What Are the Differences Between MIG Welding versus Flux- Cored Arc Welding
americanindustrialsupl and its partners may earn a commission if you purchase a product through one of our links.
Flux-Core and MIG welding are two of the most commonly used welding techniques. Flux-Core welding uses a continuously-fed consumable electrode, which is shielded by a flux compound to protect the weld area from atmospheric contamination. MIG welding, on the other hand, uses a continuously-fed consumable wire electrode and a shielding gas to protect the weld from atmospheric contamination and enable welding without gas.
Below, we will look to explain the differences between Flux-Core and MIG welding techniques. We will compare and contrast the two techniques based on various factors, including deposition rate, penetration depth, spatter levels, equipment cost, skill level required, materials that can be welded, and many others. By the end of this essay, you should have a better understanding of which welding technique is best suited for your specific welding needs.
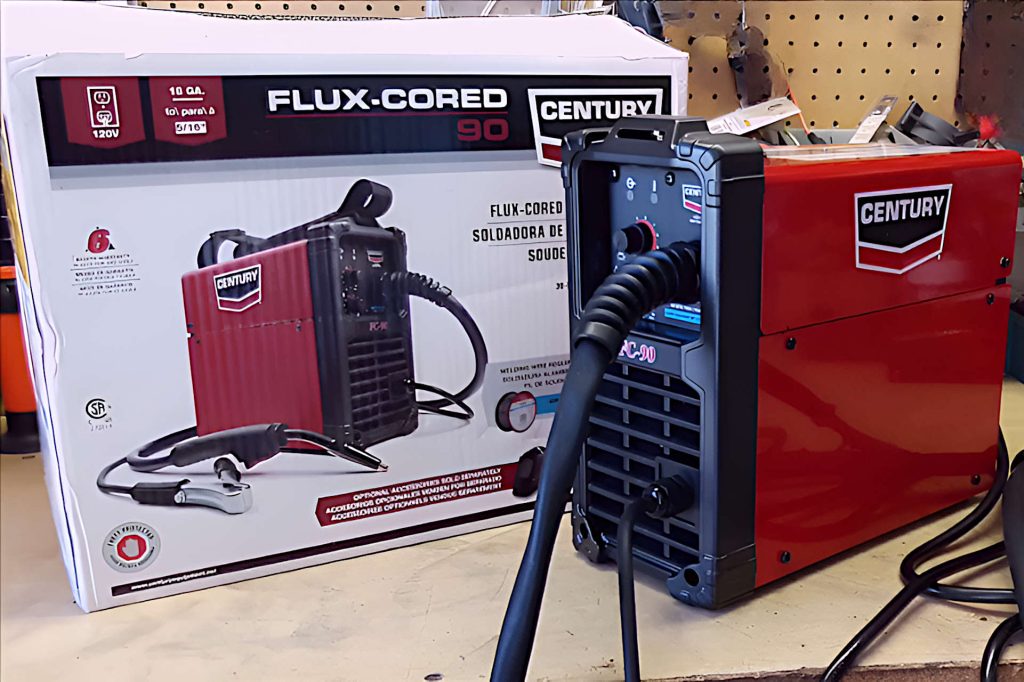
Lincoln Electric FC90 Flux Core Wire Feed Welder and Gun, 90 Amp, 120V, Inverter Power Source for Easy Operation, Portable Shoulder Strap, Best for Small Welding Jobs
Flux-Core Arc Welding | MIG Welding | |
---|---|---|
Definition | A welding process that uses a continuously-fed consumable electrode, with a flux compound that shields the weld area and produces a gas to protect the weld pool from atmospheric contamination. | A welding process that uses a continuously-fed consumable wire electrode, and a shielding gas to protect the weld from atmospheric contamination. |
Pros | High deposition rate, deep penetration, can be used in outdoor conditions. | Clean and precise welds, can be used on a variety of materials, faster than Flux-Core welding. |
Cons | Higher spatter levels, requires a higher level of skill, more expensive equipment. | Shallow penetration, limited to indoor use, can be affected by wind. |
Deposition rate | High | Lower than Flux-Core |
Penetration depth | Deep | Shallow |
Spatter levels | Higher | Lower |
Equipment cost | More expensive | Less expensive |
Skill level required | Higher | Lower |
Materials that can be welded | Thick materials, primarily steel and stainless steel. | Wide range of materials including aluminum, copper, and nickel alloys. |
Aluminum | Not recommended | Suitable |
Cast iron | Suitable | Not recommended |
Thin stock | Not recommended | Suitable |
Thick stock | Suitable | Suitable |
Learning curve | Steep | Relatively shallow |
Wire cost | Relatively low | Relatively high |
Operating cost | No gas but higher wire cost | Gas but lower wire cost |
Gas tank requirement | Not required | Required |
Surface prep | Minimal surface prep required | Requires clean, smooth surfaces |
Wind | Less affected | More affected |
Bead appearance | Coarse | Clean and precise |
Post-clean up | Slag removal required | Minimal clean up required |
Mobility of equipment | High mobility | Limited mobility |
Differences Between Flux-Core and MIG Welding
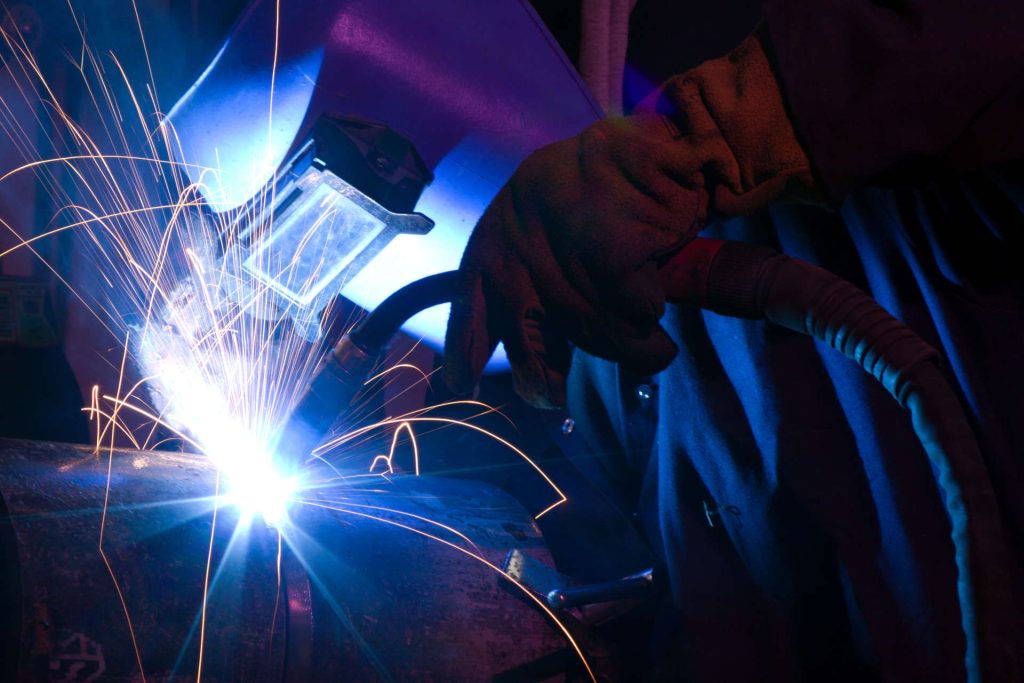
There are various factors than need to be assessed when looking at the differences between flux-cored and normal MIG Welding. The most important are deposition rates, splatter control, penetration and the skill levels that are required. We also have to consider materials and equipment and consumable costs.
Deposition Rate
Deposition rate is an important factor in welding as it determines the productivity and efficiency of the welding process. Flux-Core welding typically has a higher deposition rate than MIG welding, which makes it suitable for welding thicker materials and for applications where speed and efficiency are a priority.
The higher deposition rate of Flux-Core welding is due to the use of a consumable electrode that contains a flux core. As the electrode melts, the flux core releases shielding gases that protect the weld from atmospheric contamination. The shielding gases also help to stabilize the arc and increase the heat input, which results in a higher deposition rate.
On the other hand, MIG welding uses a solid wire electrode that is fed through a welding gun and a shielding gas is used to protect the weld from atmospheric contamination. MIG welding produces a lower deposition rate than Flux-Core welding, but it offers greater control and precision over the welding process, making it suitable for thinner materials and for applications that require a high-quality weld.
It is important to note that the deposition rate of Flux-Core welding can be further increased by increasing the welding amperage, which also increases the heat input. However, increasing the amperage can also increase the risk of burn-through and other welding defects, so it is important to balance the welding parameters to achieve the desired deposition rate without compromising the quality of the weld.
Penetration Depth
Penetration depth is a critical factor in welding as it determines the strength and integrity of the weld joint. Penetration depth refers to the depth that the weld penetrates into the base metal.
Flux-Core welding typically produces deeper penetration than MIG welding due to the higher heat input and the use of a flux core in the consumable electrode. The flux core releases gases that provide additional shielding and also help to increase the heat input. This higher heat input results in deeper penetration, making Flux-Core welding suitable for welding thicker materials and for applications that require a strong and durable weld.
In contrast, MIG welding produces less penetration than Flux-Core welding due to the lower heat input and the use of a solid wire electrode. MIG welding is more suitable for thinner materials and for applications that require a more precise and controlled weld.
It is important to note that the penetration depth of Flux-Core welding can be further increased by increasing the welding amperage and the travel speed. However, increasing the amperage and travel speed can also increase the risk of burn-through and other welding defects, so it is important to balance the welding parameters to achieve the desired penetration depth without compromising the quality of the weld.
Overall, the choice between Flux-Core and MIG welding depends on the specific requirements of the welding application. If the application requires a high deposition rate and deep penetration, then Flux-Core welding may be the best option. On the other hand, if the application requires a precise and controlled weld with less penetration, then MIG welding may be the better choice.
Spatter Levels
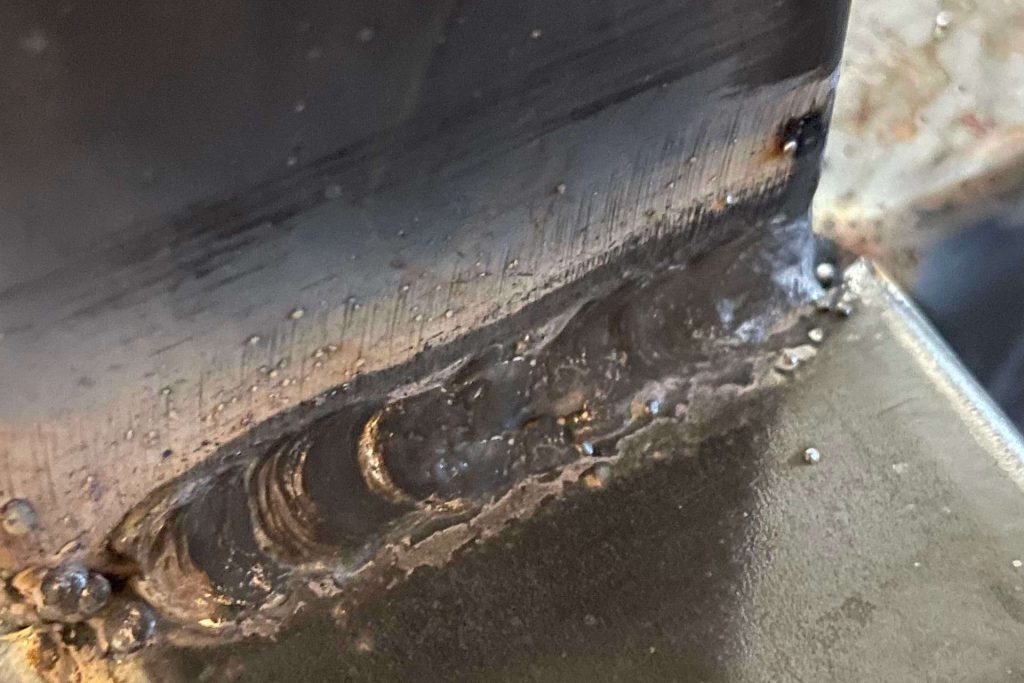
Spatter is a common issue in welding that occurs when droplets of molten metal from the welding process splash onto the workpiece or surrounding areas. Spatter can cause issues such as poor weld quality, increased post-weld clean-up time, and even safety hazards if the spatter lands on skin or clothing.
Flux-Core welding typically produces higher levels of spatter compared to MIG welding due to the use of the flux core in the consumable electrode. The flux core creates a more reactive environment in the welding arc, which can cause more splatter. Additionally, the higher heat input and higher welding amperage used in Flux-Core welding can also contribute to increased spatter.
In contrast, MIG welding typically produces less spatter due to the use of a solid wire electrode and a more stable welding arc. MIG welding also requires less welding amperage, which reduces the amount of molten metal in the weld pool, resulting in less spatter.
However, it is important to note that the spatter levels in both Flux-Core and MIG welding can be influenced by several factors, including the welding parameters, the welding technique, and the cleanliness of the workpiece. For example, using the correct welding technique and ensuring that the workpiece is free of dirt, oil, or other contaminants can help to reduce spatter levels in both Flux-Core and MIG welding.
In conclusion, while Flux-Core welding typically produces higher spatter levels than MIG welding, the spatter levels can be minimized through proper welding techniques and workpiece preparation. Ultimately, the choice between Flux-Core and MIG welding will depend on the specific requirements of the welding application, including the desired spatter levels.
Equipment and Consumable Cost
Flux-Core welding equipment tends to be more expensive than MIG welding equipment. This is because Flux-Core welding requires a specific type of welding machine, such as the Lincoln FC90 flux core welder, that can accommodate the flux core electrode. MIG welding equipment, on the other hand, is more widely available and can be used for a variety of welding applications.
However, more recently many MIG machines have been designed and sold to enable you to use your MIG welder to feed flux-cored wire. In terms of equipment this has substantially reduced the difference in cost between the two applications. Indeed ypu will often hear flux-cored welding referred to as ‘flux-cored MIG welding.’
When it comes to consumables then the cost of the filler wire is much less expensive for standard MIG applications than when using flux-cored wire. But gas usage is also a factor. Generally, you don’t need to use gas when using flux cored wire with a MIG or dedicated flux core machine. However, in some situations you can dual shield with a reduced amount of gas.
Materials That Can be Welded
Flux-Core welding and MIG welding are both versatile welding processes that can be used to weld a wide range of materials. However, each process has its limitations and is better suited to certain materials than others.
Flux-Core welding is particularly well-suited for welding thick materials and for outdoor welding applications. The flux core in the consumable electrode provides a shielding gas that protects the weld pool from atmospheric contaminants, making it less susceptible to porosity and other weld defects. Flux-Core welding is also capable of producing strong welds in materials with heavy rust, mill scale, or other surface contaminants, which can make it a good choice for welding dirty or corroded materials.
MIG welding, on the other hand, is better suited for welding thinner materials and for indoor welding applications. MIG welding produces a lower heat input and smaller weld pool, which makes it less likely to warp or distort thin materials. MIG welding is also a good choice for welding non-ferrous materials like aluminum, copper, and brass, which require a different type of shielding gas and welding wire than ferrous materials like steel.
In addition to the material type, the thickness of the material is also an important consideration when choosing between Flux-Core and MIG welding. Flux-Core welding is typically used for welding materials that are 1/8 inch or thicker, while MIG welding is better suited for materials that are 1/8 inch or thinner.
In conclusion, while both Flux-Core and MIG welding are capable of welding a wide range of materials, each process has its strengths and limitations. The choice between the two processes will depend on the specific requirements of the welding application, including the material type and thickness, as well as other factors like welding position and desired weld quality.
Skill Level Required
Flux-Core and MIG welding are both relatively easy welding processes to learn, but they do require different levels of skill and experience to master.
MIG welding is often considered to be the easier of the two processes to learn. MIG welding machines are typically more user-friendly than Flux-Core machines, with fewer settings and controls to adjust. MIG welding produces a smooth, consistent weld bead, which makes it easier to control and produces more consistent results. MIG welding is also more forgiving of mistakes, such as welding too hot or too cold, which can lead to weld defects like porosity or lack of fusion.
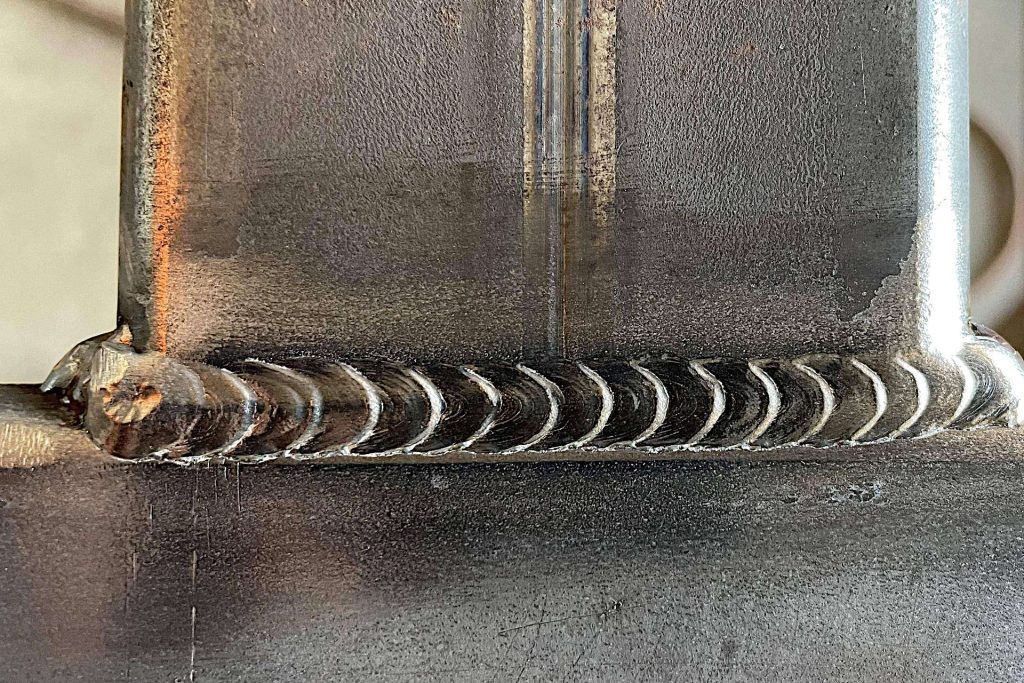
Flux-Core welding, on the other hand, requires more skill and experience to master. The process is more complex than MIG welding, with a wider range of settings and controls to adjust. Flux-Core welding also produces more spatter and smoke than MIG welding, which can make it more difficult to see the weld pool and control the arc. Additionally, Flux-Core welding requires more precise electrode manipulation, including maintaining the correct distance between the electrode and the workpiece, to achieve a strong, consistent weld.
Overall, both Flux-Core and MIG welding can be learned with proper training and practice. However, MIG welding is generally considered to be the easier process to learn for beginners, while Flux-Core welding requires more experience and skill to master.
Which Method to Use?
Choosing between Flux-Core and MIG welding depends on a number of factors, including the project requirements, the operator’s skill level, and the environment in which the welding will take place.
Consideration of the Project Requirements
The type of project being welded will play a significant role in determining which welding process to use. For example, if the project involves welding thick steel plates, Flux-Core welding may be the better choice because it can provide deeper penetration and faster deposition rates. On the other hand, if the project involves welding thin sheet metal, MIG welding may be the better choice because it produces a smoother, more controlled weld bead.
Consideration of the Welding Operator’s Skill Level
The welding operator’s skill level is also an important consideration. As previously discussed, MIG welding is generally considered to be easier to learn and master than Flux-Core welding. If the operator is a beginner, MIG welding may be the better choice because it is easier to control and produces more consistent results. However, if the operator is experienced and skilled in Flux-Core welding, that process may be the better choice for certain projects.
Consideration of the Environment
The welding environment is another important factor to consider when choosing between Flux-Core and MIG welding. For example, if the welding will take place outdoors in windy conditions, Flux-Core welding may be the better choice because it produces less affected by wind and less affected by surface contaminants. On the other hand, if the welding will take place in a controlled indoor environment with good ventilation, MIG welding may be the better choice because it produces less smoke and spatter.
Summary MIG Welding versus Flux- Cored Arc Welding
In summary, choosing between Flux-Core and MIG welding requires careful consideration of the project requirements, the operator’s skill level, and the welding environment. Here are some general guidelines to follow:
- If the project involves welding thicker materials and the operator is experienced in Flux-Core welding, that process may be the better choice.
- If the project involves welding thinner materials or the operator is a beginner, MIG welding may be the better choice.
- If the welding will take place outdoors in windy conditions or on dirty surfaces, Flux-Core welding may be the better choice.
- If the welding will take place indoors with good ventilation, MIG welding may be the better choice.
Ultimately, the decision of which welding process to use should be based on a careful analysis of the specific project requirements and conditions, and the welding operator’s experience and skill level.
Further Reading
- Universal Technical Institute: What Is GMAW Welding (MIG) & How Does it Work?
- Midlands Technical College: MIG and Flux Cored Welder
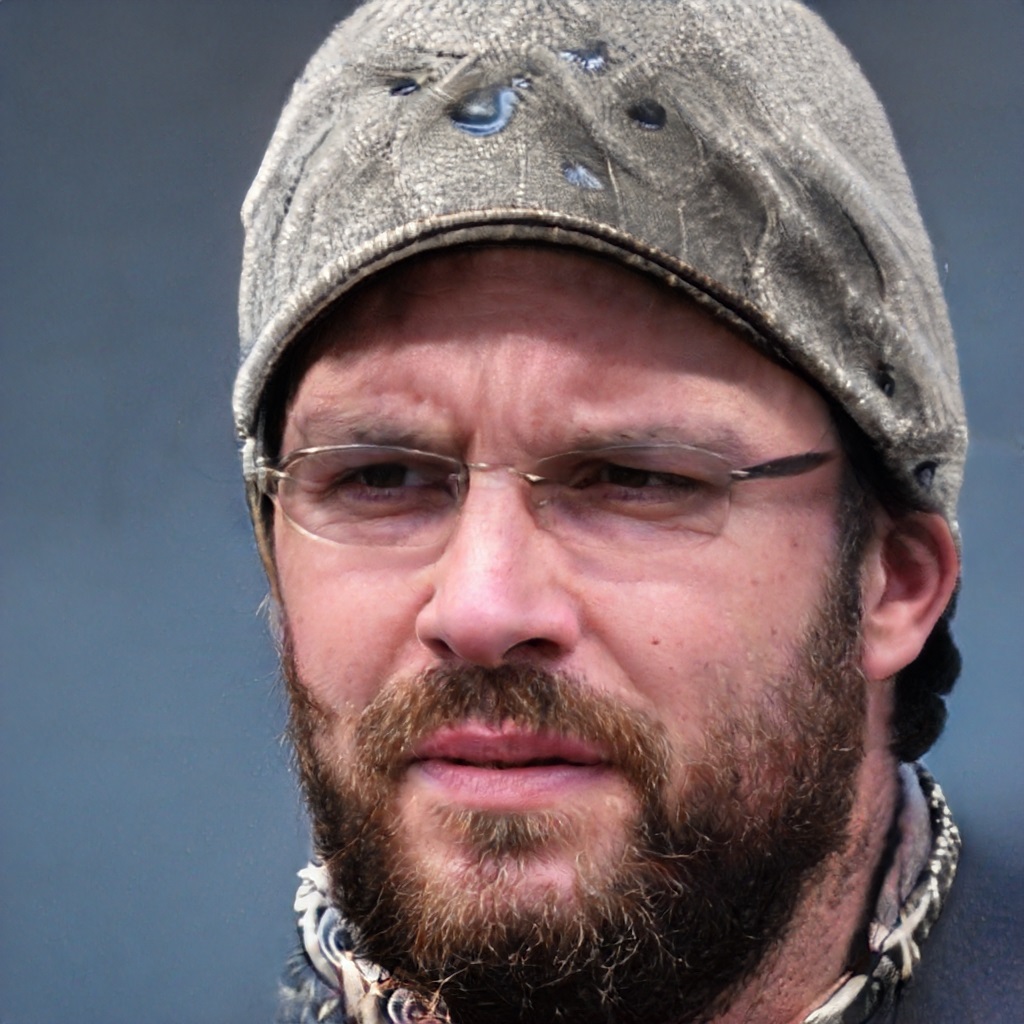
I’ve been involved in the welding industry for over twenty years. I trained in various engineering shops working on various projects from small fabrication and repairs through to industrial projects.I specialize in welding aluminum and food grade stainless steel and an now run an engineering shop fabricating equipment for the food industry.