Flux Core Welding Polarity Demystified: The Key to Perfect Welds Revealed!
americanindustrialsupl and its partners may earn a commission if you purchase a product through one of our links.
Flux core welding utilizes consumable electrode wires filled with flux to provide shielding for the weld pool. Polarity, or the direction of current flow, is an important but often overlooked parameter when flux core welding. The selection of direct current electrode positive (DCEP), sometimes referred to as reverse polarity welding, direct current electrode negative (DCEN), or alternating current influences the characteristics and quality of the weld joint.
Flux Core Wire
Understanding Flux Core Welding Polarity
What is Polarity in Welding?
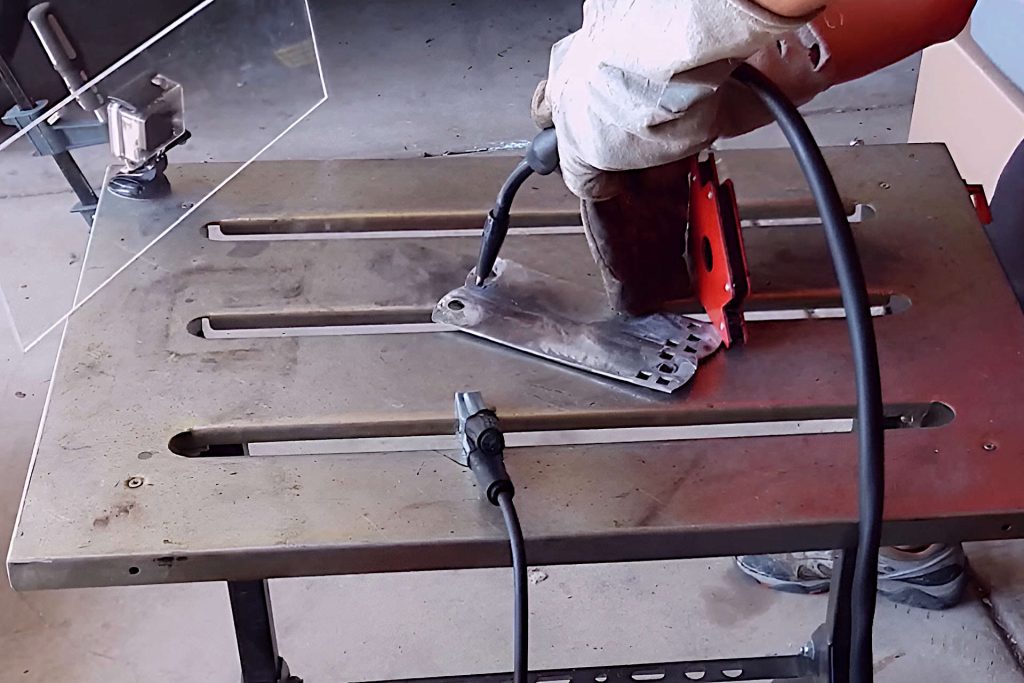
The type of current used for welding and the welding polarity have a huge bearing on the weld and it quality. Polarity refers to the direction of the current flow between the electrode (welding wire) and the workpiece being welded, while the current refers to whether it is DC or AC.
- In direct current (DC) welding, the current flows in one direction only. In DCEN, the electrode is negatively charged and the workpiece positively charged. In DCEP, the electrode becomes positively charged and the workpiece negative.
- In alternating current (AC) welding, the polarity cycles between DCEN and DCEP rapidly during welding. The electrode and workpiece alternate between being the anode and cathode.
Polarity affects the heat generation pattern and the type of metal transfer at the arc, impacting the final weld.
Understanding Flux Core Welding
Flux core arc welding (FCAW) uses a continuous metal electrode wire filled with fluxing agents. As the wire melts, the flux produces protective gases and slag to shield the weld pool. Additional shielding gas may also be used. The slag floats to the top of the weld bead and must be chipped away.
Key advantages of flux core welding include higher deposition rates, all-position capabilities, and the ability to weld outside with windy conditions. The flux core wire provides its own shielding, reducing the need for external shielding gas.
Why Polarity Matters for Flux Core Welds
- Polarity settings significantly influence the penetration profile, bead shape, deposition rate, and arc stability when flux core welding.
- The optimal polarity option depends on the base metal thickness, joint design, welding positions, and accessibility to the joint.
- While general recommendations exist, there is an ongoing debate around which polarity, DCEN or DCEP, produces superior flux core welds.
Below we will explore the benefits of both negative and positive polarity settings for flux core welding, providing guidance on when to use each for high quality, productive welds.
The Case for Positive Polarity in Flux Core Welding
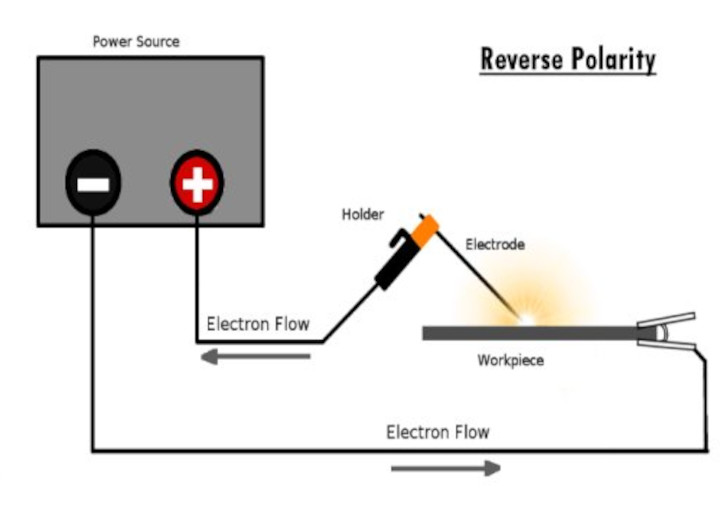
In flux core arc welding, positive polarity (sometimes referred to as reverse polarity), or DCEP, is advocated by many as the superior polarity setting for most applications. Positive polarity provides benefits like higher deposition rates, a more stable arc, and the ability to weld thicker sections.
Benefits of Using DCEP
Selecting direct current electrode positive (DCEP) polarity for flux core welding offers several advantages:
- Increased deposition rates, resulting in higher welding productivity
- Higher current densities allow faster travel speeds
- Improved arc stability for better puddle control and weld appearance
- Lower spatter levels, reducing post-weld cleanup
- Higher penetration capabilities for welding thicker materials
With DCEP, around 2/3 of the arc heat is concentrated at the positively charged workpiece. This wider, hotter weld pool enhances welding speed.
When to Use DCEP Polarity
DCEP is the preferred polarity option for flux core welding in situations like:
- Welding joints over 1/4″ thick using larger diameter FCAW wires
- Maximizing welding productivity and deposition rates
- Welding in the vertical or overhead positions
- Welding structures and frames where speed is critical
- Highly stressed connections that require deep penetration
- Automated or robotic flux core welding
The extra energy density provided by DCEP allows for faster travel speeds while still achieving full penetration on thicker sections.
Supporting Evidence for DCEP Being Superior
There is significant amount of opinion favoring DCEP polarity for flux core welding:
- Leading welding educational institutions overwhelmingly endorse DCEP in their training programs
- Some welding codes and manufacturers mandate the use of DCEP for flux core welds
- Many studies prove higher mechanical properties and quality using DCEP polarity
Except for sheet metal and thin sections, DCEP is usually the best polarity choice for flux core welding for its advantages in speed, penetration, and weld quality.
Reasons to Use Negative Polarity for Flux Core Welding
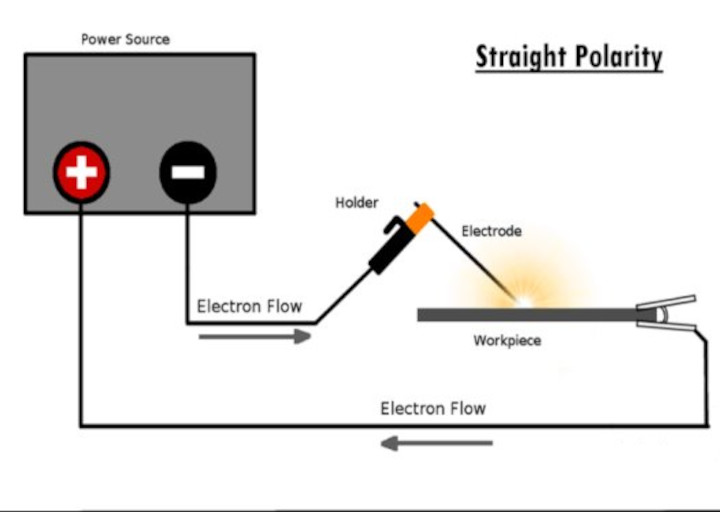
While positive polarity has its benefits, many welders have found, and thus argue, that negative polarity (DCEN) is actually optimal for most flux core welding applications. DCEN (straight polarity) provides superior arc stability, penetration, and quality on thin materials and smaller welds.
Advantages of Using DCEN
Key benefits of using direct current electrode negative polarity in flux core welding include:
- Better penetration capabilities for complete fusion
- Improved weld toe profiles with full fill at the joints
- Ability to weld thinner base metals below 1/4″ thick
- Lower heat input minimizes chances of burn through
- Excellent arc stability even at low welding currents
In DCEN, approximately 2/3 of the arc heat concentrates on the negatively charged electrode, focusing heat right at the weld.
Applications Where DCEN Excels
DCEN is the polarity of choice for flux core welding when:
- Welding sheet metal, thin sections, and smaller parts
- Welding in positions other than flat (horizontal, vertical, overhead)
- Maximizing weld fusion and reducing lack of penetration risks
- Welding root passes and first passes on pipe and plate welds
- Producing high quality welds is more important than speed
The tighter arc column and lower heat input of DCEN prevents melting away of the thinner base metal.
Data Supporting DCEN as the Ideal Polarity
There are good arguments favoring DCEN for flux core welding:
- Welding codes often specify DCEN for pipe and aerospace welding
- DCEN produces less distortion and cleaner welds with less spatter
- Many experts argue DCEN results in higher weld strength and ductility
- Welding tests show DCEN provides better impact toughness values
For thin materials and fill/cap passes requiring the highest quality, DCEN is likely the best polarity setting.
Professional Perspectives on Flux Core Polarity
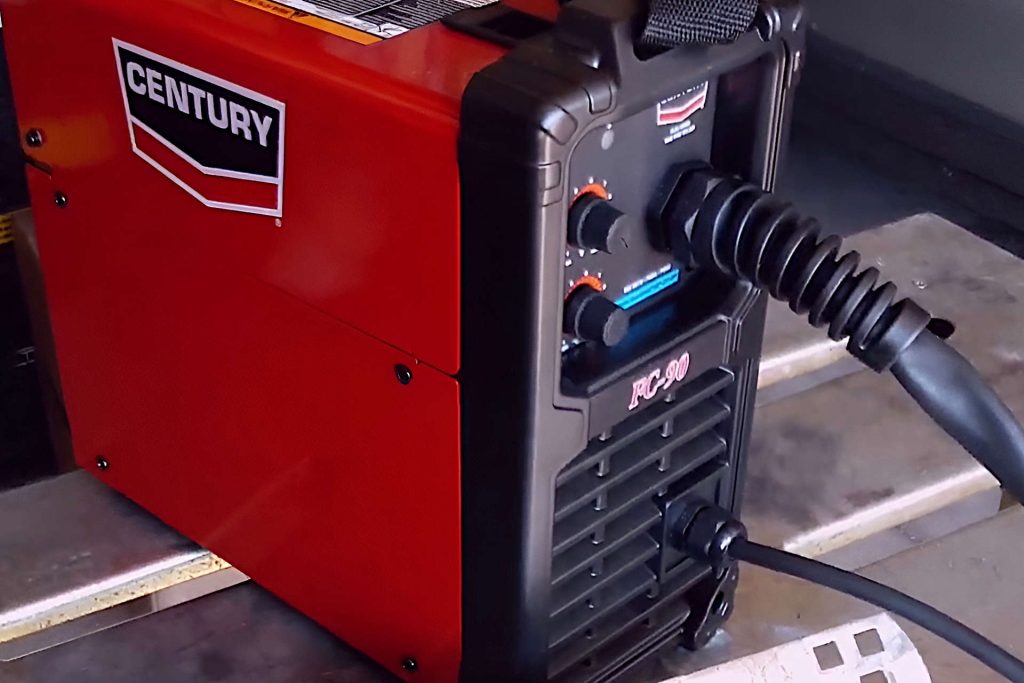
Lincoln Electric FC90 Flux Core Wire Feed Welder and Gun, 90 Amp, 120V, Inverter Power Source for Easy Operation, Portable Shoulder Strap, Best for Small Welding Jobs
When selecting polarity for flux core welding, it helps to consider the experiences and insights of various welding professionals. Each brings a unique viewpoint based on their role.
Welding Engineer Point of View
From a welding engineering perspective:
- DCEP is preferred for structural and automatic/robotic welding where speed is important
- DCEN excels on manual welds and thin materials requiring maximum penetration
- Overall, DCEP polarity is used more frequently in typical flux core applications
Welding engineers aim to balance productivity, quality, and costs when choosing polarity.
Welding Inspector Opinion
A welding inspector critiques welds from both polarities:
- DCEP can overheat and distort thinner materials if not welded carefully
- DCEN provides assurance of penetration but may lack fillet weld throat thickness
- Polarity must align with welding procedure specifications and codes
- Mechanical properties and non-destructive test results matter most
Inspectors want welds that meet quality and strength requirements regardless of polarity.
Welding Operator Experience
Welders who make the welds share important polarity insights:
- DCEN allows easier welding of fillet and groove welds out of position
- DCEP typically permits faster travel on flat welds for higher productivity
- No single polarity works best – it depends on the application
- Productivity, quality, and minimizing rework are all essential
Operators look to balance ease of use with speed based on each unique welding situation.
In the end, while preferences exist, the ideal FCAW polarity depends on many factors. Experience provides guidance but test welds validate performance.
Best Practices for Flux Core Polarity Selection
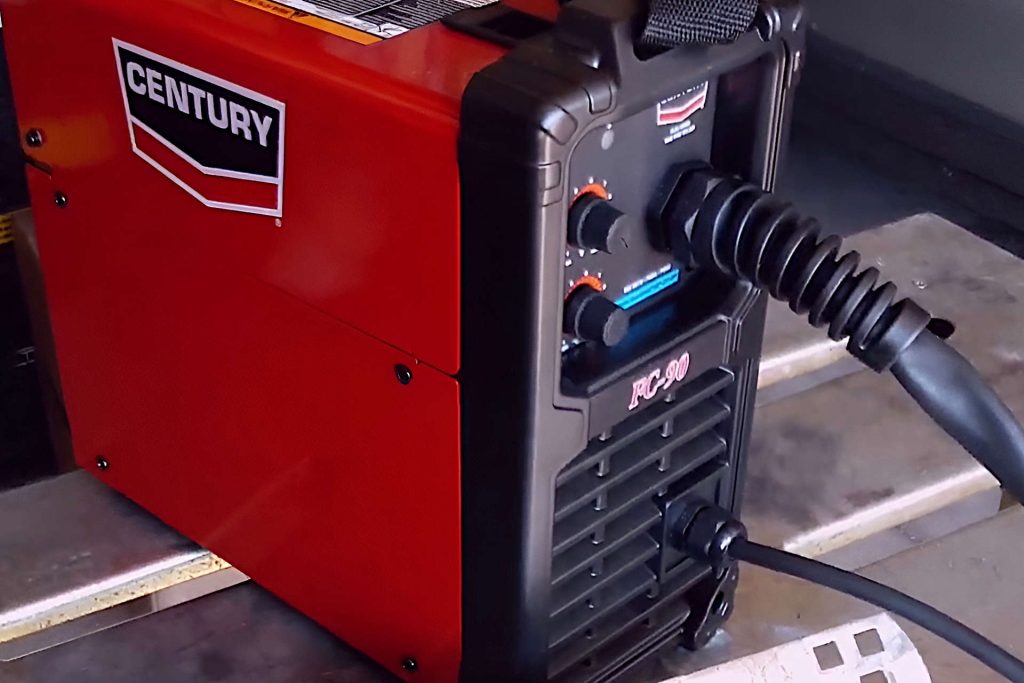
When selecting polarity for a flux core welding application, there are some best practices to follow:
Matching Polarity to the Application
Consider factors like:
- Base metal type and thickness
- Joint design and accessibility
- Welding positions and progression
- Productivity vs quality needs
Then choose:
- DCEP for thicker sections and maximizing deposition rate
- DCEN for thinner materials requiring maximum penetration
Fine-Tuning Polarity for Specific Materials
- For carbon steel, use DCEP on thicker sections over 1/4” and DCEN on thinner
- For stainless steel, use DCEN for optimal penetration and corrosion resistance
- You cant use self-shielding wires for aluminum because of the nature of the metal. Solid wire with DCEP for shallow penetration and to prevent oxide issues ids the best option.
Polarity Settings for Different Joint Configurations
- For filet welds, use DCEN for assured toe fusion, especially out of position
- For lap joints, use DCEN for penetration without excessive buildup
- For butt joints, use DCEP for higher speed on thick sections but DCEN on thin
Polarity Considerations for Welding Positions
- For flat welds, use DCEP for faster travel speed and higher deposition rate
- For vertical-up welds, use DCEN for better puddle control and penetration
- For overhead welds, use DCEN to prevent dripping and lack of fusion issues
In summary, base the polarity selection on the specific needs of the application – there is no one-setting-fits-all solution in flux core welding. Proper polarity maximizes quality and productivity.
Final Thoughts: Flux Core Welding Polarity
In flux core arc welding, polarity is a critical parameter that impacts the welding arc, heat flow, and ultimate weld quality. This guide has explored the debate around using direct current electrode positive (DCEP) versus direct current electrode negative (DCEN) polarity for FCAW.
There are good arguments on both sides. DCEP offers benefits like higher deposition rate, faster travel speeds, and deeper penetration on thick sections. DCEN provides advantages such as superior arc stability, better penetration on thin materials, and higher quality welds.
In the end, the ideal FCAW polarity depends on factors like base metal thickness, joint type, welding position, accessibility, and whether quality or productivity is more important for the application.
While general recommendations exist, welders should perform test welds to dial in the optimal polarity settings for their specific application. By matching polarity to the needs of each weld, operators can achieve the highest productivity without sacrificing weld quality.
The key is finding the right balance between penetration profile, arc characteristics, speed, and final weld properties through proper polarity selection. Understanding the nuances of flux core welding polarity allows creating perfect welds efficiently.
Commonly Asked Questions
are a few of the most commonly asked questions regarding flux core welding polarity:
What polarity should be used for flux core welding of mild steel?
For mild steel thicker than 1/4″, use DCEP for faster speeds and higher deposition rates. For thinner steels, use DCEN for better arc stability and penetration.
Is DCEN or DCEP better for lap joints?
For lap joints, DCEN allows focusing heat at the seam for penetration without excessive buildup. DCEP can overheat and melt the thinner overlapping edges.
What polarity causes less spatter when flux core welding aluminum?
You can’t uses the flux core welding method with aluminum because of the nature of the metal. You need to weld with solid wire and gas shielding. When doing so if you use DCEP it produces a wider, hotter weld pool on aluminum which increases spatter. Use DCEN for a tighter arc and lower heat input to reduce spatter.
How do you determine the right polarity setting for a weld?
Consider material thickness, joint type, welding position, quality needs, and productivity requirements. Perform test welds to compare DCEN vs DCEP for the application.
Why does polarity matter more for some metals compared to others?
Polarity has a larger impact on penetration and bead shape on conductive metals like carbon steel. On less conductive metals like stainless steel, polarity is less critical.
Is straight polarity always preferred for flux core welding?
While straight polarity (DCEN or DCEP) is most common, alternating current (AC) can help on thicker materials and exotic alloys by providing cleaning action and broader penetration.
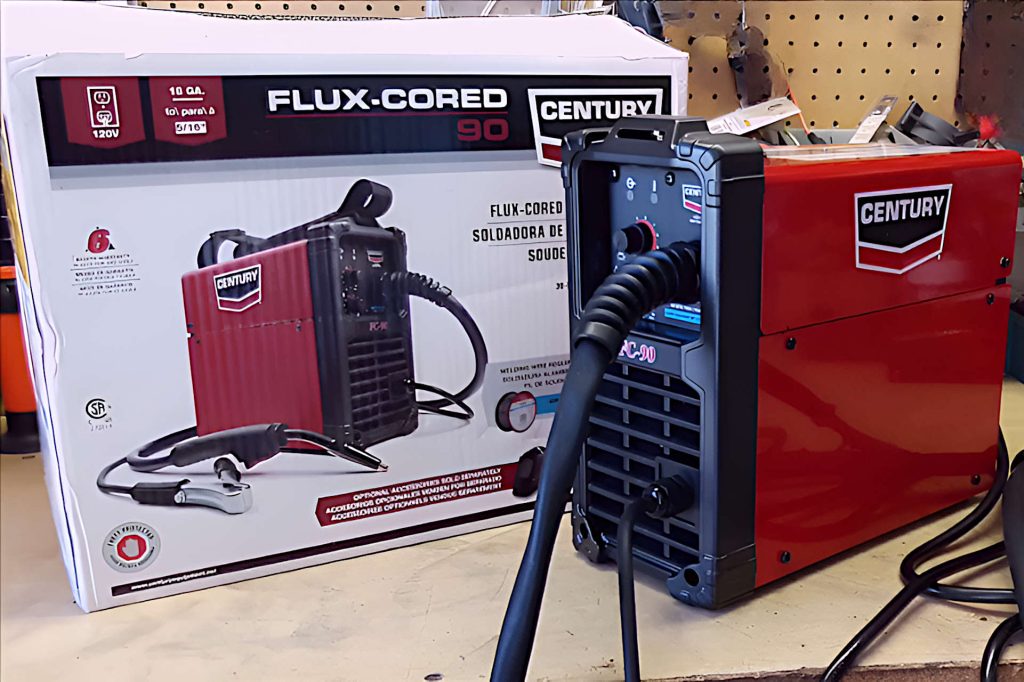
Lincoln Electric FC90 Flux Core Wire Feed Welder and Gun, 90 Amp, 120V, Inverter Power Source for Easy Operation, Portable Shoulder Strap, Best for Small Welding Jobs
Videos
Resources
- Materials: Welding Flux Core Welding Wire for Continuous Cast Roller Over Laying Welding
- Welding International: Bead Characterization of Fcaw of A Rutilic Fluxed Core Wire
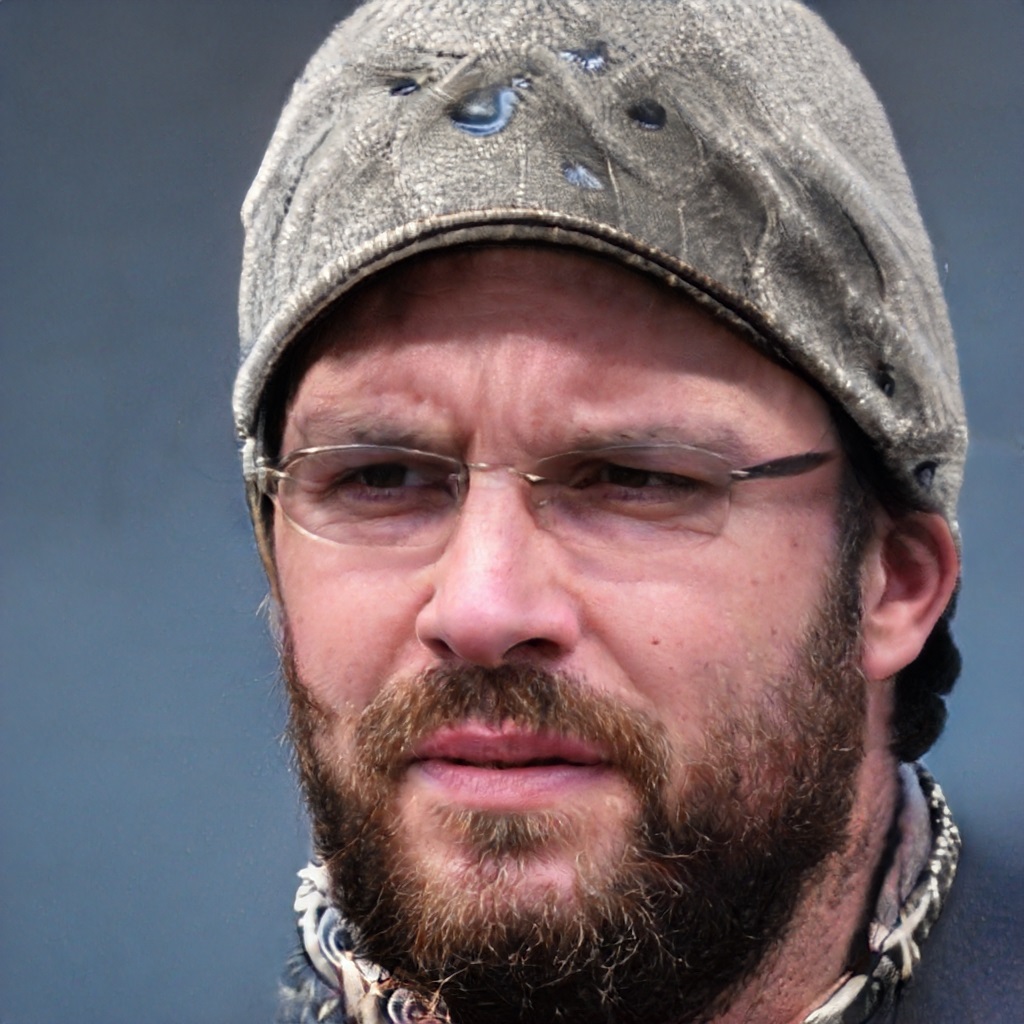
I’ve been involved in the welding industry for over twenty years. I trained in various engineering shops working on various projects from small fabrication and repairs through to industrial projects.I specialize in welding aluminum and food grade stainless steel and an now run an engineering shop fabricating equipment for the food industry.