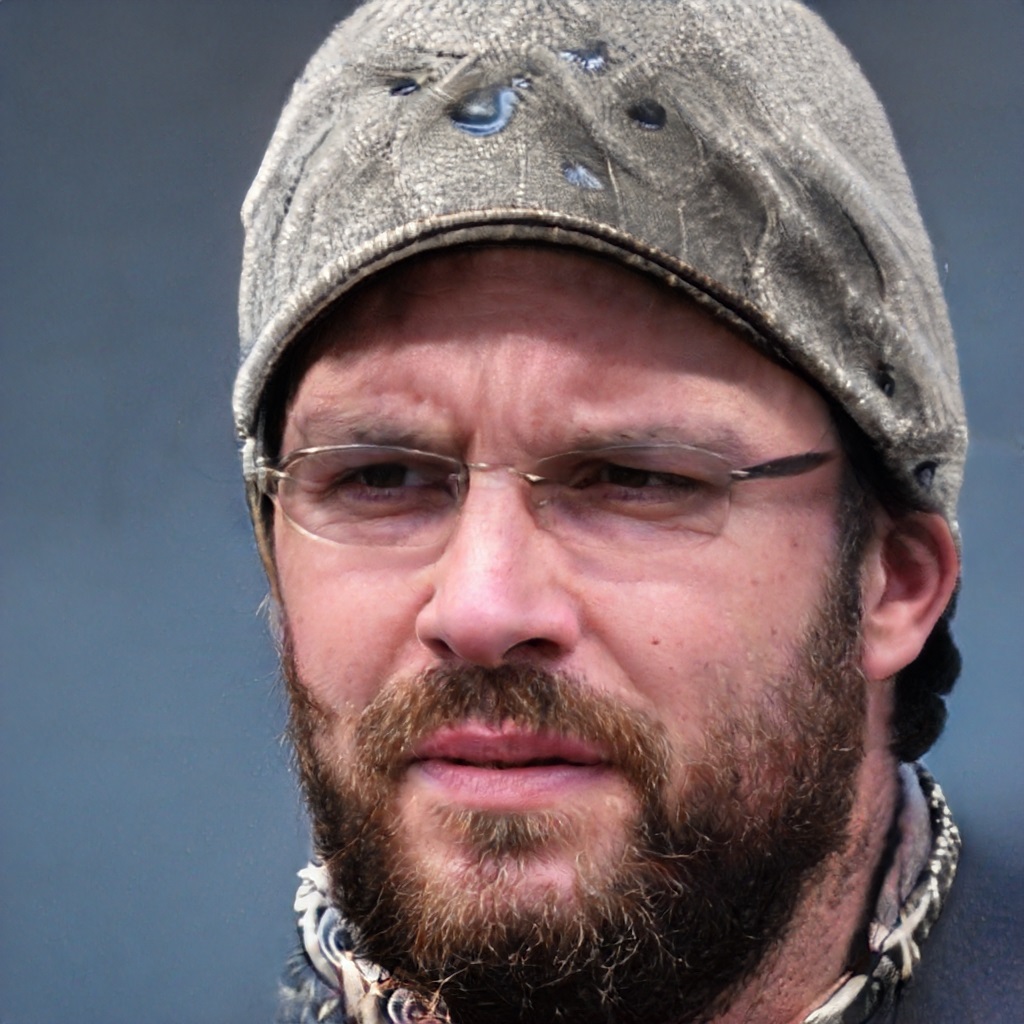
I’ve been involved in the welding industry for over twenty years. I trained in various engineering shops working on various projects from small fabrication and repairs through to industrial projects.I specialize in welding aluminum and food grade stainless steel and an now run an engineering shop fabricating equipment for the food industry.