Selecting the Best Flux Core Wire for Welding Stainless Steel
americanindustrialsupl and its partners may earn a commission if you purchase a product through one of our links.
Flux core welding can be a very effective method for welding stainless steel. However, the quality of the weld can be adversely affected unless you select the best flux core wire for welding stainless steel material.
Below, we will explain the key factors you need to consider when choosing flux core wire for welding stainless steel, the advantages and disadvantages of using flux core wire as a whole for welding stainless steel, and look at the differences between solid wire and flux core wire.
Finally, we will provide some tips and tricks to help you achieve optimal results with flux core welding on stainless steel.
The Best Flux Core Wire for Welding Stainless Steel
Flux Core Welding Stainless Steel
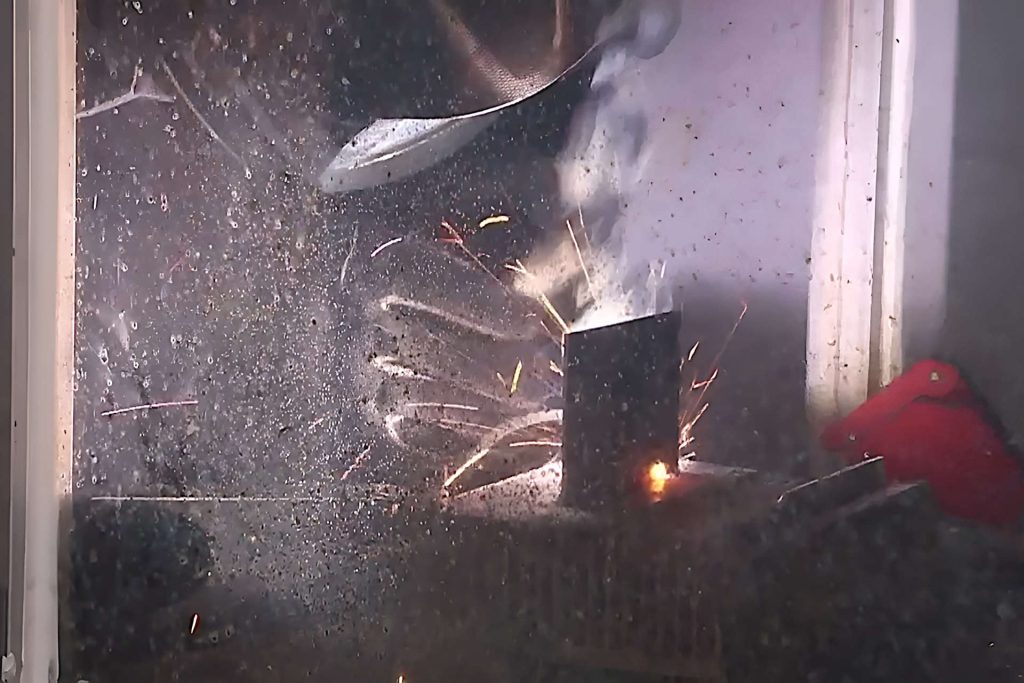
One of the most common methods of welding stainless steel is gas metal arc welding (GMAW), also known as metal inert gas (MIG) welding. GMAW, though, has some limitations when it comes to welding stainless steel. For example, it requires a gas cylinder and a regulator, which can be expensive and cumbersome to transport.
It also requires a clean and dry work environment, as any moisture or dirt can affect the quality of the weld. Moreover, it can be difficult to control the heat input and penetration with GMAW, which can lead to distortion, cracking, or porosity in the weld.
Many welders prefer to use flux core arc welding (FCAW) to MIG, also known as flux cored wire (FCW) welding. This process uses a tubular wire electrode that has a flux-filled core that generates a shielding gas when it burns. The flux also provides deoxidizers and alloying elements that improve the weld quality and appearance. FCAW can be either self-shielded or gas-shielded, depending on whether it requires an external gas supply or not.
Advantages of FCAW Over GMAW when It Comes to Welding Stainless Steel
FCAW has several advantages over GMAW when it comes to welding stainless steel.
- It does not require a shielding gas, unless it is gas-shielded (GS), which means it uses both the flux and an external gas supply.
- If self-shielded flux core wire is used it allows you to dispense with the cumbersome gas cylinder or a regulator, which makes it more portable and economical.
- It works well in windy or dirty conditions, as the flux protects the weld from atmospheric contamination.
- It allows for higher deposition rates and deeper penetration than solid wire, which can reduce the number of passes and improve productivity.
- It can produce strong and corrosion-resistant welds on stainless steel without using gas-shielded processes like TIG or MIG.
- It can be more versatile and adaptable than solid wire, as it has different types and sizes of flux cores that can provide different properties and benefits to the weld.
- It can be used in a variety of positions, such as flat, horizontal and overhead (assuming you have a flux core wire feeder).
Disadvantages FCAW Over GMAW when It Comes to Welding Stainless Steel
There are also a number of disadvantages that you need to consider.
- It produces more spatter and slag than solid wire, which can affect the appearance and cleanliness of the weld.
- It requires more skill and experience to master the dragging technique and avoid undercutting or lack of fusion.
- It will create a greater amount of toxic fumes that require proper ventilation and personal protective equipment.
- It can be more difficult to find compatible wires for different grades of stainless steel.
Differences Between Solid Wire and Flux Core Wire
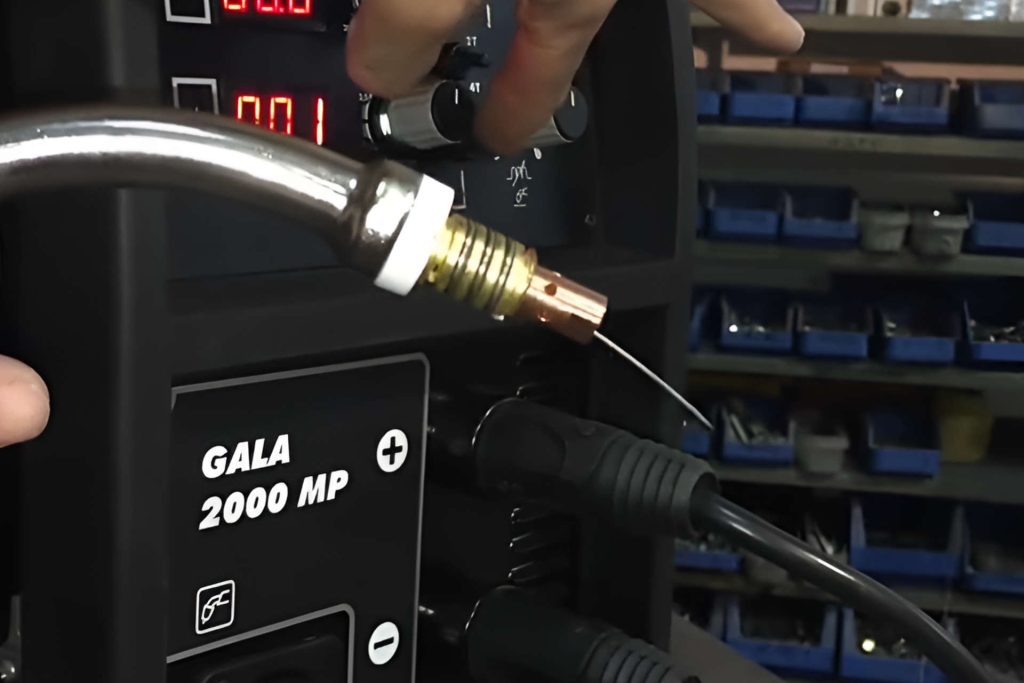
If you are an inexperienced welder it helps to understand the basic differences between the two methods to make your decision as to which is right for you and your project.
Solid Wire
- It is a solid metal wire that is fed through a welding gun and forms an arc with the base metal.
- It requires a shielding gas, such as argon or helium, to protect the weld from oxidation and contamination.
- It produces less spatter and slag than flux core wire, which makes it easier to clean and finish the weld.
- It can be used for all positions and directions of welding, as it does not depend on gravity to feed the wire.
- It can be more precise and consistent than flux core wire, as it has a uniform diameter and composition.
Flux Core Wire
- It is a tubular wire that has a flux-filled core that generates a shielding gas when it burns.
- It does not require a shielding gas, unless it is gas-shielded, which means it uses both the flux and an external gas supply.
- It produces more spatter and slag than solid wire, which can affect the appearance and cleanliness of the weld.
- It can be used for flat and horizontal positions only, as it relies on gravity to feed the wire.
- It can be more versatile and adaptable than solid wire, as it has different types and sizes of flux cores that can provide different properties and benefits to the weld.
Choosing the Best Flux Core Wire for Welding Stainless Steel
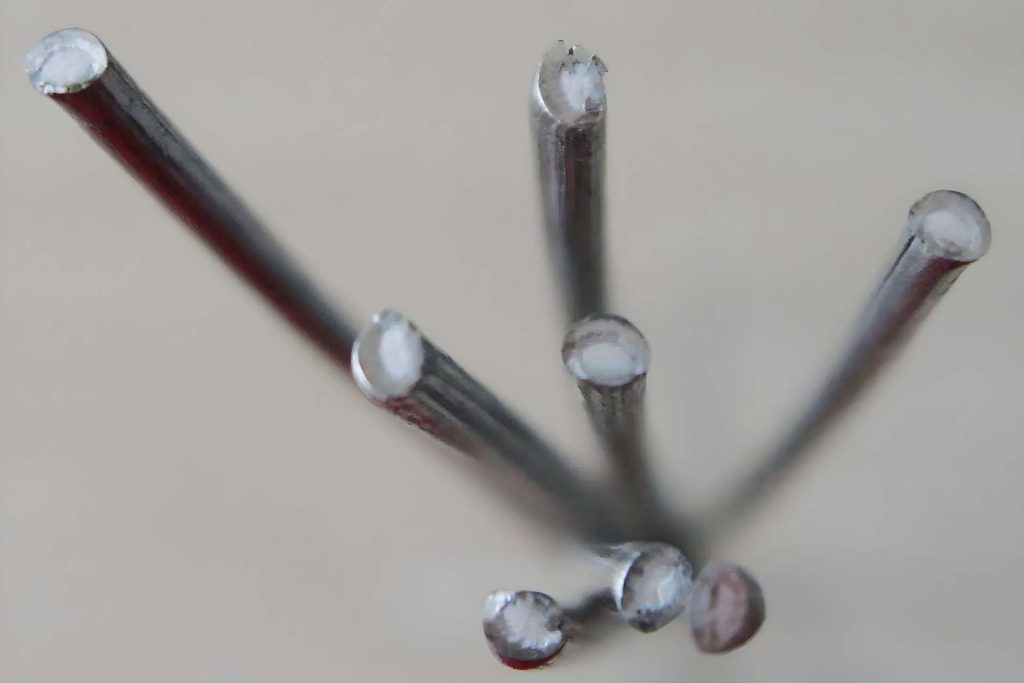
Choosing the best flux core wire for welding stainless steel depends on several factors, such as the grade of stainless steel, the thickness of the material, the welding position, the desired weld quality, and the available equipment. Here are some tips to help you make the right choice:
Use Stainless Steel Flux Core Wire
You can’t use regular flux core wires for welding stainless steel, as they are designed for carbon steel or low alloy steel. You need to use specialized stainless steel flux core wires that match the grade of your base metal. For example, if you are welding 304 stainless steel, you need to use 308L or 309L stainless steel flux core wires.
Choose Between Self-Shielded or Gas-Shielded Wires
Self-shielded wires are more convenient and economical, as they don’t require an external gas supply. However, they can produce more spatter and slag than gas-shielded wires, which can affect the weld quality and appearance. Gas-shielded flux core welding is more expensive and cumbersome, as they require a gas cylinder and a regulator. However, they can produce cleaner and smoother welds than self-shielded wires.
Gas-shielded flux core wire
Gas-shielded flux core wire is a type of flux core wire that needs an external gas supply, usually carbon dioxide or a mixture of argon and carbon dioxide, to create a protective atmosphere around the weld. This type of wire has a higher deposition rate and produces less spatter than self-shielded wire. It also creates a smoother weld appearance and less slag.
Some of the characteristics and advantages of gas-shielded flux core wire are:
- It can weld in all positions, including vertical and overhead.
- It can weld thicker materials and fill wider gaps than solid wire.
- It can weld faster and more efficiently than solid wire.
- It can weld stainless steel with low carbon content and prevent carbide precipitation.
Some of the suitable applications and recommended stainless steel grades for gas-shielded flux core wire are:
- Structural fabrication and repair
- Pressure vessels and boilers
- Petrochemical and chemical industries
- Food processing and dairy equipment
- 304, 304L, 316, 316L, 309, 309L, 310, 347
Self-Shielded Flux Core Wire
Self-shielded flux core wire is a type of flux core wire that does not need an external gas supply. It relies on the flux material in the core to generate a shielding gas when it melts. This type of wire is more portable and convenient than gas-shielded wire. It can also weld in windy or dirty conditions where gas-shielded wire may not work.
Some of the characteristics and advantages of self-shielded flux core wire are:
- It can weld in any position, including vertical and overhead.
- It can weld outdoors and in harsh environments where gas-shielded wire may fail.
- It can weld stainless steel with high carbon content and prevent cracking.
- It can weld dissimilar metals, such as stainless steel to carbon steel.
Some of the suitable applications and recommended stainless steel grades for self-shielded flux core wire are:
- Shipbuilding and offshore construction
- Mining and earthmoving equipment
- Automotive exhaust systems
- Railcar fabrication and repair
- 409, 410, 430, 446, 308H, 309H, 310H
Select the Right Diameter and Polarity
The diameter of the wire affects the deposition rate, penetration depth, and heat input of the weld. Generally, thinner wires are better for thinner materials and lower currents, while thicker wires are better for thicker materials and higher currents. The polarity of the welder also affects the performance of the wire. Generally, self-shielded wires require direct current electrode negative (DCEN), while gas-shielded wires require direct current electrode positive (DCEP).
Follow the Manufacturer’s Recommendations
If your are inexperienced then it can often be best to choose the best flux core wire for welding stainless steel by follow the manufacturer’s recommendations. They will provide you with the specifications, settings, and instructions for using their products. You should also check their data sheets and safety data sheets for more information.
Key Considerations for Selecting Flux Core Wire for Stainless Steel Welding
There are a number of important considerations that need to be made to aid your eventual flux core wire selection for stainless materials.
Stainless Steel Grade and Composition
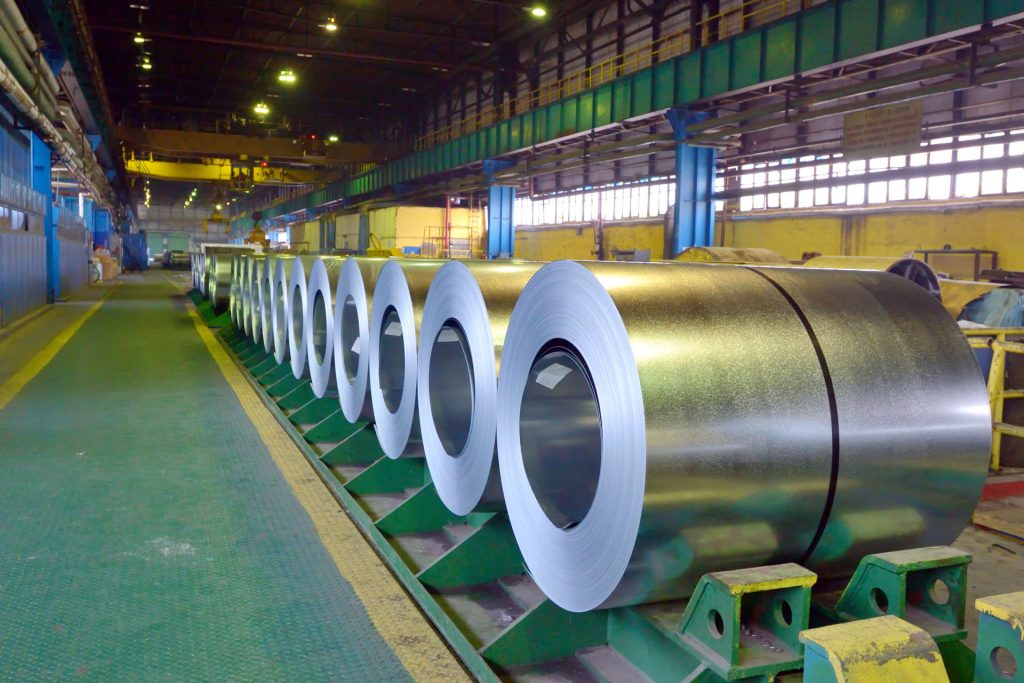
Different Stainless Steel Grades and Their Welding Characteristics
Stainless steel is a broad term that covers many types of alloys with different properties and compositions. The most common way to classify stainless steel is by its grade, which indicates the amount of chromium and other elements in the alloy. For example, 304 stainless steel contains 18% chromium and 8% nickel, while 316 stainless steel contains 16% chromium, 10% nickel and 2% molybdenum.
The grade of stainless steel affects its weldability, corrosion resistance, strength and appearance. Some grades are more suitable for certain applications than others. For example, 304 stainless steel is widely used for food processing equipment, while 316 stainless steel is preferred for marine environments.
When welding stainless steel, it is important to match the flux core wire with the base metal grade to ensure a strong and durable weld. Using a mismatched wire can result in poor weld quality, cracking, porosity or corrosion.
Matching Flux Core Wire with Stainless Steel Composition
To match the flux core wire with the stainless steel composition, you need to consider two factors: the type of shielding and the type of filler metal.
The type of shielding refers to whether the flux core wire is self-shielded or gas-shielded. Self-shielded wires have a core that produces a protective gas when melted, eliminating the need for an external gas supply. Gas-shielded wires require an external gas source, such as argon or carbon dioxide, to shield the weld from atmospheric contamination.
The type of filler metal refers to the alloy composition of the flux core wire. The filler metal should have similar or higher corrosion resistance and strength than the base metal. For example, if you are welding 304 stainless steel, you can use a 308L flux core wire, which has a lower carbon content than 304 stainless steel and is more resistant to intergranular corrosion.
There are different types of flux core wires available for welding stainless steel, each with its own advantages and disadvantages. Some of the most common ones are:
- E308LT1-1/4: A self-shielded wire that can be used for all-position welding of 301, 302, 304 and 308 stainless steel. It has good arc stability, low spatter and smooth bead appearance.
- E309LT1-1/4: A self-shielded wire that can be used for all-position welding of dissimilar metals, such as carbon steel to stainless steel. It has excellent crack resistance and high impact toughness.
- E316LT1-1/4: A self-shielded wire that can be used for all-position welding of 316 and 316L stainless steel. It has superior corrosion resistance and pitting resistance in chloride environments.
- E309LT0-1/4: A gas-shielded wire that can be used for flat and horizontal welding of dissimilar metals, such as carbon steel to stainless steel. It has high deposition rate, low spatter and good slag removal.
- E316LT0-1/4: A gas-shielded wire that can be used for flat and horizontal welding of 316 and 316L stainless steel. It has high deposition rate, low spatter and good slag removal.
Wire Diameter and Thickness
Impact of Wire Diameter on Welding Performance and Weld Bead Appearance
The wire diameter is another factor that affects the flux core welding performance and weld bead appearance. The wire diameter determines the amount of current and voltage required to melt the wire, as well as the size and shape of the weld bead.
Generally speaking, smaller wire diameters require lower current and voltage settings than larger wire diameters. Smaller wire diameters also produce smaller weld beads with less penetration and more convexity. Larger wire diameters require higher current and voltage settings than smaller wire diameters. Larger wire diameters also produce larger weld beads with more penetration and less convexity.
The choice of wire diameter depends on the thickness of the base metal, the welding position, the joint design and the desired weld quality. For example, if you are welding thin stainless steel sheets in a flat position, you may want to use a smaller wire diameter (such as 0.030 inch) to avoid burn-through and excessive distortion. If you are welding thick stainless steel plates in a vertical position, you may want to use a larger wire diameter (such as 0.045 inch) to achieve sufficient penetration and fill the gap.
Recommended Wire Diameters for Various Applications
The blow table shows various recommended wire diameters for various applications of flux core welding on stainless steel:
Application | Base Metal Thickness | Wire Diameter |
---|---|---|
Food processing equipment | 0.030 – 0.125 inch | 0.035 inch |
Marine structures | 0.125 – 0.250 inch | 0.045 inch |
Pressure vessels | 0.250 – 0.500 inch | 0.052 inch |
Heavy equipment | 0.500 – 1.000 inch | 0.062 inch |
Shielding Gas Requirements
The Role of Shielding Gas in Flux Core Wire Welding
Although often considered as mainly self-shielding there is a good argument for using gas-shielded flux core wire variant, especially in terms of weld quality. Indeed the gas-shielded variant flux core welding is particularly common in larger workshops. When using this variant of flux core wire the shielding gas becomes an essential component of flux core wire welding process. The shielding gas provides additional protection for weld pool from reacting with oxygen, nitrogen and hydrogen in the air, which can cause porosity, cracking and corrosion.
Shielding gas also affects the arc characteristics, the weld penetration, the spatter level and the weld appearance. Different types of shielding gases have different properties and effects on the welding process.
Types of shielding gases suitable for stainless steel welding
The most common types of shielding gases used for flux core welding on stainless steel are:
- Argon: A pure inert gas that provides excellent arc stability, low spatter and smooth weld appearance. However, it also produces shallow penetration and low deposition rate.
- Carbon dioxide: A pure active gas that provides deep penetration, high deposition rate and good mechanical properties. However, it also produces high spatter, rough weld appearance and increased oxidation.
- Argon-Carbon dioxide mixtures: A combination of inert and active gases that provides a balance between penetration, deposition rate, spatter level and weld appearance. The most common mixture ratios are 75% argon and 25% carbon dioxide, or 90% argon and 10% carbon dioxide.
- Argon-Oxygen mixtures: A combination of inert and active gases that provides good arc stability, low spatter and smooth weld appearance. However, it also produces shallow penetration and increased oxidation. The most common mixture ratio is 98% argon and 2% oxygen.
The choice of shielding gas depends on the type of flux core wire, the stainless metal grade, the welding position and the desired weld quality. For example, if you are using a self-shielded wire on 304 stainless steel in a flat position, you may not need any shielding gas at all. If you are using a gas-shielded wire on 316 stainless steel in a vertical position, you may want to use a mixture of argon and carbon dioxide to achieve sufficient penetration and fill the gap.
The Best Flux Core Wire for Welding Stainless Steel
Wire Feeding and Compatibility with Welding Equipment
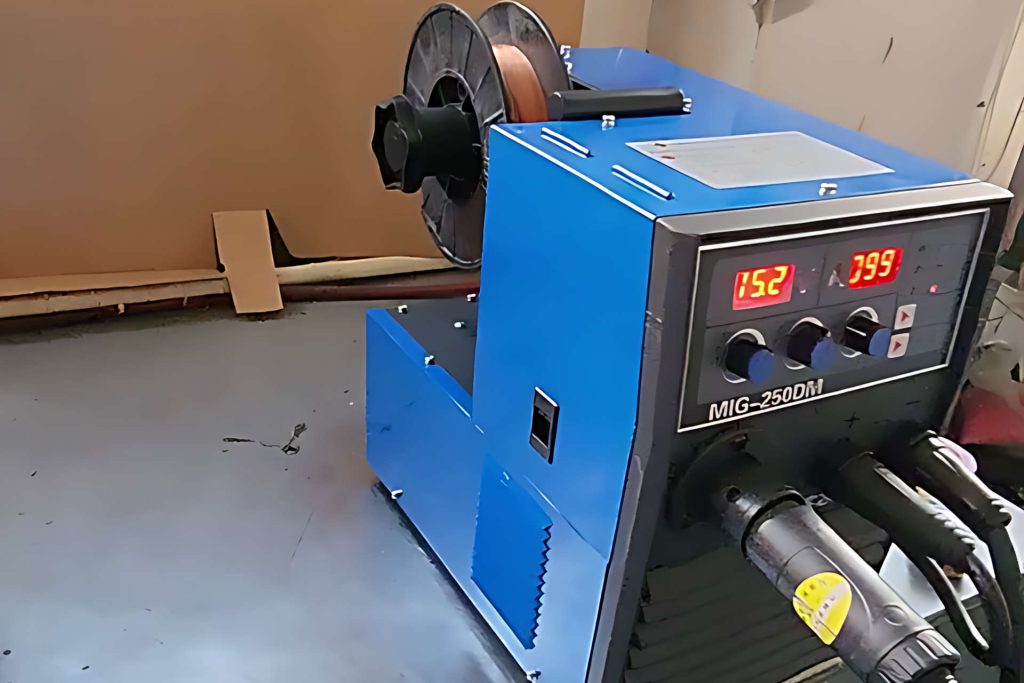
Choosing the Right Wire Feeding System for Flux Core Wire
Wire feeding is another important aspect of flux core welding on stainless steel. Wire feeding refers to how the wire is delivered from the spool to the nozzle through the gun.
Wire feeding can be either constant speed or variable speed. Constant speed wire feeding means that the wire feed rate is fixed and controlled by the welder settings. Variable speed wire feeding means that the wire feed rate is adjusted automatically by a feedback mechanism based on the arc voltage.
Constant speed wire feeding is more common for flux core welding because it provides more consistent weld quality and less spatter. Variable speed wire feeding is more suitable for MIG welding because it allows more flexibility and control over the arc length.
Wire feeding can also be either push or pull. Push wire feeding means that the wire is pushed by a motor in the welder through a long cable to the gun. Pull wire feeding means that the wire is pulled by a motor in the gun from a short cable connected to the welder.
Push wire feeding is more simple and economical, but it can cause problems such as bird-nesting, tangling and kinking when using soft or large diameter wires. Pull wire feeding is more complex and expensive, but it can prevent these problems and provide smoother wire feeding.
The choice of wire feeding system depends on the type of flux core wire, the wire diameter, the cable length and the welding position. For example, if you are using a self-shielded wire with a small diameter (such as 0.035 inch) in a flat position, you may want to use a constant speed push wire feeding system with a short cable (less than 15 feet). If you are using a gas-shielded wire with a large diameter (such as 0.062 inch) in an overhead position, you may want to use a constant speed pull wire feeding system with a long cable (more than 15 feet).
Compatibility Considerations with Welding Machines
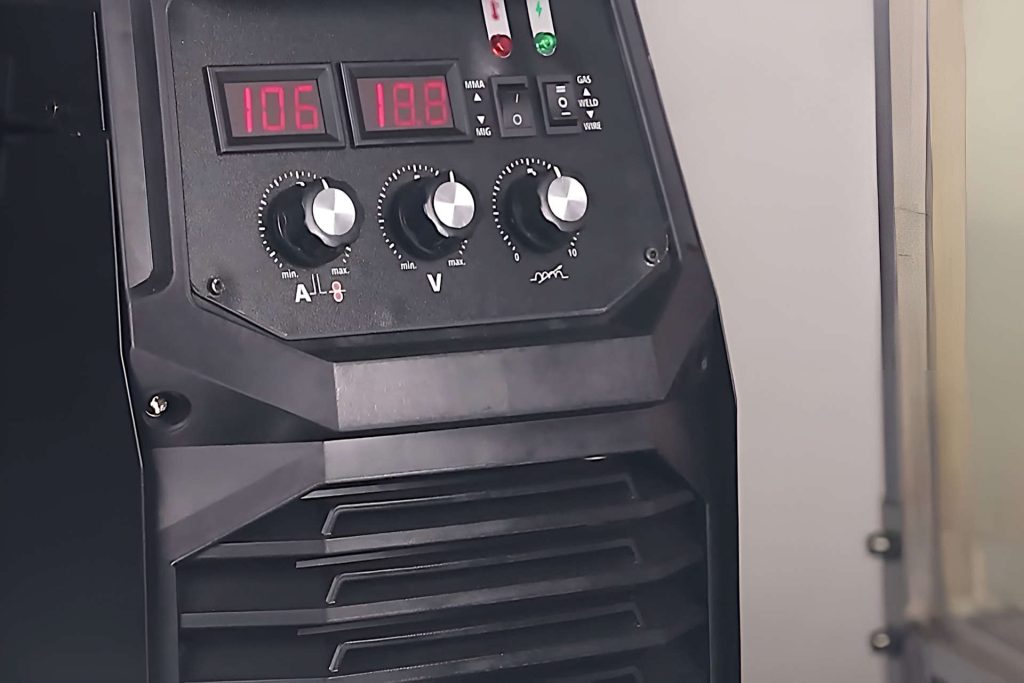
Compatibility is another factor that affects flux core welding on stainless steel. Compatibility refers to how well the flux core wire matches with the welding machine in terms of polarity, voltage and current.
Polarity is the direction of current flow in the welding circuit. Polarity can be either direct current electrode negative (DCEN) or direct current electrode positive (DCEP). DCEN means that the current flows from the electrode (wire) to the workpiece (base metal), while DCEP means that the current flows from the workpiece to the electrode. Most flux core wires for stainless steel welding require DCEN polarity.
Voltage and current settings depend on the wire diameter, base metal thickness, welding position, and joint design. It is important to consult the welding machine’s manual or follow the manufacturer’s recommendations for the appropriate voltage and current settings.
Some welding machines have built-in settings specifically designed for flux core welding, while others may require adjustments or additional accessories to accommodate flux core wires. It is crucial to ensure that your welding machine is compatible with flux core welding and can provide the necessary power and control for the desired weld quality.
Welding Position and Joint Type
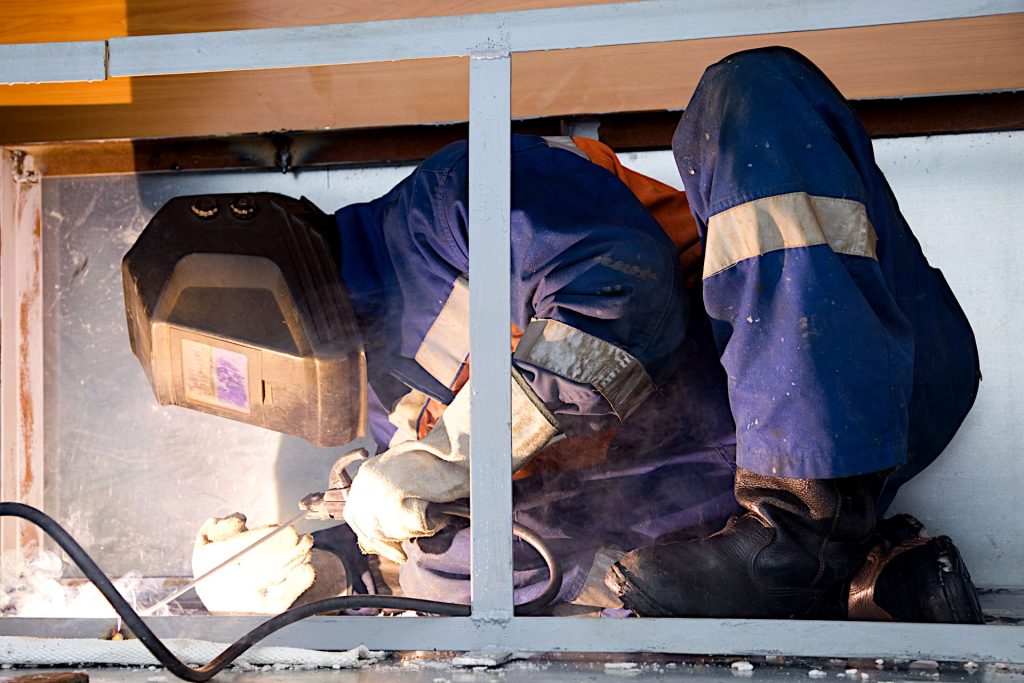
One of the main advantages of flux core welding is its versatility. You can weld in different positions and join different types of metals with the right flux core wire. However, not all wires are suitable for every situation. You need to consider the welding position and the joint type before choosing a flux core wire.
How Welding Position Affects Flux Core Wire Selection
Welding position refers to the orientation of the weld relative to gravity. There are four basic welding positions: flat, horizontal, vertical, and overhead. Each position requires a different level of skill and technique to produce a quality weld.
Flux core wires are classified into two types based on their shielding gas requirements: self-shielded and gas-shielded. Self-shielded wires do not need an external gas supply, while gas-shielded wires do. The type of wire you use affects the welding position you can perform.
Self-shielded wires are more suitable for welding in all positions, especially outdoors or in windy conditions. They produce a slag that protects the weld pool from atmospheric contamination. However, they also generate more spatter and smoke, which can affect the weld quality and visibility.
Gas-shielded wires are better for welding in flat and horizontal positions, especially indoors or in controlled environments. They produce a cleaner and smoother weld with less spatter and smoke. However, they also require a gas cylinder, a regulator, and a hose, which can limit the mobility and accessibility of the welder.
Joint Types and Their Influence on Wire Selection
Joint type refers to the configuration of the metal pieces that are being welded together. There are five basic joint types: butt, corner, edge, lap, and tee. Each joint type has a different geometry and strength requirement that affects the wire selection.
Flux core wires are also classified into two types based on their tensile strength: low alloy and high alloy. Low alloy wires have a tensile strength of less than 80 ksi (550 MPa), while high alloy wires have a tensile strength of more than 80 ksi (550 MPa). The type of wire you use affects the joint type you can weld.
Low alloy wires are more suitable for welding mild steel joints, such as butt, corner, and tee joints. They provide adequate strength and ductility for most applications. However, they may not be compatible with some stainless steel alloys or high-strength metals.
High alloy wires are better for welding stainless steel joints, such as edge and lap joints. They provide higher strength and corrosion resistance for demanding applications. However, they may also be more expensive and harder to find than low alloy wires.
Comparing Flux Core Wire Brands
There are many flux core wire brands on the market, but not all of them are suitable for stainless steel welding. In this section, we will compare some of the most popular flux core wire brands for stainless steel welding and see how they perform in terms of quality, durability, and reputation.
Overview of Popular Flux Core Wire Brands for Stainless Steel Welding
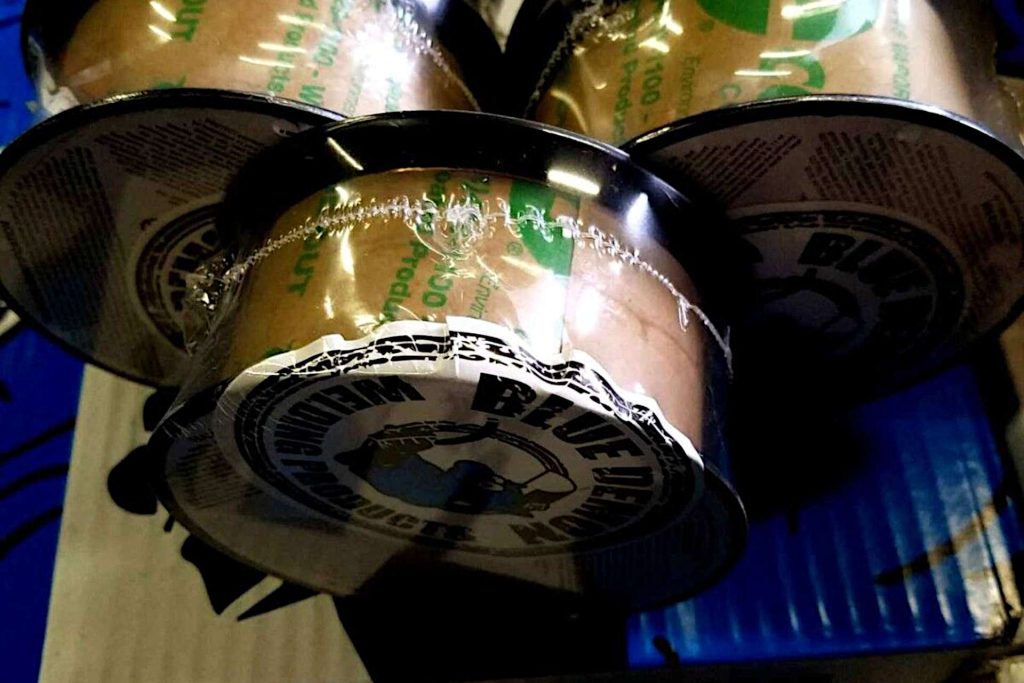
Blue Demon
One of the most reputed brands that produce gasless stainless wires is Blue Demon. They offer a variety of flux core wires for different applications, such as E71TGS, E71T-11, E316LT1-1/4, and E308LT1-1/4. These wires are designed to weld carbon steel, low alloy steel, and stainless steel with self-shielding gas. They have good arc stability, slag removal, and bead appearance.
Hobart
Another well-known brand in the market is Hobart. Hobart offers a high-quality flux core wire for both stainless and mild steel welding, called.
Forney
Forney is another brand that makes a great single-pass flux core wire for gasless welding, especially under breezy conditions and high feed rates . Their flux core wire produce s a smooth arc action and low spatter.
INETUB
INETUB is a brand that offers a good value flux core wire for stainless steel welding. It has reputation for high feedability and low spatter. It can weld in all positions and produce a bright and smooth bead.
Performance, Reliability, and Reputation
All brands has its own strengths and weaknesses when it comes to flux core welding stainless steel. To help you decide which one is best for your project, let’s compare them based on their performance, reliability, and reputation.
Performance: Performance refers to how well the flux core wire can weld stainless steel in terms of penetration, bead appearance, spatter, slag removal, and arc stability. Based on our research and user reviews, we found that Blue Demon and Hobart have the best performance among the brands. They can weld stainless steel with deep penetration, smooth bead, low spatter, easy slag removal, and stable arc. Forney and INETUB are also good performers, but they may have some issues with spatter and slag removal.
Reliability: Reliability refers to how consistent and durable the flux core wire is when welding stainless steel. Based on our research and user reviews, we found that Hobart and INETUB have the best reliability among the five brands. They have well-wound spools that feed smoothly and evenly without tangling or breaking. They also have good shelf life and resistance to corrosion. Blue Demon and Forney are also reliable brands, but they may have some issues with spool winding and feeding.
Reputation: Reputation refers to how trusted and respected the flux core wire brand is among the welding community. Based on our research and user reviews, we found that Hobart and Blue Demon have the best reputation among the brands considered. They are industry leaders that have been producing quality welding products for decades. They have loyal customers who swear by their products and service.
Forney and INETUB are also reputable brands, but they may not be as well-known or widely used as Hobart and Blue Demon.
The Best Flux Core Wire for Welding Stainless Steel
Videos
Resources
- Materials Science: Backing Welding of 304 Stainless Steel Pipeline by Flux-core Wire Without Back Shielding Gas
- Materials Science: Stainless steel wire with flux core for welding zinc coated steel sheets
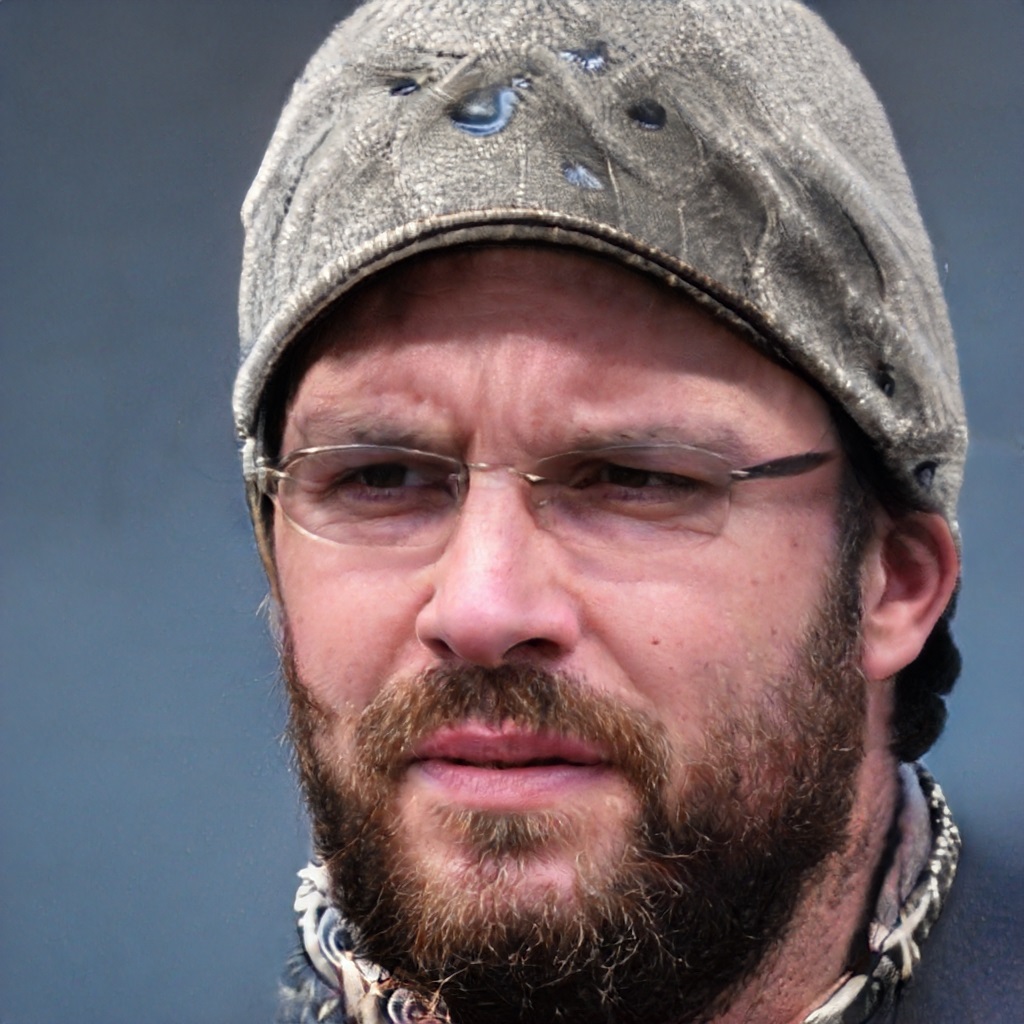
I’ve been involved in the welding industry for over twenty years. I trained in various engineering shops working on various projects from small fabrication and repairs through to industrial projects.I specialize in welding aluminum and food grade stainless steel and an now run an engineering shop fabricating equipment for the food industry.