Stick Welding (SMAW) | What is Stick Welding and How Does it Work?
Shielded Metal Arc Welding (SMAW), also known as Manual Metal Arc Welding MMA) or more commonly as Stick Welding, is a type of welding that uses a filler rod or wire as one of its electrodes. The other electrode is usually supplied by a power source connected to the work-piece through a cable. In this method, the filler rod or wire is fed into the molten pool created during the welding operation. This technique has been used for decades and it’s still widely used today. It is also known as stick welding because the filler rod or wire resembles a wooden dowel.
This welding method involves creating an arc between the electrode and a work-piece, with the heat of the arc melting the electrode coating and forming a protective slag. The weld metal is created by the core electrode wire as well as iron powder in the coating. After welding, the slag layer on top of the joint must be removed.
During the process, the flux condenses into a gas that protects the electric arc that develops between the electrode and the metal being welded. This prevents contamination from ambient gases and makes Stick Welding, as opposed to MIG (GMAW), more suitable for outdoor operations.
Shielded Metal Arc Welding Equipment
Shielded metal arc welding equipment typically consists of several components:
The Power Source: Heart of SMAW
At the core of SMAW equipment is the power source. The power supply provides a continuous output, which ensures that the current (and hence the heat) remains reasonably constant. You have two types: constant current (CC) and constant voltage (CV).
For stick welding, CC is your general go-to. It adjusts voltage to maintain a steady current, essential for a stable arc. Sustaining a suitable continuous arc distance is challenging if a constant voltage power source is utilised instead, as this might generate extreme heat changes, making welding more challenging.
However, constant voltage can be used in certain situation if you are a more experienced welder. Because with constant voltage the current is not kept perfectly constant, expert welders executing complex welds can adjust the arc length to generate slight variations in the current.
Step-Down Transformer
The stick welding process employs a step-down transformer and a rectifier to convert alternating power to direct current. The major rationale for employing the transformer is to enhance the current while simultaneously lowering the high voltage. An inverter and multiple coils are common types of devices used for this purpose. The coil alters the current by changing the number of turns in the coil or the spacing in between two coils. Inverters are portable and can alter current parameters quickly.
Electrode Holder: Your Welding Wand
Next is the electrode holder, often called the stinger. It’s not just a clamp; it’s your connection to the work. A good holder feels right in your hand, balances well, and provides excellent conductivity. It’s crucial for precise control.
Ground Clamp
Often overlooked, the ground clamp is vital. A strong, clean connection is a must. A poor ground leads to frustrating arc problems. It’s like having a great engine but bad tires; everything else must work in harmony.
Cables
Cables carry current from the power source to the holder and workpiece. There are two types of cable required the Electrode Cable and the Massa Cable.
The electrode cable links the welding machine’s electricity to the electrode used to weld the base metal. The massa cable role is tp connect current from the machine to the base metal; when the base metal and electrode come into contact, the welding process begins.
Flexibility and durability are key. They need to withstand harsh environments and remain pliable for easy movement.
Chipping Hammer and Wire Brush: The Clean-Up Crew
After each weld, slag removal is a must. That’s where your chipping hammer and wire brush come in. These tools are simple but indispensable for clean, quality welds.
Personal Protective Equipment (PPE): Safety First
Now, PPE isn’t part of the machine, but it’s critical. A good helmet with proper shading, durable gloves, and protective clothing are non-negotiable. They’re your first defense against the intense light, heat, and spatter.
Types Of Shielded Metal Arc Welders
There are two types of shielded metal arc welder: stick and automatic. Stick welders require manual feeding of the electrode and have no moving parts. Automatic welders use an automated feeder to position the electrode and control the welding parameters.
Stick Welder Types
Stick welders come in different sizes, shapes and styles. I’ve worked with various welder types, each having its unique features and applications. Let’s break down the common models: single stick welders, double stick welders, and side stick welders.
Single Stick Welders: The Standard Choice
Single stick welders are the most common and versatile. They are ideal for a wide range of applications, from home repairs to professional construction projects. These welders are designed for simplicity and ease of use, making them a great choice for both beginners and seasoned professionals. The key here is their adaptability – they can handle different materials and thicknesses with ease.
Double Stick Welders: For Enhanced Productivity
Double stick welders are a step up in terms of productivity. These are designed for scenarios where higher output is needed. With the capability to operate two electrodes simultaneously, they significantly speed up the welding process. This type is often found in industrial settings where time is of the essence and large volumes of welding work are common. However, they require a bit more skill to operate effectively.
Side Stick Welders: The Niche Specialist
Side stick welders are a bit more specialized. They are designed for specific situations where welding in tight or unusual positions is necessary. These welders have electrodes positioned at different angles, allowing for greater flexibility and reach in confined spaces. They’re not as commonly used as the other two types but are invaluable in certain industrial or construction scenarios where traditional welders can’t quite fit the bill.
Choosing the Right Type
When selecting a stick welder, consider the nature of your projects. For general use, a single stick welder offers sufficient flexibility. If you’re handling large volumes or industrial-scale projects, a double stick welder might be your ally. And for those tricky, hard-to-reach jobs, a side stick welder could be the solution. Remember, each type brings its own strengths to the table, and the best choice depends on your specific welding needs.
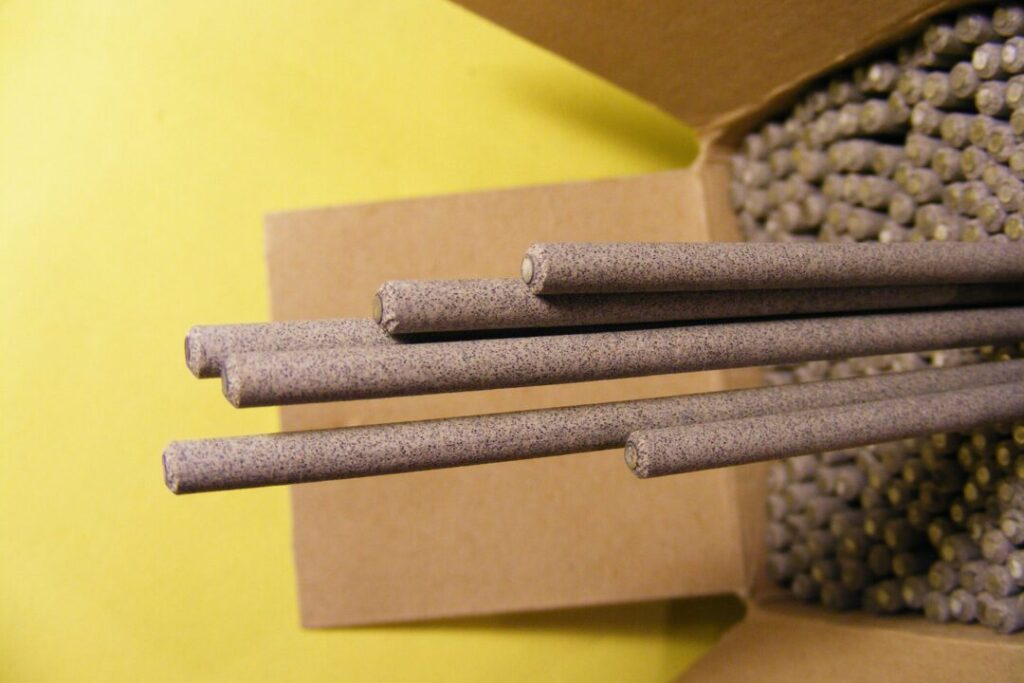
Stick Welding (Shielded Metal Arc Welding) Process
With 20 years welding stick, I’ve refined a process that ensures quality and efficiency. Here’s a walkthrough of the stick welding (Shielded Metal Arc Welding or SMAW) process, covering the setup, the weld, and the cleanup.
Key steps in the stick welding (Shielded Metal Arc Welding) process, encompassing the setup, the weld, and the cleanup.
Phase | Key Steps | Details |
---|---|---|
The Setup | 1. Selecting the Right Electrode | Choose an electrode matching the metal type and thickness. |
2. Preparing the Equipment | Adjust welder settings to suit the electrode and material. | |
3. Safety Measures | Wear protective gear and ensure a safe, ventilated workspace. | |
4. Workpiece Preparation | Clean the metal surface to remove any rust, paint, or debris. | |
The Weld | 1. Striking the Arc | Touch and lift the electrode to ignite the arc. |
2. Maintaining the Arc | Keep the electrode at an optimal distance from the workpiece. | |
3. Welding Technique | Use a steady, controlled motion, appropriate for the weld type. | |
4. Monitoring Heat | Manage the heat to prevent warping or burn-through. | |
The Cleanup | 1. Removing Slag | Chip off the slag after the weld cools and brush away debris. |
2. Inspection | Check the weld for any flaws like cracks or holes. | |
3. Post-Weld Treatment | Perform any needed grinding for a smooth finish or apply protective coatings, if necessary. |
The Setup: Laying the Groundwork
Selecting the Right Electrode:
The electrode choice is crucial. It should match the metal type and thickness you’re welding. A common choice is the E6013 for mild steel while 7018 electrode is also prevalent, but it varies based on your project. Electrodes can be powered by both AC and DC sources. Not every DC electrode can be used with AC power sources, however AC electrodes can be used with either AC or DC power sources.
The size of the electrode determines the welding current level; manufacturers propose the usual working range and current. An electrode will require around 40A per mm as a rule of thumb for determining an acceptable current level (diameter). As a result, while 160A is the recommended current level for a 4mm diameter electrode, the permissible working range is 140 to 180A.
Reverse polarity is nearly always employed in Stick welding techniques. It aids in providing the optimum bead profile and penetration, as well as reducing excessive spatter, which are beads of liquid metal produced at or near the welding arc.
Preparing the Equipment:
Ensure your welder settings match the electrode and material. The amperage is key – too high and you burn through, too low and you get a weak weld.
Safety Measures:
Gear up with a helmet, gloves, and protective clothing. Ensure your work area is well-ventilated and clear of flammable materials.
Workpiece Preparation:
Clean the metal surfaces. Any rust, paint, or debris can weaken the weld. A good, clean surface is essential for a strong bond.
The Weld: Shielded Metal Arc Welding Process
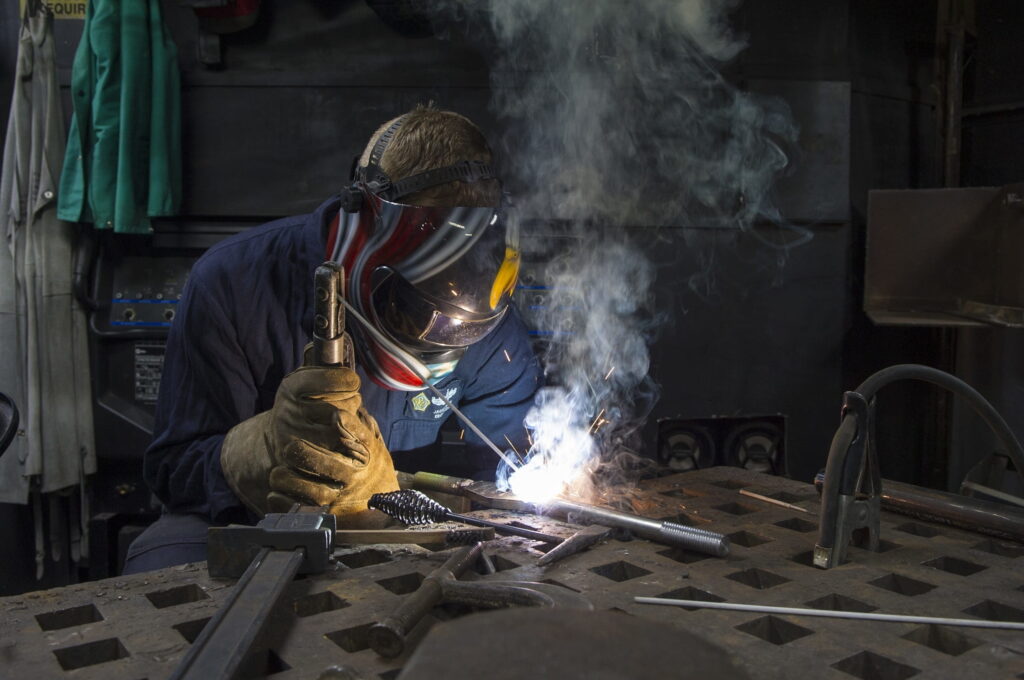
When you weld an electric arc is generated between the metal and the electrode with the assistance of an electric current to connect the metal, this is referred to as striking an arc. The welding power source provides this electric current, which might be alternating or direct current.
Following the welding of a work-piece, a small pool of molten metal is created. As the weld cools a strong joint is formed between the two pieces of metal.
During the weld, the flux coating on the electrode will emit gases that act as a shielding gas and slag layer. The production of this shielding gas and slag layer protects the weld region from atmospheric gases such as nitrogen and oxygen.
To create an electric arc, an electrode is first brought into contact with the work-piece. The electrode then need to be drawn back gently and this drawing back creates the arc and transfer small amounts of electrode to the welding region or work-piece surface.
During the welding process, the welder must be conscious of the need to change the electrode on a frequent basis and to insert a new electrode carefully. The speed of the weld is determined by the welder’s abilities, electrode type, and most importantly, welding location.
- Striking the Arc: Touch the electrode to the workpiece and lift it slightly to ignite the arc. It’s like striking a match – a swift, smooth motion.
- Maintaining the Arc: Keep the electrode at the right distance – too close, and it sticks; too far, and the arc breaks. It’s a delicate dance that requires practice.
- Welding Technique: Use a steady, controlled motion. Whether you’re using a back-and-forth weave or a straight line depends on the weld type. Consistency is key.
- Monitoring Heat: Watch for overheating. Stick welding generates a lot of heat, and managing it is vital for preventing warping or burn-through.
The Cleanup: Finishing Touches
- Removing Slag: Once the weld cools, chip off the slag with a hammer and brush away any debris. This step reveals the quality of your weld beneath.
- Inspection: Examine the weld for any cracks, holes, or inconsistencies. A good weld should be even and consistent.
- Post-Weld Treatment: Depending on the project, you might need to grind the weld for a smooth finish or apply a protective coating.
Stick welding is an art honed by practice and precision. From carefully setting up your equipment and workpiece to the skillful execution of the weld, followed by thorough cleanup and inspection – each step is crucial for a strong, durable weld. Remember, the best welds are not only about strength but also about the finesse and attention to detail you bring to your craft.
Shielding Gas for Stick Welding
While stick welding traditionally doesn’t require external gas due to the flux-coated electrodes, there are scenarios where gas might be employed.
Shielding Gas in Stick Welding: Rare but Relevant
- Flux-Cored Arc Welding (FCAW) Crossover: While not typical in standard stick welding (SMAW), the use of shielding gas is more common in FCAW, which can use similar equipment. Here, some electrodes are designed to work with shielding gas for enhanced protection, especially in outdoor conditions or with specific metals.
- Choosing the Right Gas: If you’re in a situation where shielding gas is beneficial, typically for FCAW, the common gases are:
- Carbon Dioxide (CO2): Economical and effective, CO2 provides deep penetration, suitable for thicker materials.
- Argon and CO2 Mixtures: Offering a smoother arc and less spatter, this mix is ideal for thinner metals and cleaner welds.
- When to Use Shielding Gas in Stick Welding:
- Flux-Cored Electrodes: For certain flux-cored electrodes in FCAW, adding a shielding gas can enhance the weld’s integrity, particularly in windy or unstable environments.
- Material and Thickness: Thicker, more robust materials might benefit from the added protection of a shielding gas, especially in industrial applications.
When to Stick to Traditional, Gasless Welding
- Standard SMAW Applications: In most stick welding scenarios, the flux coating on the electrode provides adequate shielding. This is the hallmark of stick welding – simplicity and effectiveness without the need for external gases.
- Outdoor and Remote Welding: One of the strengths of traditional stick welding is its adaptability to outdoor conditions. Here, the reliance on gas can be a drawback, making gasless welding more practical.
- Cost and Accessibility: Stick welding’s low reliance on additional gases makes it a more cost-effective and accessible option, especially for smaller shops or hobbyists.
While the use of shielding gases in stick welding isn’t common, understanding its application, especially in crossover techniques like FCAW, is valuable. Stick to gasless welding for most SMAW applications, but recognize situations where a shielding gas can enhance your weld, particularly in FCAW. Remember, the choice of technique and materials always dictates the approach in this skilled trade.
Stick Welding Safety (SMAW)
If necessary measures are not followed, Stick Welding, like other welding processes, can be an extremely dangerous and harmful operation. The procedure employs an open electric arc, which increases the danger of burns and possible electrocution.
In order to protect against these dangers, it is important to follow safety procedures when performing stick welding. These include:
- Using only approved electrodes
- Ensuring that all equipment is grounded before use
- Using the correct welding technique
- Preventing access to live parts during welding
- Avoiding exposure to sparks
- Keeping hands away from the welding area
- Always wearing protective clothing
- Notifying your employer about any health conditions you may have
In addition welding helmets with dark viewing windows should always be worn to protect against this exposure to the significant volumes of UV radiation that can be created during the weld.
Translucent welding curtains should also be employed to shield an spectators, especially in industrial settings. These curtains, constructed of polyvinyl chloride plastic film and protect any surrounding people from UV radiation generated by the electric arc, however these curtains should never be used to substitute the filter glass in helmets of the welder.
Advantages and Disadvantages Stick Welding:
There are various advantages and disadvantages to using the Stick welding process that you should consider before opting for this method.
Advantages Stick Welding (SMAW)
- Can be used to weld any sort of connection.
- Stick welding (SMAW) allows for the utilisation of all welding positions.
- We don’t need gas to protect the molten weld metal.
- The tools used in Stick Welding are lightweight and inexpensive.
- There isn’t much prep work required before welding.
Disadvantages Stick Welding (SMAW)
- After the welding operation is completed, you have to clear the slag.
- There is a tendency for the welding rod to cause spatter if the amperage is not dialed in perfectly.
- Only ten to fifteen centimeters of weld metal may be produced by a single electrode.
- Can be a slower process than other types of welding because of the need to change the electrode.
- It is not an automated process, its productivity is lower than that of other welding techniques.
- Stick welding cannot be used on reactive metals such as zirconium and titanium.
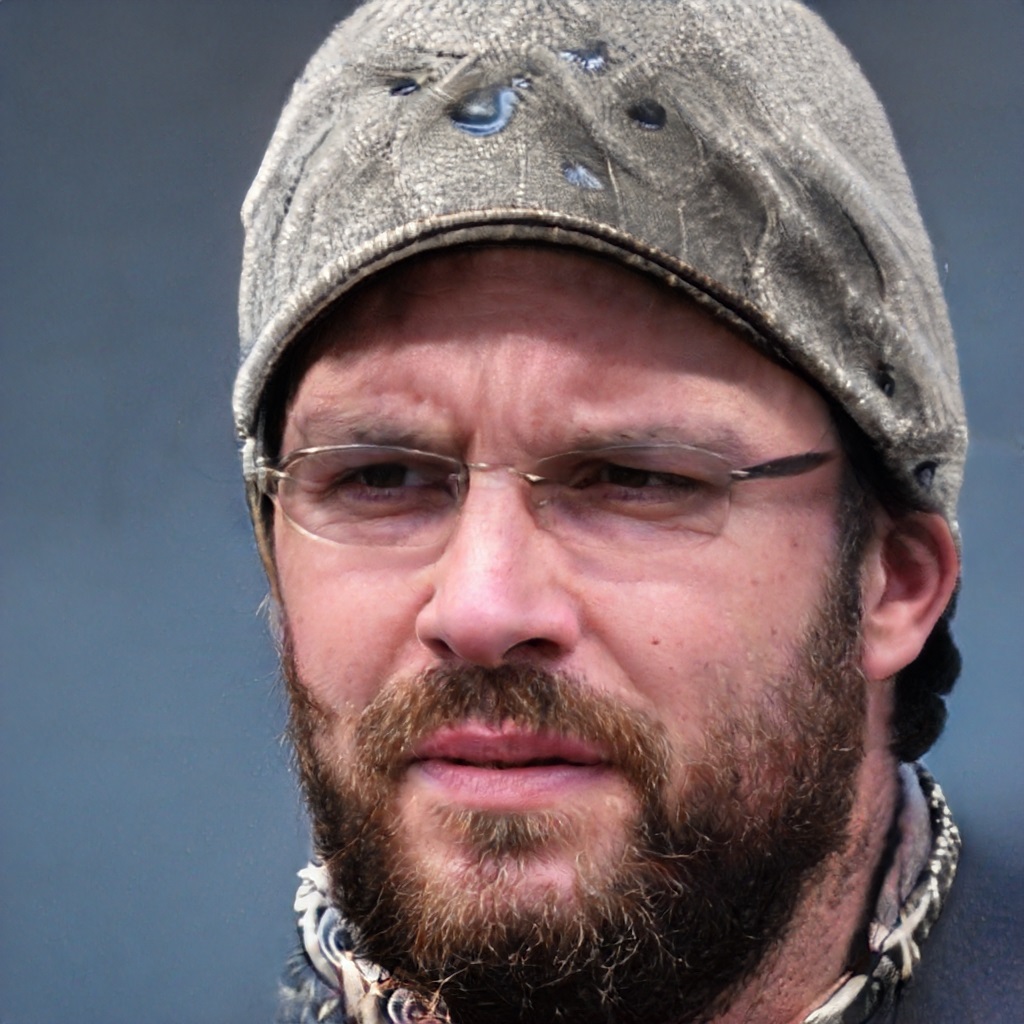
I’ve been involved in the welding industry for over twenty years. I trained in various engineering shops working on various projects from small fabrication and repairs through to industrial projects.I specialize in welding aluminum and food grade stainless steel and an now run an engineering shop fabricating equipment for the food industry.