What is the Difference Between AC and DC Welding?
americanindustrialsupl and its partners may earn a commission if you purchase a product through one of our links.
AC and DC welding are two different types of welding currents that affect how the arc is created and maintained between the electrode and the workpiece. AC stands for alternating current, which changes its direction periodically. DC stands for direct current, which flows in one direction only. The choice of welding current can have a significant impact on the welding process and the weld quality. In this article, we will explore the difference between AC and DC welding, their pros and cons, their typical applications, and how to select the best one for your needs.
Welding current is the electric current that flows through the welding circuit and creates an arc between the electrode and the workpiece. The arc provides the heat and the filler metal for the weld. There are two primary types of welding current: alternating current (AC) and direct current (DC). Each one has its own advantages and disadvantages, depending on the welding application.
Below, we will explore the differences between AC and DC welding, their strengths and weaknesses, their common applications, and the factors that influence their selection. By the end of this article, you will have a better understanding of how to choose the right welding current for your specific needs.
AC Welding: Strengths and Weaknesses
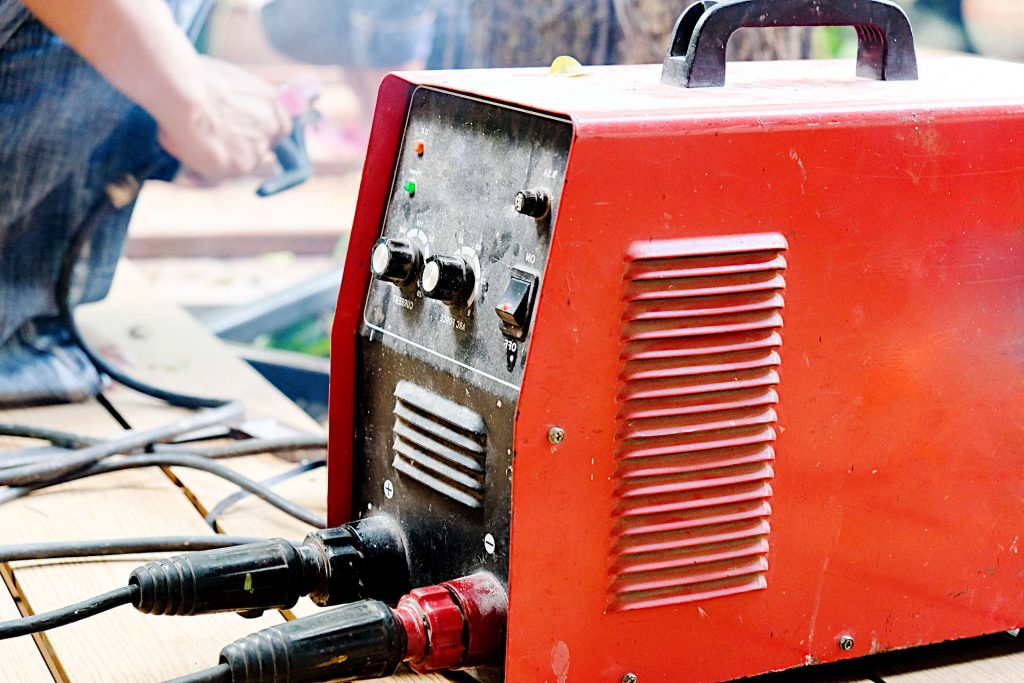
AC welding is a welding method that uses an alternating current to power the arc. An alternating current is an electric current that reverses its direction many times per second. For example, a 60-hertz current will change its polarity 120 times per second. This means that the electrode and the workpiece will switch between being positive and negative poles.
Exploring AC Welding
AC welding has some distinctive features that differentiate it from other welding methods. Some of these features are:
- AC welding does not require a constant polarity for the electrode. This means that you can use any type of electrode with AC welding, regardless of whether it is designed for positive or negative polarity.
- AC welding produces a high heat output and a high melting capacity. This means that you can weld thicker metals and faster deposition rates with AC welding than with DC welding.
- AC welding can handle various metals, including aluminum and magnesium. These metals have a tendency to form an oxide layer on their surface that hinders the arc penetration and the weld quality. AC welding can break through this oxide layer by alternating between positive and negative polarity.
Strengths of AC Welding
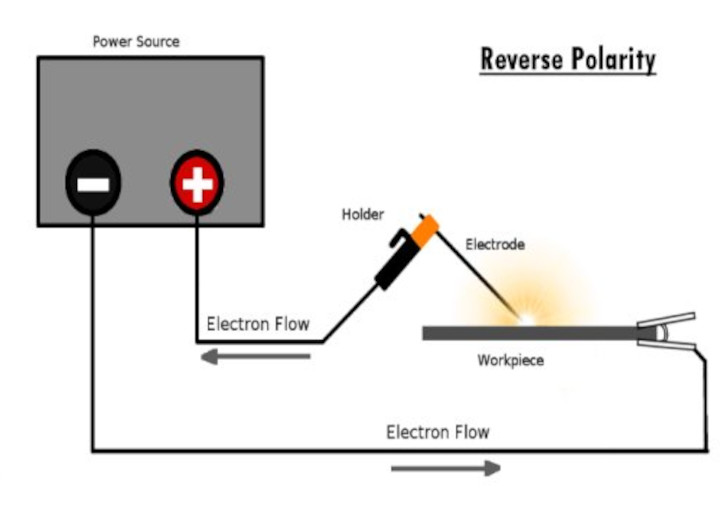
AC welding has some advantages over DC welding in certain situations. Some of these advantages are:
- AC welding can fix arc blow problems. Arc blow is a phenomenon that occurs when the magnetic field around the arc deflects it from its intended path. This can cause poor weld quality, spatter, porosity, and lack of fusion. Arc blow is more likely to happen when welding magnetized materials or near magnetic fields. AC welding can prevent arc blow by constantly changing the direction of the current and canceling out the magnetic effects.
- AC welding enables effective aluminum welding. Aluminum is a widely used metal in various industries, such as aerospace, automotive, marine, and construction. However, aluminum is also a challenging metal to weld because of its high thermal conductivity, low melting point, and oxide layer formation. AC welding can overcome these challenges by providing high heat output, deep penetration, and oxide layer removal.
- AC welding machines are cheaper than DC equipment. AC welding machines do not require any internal components to convert or rectify the current from the power source. This makes them simpler, lighter, and more affordable than DC machines.
Weaknesses of AC Welding
AC welding also has some drawbacks that limit its applicability in some cases. Some of these drawbacks are:
- AC welding generates more spatter than DC welding. Spatter is the molten metal droplets that fly out of the arc and land on the surrounding area. Spatter can cause aesthetic problems, safety hazards, and extra cleanup work. Spatter is more common with AC welding because of the frequent arc extinguishing and reigniting that occurs with every polarity change.
- AC welding has limited penetration compared to DC welding. Penetration is the depth of fusion between the base metal and the filler metal in a weld joint. Penetration is important for weld strength, durability, and resistance to cracking. Penetration is affected by several factors, such as heat input, electrode size, travel speed, and polarity. Generally speaking, DC welding provides more penetration than AC welding because of its constant heat input and stable arc.
- AC welding poses challenges in maintaining a stable arc during welding. A stable arc is essential for producing consistent and quality welds. A stable arc depends on several factors, such as electrode type, electrode angle, arc length, travel speed, and current setting. AC welding makes it harder to maintain a stable arc because of its fluctuating current and polarity.
DC Welding: Advantages and Disadvantages
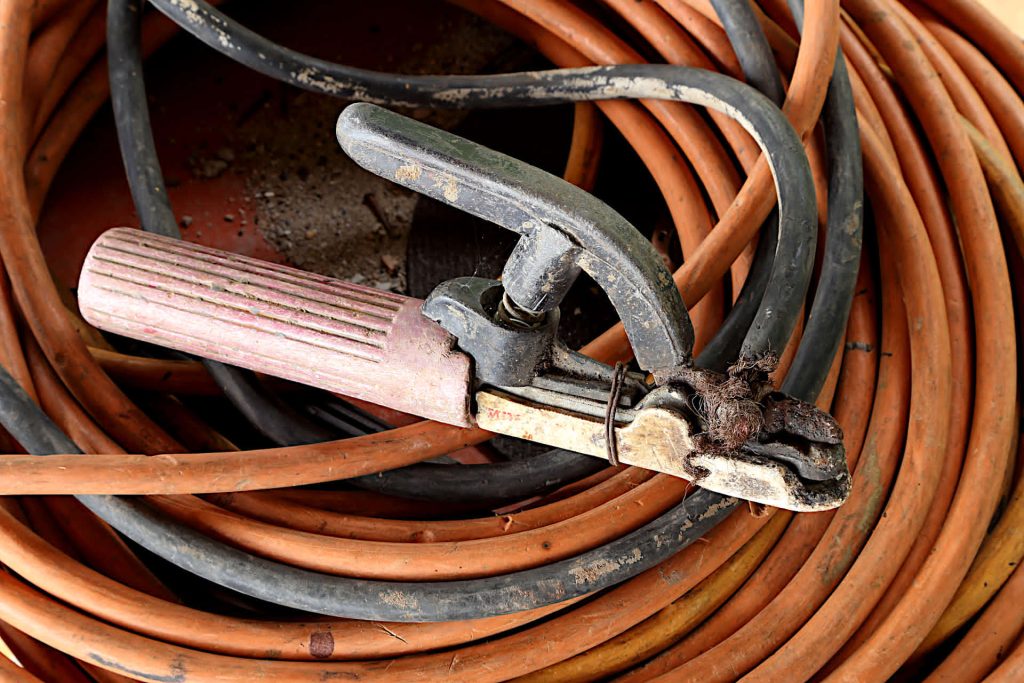
DC welding which can be Direct Current Electrode Positive (DCEP) or Direct Current Electrode Negative (DCEN), is a welding method that uses a direct current to power the arc. A direct current is an electric current that flows in one direction only. This means that the electrode and the workpiece have a fixed polarity throughout the welding process.
Understanding DC Welding
DC welding has two main types of polarity: straight polarity and reverse polarity. Straight polarity, also known as direct current electrode negative (DCEN), means that the electrode is negative and the workpiece is positive. Reverse polarity, also known as direct current electrode positive (DCEP), means that the electrode is positive and the workpiece is negative.
The choice of polarity affects the heat distribution, the penetration, and the deposition rate of the weld. Generally speaking, straight polarity provides more heat to the workpiece and less heat to the electrode, resulting in deeper penetration and faster travel speed. Reverse polarity provides more heat to the electrode and less heat to the workpiece, resulting in higher deposition rate and smoother weld surface.
Advantages of DC Welding
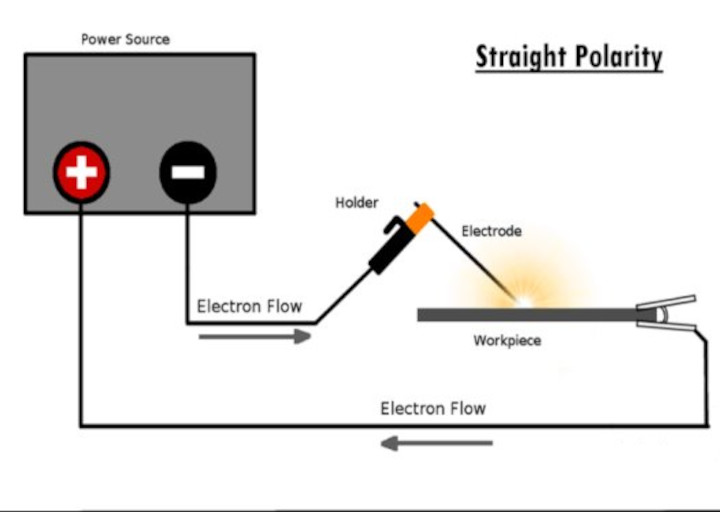
DC welding has some advantages over AC welding in most welding applications. Some of these advantages are:
- DC welding offers enhanced control over heat input. Heat input is the amount of heat transferred to the weld joint per unit length. Heat input is influenced by several factors, such as current, voltage, travel speed, and polarity. Heat input affects the weld quality, the distortion, and the residual stress of the weldment. DC welding allows you to adjust the heat input by changing the polarity, the current setting, and the travel speed.
- DC welding delivers deeper and more controlled penetration. As mentioned earlier, penetration is crucial for weld strength and durability. DC welding provides more penetration than AC welding because of its constant current and stable arc. Moreover, DC welding allows you to control the penetration by choosing between straight polarity and reverse polarity.
- DC welding produces lower spatter than AC welding. Spatter is undesirable for many reasons, such as aesthetics, safety, and cleanup. DC welding reduces spatter by providing a smooth and steady arc that does not extinguish and reignite frequently.
Disadvantages of DC Welding
DC welding also has some limitations that restrict its use in some situations. Some of these limitations are:
- DC welding has reduced suitability for certain metals like aluminum. Aluminum is a difficult metal to weld with DC because of its oxide layer, high thermal conductivity, and low melting point. DC welding cannot break through the oxide layer effectively because it does not alternate between positive and negative polarity. Moreover, DC welding can cause excessive melting and burn-through of aluminum because it does not provide enough heat variation.
- DC welding requires more complex equipment setup and maintenance. DC welding machines need internal components to convert or rectify the current from the power source. This makes them more complicated, heavier, and more expensive than AC machines. Additionally, DC welding machines need more frequent maintenance and calibration to ensure their proper functioning.
- DC welding can cause tungsten contamination in TIG welding. TIG welding is a type of arc welding that uses a non-consumable tungsten electrode to create an arc between the electrode and the workpiece. TIG welding requires a shielding gas, such as argon or helium, to protect the arc and the weld pool from atmospheric contamination. TIG welding can use either AC or DC current, depending on the metal being welded. However, when using DC with reverse polarity (DCEP), there is a risk of tungsten contamination in the weld pool. This happens because the positive electrode attracts electrons from the negative workpiece, causing some tungsten particles to detach from the electrode tip and enter the weld pool.
Comparing AC and DC Welding Applications
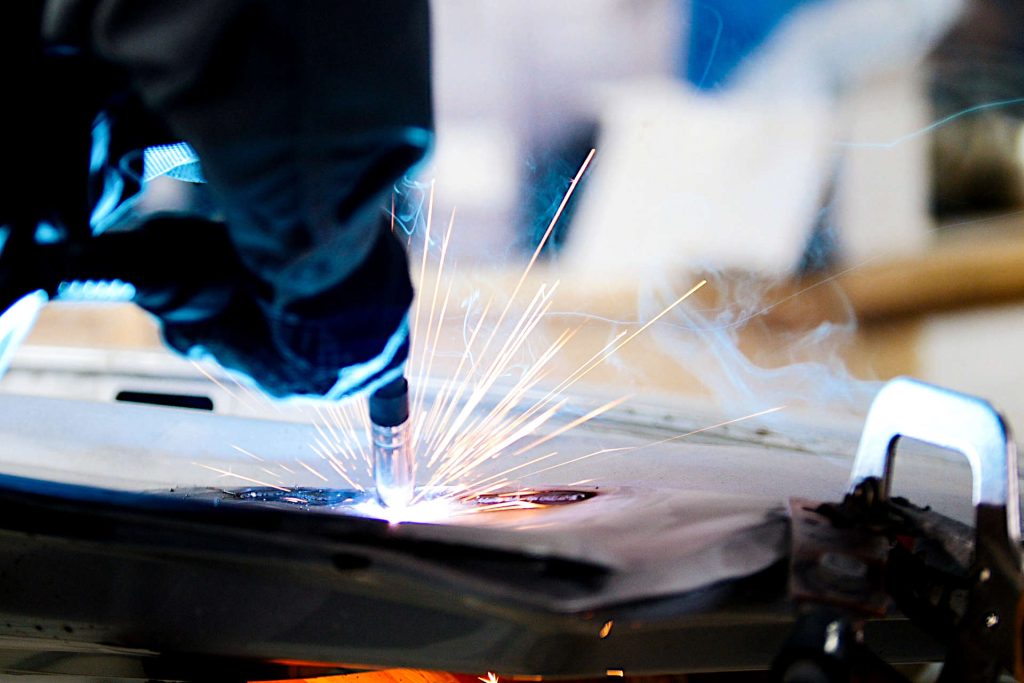
AC and DC welding have different applications depending on the industry, the project, and the metal being welded. Here are some examples of where each type of welding current is more suitable.
AC Welding Applications
AC welding is more suitable for applications that require high heat output, high deposition rate, or effective aluminum welding. Some examples are:
- Shipbuilding: Shipbuilding involves welding thick plates of steel or aluminum that require high heat output and high deposition rate to achieve adequate fusion and fill large gaps. AC welding can provide these benefits by producing a high-intensity arc that can melt thick metals quickly.
- Pipeline: Pipeline involves welding long seams of steel pipes that require high heat output and high deposition rate to ensure complete penetration and fill large gaps. AC welding can provide these benefits by producing a high-intensity arc that can melt thick metals quickly.
- Aerospace: Aerospace involves welding thin sheets of aluminum or magnesium alloys that require effective oxide layer removal and low distortion. AC welding can provide these benefits by alternating between positive and negative polarity that can break through the oxide layer and vary the heat input.
DC Welding Applications
DC welding is more suitable for applications that require controlled heat input, deep penetration, or low spatter production. Some examples are:
- Automotive: Automotive involves welding thin sheets of steel or stainless steel that require controlled heat input and deep penetration to avoid burn-through and ensure strength. DC welding can provide these benefits by using straight polarity (DCEN) which can deliver more heat to the workpiece and less heat to the electrode.
Construction: Construction involves welding structural steel beams or columns that require controlled heat input and deep penetration to avoid distortion and ensure durability. DC welding can provide these benefits by using straight polarity (DCEN) that can deliver more heat to the workpiece and less heat to the electrode.
Factors Influencing AC and DC Welding Selection
Choosing between AC and DC welding is not a simple matter of preference or convenience. There are several factors that you need to consider before making a decision. Some of these factors are:
Material and Project Considerations
The most important factor in selecting a welding current is the type of material you are welding. Different metals have different characteristics, such as melting point, thermal conductivity, oxide layer formation, and magnetic properties. These characteristics affect the weldability, the weld quality, and the weld performance of the metal.
For example, aluminum is a metal that requires AC welding because of its oxide layer, high thermal conductivity, and low melting point. Steel is a metal that can be welded with either AC or DC, depending on the thickness, the joint design, and the desired weld appearance. Stainless steel is a metal that requires DC welding because of its low thermal conductivity, high melting point, and corrosion resistance.
Another factor to consider is the project specifications. Depending on the project, you may have different requirements for the weld strength, the weld appearance, the weld speed, and the weld cost. These requirements may influence your choice of welding current.
For example, if you need a strong and durable weld, you may prefer DC welding because of its deeper penetration and lower spatter. If you need a smooth and clean weld, you may prefer AC welding because of its higher deposition rate and oxide layer removal. If you need a fast and cheap weld, you may prefer AC welding because of its simpler equipment and faster travel speed.
Skill Level and Equipment Availability
Another factor to consider is your skill level as a welder. Depending on your experience and proficiency, you may find one type of welding current easier or harder to use than the other. You may also have a personal preference or comfort level with one type of welding current over the other.
For example, if you are a beginner or an intermediate welder, you may find AC welding easier to use because of its simpler equipment setup and maintenance. You may also find AC welding more forgiving because of its high heat output and high deposition rate. If you are an advanced or an expert welder, you may find DC welding more challenging and rewarding because of its enhanced control over heat input and penetration. You may also find DC welding more versatile because of its ability to handle different metals and polarities.
Another factor to consider is the availability of equipment. Depending on your location and budget, you may have access to different types of welding machines and accessories. You may also have different power sources and outlets available for your welding operations.
For example, if you live in a rural area or have a limited budget, you may only have access to AC welding machines that run on standard household power outlets. If you live in an urban area or have a generous budget, you may have access to DC welding machines that run on industrial power outlets or generators.
Final Thoughts: Difference Between AC and DC Welding
AC and DC welding are two different types of welding currents that have their own strengths and weaknesses. AC welding is more suitable for applications that require high heat output, high deposition rate, or effective aluminum welding. DC welding is more suitable for applications that require controlled heat input, deep penetration, or low spatter production.
The choice between AC and DC welding depends on several factors, such as material type, project specifications, skill level, and equipment availability. You need to consider all these factors before making a decision that suits your specific needs.
Welding is a complex and fascinating process that requires knowledge, skill, and practice. By understanding the differences between AC and DC welding, you can improve your welding performance and quality. You can also expand your welding opportunities and possibilities. We hope this article has helped you learn more about AC and DC welding. If you have any questions, please feel free to contact us. We would love to hear from you!
Videos
Resources
- Journal of Manufacturing Science and Engineering: A Comparative Study of Single-Phase Ac and Multiphase Dc Resistance Spot Welding
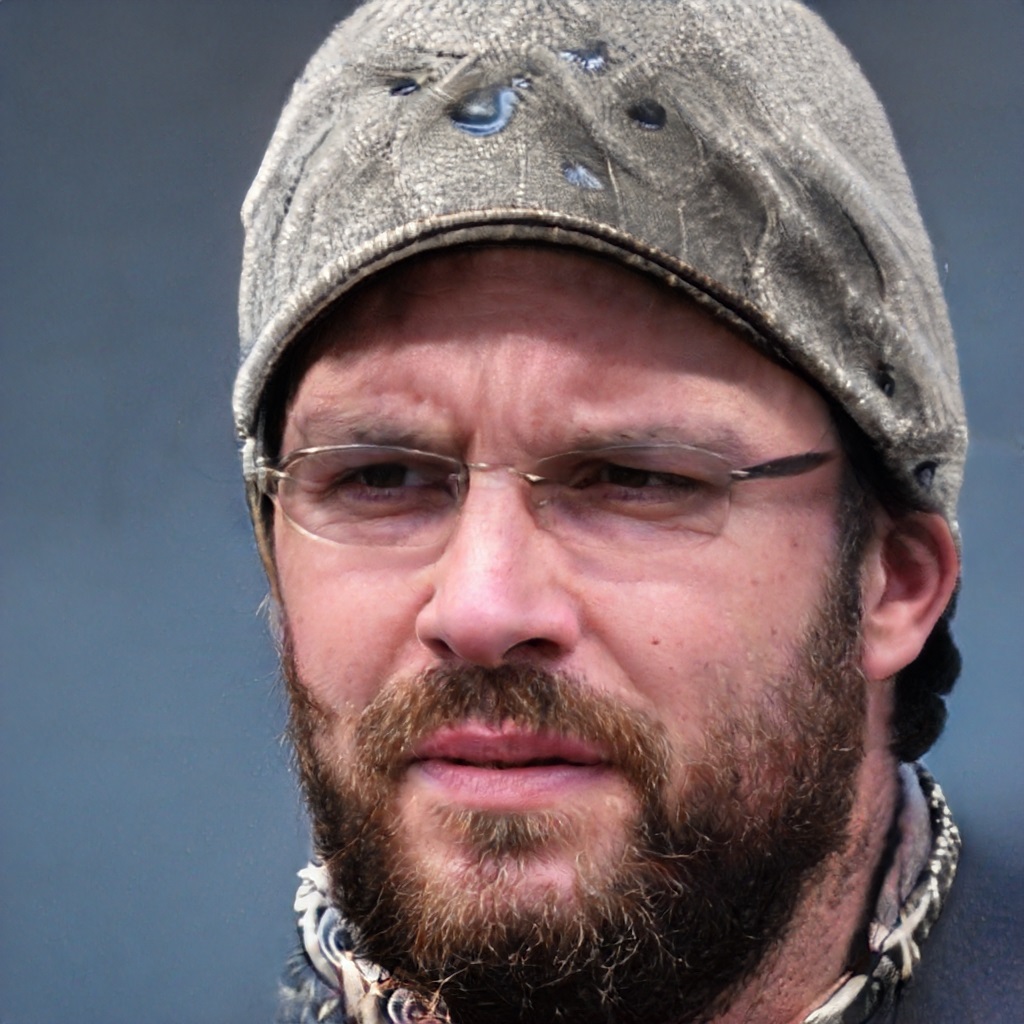
I’ve been involved in the welding industry for over twenty years. I trained in various engineering shops working on various projects from small fabrication and repairs through to industrial projects.I specialize in welding aluminum and food grade stainless steel and an now run an engineering shop fabricating equipment for the food industry.