Amperage Ranges for Different Flux Core Wire Diameters
The recommended amperage ranges for different flux core wire diameters is important for getting the best welding results. An essential aspect of this is using the correct amperage ranges for the materials employed and to be welded.
With Flux Cored Arc Welding (FCAW), the selection and calibration of these amperage ranges according to the flux core wire diameter plays a critical role in welding productivity, quality and safety. Acquiring a comprehensive knowledge of the different ranges, settings and their implications can help you to achieve optimal efficiency and exceptional results.
Table of Amperage Ranges Based on Diameter
Flux Core Wire Diameter | Recommended Amperage Range |
---|---|
0.030 inch | Up to 125 amperes |
0.035 inch | 140 amperes or higher |
5/64 inch | 400-450 amperes |
3/32 inch | 400-450 amperes |
0.45 inch | Dependent on factors |
T-11 wires | 17-22 volts, 50-275 amps |
0.031-0.188 inch | Dependent on factors |
Please note that the amperage range for 0.45-inch flux core wire and 0.031-0.188 inch diameter wires can vary depending on factors such as metal thickness, voltage, and specific requirements. The table provides a general overview of the recommended amperage ranges.
What is Flux Core Wire?
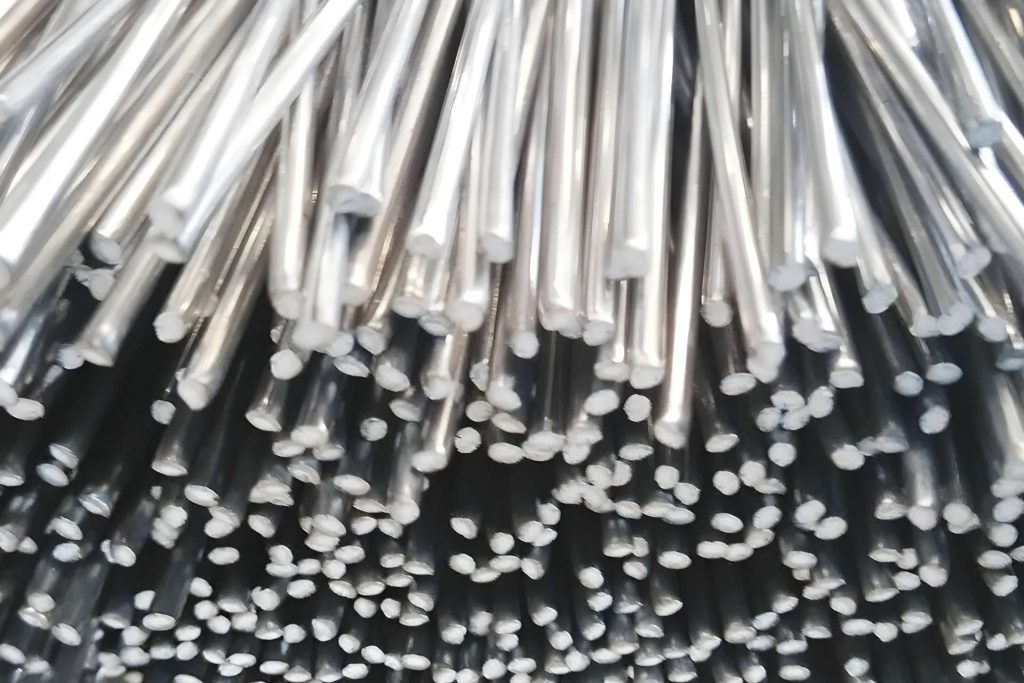
Flux core wire is an electrode or filler wire, utilized in FCAW. Its distinctive feature lies in its structural makeup—it is a tubular wire with a flux-filled inner core. The flux material, when subjected to the welding arc’s intense heat, assists in shielding the weld pool from contamination. It does so by producing a gas cloud that prevents atmospheric gases from interacting with the fresh weld.
Beyond shielding, the flux also contributes in forming slag, which further protects the cooling weld and assists in shaping the weld bead.
Types of Flux Core Wire
A comprehensive survey of flux core wire reveals its availability in two main types: self-shielding wires and gas-shielded wires.
Self-Shielding Flux Core Wire
Self-shielding flux core wires contain a flux compound that generates a protective gas shield around the weld pool when heated. This property renders an external shielding gas unnecessary, proving advantageous in windy conditions where such a gas might be blown away, compromising weld quality.
- Does not require a shielding gas when the arc is active.
- The wire has a core of flux chemicals that, when heated, produce a shielding gas that protects the weld from contamination and oxidation.
- Eliminates the need for a gas cylinder.
- Suitable for outdoor conditions.
- Can be more difficult to control and use.
- May produce lower quality welds compared to gas-shielded flux core wire.
Gas-Shielded Flux Core Wire
Gas-shielded flux core wires, on the other hand, necessitate the injection of a shielding gas during welding. Notwithstanding the effort required for gas management, this wire type typically yields a cleaner weld, given the total absence of slag. It facilitates higher welding speeds and proves fitting for thicker metals, vertical and overhead welding scenarios. In terms of versatility and usage, both self-shielding and gas-shielded flux core wires hold their unique standing, firmly entrenched in the world of welding.
- Requires a shielding gas when the arc is active.
- The shielding gas protects the weld from contamination and oxidation.
- Produces higher quality welds and is easier to control and use.
- Not suitable for outdoor conditions as any wind or movement in the air can affect the shielding gas performance.
Recommended Amperage Ranges for Different Flux Core Wire Diameters
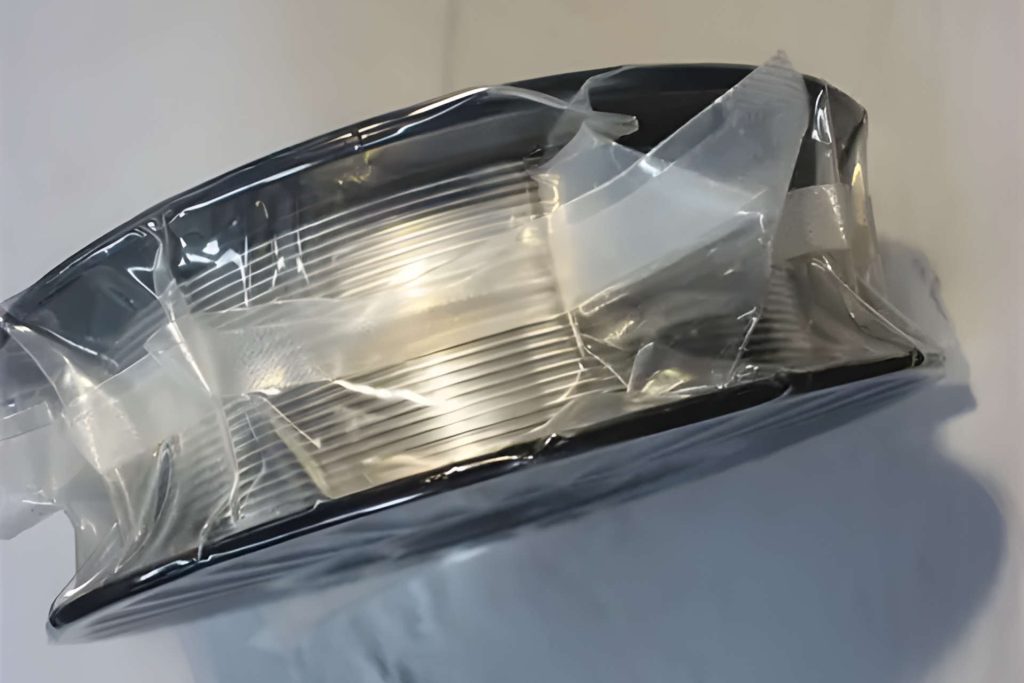
When you understanding the significant role and types of flux core wire, we can now look at recognizing and applying the recommended amperage ranges corresponding to varied flux core wire diameters. Achieving optimal welding results can depend upon
0.03 Inch or 0.035 Inch
One of the most common go-to choices for beginner welders with general welding jobs is flux core wire of either 0.03 inch or 0.035 inch in diameter. Both these diameters have broad applications, suitable for an array of metal thicknesses.
To illustrate the distinctions: in situations where the current level is set at approximately 125 amperes or a touch lower, the 0.030 inch flux core wire shows its true potential. However, to accommodate a surge in the current level to over 140 amperes, opt for the 0.035 inch wire. Thus, these wire options exhibit versatility, easily adapting to fluctuations in amperage settings.
5/64 Inch and 3/32 Inch
Graduating to larger dimensions, you will find flux core wires sized 5/64 inch and 3/32 inch. What sets them apart as EX0T-X types is their exclusive application to flat and horizontal welding working. They are custom-built to handle higher amperage levels, usually spanning from 400 to 450 amperes.
Such large thickness wire deliver strength and robustness and require the use of powerful welding machines, designed to handle these metal thicknesses and higher temperatures.
0.45 Inches
For projects demanding robustness and power, flux core wire reaching to 0.45 inches in diameter comes into play. Generally used for what is referred either welding thicker metals, like heavy structural steel, where a more substantial weld bead is required to ensure proper penetration and out-of-position welding, such as welding overhead or vertically up, where the molten pool needs to be held in place to prevent it from falling out of the joint.
These wires accommodate significant variations in voltage and amperage, with the precise settings rely heavily on the thickness of the metal being worked on.
T-11 Wires
In the area of specific types of flux core wires, T-11 wires have devised their unique range of parameters– a voltage oscillating between 17 to 22 volts, alongside amperage ranging from 50 to a powerful 275 amps. The versatility of the voltage and amperage levels these wires accept makes them adept at dealing with a range of wire diameters, hence their usage varies from case to case.
Relationship Between Wire Diameter, Material Thickness
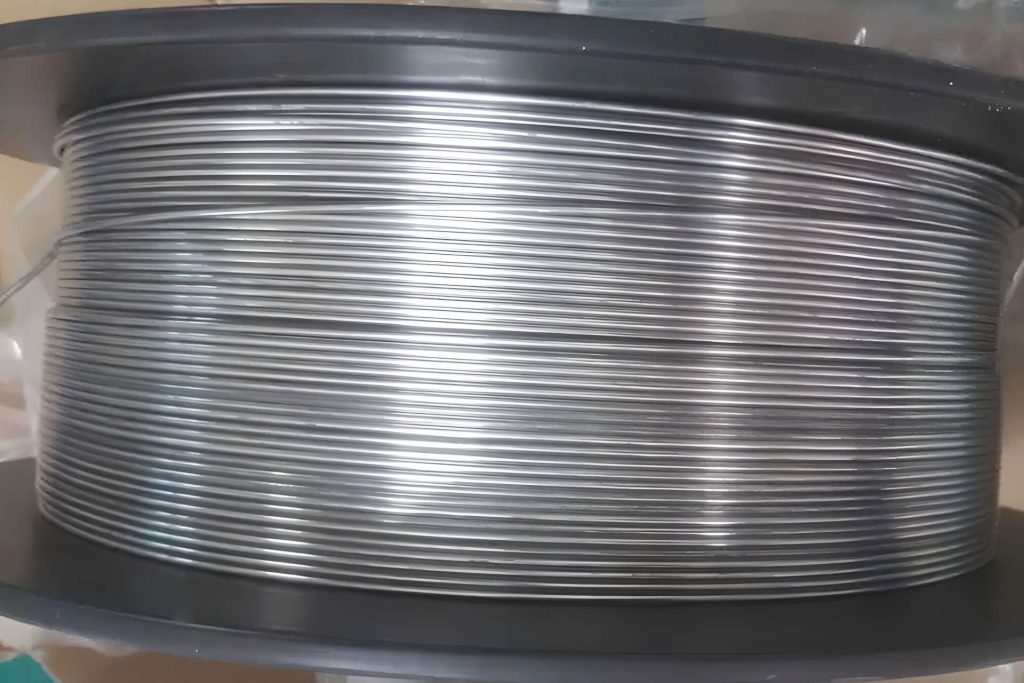
Finally, circle back to the intricate relationship between wire diameter, material thickness, and the consequent amperage. For single pass mild steel, flux core wire sizes of 0.030 inch and 0.035 inch display a noteworthy range: the amperage may range from 22 gauge (0.031 inches in thickness) to 14 gauge (0.078 inches thick) for the former, and from 20 gauge (0.037inches in thickness) to 3/16 inches (0.188 inches thick) for the latter.
By recognizing the interplay between wire diameter, material thickness, and necessary amperage, one can perfect the art of selecting the right tools for the job at hand.
Flux Core Wire
Wrap Up: Amperage Ranges for Different Flux Core Wire Diameters
To achieve optimal welding results on your material, understanding the recommended amperage ranges for different flux core wire diameters is crucial. The selection and calibration of these ranges play a significant role in welding productivity, quality, and safety, particularly in Flux Cored Arc Welding (FCAW). By gaining comprehensive knowledge of these ranges and their implications, welders can strive for optimal efficiency and exceptional outcomes.
While have the correct amperage is crucial for the diameter wire you are using it is of course also crucial that you choose the most suitable type of flux core wire for the materials that you are welding,
Videos
Resources
- Pennsylvania State University: A Comparison of Pulsed and Conventional Welding with Basic Flux Cored and Metal Cored Welding Wires
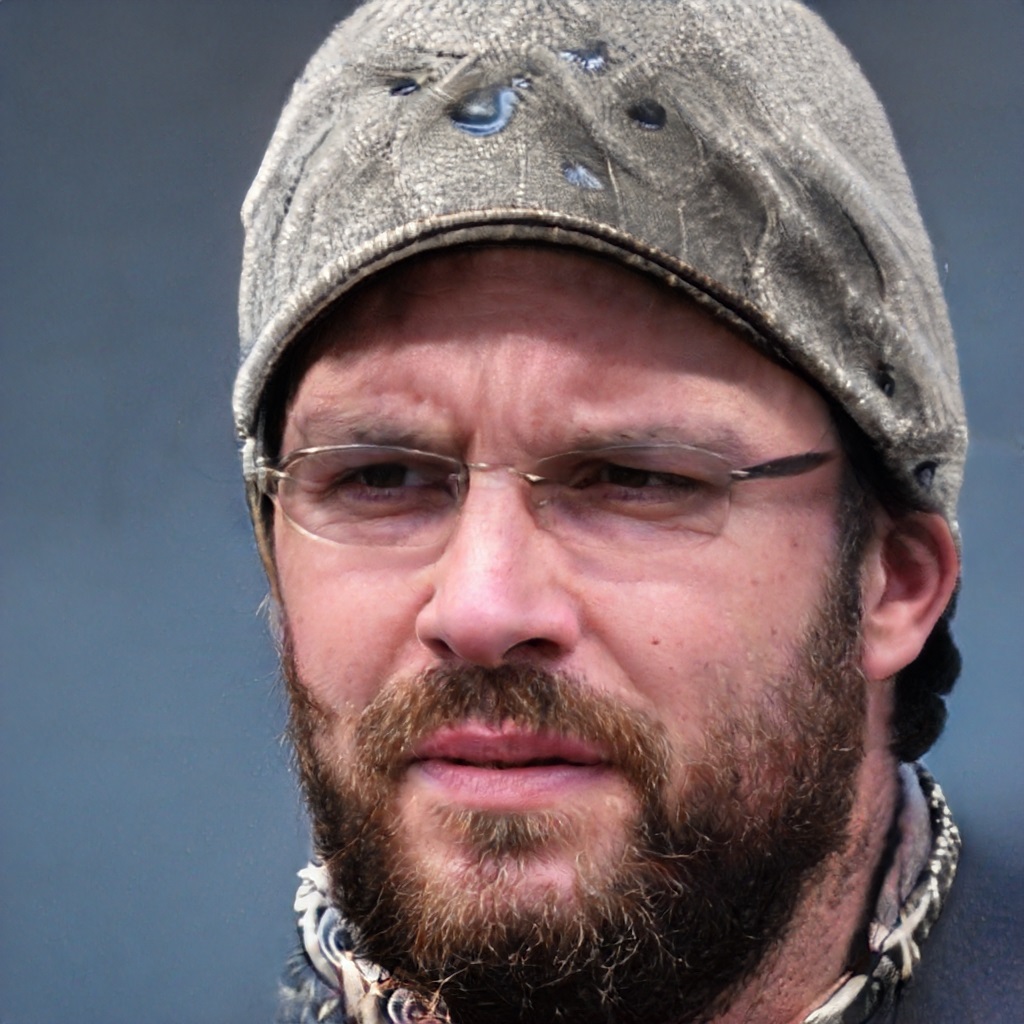
I’ve been involved in the welding industry for over twenty years. I trained in various engineering shops working on various projects from small fabrication and repairs through to industrial projects.I specialize in welding aluminum and food grade stainless steel and an now run an engineering shop fabricating equipment for the food industry.