Low Hydrogen Open Root Welding: A Comprehensive Guide
americanindustrialsupl and its partners may earn a commission if you purchase a product through one of our links.
What is Low Hydrogen Open Root Welding?
Low hydrogen open root welding is a technique that combines the use of low hydrogen electrodes with an open root joint configuration. This approach is crucial in preventing hydrogen embrittlement, a metal failure caused by trapped hydrogen leading to brittleness and fractures. Low hydrogen electrodes are designed to minimize porosity and cracking by controlling hydrogen content in the weld and using special coatings to reduce hydrogen penetration. The technique requires a dry, controlled environment for the weld’s quality and durability.
An open root weld joint is characterized by a gap between the base metals, allowing for better penetration and a stronger bond. This joint type is common in processes requiring full penetration welds like structural steel fabrication and pipeline construction, ensuring the weld’s integrity and strength.
Applications of Low Hydrogen Open Root Welding
Low hydrogen open root welding is widely utilized across various industries due to its strong, durable welds and compatibility with different types of steel. Notable applications include:
- Construction and Infrastructure: Essential for constructing buildings, bridges, and other structures where weld integrity is critical.
- Shipbuilding and Marine Engineering: Used in the fabrication of ships and offshore platforms, where the strength and durability of welds are paramount.
- Oil and Gas Industry: Crucial for pipelines, refineries, and processing plants, where welds must withstand harsh environments and high pressures.
- Power Generation: Employed in nuclear, thermal, and renewable energy plants, where reliable welds ensure the safety and efficiency of power production.
This welding technique is compatible with carbon steels, low alloy steels, stainless steels, and some nickel alloys, making it versatile for various industrial applications.
Advantages of Low Hydrogen Open Root Welding
The adoption of low hydrogen open root welding offers several benefits over other welding methods:
- Improved Weld Strength and Toughness: The use of low hydrogen electrodes significantly enhances the strength and toughness of welds, reducing the risk of metal failure.
- Reduced Risk of Hydrogen Cracking: This method minimizes the potential for hydrogen-induced cracking, a common issue in welding, by limiting the amount of hydrogen in the weld area.
The advantages of LHORW underscore the importance of low hydrogen open root welding in ensuring the structural integrity and longevity of welded joints across diverse applications.
Preparation for Low Hydrogen Open Root Welding
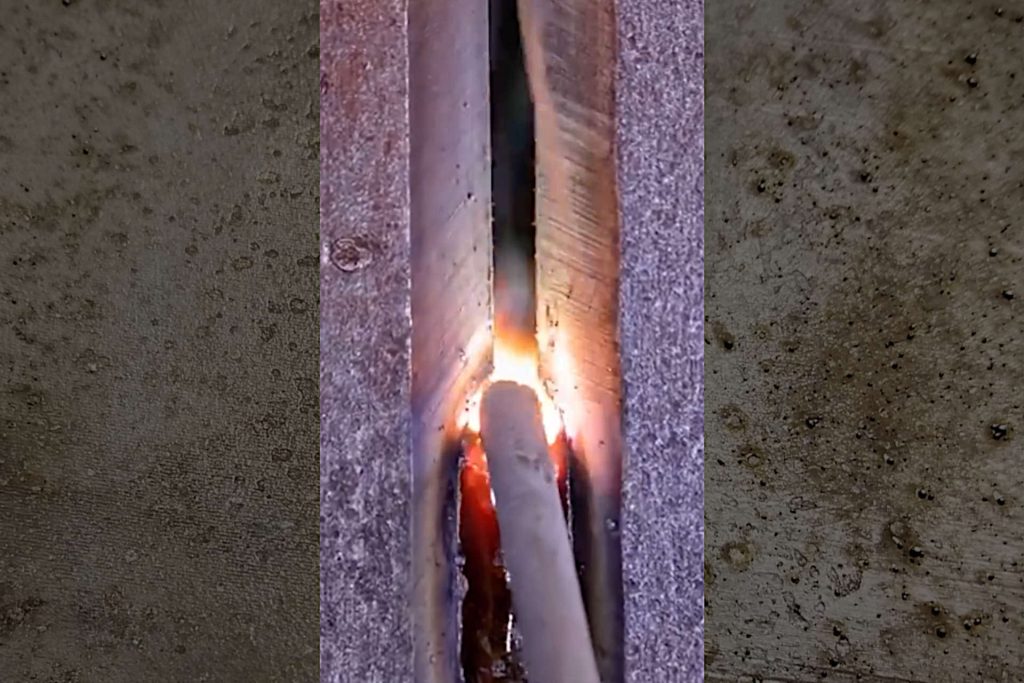
Material Selection: Base Metal Types
Carbon Steels
- Compatibility: Carbon steels are highly compatible with low hydrogen electrodes. These metals, ranging from mild to high carbon content, are foundational in various structural and engineering applications due to their strength and versatility.
- Considerations: The key is managing carbon content; higher carbon steels may require preheating to avoid cracking due to the rapid cooling that can increase hardness and brittleness.
Low Alloy Steels
- Compatibility: Low alloy steels, which have small amounts of alloying elements added to improve their mechanical properties, are also well-suited for low hydrogen welding. These steels can achieve enhanced toughness, strength, and resistance to wear and atmospheric corrosion.
- Considerations: Similar to carbon steels, attention to preheat and interpass temperatures is crucial, especially for thicker sections or steels with higher alloy content, to mitigate the risk of hydrogen-induced cracking.
Stainless Steels
- Compatibility: Stainless steels, known for their corrosion resistance, can be welded with low hydrogen electrodes, particularly those designed for this group of steels. The choice of electrode depends on the stainless steel grade (austenitic, ferritic, martensitic, duplex).
- Considerations: Preheating is generally not required for austenitic stainless steels, but ferritic and martensitic grades may benefit from it. Control of heat input and post-weld cooling rates is critical to prevent warping and cracking.
Some Nickel Alloys
- Compatibility: Nickel alloys are used in environments that demand high strength and resistance to heat, corrosion, and oxidation. Low hydrogen electrodes suitable for nickel alloys are available and used in critical applications such as the chemical processing industry and high-temperature environments.
- Considerations: Nickel alloys’ high thermal expansion coefficient and thermal conductivity require careful control of welding parameters to prevent distortion and cracking. Preheating and post-weld stress relief can be necessary for some nickel alloys to ensure the integrity of the weld.
General Considerations
When welding with low hydrogen electrodes, understanding the base metal’s properties is essential. Factors such as the metal’s susceptibility to cracking, required mechanical properties of the weld, and the operating environment must guide the selection of both the base metal and the electrode. Additionally, welding procedures including preheat and post-weld heat treatment (PWHT) requirements, welding speed, and amperage settings should be tailored to the specific characteristics of the base metal to optimize weld quality and performance.
Properly matching low hydrogen electrodes to the base metal not only ensures a high-quality weld but also maximizes the welded joint’s performance in its intended application. Each base metal type brings its own set of challenges and requirements to the welding process, underscoring the importance of a well-considered approach to material selection.
Joint Design Considerations for Open Root
The design of the joint is critical in open root welding. It must facilitate complete penetration and fusion of the base metals. Two key aspects of this are bevel angles and root gaps.
- Bevel Angles: The bevel angle, the angle formed between the prepared edges of the base metals, is crucial for directing the welding arc into the joint’s root, ensuring deep penetration and strong fusion. The choice of angle is influenced by several factors:
- Material Thickness: Thicker materials often require larger bevel angles to allow the welding arc to reach the root of the joint effectively. Conversely, thinner materials may need smaller angles to prevent burn-through.
- Welding Process: The welding process being used can also dictate the bevel angle. Processes that concentrate heat more narrowly, such as TIG welding, might allow for steeper angles compared to those with a broader heat-affected zone, like stick welding.
- Joint Access: Accessibility for welding on both sides of the joint can allow for steeper angles, as each side can be adequately penetrated. Single-sided welding might require shallower angles to ensure complete penetration from one side.
- Root Gap: This is the space between the base metals at the root of the joint. It’s a critical feature that allows the welding arc and filler material to penetrate and fuse the base metals fully. Several considerations affect the optimal root gap:
- Electrode Diameter: The diameter of the electrode often dictates the minimum root gap, as sufficient space is needed for the electrode to access the root without interference.
- Welding Current: Higher welding currents can allow for a larger root gap, as the increased heat can ensure penetration across the gap. Lower currents might require a narrower gap to maintain adequate heat concentration.
- Material Type: Different materials conduct and retain heat differently, affecting how the weld pool behaves and thus how wide the root gap should be. For example, aluminum, with its high thermal conductivity, might require adjustments to the root gap compared to steel.
Having a comprehensive grasp and applying these considerations in joint design are paramount for achieving a successful low hydrogen open root weld. Proper bevel angles and root gaps ensure that the weld penetrates deeply enough to create a strong, durable joint while minimizing defects such as lack of fusion or excessive penetration.
Equipment Selection
Welding Machine
- Type and Power Source: The choice between AC (Alternating Current) and DC (Direct Current) welding machines is pivotal. While AC machines are versatile and cost-effective, DC machines are typically preferred for low hydrogen open root welding due to their stable arc, which is crucial for maintaining control over the welding process. The machine’s power source should be compatible with the electrode’s requirements and the thickness of the base metal.
- Current Range and Adjustability: The machine’s current range is essential for accommodating various electrode diameters and material thicknesses. An adjustable current setting allows for fine-tuning the welding parameters to achieve the desired penetration and bead profile, which are critical for the integrity of open root welds.
- Duty Cycle: The duty cycle of a welding machine indicates how long it can operate at a given output without overheating. For intensive welding projects, a machine with a high duty cycle is recommended to ensure continuous operation without frequent breaks for cooling down.
Consumables
- Low Hydrogen Electrodes: The cornerstone of equipment selection, the choice of low hydrogen electrodes (such as E7018, E7016, E8018, etc.), should be based on the base metal’s composition and the specific requirements of the weld. Electrode diameter and coating type affect arc stability, penetration depth, and slag detachability.
- Selection Based on Material: The electrode must be suitable for the particular type of steel or alloy being welded. Certain electrodes are formulated for specific materials, offering enhanced performance, such as improved crack resistance or better mechanical properties in the weld deposit.
- Storage Conditions: Low hydrogen electrodes are susceptible to moisture absorption, which can introduce hydrogen into the weld and increase the risk of cracking. Proper storage solutions, such as rod ovens or vacuum-sealed containers, are essential to maintain the electrodes’ low hydrogen characteristics.
Personal Protective Equipment (PPE)
- Welding Helmets with Auto-Darkening Lenses: These helmets protect against harmful UV and IR radiation and bright welding arcs. Auto-darkening lenses adjust the shade in real-time, allowing for clear vision before the arc starts and adequate protection during welding.
- Flame-Resistant Clothing: Welders should wear flame-resistant overalls or jackets to protect against sparks and molten metal. Materials like leather or specially treated fabrics offer effective protection.
- Gloves and Boots: High-quality welding gloves provide dexterity and heat resistance, essential for handling hot materials and operating the welding machine. Safety boots, preferably made from leather and with steel toes, protect against falling objects and sparks.
- Respiratory Protection: When welding in environments with insufficient ventilation, wearing a welding respirator can help protect against inhaling harmful fumes and gases produced during the welding process.
Joint Preparation
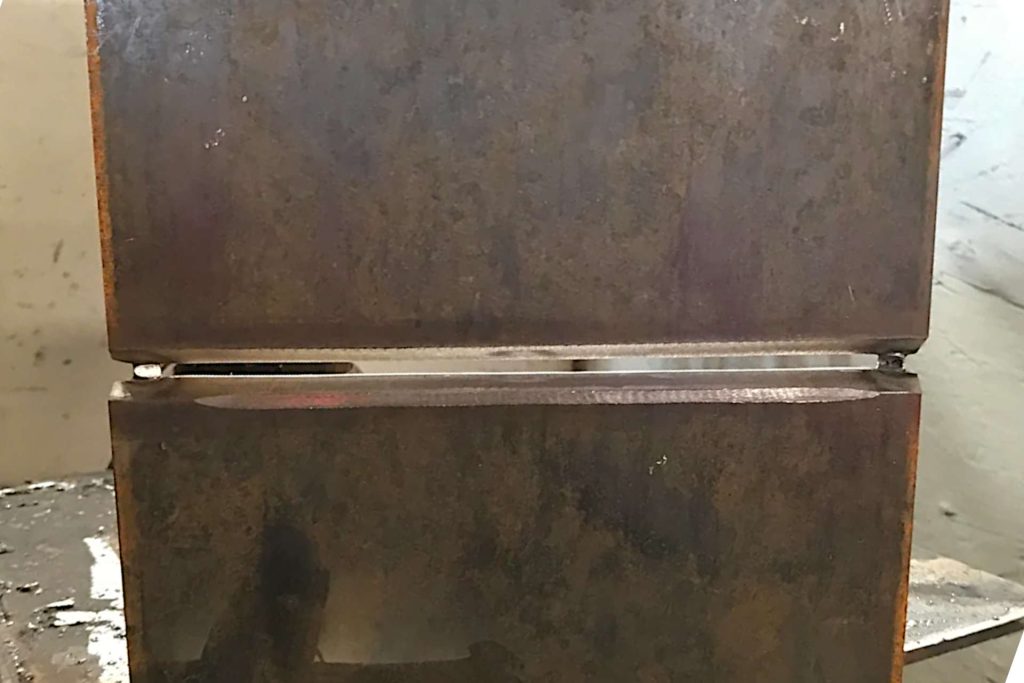
Joint preparation consideration is essential in ensuring clean, properly aligned, and well-prepared joints. This phase is critical, as the quality of the finished weld significantly depends on the initial joint preparation.
Cleaning Procedures
- Surface Cleanliness: The importance of starting with clean joint surfaces cannot be overstated. All contaminants, including rust, paint, oil, and grease, must be thoroughly removed. These contaminants can introduce impurities into the weld, leading to defects such as porosity or lack of fusion.
- Methods: Mechanical cleaning methods, such as grinding, wire brushing, or sandblasting, are effective for removing rust and scale. Chemical cleaners can be used to degrease surfaces. It’s essential that the selected cleaning method does not introduce new contaminants.
Tack Welding Techniques for Open Root
- Purpose: Tack welds serve as temporary fixes that hold the joint in alignment during the welding process. Properly placed tack welds ensure the gap remains consistent and prevents the base metals from moving due to thermal expansion.
- Placement and Size: Tack welds should be strategically placed to maintain the joint’s alignment and spacing without interfering with the final weld. The size of the tack welds should be sufficient to hold the pieces together but minimal enough to avoid excessive heat input and distortion.
- Number and Distribution: The number and distribution of tack welds depend on the joint’s length and configuration. For longer joints, more tack welds may be needed to maintain stability. They should be evenly distributed to prevent uneven heating and distortion.
Fit-Up and Alignment
- Root Gap Consistency: Achieving a consistent root gap across the entire joint is crucial for uniform weld penetration. Use spacers or gauges as necessary to ensure the gap meets the specifications outlined in the welding procedure.
- Bevel Angle Accuracy: The bevel angle must be consistent along the joint to facilitate proper weld penetration and fusion. Any deviations can affect the weld’s quality and strength.
- Checking Alignment: Before beginning the welding process, a final check of the joint alignment and fit-up should be conducted. Misalignment can lead to various weld defects, including lack of fusion and excessive stress concentrations.
Considerations for Different Base Metals
- Material Specifics: Different base metals may require unique preparation steps. For example, stainless steels might need particular attention to avoid contamination, while high-carbon steels may require preheating to reduce the risk of cracking.
- Heat-Affected Zone (HAZ) Management: In some cases, the preparation process must consider the potential effects of welding on the base metal, such as hardening or softening in the HAZ. Preheat and post-weld heat treatment (PWHT) procedures can mitigate these effects.
Having proper preparation steps significantly improve the likelihood of producing high-quality, defect-free low hydrogen open root welds. Proper joint preparation not only affects the weld itself but also the overall structural integrity of the welded assembly.
Low Hydrogen Open Root Welding Technique
The4re are the specific techniques involved when employing low hydrogen open root welding, Below we will covers welding parameters, nuances in technique, and interpass cleaning to ensure high-quality welds and structural integrity.
Welding Positions
Mastering various welding positions is essential for welders, especially when working with low hydrogen open root welding techniques.
1G (Flat Position):
The 1G position is where the welding is performed on the upper side of a horizontal joint. It’s the simplest position, offering the greatest stability for the weld pool, which is particularly beneficial when using low hydrogen electrodes to minimize the risk of defects such as porosity or slag inclusions.
Tip: For low hydrogen electrodes, preheating the base material can be beneficial to reduce moisture and minimize the risk of hydrogen-induced cracking.
2G (Horizontal Position):
In the 2G position, the weld is made on a vertical plane, with the axis of the weld lying horizontally. This position requires more skill than 1G, as gravity affects the weld pool differently, challenging the welder to maintain control over the weld bead shape and penetration.
Tip: Incremental pauses on the sides of the weave pattern allow the weld pool to solidify sufficiently, preventing sagging.
3G (Vertical Position):
Welding in the 3G position involves a vertical joint orientation. The welder works upward or downward along the vertical joint. This position is challenging due to the effect of gravity on the weld pool, necessitating precise control of the welding parameters and technique to ensure consistent penetration and avoid excessive runoff.
Tip: Managing heat input is crucial; too much heat can cause the weld pool to become unmanageable, whereas too little can lead to lack of fusion.
4G (Overhead Position):
The 4G position is where the welding is performed from underneath a horizontal joint. It’s the most challenging position because of the need to control a weld pool that gravity pulls away from the joint. Achieving proficiency in this position with low hydrogen electrodes is essential for scenarios where overhead welding cannot be avoided.
Tip: Welding in short segments and allowing cooling periods in between can help maintain a manageable weld pool size and reduce heat buildup, which is particularly important to prevent hydrogen-induced issues.
For low hydrogen open root welding, it’s especially important to manage heat input carefully and maintain a clean joint to prevent hydrogen-induced cracking. Making adjustments to the welding parameters to accommodate the effects of gravity on the weld pool and to ensure adequate penetration and fusion is essential.
Welding Parameters
- Current Settings: The choice of welding current is pivotal and should be finely tuned based on the electrode’s diameter and the material’s thickness. For low hydrogen electrodes, correct current selection facilitates the arc’s stability and penetration depth, essential for robust welds. It’s a balancing act; too high a current may lead to overheating and potential weld defects, while too low a current might not penetrate sufficiently. Typically, electrodes come with manufacturers’ recommendations that specify optimal current ranges, serving as a valuable starting point for adjustments based on specific welding conditions.
- Travel Speed: The rate at which the welder moves the electrode along the joint impacts the weld bead’s appearance, penetration, and potential for defects. A speed that’s too fast can lead to insufficient penetration and a narrow, underfilled weld bead. Conversely, a slow travel speed might cause excessive penetration and potential burn-through, especially in thinner materials. The goal is a consistent speed that allows for the formation of a smooth, evenly distributed weld bead, reflecting a balance between the amount of heat introduced and the rate of travel.
- Arc Length: The distance between the electrode tip and the workpiece significantly influences the welding process. Maintaining a short arc length is generally advised, as it enhances arc stability, increases penetration, and reduces spatter. A longer arc might be momentarily useful in certain situations to increase visibility or reach difficult areas, but it typically leads to less control over the weld pool and a higher risk of introducing contaminants into the weld. An arc length approximately equal to the diameter of the electrode core is a good rule of thumb for maintaining control and ensuring quality.
Adhering to these refined welding parameters not only ensures the structural integrity of the weld but also minimizes the likelihood of defects, paving the way for successful low hydrogen open root welding projects. Mastery of these parameters is crucial for welders seeking to optimize their technique in line with best practices.
Welding Technique
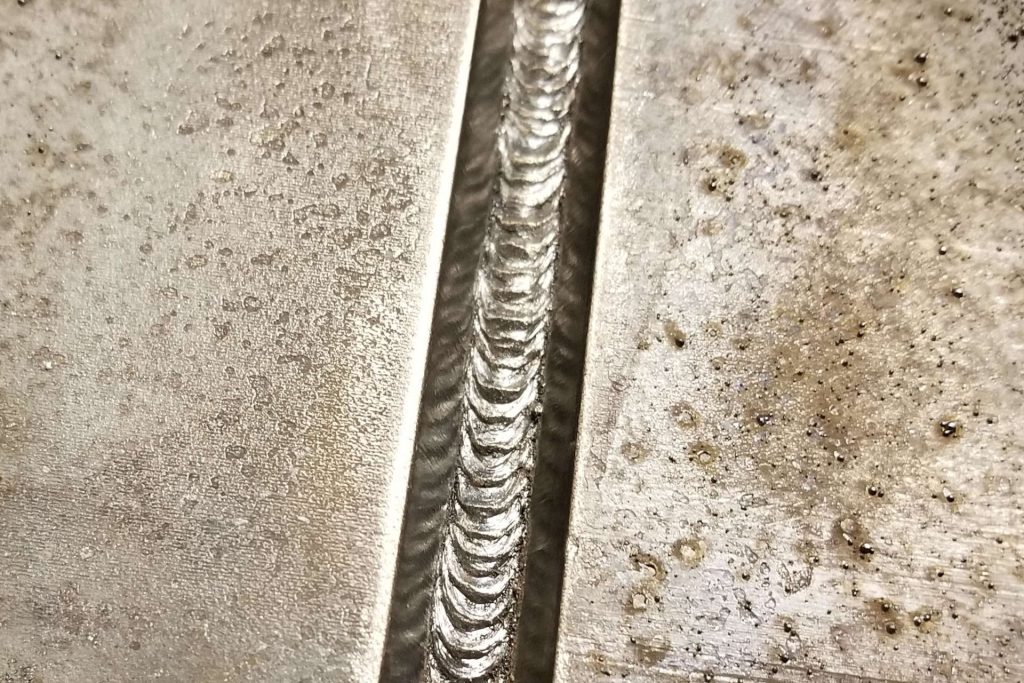
- Travel Angle: The correct travel angle, ranging between 10 to 20 degrees in the direction of welding, is key. This angle helps in directing the weld pool and arc force effectively into the root of the joint, ensuring deep penetration and a solid bond. Maintaining this angle allows for optimal heat input and distribution, crucial for achieving a defect-free weld.1
- Weave Techniques: The application of weave techniques in low hydrogen open root welding can significantly influence the outcome of the weld. These techniques, which involve moving the electrode in a controlled pattern (such as side-to-side or in a circular motion), are employed to manage the weld pool, control heat input, and ensure uniform penetration across the weld joint. The choice of weaving pattern is determined by several factors, including joint design, welding position, and the desired final weld appearance. Weaving allows for better coverage of the joint, aiding in the elimination of potential voids or lack of fusion areas.
- Rod Manipulation: Effective rod manipulation techniques are vital for ensuring thorough penetration and a high-quality weld pool. Techniques vary from slight oscillations to a more pronounced whip and pause method, depending on the welder’s preference and the specific requirements of the joint. The goal is to achieve a consistent, controlled weld pool that adequately fills the joint without overheating or causing weld defects. Skillful manipulation of the electrode also helps in avoiding common issues such as slag inclusion and porosity, ensuring a clean and strong weld.
Mastering these welding techniques is crucial for welders aiming to excel in low hydrogen open root welding. The proper execution of travel angle, weave patterns, and rod manipulation directly impacts the quality and integrity of the weld, highlighting the importance of precision and skill in this specialized welding process.
Interpass Cleaning
Interpass cleaning in low hydrogen open root welding is a critical step that directly influences the quality and integrity of the weld. This procedure involves removing slag, spatter, and any other contaminants from the weld surface between passes, ensuring a clean area for subsequent welding
- Significance: The primary goal of interpass cleaning is to ensure that the weld surface is free from contaminants that could lead to defects such as porosity, slag inclusions, or weak fusion. Each layer of the weld must bond cleanly with the next, and any barrier to this bond can compromise the weld’s overall integrity. Effective interpass cleaning also contributes to better arc stability and weld pool control in subsequent passes.
- Methods:
- Slag Removal: After each pass, especially when using covered electrodes that produce slag, it’s imperative to remove all slag from the weld surface. Tools such as chipping hammers and wire brushes are commonly used for this purpose. Slag must be chipped away carefully to avoid damaging the underlying weld.
- Surface Cleaning: Beyond slag, other surface contaminants such as oxides or residual dirt must be removed. Abrasive grinding or a clean wire brush can be effective for this task. It’s important that the tools used for cleaning between passes are clean and free from contaminants themselves to avoid reintroducing impurities into the weld area.
- Visual Inspection: After cleaning, a thorough visual inspection is recommended to confirm the removal of all contaminants. This step is crucial for identifying any potential defects early in the welding process, allowing for corrective action before the weld progresses further.
- Considerations for Different Materials: The approach to interpass cleaning may vary based on the base metal’s sensitivity to contamination. For example, stainless steels and nickel alloys might require more stringent cleaning to prevent alloy contamination and ensure the desired corrosion resistance in the final weld.
Spending time on interpass cleaning practices between each pass ensures the creation of high-quality, defect-free welds in low hydrogen open root welding applications. This aspect of the welding process, though sometimes considered merely preparatory, holds significant importance in achieving the desired weld performance and longevity.
Challenges and Troubleshooting with Low Hydrogen Open Root Welding
When using hydrogen open root welding, welders can encounter several challenges that, if not properly addressed, can lead to defects compromising the weld’s integrity and performance.
Common Defects
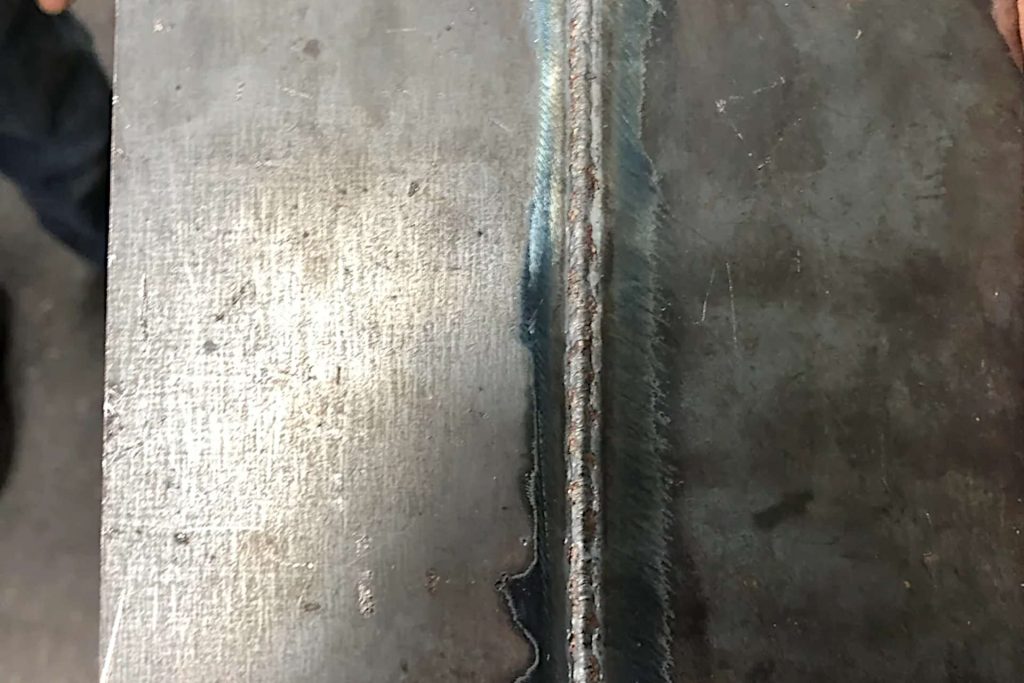
Lack of Fusion:
- A situation where the weld metal fails to adequately fuse with the base metal or preceding weld layers. This defect often arises from insufficient heat input, incorrect travel speed, or improper angle of the welding electrode.
- Prevention: Ensure adequate heat input by selecting the appropriate current and maintaining an optimal travel speed that allows the weld pool to sufficiently heat the base metal. The electrode angle should also be adjusted according to the joint configuration to promote thorough fusion.
- Correction: Identify areas of lack of fusion through visual inspection or non-destructive testing methods. Removal of the defective section followed by careful preparation and rewelding, adhering to the corrected parameters, is necessary.
Porosity
Porosity is a defect is characterized by trapped gas bubbles in the solidified weld metal, leading to cavities or pores. Common causes include contamination of the weld area, moisture in the electrode, or improper gas shielding in gas-shielded welding processes.
- Prevention: Clean the weld area thoroughly before welding to remove any contaminants. Ensure electrodes are stored in a dry environment and that gas-shielded processes have adequate and consistent gas flow to protect the weld pool from atmospheric gases.
- Correction: Porous welds often require removal of the affected area. After ensuring the cause of porosity has been addressed (e.g., by improving cleaning procedures or adjusting shielding gas flow), the section can be rewelded.
Hydrogen Cracking
Hydrogen Cracking, also known as cold cracking, this defect occurs when hydrogen dissolved in the weld metal does not escape before the metal solidifies, leading to cracks. It is more likely to occur in high-strength steels and can be influenced by factors such as residual stress and the hardness of the weld zone.
- Prevention: Use low hydrogen electrodes and ensure they are properly dried before use. Preheat the base metal as necessary to slow the cooling rate, allowing hydrogen to escape. Avoid excessive heat input that could introduce additional stresses.
- Correction: Cracks must be completely removed by grinding or gouging, followed by stress-relieving the area if necessary before rewelding. Implementing preheat or adjusting the welding technique to minimize residual stresses can help prevent recurrence.
Addressing these common defects involves a combination of preventative measures, proper technique, and, when defects do occur, corrective actions that target the root cause. Through diligent practice, adherence to established welding procedures, and responsive troubleshooting, welders can significantly improve the quality and reliability of their low hydrogen open root welds.
Inspection and Testing
After completing a low hydrogen open root welding project, a comprehensive inspection and testing phase is crucial to ensure the integrity and quality of the weld.
Visual Inspection Techniques
- Surface Examination for Defects:
- Objective: The primary goal of visual inspection is to identify any visible defects on the weld surface that could compromise the weld’s structural integrity. These defects might include cracks, porosity, undercutting, lack of fusion, or slag inclusions.
- Process: A systematic approach to visual inspection involves examining the entire weld length under adequate lighting. This allows the inspector to detect surface irregularities, color changes, or any discontinuities that suggest the presence of defects.
- Tools and Aids: While much of the visual inspection relies on the inspector’s trained eye, tools such as magnifying glasses or fillet weld gauges can enhance the accuracy of the inspection. These aids are particularly useful for identifying smaller defects and for verifying compliance with weld size requirements.
- Documentation: Recording findings during the visual inspection is important for quality control and future reference. Any detected defects should be clearly marked and described in inspection reports. This documentation aids in decision-making regarding the need for further non-destructive testing (NDT) or corrective actions.
- Qualified Personnel: Conducting effective visual inspections requires personnel with adequate training and experience. Inspectors should be familiar with the welding process, the types of defects that can occur, and the standards and specifications applicable to the weldment.
Visual inspection serves as the first line of defense in quality assurance, offering a non-invasive means to assess weld quality promptly. By identifying potential defects early, corrective measures can be implemented before proceeding to more specialized testing techniques, saving time and resources.
Non-Destructive Testing (NDT) Methods
Continuing with the inspection and testing phase, we transition from visual inspection techniques to more detailed assessments through non-destructive testing (NDT) methods. These advanced techniques allow for a deeper evaluation of the weld’s integrity without altering the physical state of the workpiece.
What is Non-Destructive Testing
Non-Destructive Testing provides invaluable insights into the internal and surface integrity of welds, detecting defects that aren’t visible to the naked eye. Two widely used NDT methods in assessing low hydrogen open root welds are Radiographic Testing (RT) and Ultrasonic Testing (UT).
Radiographic Testing (RT):
- Principle: RT uses X-rays or gamma rays to penetrate the welded material, capturing an image on a radiographic film or digital sensor. Differences in material density or thickness, due to defects such as cracks, porosity, or slag inclusions, alter the radiation’s transmission, creating a detailed image of the weld’s internal structure.
- Application: RT is particularly suited for detecting volumetric defects and verifying the completeness of the weld penetration. It’s applicable to a wide range of materials and thicknesses, making it a versatile tool in weld inspection.
- Considerations: Safety precautions are paramount due to the use of ionizing radiation. Only trained and certified personnel should perform RT, and the area must be appropriately shielded and marked to protect against radiation exposure.
Advantages: RT provides a permanent visual record of the weld quality that can be reviewed by multiple inspectors, offering a broad assessment of the internal structure. It’s particularly effective for identifying porosity, slag inclusions, and cracks within the weld and adjacent base metal.
Limitations: RT’s main limitations include the safety concerns associated with ionizing radiation, the inability to precisely size planar defects (like cracks) perpendicular to the radiation beam, and the cost and time associated with setting up and executing the test. Additionally, accessibility from both sides of the weldment is required for effective testing.
Technical Considerations: Achieving accurate results with RT depends on the correct selection of radiation sources (X-ray vs. gamma-ray), appropriate exposure times, and the use of suitable imaging techniques (film or digital). Factors such as the thickness of the material and the type of defects targeted influence these choices.
Ultrasonic Testing (UT):
- Principle: UT employs high-frequency sound waves that are transmitted into the weld. When these sound waves encounter boundaries between different materials (such as air in a crack or a void in the metal), they reflect back to the transducer. The time it takes for the echoes to return is measured to determine the location and size of the defect.
- Application: UT is effective for detecting both surface and subsurface defects, including cracks, voids, and inclusions. It’s highly sensitive and can be used for thickness measurements and detecting flaws deep within the weld.
- Considerations: UT requires a skilled operator to interpret the results accurately. The surface condition and weld geometry can affect the test’s effectiveness. Proper calibration and a clear understanding of the sound path are necessary for reliable inspections.
Advantages: UT excels in detecting both surface and subsurface defects, including those not visible on radiographs. It allows for immediate results and precise defect sizing, especially for linear flaws. UT is also safe, as it doesn’t involve harmful radiation, and is less disruptive to the surrounding environment.
Limitations: The technique’s effectiveness is highly operator-dependent, requiring significant skill and experience to interpret the signals accurately. Surface conditions, weld geometry, and the orientation of defects can complicate the testing process. UT is also challenged by coarse-grained materials, which can scatter the ultrasonic waves and obscure defect signals.
Technical Considerations: Proper transducer selection (frequency and type) and the use of appropriate couplants (to facilitate sound transmission) are critical. Calibration blocks of known thickness and defect sizes are used to adjust the equipment settings before testing on actual welds. Advanced UT techniques, such as Phased Array UT (PAUT) and Time-of-Flight Diffraction (TOFD), offer enhanced imaging and defect characterization capabilities.
Both RT and UT are indispensable in the quality assurance process for low hydrogen open root welding, providing deep insights into the weld’s integrity. Their strategic application, informed by a thorough understanding of their advantages and limitations, ensures the reliability and safety of welded structures across industries.
Safety Concerns When Using Low Hydrogen Welding Electrodes
Ensuring safety during low hydrogen open root welding is paramount, not only to protect the welders but also to maintain a secure working environment. Low hydrogen electrodes, while essential for reducing the risk of hydrogen-induced cracking, come with specific safety concerns that must be addressed.
- Handling and Storage: Low hydrogen electrodes are sensitive to moisture absorption, which can compromise their low hydrogen characteristics and lead to increased risk of hydrogen cracking in the weld.
- Guidelines: Store electrodes in their original packaging until ready for use. Use electrode ovens or sealed containers to keep them dry. Follow manufacturer recommendations for storage temperature and humidity levels to prevent moisture absorption.
- Electrode Drying: Improperly dried electrodes can introduce hydrogen into the weld pool, negating the benefits of using low hydrogen electrodes.
- Guidelines: Dry electrodes according to the manufacturer’s specifications before use. This often involves using a drying oven set to a specific temperature for a defined period. Regularly check the oven’s temperature accuracy to ensure effective drying.
- Ventilation: Welding, in general, generates fumes and gases that can be hazardous to health if inhaled. Low hydrogen welding is no exception and requires adequate ventilation to remove these fumes from the welder’s breathing zone.
- Guidelines: Ensure that welding areas are well-ventilated, either through natural ventilation in outdoor settings or mechanical ventilation systems for indoor welding. Consider the use of respiratory protection equipment when ventilation is insufficient to reduce fume exposure to safe levels.
- Electric Shock: Welding equipment operates at voltages that pose a risk of electric shock, a concern that applies to all welding processes, including those using low hydrogen electrodes.
- Guidelines: Wear dry, insulating gloves. Ensure all equipment, including welding machines, cables, and electrode holders, is properly insulated and in good condition. Do not touch the electrode or metal parts of the electrode holder with skin or wet clothing.
- Arc Radiation: The welding arc emits intense ultraviolet (UV) and infrared (IR) radiation that can cause burns to skin and eyes, known as “arc flash.”
- Guidelines: Use appropriate personal protective equipment (PPE), including welding helmets with suitable filter shades, protective clothing covering all exposed skin, and safety glasses with side shields under the helmet.
- Fire and Explosion Risk: The heat from the welding arc can ignite combustible materials in the vicinity, while sparks can cause explosions in environments containing flammable gases or dust.
- Guidelines: Remove all flammable materials from the welding area. Use fire-resistant shields to contain sparks and slag. Keep fire extinguishers and fire blankets readily accessible.
Addressing these safety concerns is essential for the well-being of individuals performing welding tasks and for the overall safety of the workplace. Adhering to these guidelines helps mitigate risks associated with low hydrogen open root welding, ensuring that welding operations are conducted safely and effectively.
Common Injuries Associated with Using Low Hydrogen Welding Electrodes
While these electrodes are chosen for their performance characteristics and benefits in reducing hydrogen-induced cracking, it’s important to be aware of the common injuries that can occur if proper safety measures are not observed.
- Burns (Thermal and Radiation): Direct contact with the hot electrode, molten metal, or exposure to the welding arc can result in serious burns. Arc radiation, particularly ultraviolet (UV) light, can cause burns to exposed skin and eyes, similar to sunburn.
- Prevention: Wear appropriate personal protective equipment (PPE), including gloves, long-sleeve jackets, and pants made from durable, flame-resistant materials. Ensure that all skin areas are covered. Use welding helmets with proper shading to protect eyes and face from UV radiation.
- Eye Injuries (Arc Eye): Exposure to the intense UV light from the welding arc without adequate eye protection can lead to “arc eye” or welder’s flash, a painful condition affecting the cornea.
- Prevention: Always wear a welding helmet with a suitably rated auto-darkening filter to protect eyes from UV exposure. Safety glasses with side shields should be worn underneath the helmet for additional protection.
- Inhalation of Fumes and Gases: Welding processes generate harmful fumes and gases that can cause respiratory issues, metal fume fever, or long-term lung damage.
- Prevention: Ensure adequate ventilation in the welding area to dissipate fumes and gases. Use local exhaust ventilation (LEV) systems or respiratory protective equipment (RPE) when necessary, especially in confined spaces.
- Electric Shock: Contact with live electrical components of the welding equipment can lead to electric shock, a potentially fatal injury.
- Prevention: Maintain dry working conditions and wear dry, insulating gloves. Regularly inspect welding cables, electrode holders, and equipment for wear and damage. Follow proper grounding procedures for the welding equipment.
- Hearing Loss: Prolonged exposure to the noise produced by welding operations can result in temporary or permanent hearing loss.
- Prevention: Use earplugs or earmuffs to protect against noise in environments where sound levels are high. Regular breaks from noisy areas can also help reduce the risk of hearing damage.
- Musculoskeletal Disorders: Repetitive motions, awkward postures, and prolonged periods of welding can lead to musculoskeletal disorders, including back pain, tendonitis, and carpal tunnel syndrome.
- Prevention: Implement ergonomic solutions, such as adjustable work tables and anti-fatigue mats. Encourage regular breaks and stretching exercises. Train welders on proper lifting techniques and the use of mechanical aids to handle heavy objects.
Adherence to safety protocols and the use of appropriate PPE are crucial in minimizing the risk of these common injuries.
Welding Codes and Standards for Low Hydrogen Open Root Welding
- AWS D1.1/D1.1M, Structural Welding Code – Steel: Published by the American Welding Society (AWS), this code is one of the most widely used standards for welding structural steel. It provides guidelines for the welding of carbon and low-alloy steels, including provisions for the use of low hydrogen electrodes in various welding positions and joint configurations.
- ASME Boiler and Pressure Vessel Code, Section IX, Welding, Brazing, and Fusing Qualifications: The ASME BPVC Section IX establishes rules for the qualification of welding and brazing procedures as well as welders, brazers, and welding and brazing operators in the construction of boilers, pressure vessels, and nuclear components. It includes requirements for welding procedure specifications (WPS) that ensure the use of appropriate materials and methods, including low hydrogen welding techniques, for critical applications.
- API 1104, Welding of Pipelines and Related Facilities: Published by the American Petroleum Institute, API 1104 provides standards for the welding of pipelines used in the transportation of gas, petroleum, and related products. This code addresses the use of low hydrogen electrodes for the welding of pipeline joints, emphasizing the importance of preventing hydrogen-induced cracking in high-strength pipeline steels.
- ISO 15614, Specification and Qualification of Welding Procedures for Metallic Materials: This international standard series covers the qualification of welding procedures for metallic materials. It specifies how preliminary welding procedure specification (pWPS) tests should be conducted to determine optimal welding conditions, including the use of low hydrogen electrodes for various metals and welding processes.
Compliance with these welding codes and standards is essential for welders and welding engineers involved in low hydrogen open root welding projects. They serve as authoritative references that guide the welding process, ensuring that welded structures meet the required performance criteria for strength, durability, and safety.
Alternatives to Low Hydrogen Open Root Welding
The objective of LHORW is the the creation of strong, reliable welds in situations where minimizing the risk of hydrogen-induced cracking is crucial. There are several alternative solutions, each having its own set of advantages and considerations, making them suitable for different applications and material types.
Gas Tungsten Arc Welding (GTAW) or TIG Welding:
GTAW is a welding process that uses a non-consumable tungsten electrode to produce the weld. The TIG process is known for its ability to produce high-quality, precise welds, especially on thinner materials or where aesthetic appearance is important. GTAW can be used with or without filler material and is an excellent alternative for materials sensitive to hydrogen cracking.
Gas Metal Arc Welding (GMAW) or MIG Welding:
GMAW is a process that uses a continuously fed consumable wire electrode and a shielding gas to melt the metal and join it together. For applications where low hydrogen open root welding is considered, GMAW with a suitable filler material and gas mixture can provide an efficient and productive alternative, particularly for thicker materials and longer welds.
Flux-Cored Arc Welding (FCAW):
FCAW combines the advantages of shielded metal arc welding (SMAW) with those of GMAW. It uses a tubular wire filled with flux to facilitate the welding process. FCAW is adaptable to outdoor conditions and is effective for a wide range of thick materials. It offers the benefit of deep penetration and a high deposition rate, making it a viable alternative for projects where low hydrogen electrodes are typically used.
Submerged Arc Welding (SAW):
SAW is a process that employs a continuously fed consumable electrode and a blanket of fusible flux, which becomes conductive when molten and provides a current path between the workpiece and the electrode. This process is well-suited for welding thick sections and is known for its high deposition rates and deep penetration capabilities. SAW can be an alternative for fabricating large structures where controlling hydrogen is essential.
Electroslag Welding (ESW):
ESW is a highly productive, single pass welding process for thick materials, commonly used in the vertical position. It’s particularly useful for joining large plates and is noted for its ability to produce quality welds with minimal hydrogen content, making it an alternative for certain applications where low hydrogen welding is desired.
Each of these alternatives to low hydrogen open root welding offers unique benefits and is best suited to specific situations and material types. The choice of process should be guided by the specific requirements of the project, including the material properties, joint configuration, and desired weld characteristics.
Notes:
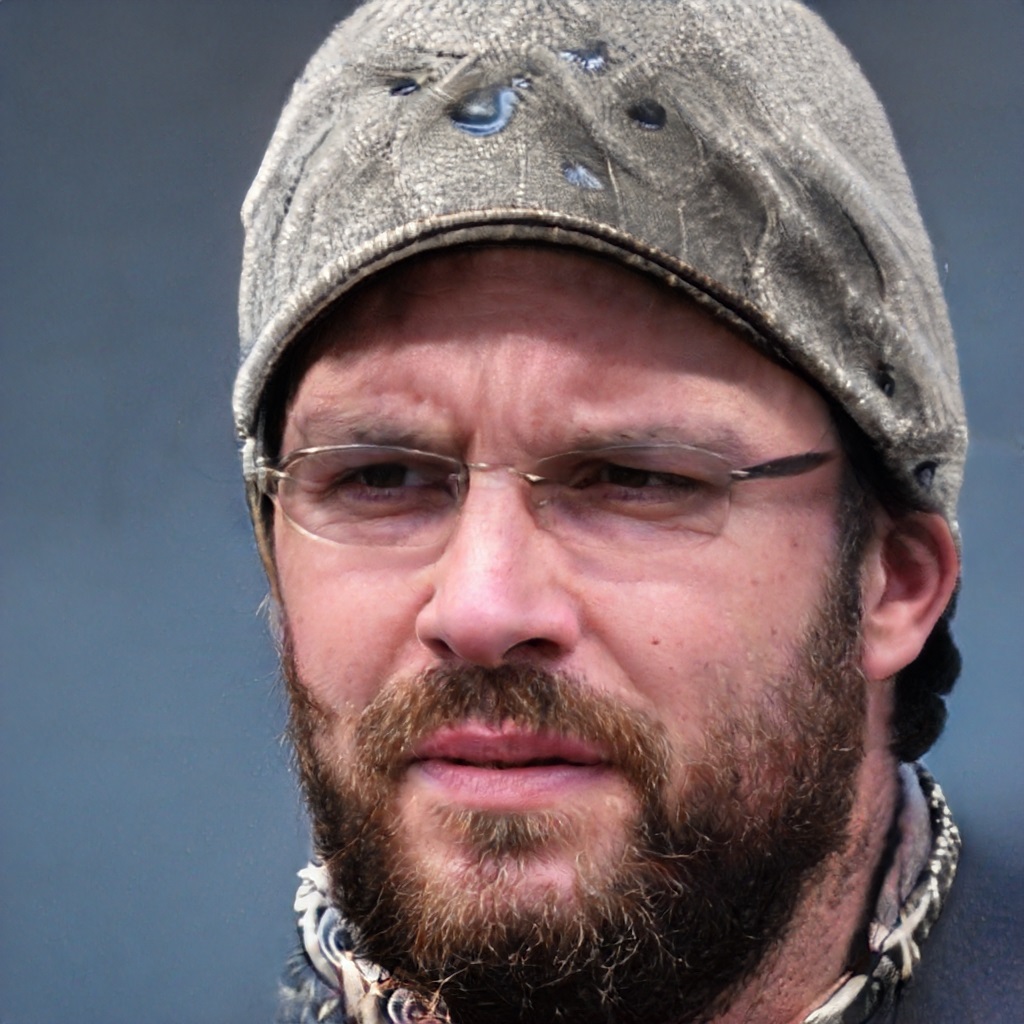
I’ve been involved in the welding industry for over twenty years. I trained in various engineering shops working on various projects from small fabrication and repairs through to industrial projects.I specialize in welding aluminum and food grade stainless steel and an now run an engineering shop fabricating equipment for the food industry.