How TIG Welding Without Gas Works
americanindustrialsupl and its partners may earn a commission if you purchase a product through one of our links.
- It is possible to TIG weld without gas but results can be variable, requires considerable skill, and only advised if there are no other options
- Although the flux will provide some sort of shield it is not usually enough causing contamination to and burning out of the tungsten.
- If using flux-cored wire or filler rods it is better to use on short welds
- If it is a question of reducing or saving gas consider a gas lens or dual shield flux-cored rod combination.
It is possible to perform TIG welding without gas, although it require a certain amount of skill and even then can be problem. This gasless method that is used is usually referred to as Flux-cored TIG welding.
In this article, we will focus on how you can TIG weld without using gas, discussing the process and characteristics of the Flux-cored TIG welding method, the power source and types of tungsten electrodes used, the materials and industries where it is commonly used, and the potential advantages and disadvantages compared to TIG welding with gas.
We will also cover alternatives and consequences of the TIG welding without a shielding gas, plus the additional safety considerations that you will need to consider when using this welding technique.
What is TIG Welding and the Role of Gas?

TIG welding (Tungsten Inert Gas welding) is a method of welding that uses a tungsten electrode to create an arc between the base metal and filler metal. The tungsten electrode is heated by passing electricity through it, which melts the electrode and produces heat.
Generally, TIG welding requires a shielding gas to protect the weld pool and the tungsten electrode from atmospheric contamination. The operator controls the weld puddle by manipulating the tungsten electrode and filler metal with the gas, usually argon, helium or a mix. To perform TIG welding safely, a power source must be connected to the work area to prevent the risk of electrical shock or overheating equipment.
Characteristics of TIG Welding:
TIG welding is a manual welding process that uses a tungsten electrode and inert gas to create a weld. The process involves heating the work piece to its melting temperature, usually around 1500°C (2700°F), using electricity or an arc between electrodes. To ensure a successful TIG weld, the work piece must be free of contaminants and properly cleaned before welding. TIG welding is suitable for a variety of materials, including steel, aluminum, and alloys, and is commonly used in industries such as construction, automotive, aerospace, and manufacturing.
Supplies and Techniques for TIG Welding Without Gas:
There are a few different materials and techniques that can be used for TIG welding without gas. The most common is flux-cored welding, which uses flux-coated tungsten electrode. The flux helps to shield the weld puddle from the surrounding atmosphere in order to prevent contamination.
Another option is to use a “gas lens” on the TIG torch, which helps to focus the flow of gas and improve shielding. In addition to these materials, there are also specific techniques that can be used to help maintain a stable arc and produce a high-quality weld. For example, operators can use a “walking the cup” technique, where they slowly rotate the TIG torch around the weld joint while maintaining a consistent arc length.
Flux-Cored TIG Welding
In this process, the welding torch is used to feed the flux-cored wire into the weld pool, where it melts and forms the weld bead. The flux in the wire provides a shield around the weld pool, preventing atmospheric contamination from affecting the quality of the weld.
There are several different types of flux materials used in flux-cored TIG welding, each designed for specific applications. Three of the main ones are:
- Rutile flux: Often used on sheet material as it produces less spatter.
- Basic flux: Higher quality weld used mainly on heavy materials.
- Cellulose flux: This flux allows deeper penetration and is better for thick metals.
Using a Gas Lens with Your TIG Torch
Although not a gasless method, using a “gas lens” on the TIG torch can reduce the amount of gas used and help to improve the quality of the weld by providing better gas coverage around the welding area.
The gas lens is a small device that fits inside the TIG torch and helps to distribute the shielding gas evenly around the weld. This is achieved by creating a vortex of gas that flows around the electrode, ensuring that the gas is directed towards the welding area.
Dual Shield Process
If it is a question of reducing gas consumption then using a dual shielding process incorporating flux-cored welding rods with shielding gas is another option. The flux-core is not good enough on its own to enable gasless welds easily but it does provide enough of a shield for you to dial-down the amount of argon that you use, possibly being able to reduce it by half.
Safety Considerations for TIG Welding Without Gas:
TIG welding without gas can present some additional safety considerations compared to TIG welding with gas. One potential hazard is the risk of electrical shock, as the operator is directly handling the tungsten electrode and filler metal.
It is important to ensure that the work area is properly grounded and that all safety equipment, such as gloves and eye protection, is worn. Another concern is the risk of overheating the equipment or the work piece, which can lead to a fire hazard. To prevent this, operators should use a proper power source and follow the manufacturer’s recommendations for amperage and voltage settings.
Materials and Industries for TIG Welding:
TIG welding can be used to weld a wide variety of materials, including metals such as steel, aluminum, and copper, as well as alloys and other specialty materials. TIG welding is commonly used in industries such as construction, automotive, aerospace, and manufacturing, where precise and high-quality welds are required.
Types of Tungsten Electrodes for TIG Welding:
There are several different types of tungsten electrodes that can be used for TIG welding, each with their own characteristics and best uses. The most common type is a pure tungsten electrode, which is suitable for most general TIG welding applications.
Other options include seriated tungsten electrodes, which are good for low amperage welding, and lanthanotid tungsten electrodes, which have a longer lifespan and are resistant to contamination. To choose the right tungsten electrode for a specific application, it is important to consider the material being welded, the amperage and voltage of the power source, and the type of gas being used (if applicable).
Types of Power Sources for TIG Welding:
TIG welding can be performed using either an AC (alternating current) or DC (direct current) power source. AC power sources are typically used for welding aluminum and other non-ferrous metals, as they provide a more stable arc and are less prone to tungsten contamination
How to Decide if TIG Welding Without Gas is Worth It
When deciding if TIG welding without gas is worth it, you need to consider the following:
- How much you are willing to spend on equipment. This will include the cost of your welder and any accessories such as torches or wire feeders.
- How much time you want to spend learning how to operate your equipment safely and effectively. If this is a priority for you then perhaps purchasing an entire set up would be best because it will cut down on learning curves later on when trying out other methods such as stick welding with flux cored electrodes (FCX).
- Whether or not any additional benefits come from using TIG welds in contrast with other types like MIG/TIG or stick welding with FCX instead of flux core wires only.”
Other than TIG What Other Options Do You Have?
There are a number of options that you can use to weld steel without gas. They include:
- MIG welding
- Stick welding
Probably the most popular method of welding without gas is stick welding. Stick welding doesn’t require gas as the electrode is coated in a flux that shields the weld in the similar fashion to Flux-cored TIG welding. The other option is MIG Flux-cored welding which tends to be easier to master than the TIG equivalent.
You can also use these methods, including TIG flux-cored, when you don’t have access to a machine shop or need something quick and easy, such as when working with scrap metal.
What Are Alternatives Methods to TIG welding without Gas?
There are a number of probably better alternatives to TIG welding without gas, depending on the type of material you are working with. The main one you will come across is MIG welder (flux core), which is actually more properly referred to as Flux-cored arc welding (FCAW) .
The advantages of MIG flux-corded over TIG flux-coded and that relates to the way the wire is fed. TIG torch cannot feed the wire while a MIG gun is set up to do so, normally through the machine or sometimes using a spool attachment on the gun.
Plasma cutters are great for stainless steel and other tough metals because they don’t require any shielding gas.
Why You Might Want to Lear to TIG Without Gas
One good reason to reason why you would want to learn how to weld without gas is because it will help you learn the basics of TIG welding and teach you how these machines work. It’s important for new welders because they will be able to start out by learning how their newfound skills translate into actual projects in their workplace or at home.
TIG Welding Without Gas vs. MIG Welding Without Gas
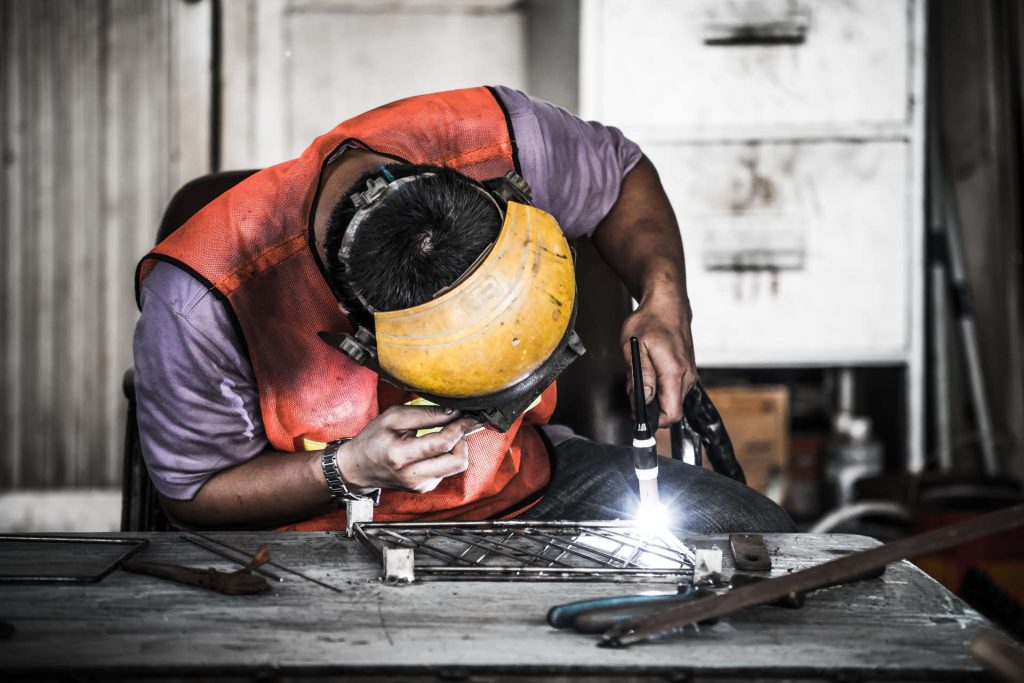
TIG welding without gas is a possible option although MIG welding without gas is also a viable option. Both have pros and cons, but both are quite different from each other.
One major difference between TIG flux-cored welding and MIG flux-cored welding is the type of welding process used. TIG welding is a manual process that requires a skilled operator to control the welding torch and the feed the wire manually, while MIG welding is a semi-automatic process that uses a spool gun to feed the wire automatically. This can make MIG welding faster and more efficient, but it can also lead to more inconsistency in the weld.
Another difference between the two methods is the type of flux-cored wire used. TIG flux-cored wire is typically thinner and softer than MIG flux-cored wire, which can make it easier to feed into the weld pool and control the weld. However, MIG flux-cored wire is often more durable and can be used to weld thicker materials more easily.
When it comes to welding position, TIG flux-cored welding is generally better suited for vertical and overhead welding, while MIG flux-cored welding is better suited for flat and horizontal welding positions. This is because the softer TIG flux-cored wire can be more prone to sagging and drooping when used in horizontal positions.
Finally, there is a difference in the level of skill required to perform TIG flux-cored welding versus MIG flux-cored welding. TIG welding is generally considered to be more difficult and requires more skill and experience, while MIG welding can be learned more quickly and is often used in less demanding applications.
How to Perform TIG Welding Without Gas?
TIG welding without gas is a method that uses a low voltage power source and high frequency current. The process can be used to weld thin metal sheets as well as thick steel and stainless steel.
The process involves using an alternating current (AC) source, which takes the form of an electric arc between two electrodes placed in direct contact with each other. This means that you will need to purchase special equipment for this type of welding method, such as an oscillating spool welder or “spider.”
General Tips For TIG Welding Without Gas
- TIG welding is a good choice if you want to do more than just stick welding.
- TIG welders are used in the aerospace industry and other industries that require complex joints or fragile materials.
- If you’re interested in learning about TIG welding, this could be an excellent way for you to get started on your journey towards becoming an expert in the field.
Advantages and Disadvantages of TIG Welding Without Gas:
As with most things there are a number of advantages and disadvantages that need to be weighed up when considering TIG welding without gas.
Advantages TIG Flux-Cored Welding
To be honest there probably aren’t very many other than it can be done with extreme skill and if you have no other realistic options. However in theory:
- TIG welding without gas is more affordable than traditional TIG welding methods that use a shielding gas setup, making it a cost-effective solution.
- It can be used in environments where using a shielding gas is difficult or impractical, such as in outdoor or windy conditions.
Disadvantages of TIG Welding Without Gas
- One of the biggest disadvantages of TIG welding without gas is that it is not as strong as a typical weld. When you are using this method, your welds will be weaker and more susceptible to breakage.
- The second disadvantage is that the tungsten will burn away rapidly as will become contaminated by oxides or other impurities. In essence, the process is not suitable for long welds.
- Another disadvantage is that it takes longer to complete a weld because you have to hold your torch steady for longer periods of time than if you were using gas in order to get an even bead on both sides of your joint. This means it is also more difficult to maintain a stable and can lead to a lower-quality weld, as well as potentially damaging the tungsten electrode.
- This can cause problems when working with large pieces of metal or difficult-to-weld areas, such as corners where the metal may not fit perfectly together due to unevenness caused by imperfections in either part being joined together (such as rust).
What to Expect When Using a TIG Welder Without Gas
- You will need to replace the electrode regularly.
- You might need to use a smaller diameter tungsten.
- Flux cored welding rods rather than wire will be better for your TIG welder without gas.
You will also have less control and therefore, more difficulty in welding with it. The weld bead may be larger than usual as well because of this lack of control over the arc during welding without gas.
Summary – TIG Welding Without Gas
TIG welding without gas is not a particularly common method for welding without gas. Although possible, it needs a high skill level and probably is only good over short welds.
There are further drawbacks too such as the burning of the burning through of the tungsten electrodes. This will happen at all temperatures but will be accelerated with higher temperature applications.
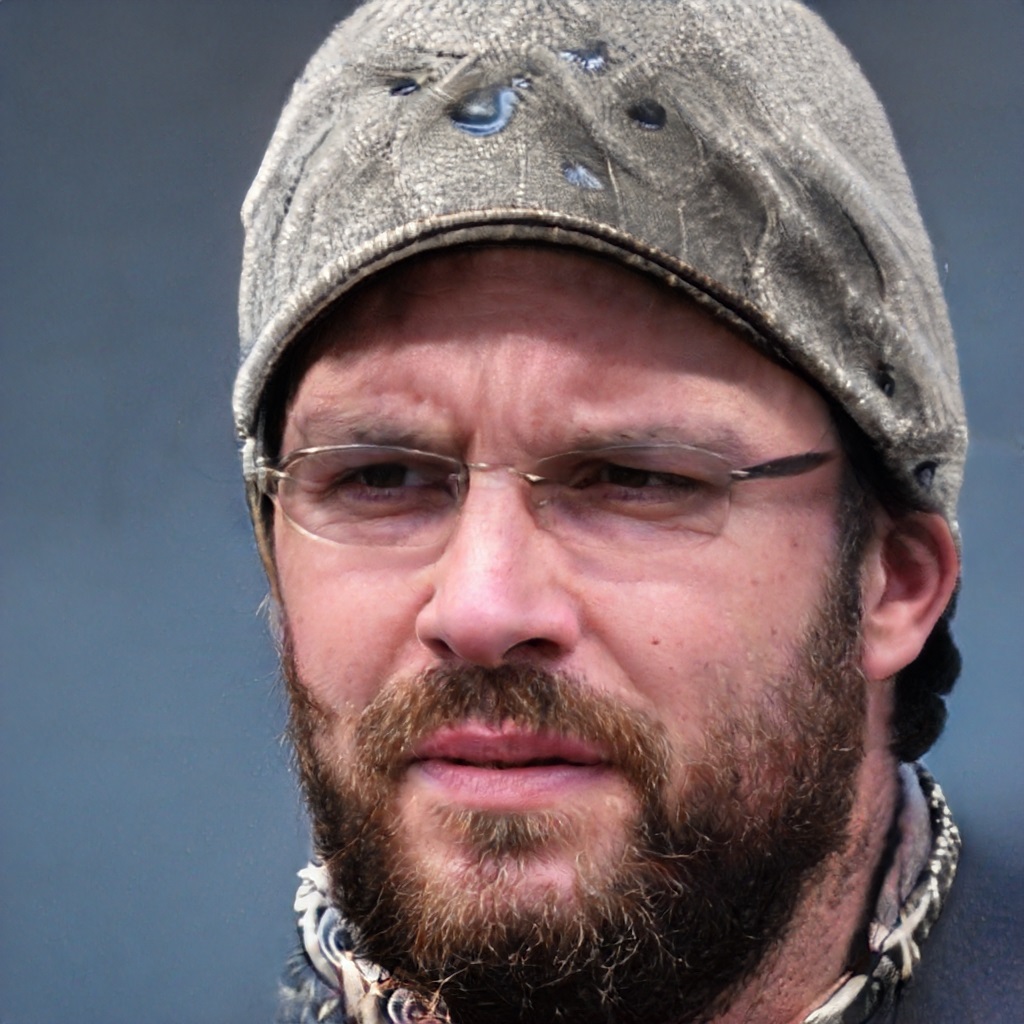
I’ve been involved in the welding industry for over twenty years. I trained in various engineering shops working on various projects from small fabrication and repairs through to industrial projects.I specialize in welding aluminum and food grade stainless steel and an now run an engineering shop fabricating equipment for the food industry.