Exploring the Applications of Gasless MIG Welding Wire
The wind is blowing, and you are trying to weld the axle on your trailer, but you can see the weld puddle being affected as the shielding gas is blown away, causing you to end up with weak and untenable welds. Such conditions can be incredibly frustrating, but a change in wire to a self-shielding flux core wire can reduce wind-related and other problems as the applications of gasless MIG welding wire are extensive.
Gasless MIG (Metal Inert Gas) welding, also known as flux-cored arc welding (FCAW), offers key advantages for many welding applications where using bottled shielding gas may be impractical or challenging. By utilizing a hollow wire electrode filled with fluxing agents, gasless MIG is able to operate without requiring an external supply of expensive bottled gas mixtures.
The flux core provides shielding, arc stabilization, and alloying elements as the wire melts and deposits into the weld pool. This makes gasless MIG an extremely versatile, portable, and cost-effective welding process suitable for various materials and environments.
Below, we will briefly overview how gasless MIG welding works and its primary benefits compared to traditional shielded gas MIG welding. Key topics covered include:
- How gasless flux-cored wires operate without shielding gas
- Advantages for outdoor, remote, and windy welding conditions
- Portability and ease of use without gas cylinders
- Capability to weld mild steel, stainless, aluminum, and galvanized metals
- Cost savings versus gas-shielded MIG
- Applications ranging from DIY to professional fabrication/repair
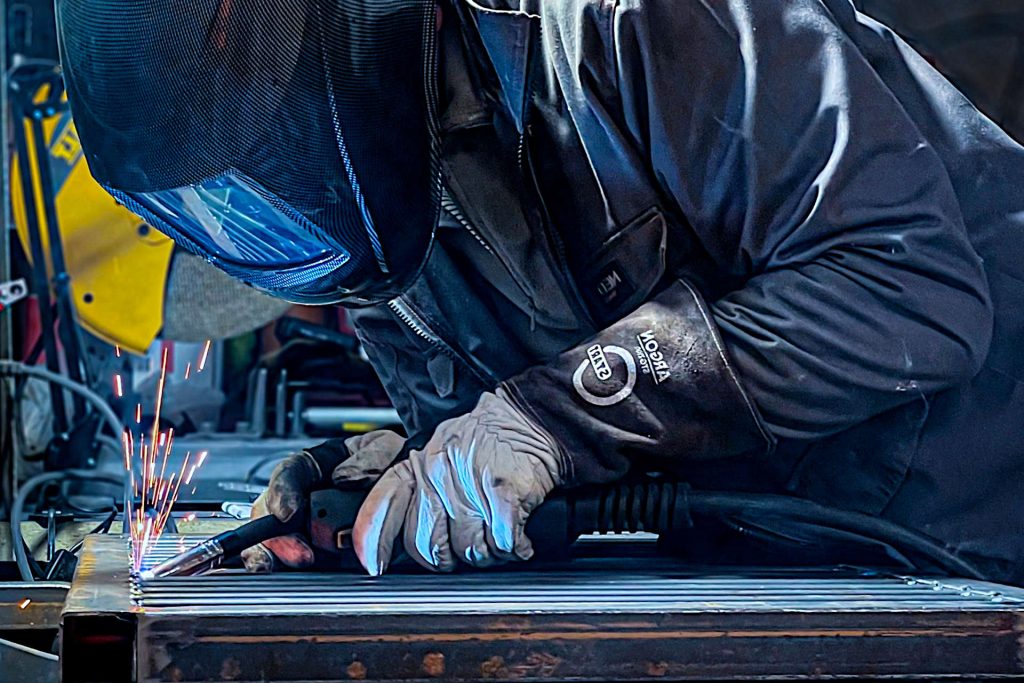
Gasless MIG’s ability to operate without bottled shielding gas makes it an excellent choice for welding in remote locations, in windy/drafty conditions, outdoors, and in confined spaces where gas cylinders may be impractical, hazardous, or costly. The self-shielding flux-cored wire allows a stable arc and good weld quality while eliminating setup time, equipment requirements, and costs associated with traditional bottled gas MIG welding.
Whether you are a farmer repairing equipment in the field, a construction worker on an outdoor job site, or a hobbyist in the garage, gasless MIG welding can provide quality welds without the need for gas cylinders and related equipment. Its all-in-one wire, ease of use, and portability help open up new possibilities for welding in unique environments and situations.
Applications: Where Gasless MIG Excels
Gasless MIG welding offers clear advantages over traditional gas-shielded MIG in certain applications and environments. By eliminating the need for bottled shielding gas and related equipment, gasless flux-cored welding greatly expands the possibilities for high-quality welding in unique conditions and remote locations.
Some of the key applications where gasless MIG can excel include:
Applications of Gasless MIG Welding: Outdoor Welding
For any welding job outdoors, gasless MIG provides benefits. The absence of shielding gas cylinders means no need to worry about regulators, hoses, or gas bottles getting knocked over or damaged on a breezy worksite. The self-shielding wire protects the weld pool from disruption even in moderately windy conditions. This makes gasless MIG ideal for outdoor welding projects like:
- Construction sites
- Sculpture/art installations
- Park/playground equipment
- Farming and agriculture equipment
- Automotive repair and restoration
Portability is also improved without heavy gas cylinders to transport. The spool of flux-cored wire is lightweight, making it easy to move the welder to wherever it’s needed outdoors.
Windy Area Welding
In particularly drafty conditions like wind tunnels, open warehouses, or gusty elevated work platforms, gasless MIG really shines. The flux core of the wire prevents the shielding envelope around the weld from being disrupted by wind.
This results in a more stable arc and higher quality welds compared to trying to gas shield weld in high winds. For any fabrication or repair job in consistent breezy conditions, gasless MIG is the way to go.
Remote Location Welding
For worksites situated far from industrial gas supply infrastructure, gasless MIG provides a high-performance welding solution without the logistical headache of transporting bulk gas cylinders long distances.
Examples include:
- Offshore oil platforms
- Mining operations
- Forestry/logging equipment repair
- Agriculture equipment in rural locations
- Remote construction projects
Welding with just a spool of wire allows greater flexibility and productivity in these remote field locations.
Unique Capabilities of Gasless MIG
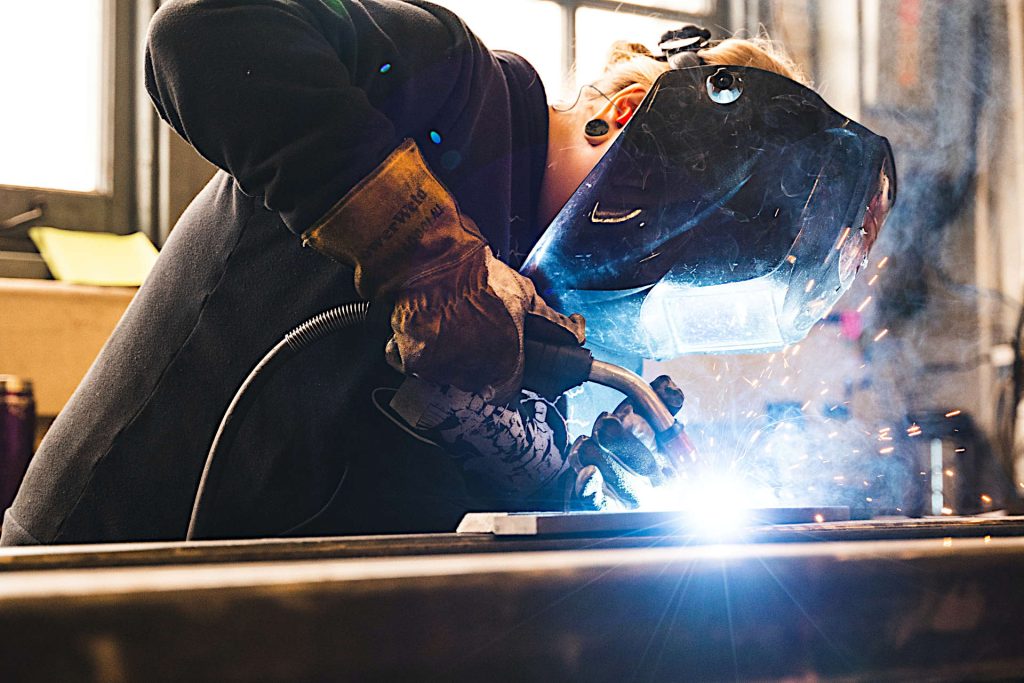
Beyond its advantages for specific applications, gasless MIG welding offers unique capabilities that increase its versatility for different materials and welding positions. Understanding these capabilities helps identify even more situations where a gasless MIG welder can be the best tool for the job.
Ability to Weld Many Common Metals
Gasless flux-cored wires are available for welding a wide range of metals beyond just standard carbon steel. Quality welds can be achieved in:
- Stainless steel
- Galvanized steel
- Chrome-moly alloys
- Nickel alloys
Add this to the ability of flux core to weld weld dissimilar metals as well as such diverse metals makes gasless MIG highly useful for mixed metal fabrication, art projects using dissimilar metals, and repairs on items with exotic alloy components. No need to switch processes – just change the wire.
All Position Welding
While specialized expertise is required for critical structural welds, gasless MIG provides the capability to make high-quality welds in multiple positions:
- Flat welds (1F/1G)
- Horizontal welds (2F/2G)
- Vertical up welds (3F/3G)
- Vertical down welds (4F/4G)
- Overhead welds (5F/5G)
This versatility expands the possibilities for creative applications like sculpture, decorative metalworking, and structural fabrication where flat welds are not always possible.
Low Voltage Power Operation
Gasless MIG can operate on portable generators and alternative power sources that provide only low-voltage electricity. This makes it ideal for:
- Remote job sites with small gas/diesel generators
- Portable solar, wind, or battery-based power systems
- Areas with limited electrical infrastructure
Additionally, there is no need for high-voltage input or costly heavy-duty generators.
No Bottled Gas Requirements
At its core, the fact that gasless MIG doesn’t require any external shielding gas supply opens up many possibilities that would be difficult and costly with traditional MIG.
Situations where bottled gas isn’t practical now become welding opportunities – whether 200 feet underwater or on top of a remote mountain.
Final Thoughts: Applications of Gasless MIG Welding
In summary, gasless flux-cored MIG welding offers significant advantages over traditional shielded gas MIG in many situations. Utilizing self-shielding wire eliminates the need for external shielding gas and associated equipment.
This improves portability, flexibility, and accessibility of high-quality MIG welding – expanding the possibilities for welding in outdoor, remote, windy, and confined space environments. Cost savings, ease of use, and environmental benefits are also realized with the gasless MIG process.
While traditional shielded MIG maintains advantages for particular heavy-duty fabrication, gasless MIG has proven itself as a highly versatile, high-performance welding technology. Continued developments in welding wire technology and welder design will only increase its capabilities and widen its applications in the future.
For everyone from farmers and builders to artists and hobbyists, gasless MIG opens up new potential. No longer limited by bottled gas logistics and costs, quality welding can happen anywhere the welder and wire can go. This will lead to innovations in repair, maintenance, construction, and creative fabrication in remote locations that are just now being realized.
The benefits of gasless MIG welding are extensive and have yet to be fully tapped. But it’s obvious that this technology will continue growing in popularity and usage as more people discover its portable, flexible, cost-effective, and environmentally friendly capabilities.
Commonly Asked Questions
Q: Is gasless MIG welding suitable for heavy industrial applications?
A: Gasless MIG may not be the best choice for certain heavy fabrication or high duty cycle industrial welding where traditional gas-shielded MIG is preferred. But it can be applicable for many repair and maintenance applications in industrial settings.
Q: Does gasless MIG welding produce welds of the same quality as gas-shielded MIG?
A: When used correctly within its limitations, gasless MIG can produce high quality welds. However, for thick materials or more critical welds, gas-shielded MIG may provide advantages in weld appearance and metallurgical properties.
Q: Can gasless MIG weld thick materials?
A: Gasless MIG welding is generally limited to thinner gauge materials under 1/4 inch thickness. For thicker materials, the conventional gas-shielded MIG process is preferable.
Q: What metals can be welded with gasless MIG wire?
A: Gasless MIG is capable of welding common metals like mild steel, stainless steel, and titanium. Aluminum, because of the nature of the metal is more problematic and self-shielded flux-core is generally not used requires traditional gas-shielded MIG depending on material properties and required weld quality.
Q: Is special equipment required for gasless MIG welding?
A: You can use a standard MIG welder designed for gas-shielded welding. The main difference is that you will not connect the shielding gas supply. Proper wire feed settings are important for best results.
Videos
Resources
- Aloraier, A., Ibrahim, R., & Thomson, P.: FCAW process to avoid the use of post weld heat treatment. International Journal of Pressure Vessels and Piping, 83, 394-398.
- Zhang, Z., Liu, L., Shen, Y., & Wang, L: Welding of magnesium alloys with activating flux. Science and Technology of Welding and Joining, 10, 737 – 743.
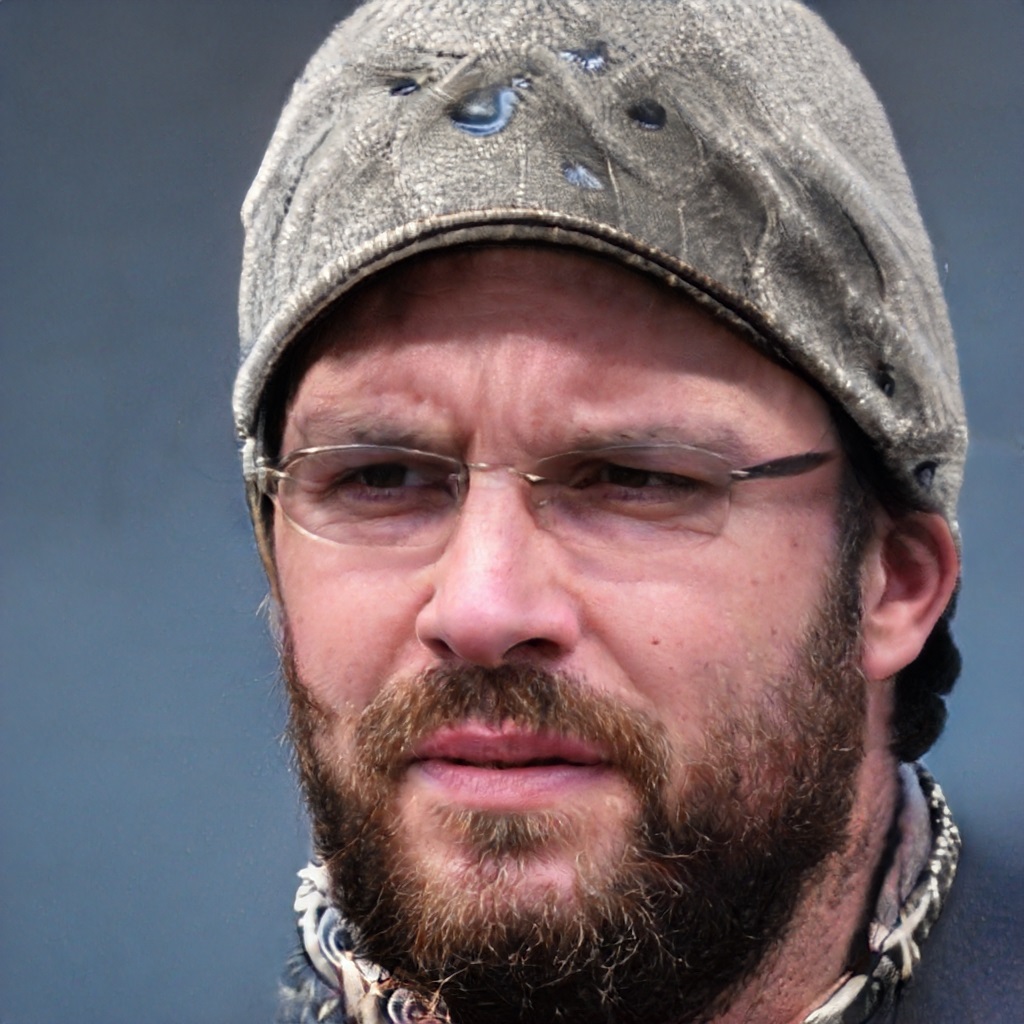
I’ve been involved in the welding industry for over twenty years. I trained in various engineering shops working on various projects from small fabrication and repairs through to industrial projects.I specialize in welding aluminum and food grade stainless steel and an now run an engineering shop fabricating equipment for the food industry.