Weld Spatter: How to Eliminate or Minimize the Problem
americanindustrialsupl and its partners may earn a commission if you purchase a product through one of our links.
Preventing and mitigating weld spatter (splatter) is essential for ensuring a successful welding process. Not only can weld spatter impact the appearance of the finished product, but it can also create safety hazards and result in added cleanup time. Weld spatter can damage surrounding equipment, contaminate surfaces, and even pose a risk of injury to nearby personnel.
By implementing prevention and mitigation techniques, welders can minimize these unwanted effects and improve their overall welding process. This includes selecting the right welding equipment and materials, adjusting heat input levels, and properly preparing the workpiece. In the following sections, we will delve into the specific causes of weld spatter and the strategies for minimizing its effects.
Shielding Gas Flow Complications:
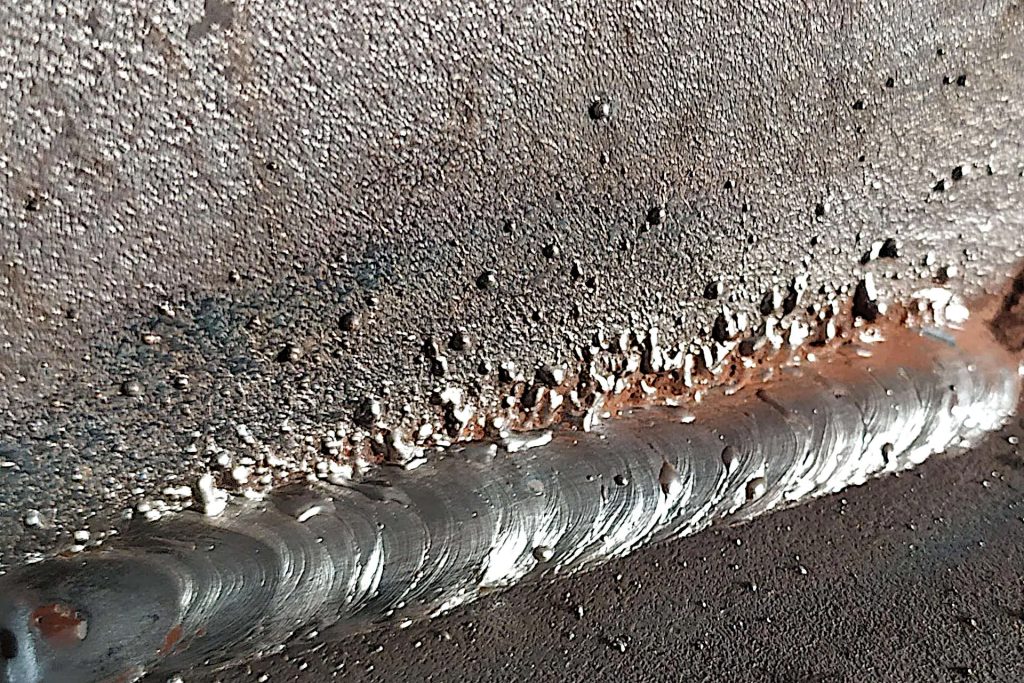
Shielding gas is an essential component of the welding process, as it prevents the weld area from being exposed to the surrounding air, which can lead to oxidation and contamination. When there are complications with the flow of shielding gas, it can cause significant problems, including increased weld spatter.
One of the main issues that can arise due to inadequate or disrupted shielding gas flow is an unstable arc. When the arc is unstable, it can cause irregular and uneven heat distribution, which in turn leads to increased spatter. Additionally, an unstable arc can cause the weld to become porous or weak, compromising the integrity of the weld joint.
Another issue that can arise due to shielding gas flow complications is blockages or leaks in the gas lines. Blockages can cause a reduction in gas flow, leading to an unstable arc and increased spatter. Leaks in the gas lines can also cause a reduction in gas flow and can create additional hazards, such as the risk of a gas explosion.
Finally, inadequate gas flow rates can also contribute to increased spatter. If the flow rate is too low, it may not provide adequate coverage for the weld pool, resulting in increased exposure to air and the formation of spatter.
In order to mitigate the impact of shielding gas flow complications, welders should regularly inspect and maintain their gas lines, ensuring that there are no leaks or blockages. They should also check gas flow rates to ensure they are within the recommended range for their specific welding process. By taking these steps, welders can help prevent weld spatter caused by shielding gas flow complications.
[amazon_auto_links id=”6660″]
Selection of Shielding Gas
The choice of shielding gas used during welding can also have a significant impact on the level of weld spatter. Different types of gas, such as carbon dioxide, argon, and a mixture of carbon dioxide and argon, can each present their own unique challenges.
Carbon Dioxide
Carbon dioxide is a common shielding gas used in welding, especially in MIG welding applications. While it is an effective gas for producing high-quality welds, it can also lead to increased levels of weld spatter.
One of the primary causes of spatter when using carbon dioxide is its high reactivity with the weld pool. This reactivity can cause the weld pool to become unstable and produce more spatter. Additionally, carbon dioxide can create a more turbulent weld pool, which can also contribute to increased spatter.
Argon
Argon is another commonly used shielding gas in welding, particularly for TIG welding applications. Compared to carbon dioxide, it is less reactive and can produce a more stable weld pool.
However, while argon can lead to lower levels of spatter overall, it can still cause issues if not used properly. For example, if the gas flow rate is too high, it can cause turbulence in the weld pool and lead to increased spatter.
Mix of Carbon Dioxide and Argon
Many welding applications use a mixture of carbon dioxide and argon to take advantage of the benefits of both gases. However, finding the right balance can be tricky, as too much of either gas can cause issues.
In general, a higher percentage of argon in the mixture can lead to a more stable weld pool and lower levels of spatter. However, a higher percentage of carbon dioxide can increase penetration and weld speed, making it useful in certain applications.
Overall, selecting the right shielding gas and ensuring it is used properly is key to minimizing the negative effects of weld spatter. Welders should carefully consider the specific requirements of each job and choose the gas and gas flow rate accordingly.
Suboptimal Electrode Selection:
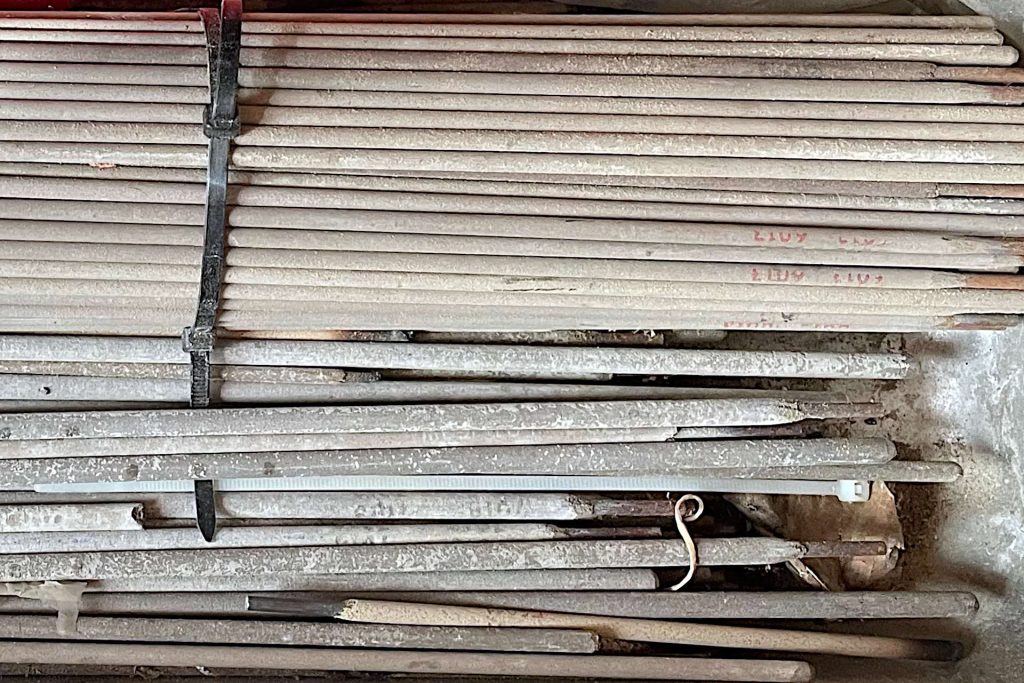
Choosing the right electrode is crucial to ensuring a successful welding process. Using the wrong electrode material or size can lead to increased spatter, porosity, and even weld defects. Suboptimal electrode selection can cause a number of problems during the welding process, including:
Unstable Arc:
If the electrode is too small or too large for the welding process, it can lead to an unstable arc. An unstable arc causes irregular and uneven heat distribution, which in turn leads to increased spatter.
Porosity:
If the electrode is not compatible with the base metal, it can cause porosity in the weld. Porosity is the presence of small gas pockets or holes in the weld, which can compromise the strength of the joint and lead to weld failure.
Increased spatter:
Using an electrode that is too large can result in increased spatter. This occurs because the larger electrode requires more heat to melt, leading to a greater amount of spatter during the welding process.
Weld defects:
Choosing the wrong electrode material can result in weld defects. For example, using a high-carbon electrode on low-carbon steel can cause cracks or fissures in the weld joint.
To avoid these problems, it is essential to choose the right electrode for the welding process. This includes selecting an electrode with the right material and size for the base metal and the welding process. Welders should also ensure that their electrodes are stored properly and that they are using electrodes that are not damaged or expired. By taking these steps, welders can minimize the impact of suboptimal electrode selection on their welding process and reduce the likelihood of weld spatter.
Poor Joint Design Issues:
Poor joint design is another common cause of weld spatter, and can lead to a range of problems during the welding process. A poorly designed joint can lead to increased spatter, porosity, and even weld defects. Some common problems associated with poor joint design include:
Uneven joint fit-up:
If the joint is not properly aligned and fitted, it can cause irregular and uneven heat distribution during the welding process. This can lead to increased spatter and porosity, as well as weld defects.
Insufficient weld preparation:
Poor weld preparation can lead to a range of problems, including increased spatter and weld defects. If the weld preparation is inadequate, it can lead to the accumulation of contaminants or other impurities in the joint, which can compromise the quality of the weld.
Inadequate joint reinforcement:
Joint reinforcement refers to the additional metal added to a joint to improve its strength. If the joint reinforcement is inadequate, it can lead to increased spatter and porosity during the welding process, as well as decreased joint strength.
Lack of root gap:
The root gap is the space between the base metal components that is filled by the welding material. If the root gap is inadequate, it can lead to increased spatter and porosity, as well as decreased joint strength.
To avoid these problems, it is important to properly design and prepare the joint before beginning the welding process. This includes ensuring that the joint is properly aligned and fitted, that the weld preparation is adequate, and that the joint reinforcement and root gap are appropriate for the welding process. By taking these steps, welders can minimize the impact of poor joint design on their welding process and reduce the likelihood of weld spatter.
Dirty or Grimy Metal Causing Weld Spatter
While shielding gas, electrode selection, and joint design are some of the most common causes of weld spatter, dirty or grimy metal can also contribute to this issue. When welding on contaminated metal surfaces, the impurities can vaporize and get trapped in the molten metal, leading to spatter.
To prevent this from happening, it is crucial to properly clean the metal surface before starting the welding process. This can involve using solvents, degreasers, or other cleaning agents to remove dirt, oil, rust, or other contaminants that may be present on the metal.
Another important aspect to consider is the storage and handling of the metal. If the metal has been exposed to moisture or other corrosive agents, it can develop rust or other types of oxidation that can also contribute to spatter. Therefore, it is essential to store and handle metal in a dry, clean, and controlled environment to prevent contamination and ensure the best welding results.
By taking proper cleaning and handling precautions, welders can minimize the risk of spatter caused by dirty or grimy metal and achieve high-quality welds that meet the required standards.
Strategies for Minimizing Unwelcome Effects of Spatter
Welding spatter can be minimized or eliminated if you employ the right welding practices.
Adjustment of Heat Input Levels:
One of the most effective strategies for minimizing weld spatter is to adjust the heat input levels during the welding process. Heat input is a critical factor in the welding process, as it determines the amount of heat that is applied to the joint during welding. If the heat input is too high or too low, it can lead to increased spatter, porosity, and other defects.
To minimize the impact of heat input on weld spatter, it is important to understand how heat input affects the welding process. Heat input is determined by the welding parameters, including the welding speed, voltage, and current. These parameters can be adjusted to control the amount of heat input that is applied to the joint during welding.
To adjust the heat input levels, welders can make several changes to the welding parameters. For example, reducing the welding speed can reduce the heat input, which can help to minimize the impact of spatter. Similarly, reducing the welding voltage and current can also reduce the heat input, and help to minimize the impact of spatter.
It is important to note, however, that adjusting the heat input levels can also impact the quality of the weld. If the heat input is too low, it can lead to insufficient fusion and poor joint strength. Conversely, if the heat input is too high, it can lead to excessive distortion and other defects.
Therefore, it is important to carefully balance the heat input with other welding parameters to achieve the desired welding results. This may require some experimentation and adjustment to find the optimal settings for each welding job. Welders should also consider the specific requirements of the job, including the material being welded, the joint design, and other factors that may impact the welding process.
By carefully adjusting the heat input levels and other welding parameters, welders can minimize the impact of spatter on their welding process and achieve high-quality welds with minimal defects.
Use of Backing Plates:
Another effective strategy for minimizing weld spatter is to use backing plates during the welding process. Backing plates are essentially metal plates that are placed behind the joint being welded to provide support and prevent the molten metal from flowing through the joint and creating spatter.
Backing plates can be made from a variety of materials, including steel, copper, and aluminum. The type of material used will depend on the specific welding application, as well as the size and shape of the joint being welded.
When using a backing plate, it is important to ensure that it is positioned correctly and securely behind the joint being welded. This can help to prevent the plate from moving during the welding process, which could cause additional spatter and defects.
In addition to providing support, backing plates can also help to improve the quality of the weld. By preventing the molten metal from flowing through the joint, backing plates can help to ensure that the weld is fully penetrated and free of defects. This can be particularly important when welding thicker materials or complex joint designs.
However, it is important to note that the use of backing plates can also introduce some new challenges to the welding process. For example, the added mass of the backing plate can cause the joint to heat up more slowly, which could impact the overall welding speed and productivity. Additionally, the use of a backing plate may require additional setup time and preparation, which could increase the overall cost of the welding job.
Despite these challenges, the use of backing plates can be an effective strategy for minimizing weld spatter and achieving high-quality welds. Welders should carefully consider the specific requirements of each welding job, including the material being welded, the joint design, and other factors, in order to determine whether a backing plate is the best solution for their particular application.
Weld Spatter Spray
With some welding methods particularly gasless welding such as flux cored welding or if using stick welding, a certain amount of spatter is sometimes inevitable. In these vases you can reduce the clean up requirements by applying a anti spatter spray.
Weld anti spatter spray is a commonly used product that helps prevent weld spatter from sticking to surfaces such as the weld nozzle, welding table, and workpiece. It is typically a liquid or aerosol that is sprayed onto the surfaces before welding to create a barrier between the metal and the spatter.
The spray works by creating a thin layer of lubrication on the metal surface, which helps prevent the spatter from adhering to the surface. This reduces the amount of spatter that is produced during the welding process and makes it easier to clean up any spatter that does occur.
While weld anti spatter sprays can be effective in reducing spatter, they are not always the best solution. In some cases, the spray can interfere with the welding process and cause issues such as porosity or contamination of the weld. Additionally, if the spray is not properly applied or if too much is used, it can cause the spatter to be flung further away from the weld and increase the risk of it sticking to other surfaces.
Key Takeaways
Weld spatter is a common problem that can negatively impact the quality and efficiency of welding operations. Understanding the causes of weld spatter, including shielding gas flow complications, suboptimal electrode selection, and poor joint design issues, is key to developing effective strategies for preventing and mitigating its effects.
Adjusting heat input levels, using backing plates, and implementing other strategies can help to minimize the negative effects of weld spatter and improve the overall quality of welding operations.
In some instances anti spatter spray can be a useful tool in preventing weld spatter and improving the quality of the welds. However they are far from full proof and we would always advise other methods, such as adjusting the welding settings or improving the joint design as these are going to be more effective in reducing spatter.
Welders should carefully consider the specific requirements of each welding job, including the material being welded, the joint design, and other factors, in order to develop the most effective strategy for preventing and mitigating weld spatter.
Further Reading
- Wikipedia: Techniques to Help Reduce Spatter
- Journal of laser Applications: Spatter in Laser Welding
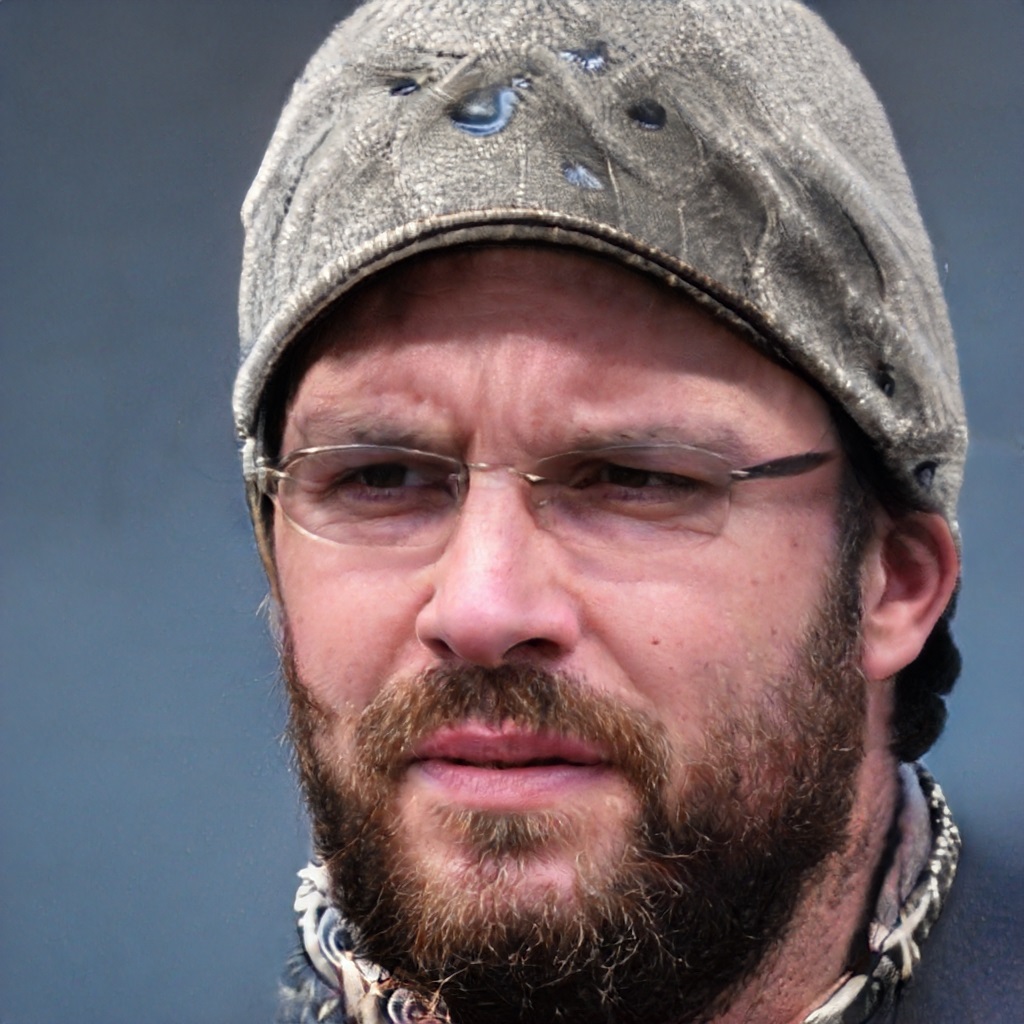
I’ve been involved in the welding industry for over twenty years. I trained in various engineering shops working on various projects from small fabrication and repairs through to industrial projects.I specialize in welding aluminum and food grade stainless steel and an now run an engineering shop fabricating equipment for the food industry.