Stick Welding Problems and Solutions
Welding isn’t just a skill; it’s a craft that combines art, science, and a bit of sweat. Shielded metal arc welding (SMAW) more commonly known as stick welding, in particular, can throw up problems. From the sudden stickiness of an electrode to a sudden porosity of the weld, these issues can become trying. However, in general, each problem has a fairly simple explanation and solution. Below we will look at some of the most common stick welding problems and solutions.
Key Takeaways
- Stick welding challenges are common but manageable with the right knowledge.
- Solutions involve precise technique, correct equipment setup, and regular practice.
- Safety and proper electrode handling are paramount to successful welding outcomes.
Common Stick Welding Challenges and Troubleshooting Tips
Stick welding throws a myriad of challenges at both the novice and the experienced welder. It’s a balancing act between too hot or too cold, too fast or too slow, and that’s just the start. Let’s tackle these one by one.
Electrode Sticking – Why Does My Welding Rod Keep Sticking
Electrode sticking is the bane of smooth welding operations. It’s when your welding rod decides to become one with the workpiece, refusing to budge. Often, it’s a tale of amperage gone awry. Too low, and your rod is a magnet; too high, and you’re sparking a fireworks show. The fix? Start with the Goldilocks zone of amperage, not too low, not too high, just right as per the rod’s specifications.
Porosity – What Causes Porosity in Stick Welding
Porosity can turn your solid weld into a sponge, with holes that could sink the proverbial ship. The culprit? Contaminants that sneak into the weld pool, whether it’s rust, oil, or even the wrong atmosphere.
Eliminating Porosity in Your Weld
A clean work surface and the right shielding gas can make all the difference. Proper preparation of the work surface is crucial, if you want to avoid porosity. In addition, to produce a smoother and more stable arc the use of Argon-CO2 shielding gas in a 75% t0 25% ration. If stick welding without gas, choice of the correct flux electrode is key.
Spatter – Why Does My Welding Rod Produce Spatter
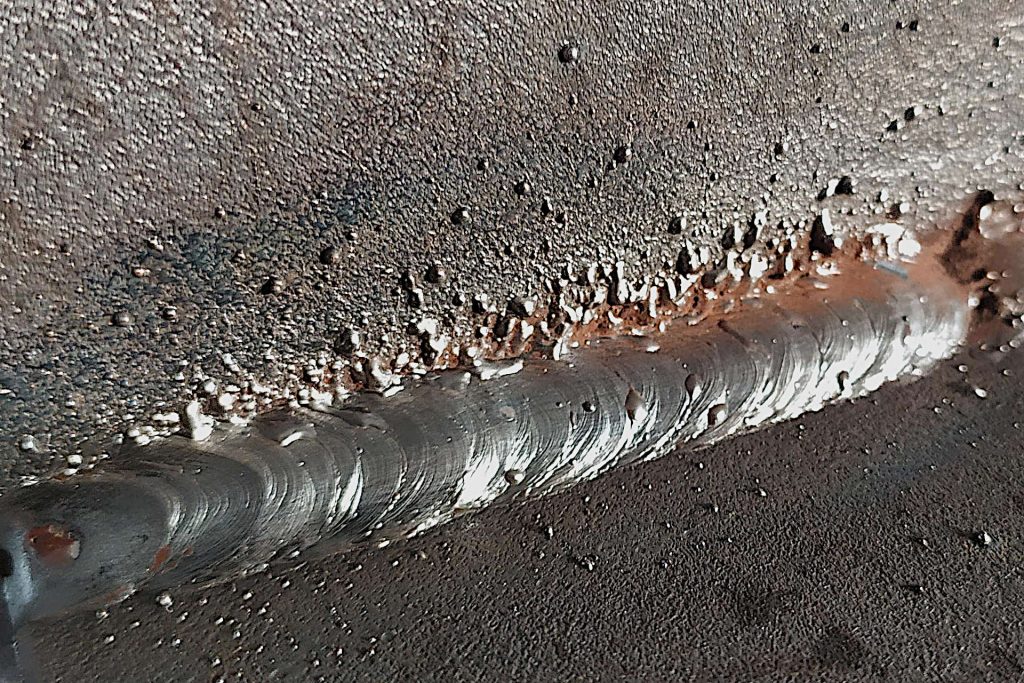
Spatter is like that guest who shows up uninvited and leaves a mess. It’s the metal that scatters when the arc is too lively, often due to an amperage party that’s too intense.
Reducing Spatter: A Clean Weld
To reduce spatter, fine-tune your amperage, and maintain a firm yet gentle arc length. A tidy welder is a proficient welder.
Undercut and Overlap – Unwanted Groove
The undercut is the groove that wasn’t meant to be there, and overlap is the metal that just didn’t fuse as it should have. Both can be attributed to the travel speed of your hand that either lags or races.
Preventing Undercut and Overlap
To prevent undercut and overlap when stick welding you need to work on achieving a steady, consistent speed that’s in sync with the metal’s melting rate.
General Solutions for Stick Welding Problems
Usually most of the problems that you come across while stick welding have straight forward solutions that will iron out these wrinkles in your welding workflow.
Stick Welding Troubleshooting Tips
- Correct Amperage: Reference your electrode’s manual and start at the recommended setting. Adjust as needed, but remember, too much heat is as bad as too little.
- Clean Work Surface: A little grime can cause a lot of grief. Before striking an arc, ensure your metal is as clean as your intentions.
- Steady Arc Length: Keep the arc short but not too short. Think of it as the cozy middle ground where welding magic happens.
- Skill Development: Like any craft, perfection comes with practice. Invest time in honing your hand movements for better control and precision.
Stick Welding Problems and Solutions – The Tools and Techniques
Your electrode and your machine are your best friends in the welding world. Treat them right, and they’ll do the same for you.
Electrode Considerations
The electrode is not just a stick of metal. It’s the key to your weld’s character. Size matters, as does the coating. Match the electrode to the job, keep it dry, and it will serve you well.
Welding Machine Setup
The heart of your operation, the welding machine, needs to be in top form. Set it up as per the book, keep those cables tight, and ensure the current is steady.
FAQs
- What causes porosity in stick welding? Impurities and moisture are the main villains. Keep everything clean and dry.
- Why does my welding rod keep sticking? Low amperage is often the culprit. Consult the electrode’s guidelines for the right setting.
Part One: Identifying and Preventing Stick Welding Issues
Setting the Stage for Success – Preparation and Practice
Before the first spark ignites, the workpiece must be prepared with meticulous care. Success in stick welding is deeply rooted in the preparation of your materials and the calibration of your tools. The adage “well begun is half done” rings true in the welding world.
Preparation of the Work Piece
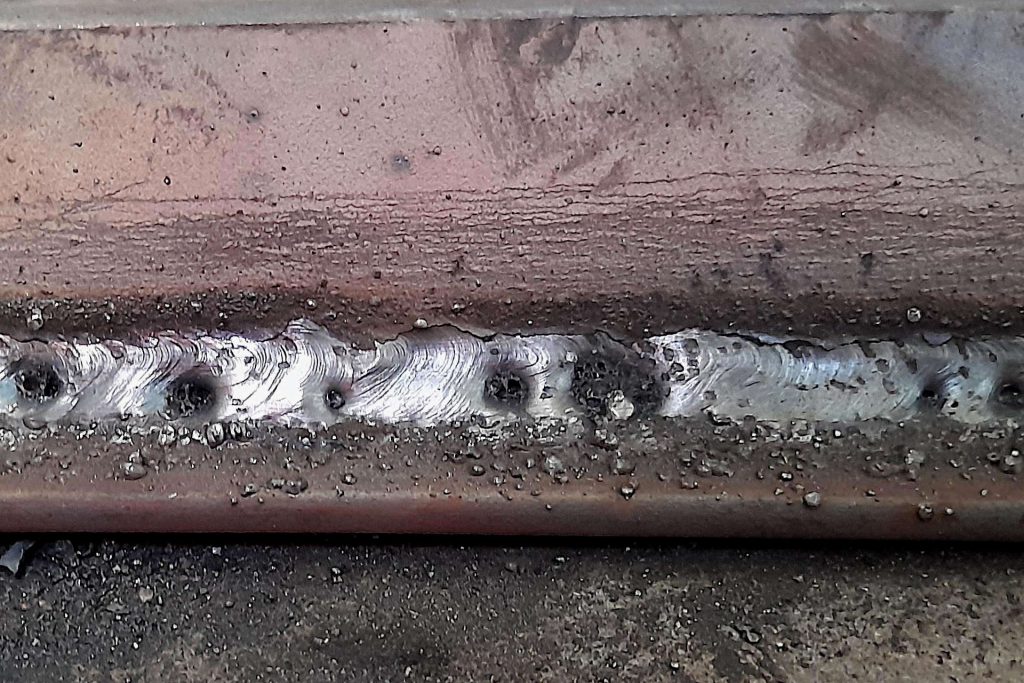
Begin with a workpiece devoid of contaminants. Rust, paint, and debris are more than just cosmetic flaws; they’re barriers to a quality weld. Employ a grinder, a wire brush, or a sandblaster—whatever it takes to achieve a surface as immaculate as your craftsmanship aims to be.
Electrode Selection – Common Electrode Challenges in Stick Welding
There a variety of challenges linked to different electrodes. Each type, like the 7018 or 6010, comes with its unique set of potential issues. Understanding these can greatly enhance your welding results.
The table below primary characteristics and challenges of each electrode type, offering a quick reference to assist in choosing the right electrode for specific welding tasks
Electrode Type | Main Advantage | Key Challenge | Notes |
---|---|---|---|
6010 | High Penetration | Risk of Burn-through; Requires high skill | Less stable arc, demanding precise control |
7018 | Strong, Clean Welds | Moisture Sensitivity | Needs dry storage to prevent hydrogen cracking in welds |
7024 | High Deposition Rates | Limited to Flat/Horizontal Positions | Fluid-like slag makes it unsuitable for vertical/overhead |
6011 | Versatility with AC/DC Current | Erratic Arc; More Slag | Requires additional cleaning post-weld |
6010 Electrodes: High Penetration, High Skill
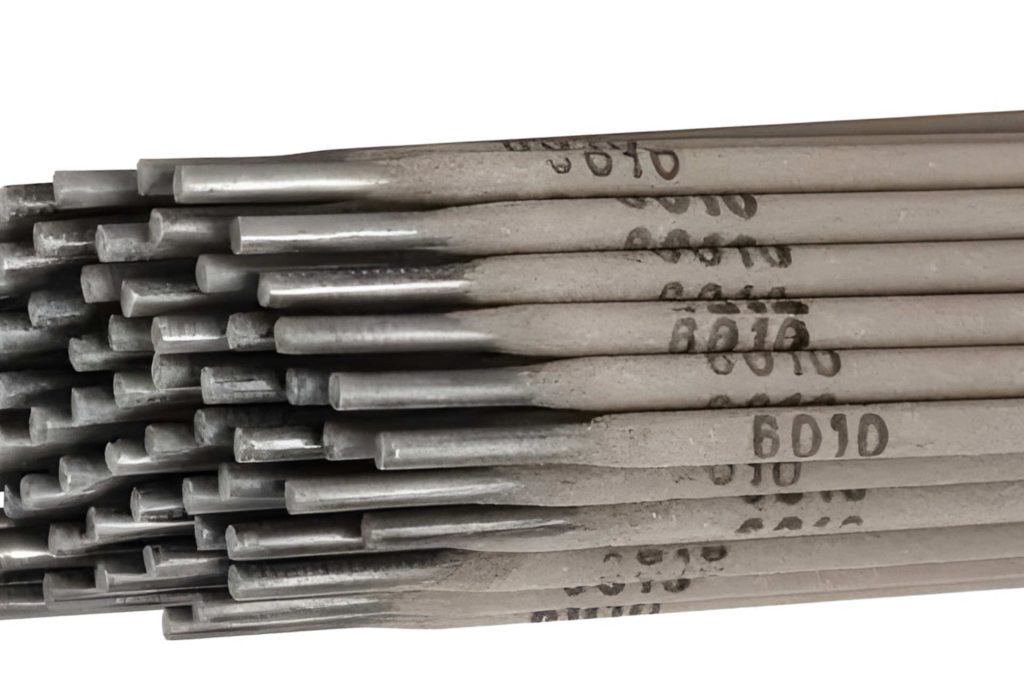
The 6010 electrodes are known for their deep penetration, making them ideal for tough welding jobs. However, this advantage is also a challenge. The deep penetration requires a high level of skill to manage effectively. If you’re not careful, it can lead to excessive burn-through, especially on thinner materials. Moreover, 6010s produce a somewhat less stable arc, which demands steady hands and precise control.
7018 Electrodes: Moisture Sensitivity
The 7018 electrodes are popular for their strong, clean welds and are often used in structural welding. But, they are highly sensitive to moisture. If not stored properly in a rod oven or a dry environment, they can absorb moisture. This absorption leads to hydrogen cracking in your welds, compromising the structural integrity. Always ensure your 7018s are kept dry for optimal performance.
7024 Electrodes: Position Limitations
Known for high deposition rates, 7024 electrodes are great for laying down a lot of material quickly. However, they’re primarily designed for flat or horizontal welding positions. When you’re working in vertical or overhead positions, 7024s may not be your best choice. Their slag can be fluid-like, making it tricky to control in these positions.
6011 Electrodes: Versatility with a Twist
The 6011 electrodes are the versatile cousins of the 6010s. They can be used with AC and DC currents and are less sensitive to dirty or rusty metals. While this versatility is a plus, it doesn’t come without a challenge. The 6011s can produce a more erratic arc and leave behind more slag, requiring extra cleaning post-weld.
Every electrode type in stick welding has its unique strengths and corresponding challenges. By understanding these, you can choose the right electrode for your project and mitigate potential issues.
The size and type of electrode must match the task at hand—too large, and you risk overwhelming the metal; too small, and you may not penetrate deeply enough. Look for those that promise ease of use, such as E6010 for deep penetration or E7018 for smooth and strong welds.
Machine Calibration
Your welding machine is the bedrock of your welding work, dictating the flow and the fusion. Ensure you set your amperage based on the electrode’s specifications and the thickness of the metal. A well-calibrated machine speaks through the consistency and quality of the arc it produces.
Technique Tuning
With everything properly prepared set and calibrated, it’s time for the weld. The skill resides in the interplay of hand, eye, and metal. The electrode angle is pivotal; it dictates the arc’s penetration and the bead’s width. A slight tilt, about 10 to 15 degrees in the direction of travel, is often ideal. But like any dance, it’s the rhythm that truly matters. The travel speed of your hand must be steady and synchronized to the metal’s melting rate, a tempo learned through practice and patience.
The Practice Paradigm
Practice is not merely repetition; it’s an act of refinement. Each bead run, every metal joined, is a step closer to being a better welder. Practice on scrap metal, simulate different welding positions, and challenge yourself with varying material thicknesses. As they say, mastery is not a destination but a journey—one that begins anew with every strike of the arc.
The Art of the Weld – Technique
Stick welding is as much about the feel as it is about the numbers. It is a delicate balance of skill, precision, and technique. The right amperage and speed are foundational, but the true skill comes from the subtle tilt of the rod, the careful arc movement, and the gentle drag across the material. It’s a combination of movements that come together to create the best weld.
The Arc
The arc is not just a source of heat; it’s the paintbrush of the welder. Its effectiveness is defined by the steadiness of the hand that guides it. The arc strike is the first requires a firm yet gentle touch to ignite and a steady hand to maintain. The key lies in maintaining just the right arc length—too short an arc length, and it may stutter and stick; too long an arc length, and it loses its potency and precision.
Smooth Movement
As in any weld every movement of the electrode is intentional. Its angle, the direction of the travel, and the speed at which you move all contribute to the final weld’s quality. The electrode must glide across the metal, not just with purpose but with an a rhythm. It’s a back-and-forth motion, a push-and-pull between the welder and the molten pool that forms the bead.
Reading the Metal
Each metal has its own tempo, a unique rate at which it melts and fuses. The welder must tune in to this tempo, adjusting their speed and motion accordingly. Too fast, and the weld is weak, lacking penetration; too slow, and it risks defects such as burn-through or excessive reinforcement. The right tempo ensures a weld that is as strong internally as it is aesthetically pleasing on the surface.
Neat Weld Beads
After penertration, achieving a symmetric and even bead is should be the aim. It is where the skill of the welder is most apparent. This symmetry is achieved through uniformity in speed and angle, ensuring that each segment of the bead seamlessly blends with the next. The welder’s motion must be smooth and continuous, ensuring even heat distribution and consistency in the weld’s appearance.
Part Two: Stick Welding – Advanced Troubleshooting
Beyond the Basics
Now that we’ve covered the groundwork, it’s time to tackle the stick welding conundrums that test even seasoned welders.
Dialing in the Perfect Amperage
It’s a game of precision. The amperage sweet spot is where your rod’s potential is fully realized. Begin with the manufacturer’s recommendation and adjust incrementally. The signs of a well-adjusted amperage are a steady arc and a clean, controlled pool of molten metal.
The Finer Points of Electrode Angles
Angles are not just for geometry enthusiasts. The right electrode angle affects penetration, bead shape, and overall weld strength. Tilt your electrode at about 10-15 degrees in the direction of travel to promote a smooth flow of metal.
Travel Speed and Motion
Consistency is key in the rhythm of stick welding. The travel speed should be steady, allowing the metal to properly fuse without rushing or dawdling. Develop a feel for the right speed through practice on scrap metal.
Tackling Difficult Weld Positions
Welding is not always a flat affair. Vertical and overhead welds throw gravity into the mix, demanding even more skill.
Vertical Welding: Stick Welding Uphill
For uphill welding, a zigzag or weave pattern can help manage the weld pool and ensure good penetration. Keep the electrode angle more perpendicular and use a side-to-side motion to distribute the weld metal evenly.
Overhead Welding
When welding overhead, less is more. Lower amperage and quick, consistent movements prevent the molten metal from becoming disobedient droplets.
Final Thoughts: Stick Welding Problems and Solutions
As a seasoned stick welder with two decades of hands-on experience, I’ve faced a variety of challenges when stick welding and we have looked at and discussed some of the main issues that arise and the solutions. I have also laid out several advanced techniques you can use and hopefully underscored the importance of preparation and practice,
Stick welding, with its challenges and nuances, is a craft worth mastering. It’s a journey of continuous learning and improvement, where each weld is a testament to the welder’s skill.
Remember, the most effective way to avoid problems and become an expert stick welder is through, practice, persistence and precision. Experience will count for a lot as you progress. Keep the arc alive and the passion kindled.
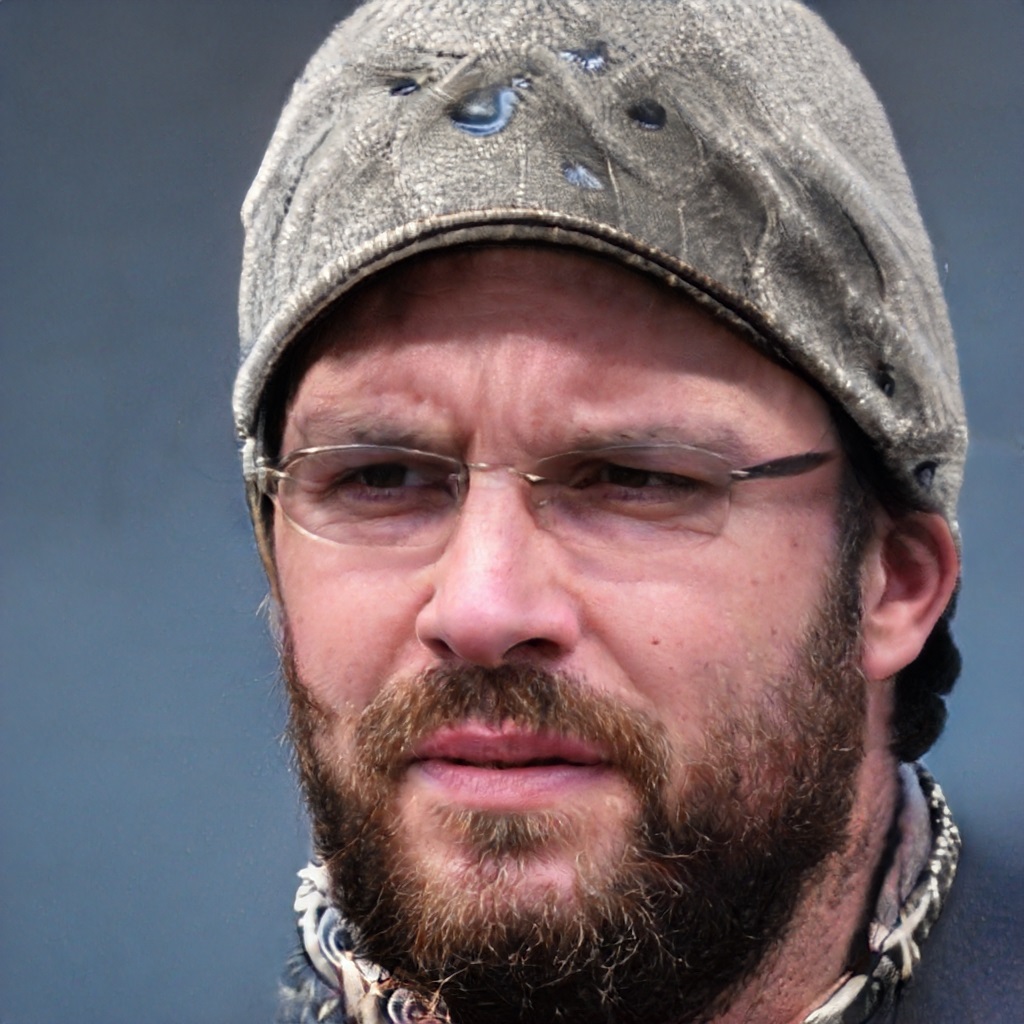
I’ve been involved in the welding industry for over twenty years. I trained in various engineering shops working on various projects from small fabrication and repairs through to industrial projects.I specialize in welding aluminum and food grade stainless steel and an now run an engineering shop fabricating equipment for the food industry.