Guide to the Properties and Uses Properties and Uses 030 Flux Core Wire
americanindustrialsupl and its partners may earn a commission if you purchase a product through one of our links.
Flux core welding is a popular welding method, and the properties and uses 030 flux core wire makes it common choice. The wire is self-shielded, meaning it does not require an external shielding gas, making it ideal for outdoor welding or use on rusty, dirty, or painted materials. Flux core wire has a flux material inside it, which helps to protect the weld from contamination and create a strong bond between the metals.
The wire can be used for different types of welding, such as self-shielded (gasless) or gas-shielded welding. Self-shielded flux core wire does not need additional gas, while gas-shielded flux core wire requires a shielding gas such as carbon dioxide or argon to enhance the weld quality and appearance. Gas-shielded flux core wire is more commonly used in industrial applications, while self-shielded flux core wire is more prevalent among smaller workshops, outdoor applications, and home use.
Below, we will focus specifically on 030 flux core wire, one of the most common flux core wire sizes. We will discuss the properties and uses of 030 flux core wire for mild steel, stainless steel, and other popular materials for welding and how to choose the best flux core wire for the job.
030 Flux Core Wire
Materials used in 030 flux core wire
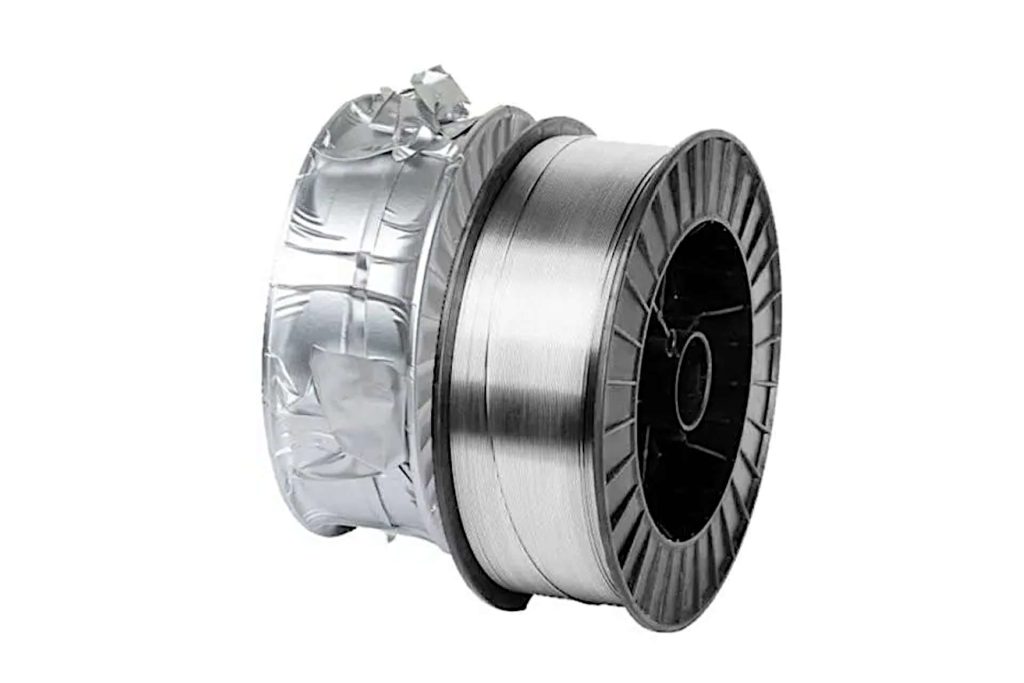
Mild steel
Mild steel is a type of carbon steel that contains a low level of carbon, usually between 0.05% and 0.25%, which makes it malleable, ductile, and easy to work with. Mild steel also has a high tensile strength, which means it can withstand much force without breaking. Mild steel is also relatively inexpensive and widely available, making it a cost-effective choice for many welding projects.
Mild steel is the primary material used in 030 flux core wire. The wire is made of mild steel strands coated with a thin layer of copper to improve conductivity and prevent rusting. The flux inside the wire is generally made of various chemicals, such as potassium, sodium, calcium, or manganese, that react with oxygen and carbon dioxide in the air to form a protective slag layer over the weld.
Mild steel flux core wire suits various welding tasks, including general fabrication, automotive repairs, and structural applications. Flux core can be used to weld galvanized steel to itself or other metals, such as cast iron or low alloy steel. The added advantage is that this variety of flux core wire can also be used in different positions, such as flat, horizontal, vertical, or overhead.
Stainless steel
Stainless steel is another type of alloy steel that contains at least 10.5% chromium, usually along with nickel and other elements. Chromium is the crucial element that gives stainless steel its corrosion resistance, as it forms a thin, passive film of chromium oxide on the surface of the metal that protects it from rusting. Stainless steel also has high strength, durability, and aesthetic appeal.
Stainless steel is another common material used in 030 flux core wire. In this case, the wire is made of stainless steel strands and, similarly to the mild steel variety, is coated with copper for conductivity and corrosion resistance. Again the flux inside the wire is usually made of chromium or nickel compounds that enhance the corrosion resistance and strength of the weld.
Stainless steel flux core wire is advantageous for specific applications where corrosion resistance, high strength, or aesthetic appeal are important factors. For example, stainless steel flux core wire can be used to weld food processing equipment, marine structures, or architectural projects that require a clean and shiny appearance. Stainless steel flux core wire can also withstand high temperatures and harsh environments better than mild steel flux core wire.
Possible Disadvantages of Stainless Steel Flux Core Wire
There are some disadvantages to using stainless steel flux core wire, and these include:
- Higher cost compared to mild steel flux core wire due to more alloying elements and additional processing
- More spatter and slag production, affecting weld quality and appearance if not properly removed
- Increased distortion and warping of the base metal due to higher thermal expansion coefficient, requiring proper clamping and cooling techniques to prevent these issues
Aluminum
One of the widest held misconceptions in welding is the notion that you can use flux core welding method to weld aluminum. The reason that you can’t use the flux core welding method is down to the properties off aluminum.
Aluminum has a high thermal conductivity, meaning it transfers heat quickly. This makes it hard to maintain a stable arc and consistent temperature with flux core wire. This can result in poor weld quality and porosity, which are tiny holes that form in the weld due to trapped gas or contaminants. These holes can weaken the weld and affect its appearance. Additionally, flux core wire can introduce unwanted elements like hydrogen into the weld pool, causing cracking and embrittlement in aluminum.
As such their is therefore no flux core wire available for welding aluminum elements, and you should ignore advice to the contrary.
Welding dissimilar metals
Welding dissimilar metals is a challenging task that requires careful selection of the filler metal and the welding parameters. Dissimilar metals have different physical and chemical properties, such as melting points, thermal expansion rates, and metallurgical compatibility. These differences can cause problems during and after welding, such as cracking, distortion, corrosion, or loss of strength.
One way to overcome these problems is to use flux core wire that is specially designed for joining different types of metals together. Flux core wire has a hollow core filled with flux, which is a substance that helps create the arc and protect the weld from contaminants. Some flux core wires also have alloying elements in the core or in the sheath that modify the chemical composition of the filler metal to match the base metals.
For example, if you want to weld stainless steel to carbon steel, you can use a flux core wire with a stainless steel sheath and a carbon steel core. This way, the filler metal will have a balanced mixture of both metals, improving the weldability and the mechanical properties of the joint.
Some examples of dissimilar metal combinations that can be welded with flux core wire are:
- Stainless steel to carbon steel
- Carbon steel to cast iron
- Copper to steel
- Nickel to steel
When welding dissimilar metals with flux core wire, preparing the joint properly and selecting the appropriate welding parameters is essential. The joint should be clean and free of dirt, oil, or rust. The gap between the base metals should be as small as possible to reduce the filler metal needed. The welding parameters, such as voltage, amperage, wire feed speed, and travel speed, should be adjusted according to the thickness and type of the base metals and the desired penetration and bead shape.
Properties and uses of 030 flux core wire for alloyed materials
Alloyed materials are metals that contain other elements, such as nickel, copper, or chromium, to enhance their properties. Alloyed materials are used for applications requiring high strength, corrosion resistance, or electrical conductivity.
Other alloyed materials
Besides carbon and low-alloy steels, flux core wire can also be used to weld other alloyed materials, such as nickel alloys or copper alloys. These materials have specific applications, such as high-temperature environments or electrical conductivity requirements.
For example, nickel alloys are used for power generation, chemical processing, or aerospace industries. They can withstand high temperatures and pressures, as well as resist corrosion and oxidation. To match the base metal composition, the flux core wire for nickel alloys contains nickel and other elements, such as chromium, molybdenum, or iron. The flux also contains deoxidizers and slag formers to ensure a smooth and clean weld.
Copper alloys, such as wires, cables, or heat exchangers, are used for electrical and thermal applications. They have high electrical conductivity and thermal conductivity, as well as good ductility and corrosion resistance. Flux core wire for copper alloys contains copper and other elements, such as tin, zinc, or silicon, to match the base metal composition. The flux also contains deoxidizers and fluxing agents to prevent oxidation and porosity in the weld.
030 Flux Core Wire
Benefits of using 030 flux core wire for alloyed materials
Using 030 flux core wire for alloyed materials has some unique benefits, such as:
- High deposition rates: Flux core wire can deposit more metal per unit time than solid wire, which increases productivity and reduces welding time.
- Out-of-position welding: Flux core wire can be used for all-position welding, which means it can weld in flat, horizontal, vertical, or overhead positions. This is because the flux creates a slag that supports the molten metal and prevents it from sagging or falling.
- Low spatter: Flux core wire produces less spatter than solid wire, which means less post-weld cleaning and less material waste.
- Hydrogen control: Flux core wire can control the amount of hydrogen in the weld metal using different fluxes. Hydrogen can cause cracking or embrittlement in some alloyed materials, especially high-strength steel. The risk of hydrogen-induced cracking can be reduced by using low-hydrogen fluxes, such as basic or metal-cored fluxes.
It is clear that using 030 flux core wire for different types of alloyed materials can have considerable advantages over solid wire, such as high deposition rates, out-of-position welding capability, low spatter, and hydrogen control.
You can achieve high-quality welds with excellent mechanical properties and corrosion resistance by choosing the correct flux core wire for the base metal composition and application requirements.
Setting the right Amperage for 030 flux core wire:
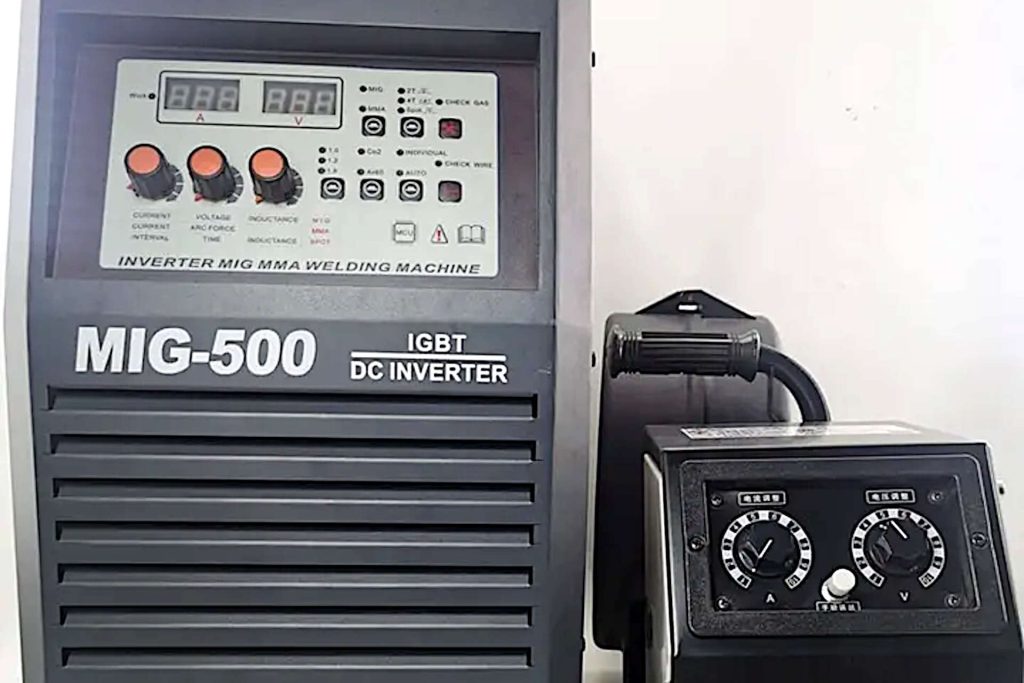
Setting the correct amperage is crucial for achieving optimal welding results with 030 flux core wire. Several factors affect amperage, and using the proper amperage for flux core welding is crucial to achieving the best weld.
Amperage
Amperage is the measure of electric current that flows through the welding circuit. It determines the heat input and the penetration depth of the weld. Too much or too little amperage can cause various welding defects, such as incomplete fusion, excessive spatter, or overheating of the base metal.
Recommended amperage range
The approximate welding range for 030 flux core wire is 50 to 175 Amp, depending on the material thickness and joint configuration. For example, if you are welding a flat 1/4 inch plate with a butt joint, you can use an amperage of 180 to 200 Amp. However, if you are welding a vertical 3/8 inch plate with a fillet joint, you should use 110 to 140 Amp amperage.
The best way to find the optimal amperage for your welding project is to perform a test weld on a scrap piece of metal with the same thickness and joint design as your workpiece. You can adjust the amperage until you get a smooth, consistent weld bead with good fusion and penetration.
Factors that affect amperage
Various factors influence the required amperage for flux core welding, such as:
- Wire diameter: The thicker the wire, the higher the amperage needed. For example, 035 flux core wire requires an amperage of 75 to 200 Amp, while 045 flux core wire requires an amperage of 170 to 290 Amp.
- Base metal thickness: The thicker the base metal, the higher the amperage needed. For example, if you are welding a 1/16 inch sheet metal, you can use an amperage of 50 to 90 Amp, while if you are welding a 1/2 inch plate, you need an amperage of 210 to 300 Amp.
- Joint design: The type and size of the joint also affect the required amperage. For example, a butt joint requires more amperage than a lap joint, and a large fillet joint requires more amperage than a small fillet joint.
- Welding technique: How you manipulate the welding gun also affects the amperage. For example, if you use a long arc length or a fast travel speed, you need more amperage than if you use a short arc length or a slow travel speed.
You should adjust the amperage based on these factors to achieve optimal welding results. You can use a flux core welding calculator to help you determine the appropriate wire size and voltage settings for your welding project.
Importance of Using the Correct Amperage
Using the correct amperage settings is essential for preventing issues like:
- Incomplete fusion occurs when the weld metal does not bond properly with the base metal, creating gaps or voids in the weld joint. The strength and integrity of the weld can be compromised in this situation.
- Incomplete fusion can be caused by insufficient amperage or poor joint preparation.
- Excessive spatter occurs when molten metal droplets are ejected from the weld pool and stick to the surrounding area. As a result, it can create a messy appearance and waste material. Excessive spatter can be caused by excessive amperage or improper voltage settings.
- Overheating of the base metal occurs when too much heat is applied to the base metal, causing it to warp or crack. One consequence is its effect on the dimensional accuracy and durability of the workpiece. Overheating of the base metal can be caused by excessive amperage or prolonged arc time.
Using the proper amperage settings ensures good fusion, proper penetration, and minimized heat distortion of your welds.
Practical Advice
030 flux core wire is a versatile welding wire that can be used for various applications. As we have seen, you should actively consider factors such as wire diameter, base metal thickness, joint design, and welding technique when adjusting your amperage settings.
You should also perform a test weld on a scrap piece of metal to find the optimal amperage for your welding project. Using the proper amperage settings can prevent issues like incomplete fusion, excessive spatter, or overheating of the base metal.
Differences Between Various Manufacturers’ 030 Flux Core Wire
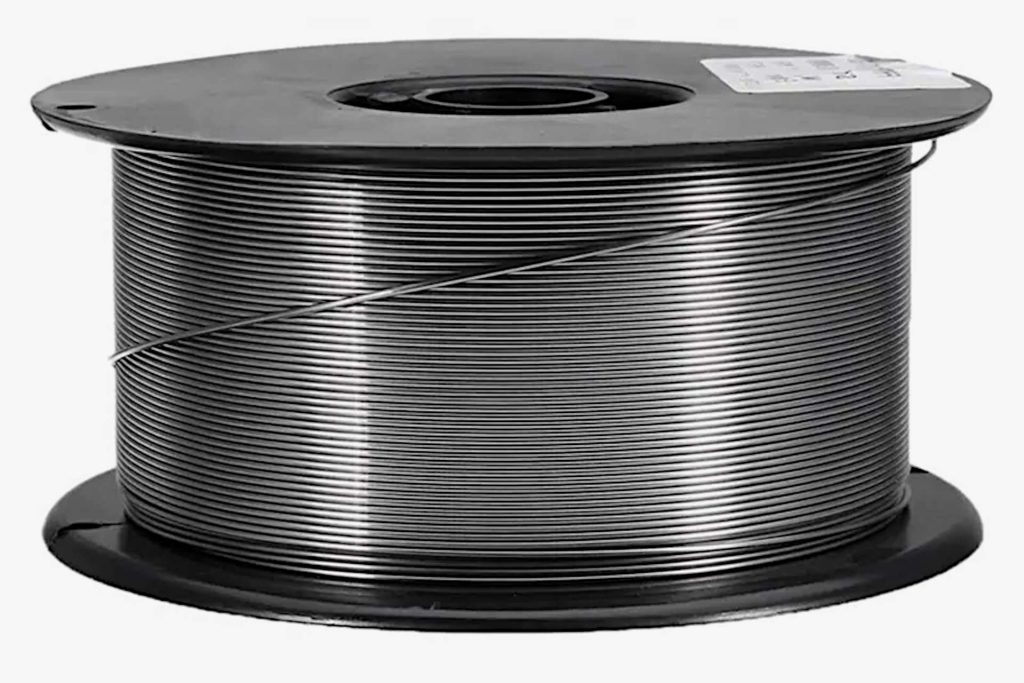
Despite all the advice above, you will find different manufacturers’ wires can perform very differently when used in the heat of use, and it is essential to understand the problems and befits that this can sometimes throw up.
Comparison of differences between various manufacturers’ 030 flux core wire
Many brands of 030 flux core wire are available in the market, each with its own features, specifications, and reputation. Some of the most popular ones are:
- Lincoln Electric Innershield NR-211-MP: The Lincoln Electric Innershield NR-211-MP wire is designed for all-position welding and has a smooth arc action, low spatter, and good slag removal. It can weld up to 5/16 inch thick steel in a single pass and has a wide voltage range. It comes in 1 lb., 2 lb., 10 lb., and 25 lb. spools and can be used with any DC+ MIG welder.
- Hobart H222106-R19: The Hobart H222106-R19 wire is also suitable for all-position welding and has a high tensile strength of 70,000 psi. It can weld 18 gauge to 3/16 inch thick steel with a low spatter level. It comes in 2 lb. spools and can be used with any DC+ MIG welder.
- Blue Demon E71TGS: The Blue Demon E71TGS wire is designed for single-pass welding and has a smooth arc transfer, low smoke, and full slag coverage. It can weld 16 gauge to 3/8 inch thick steel and has a high deposition rate. It comes in 2 lb., 10 lb., and 33 lb. spools and can be used with any DC+ MIG welder.
- Forney 42300: The Forney 42300 wire is an all-position flux core wire for mild steel that works well on rusty, dirty, and painted materials. It has a high feedability and produces quality welds with the minimal post-weld cleanup. It comes in 2 lb. spools and can be used with any DC+ MIG welder.
Advantages and disadvantages of each brand
Each brand of 030 flux core wire has its strengths and weaknesses, depending on the user’s application, preference, and budget. Here are some of the pros and cons of each brand:
- Lincoln Electric Innershield NR-211-MP: This wire is versatile, easy to use, and reliable. It produces consistent welds with good penetration and appearance. It is also widely available and affordable. However, some users may find it too soft or brittle, prone to breaking or tangling during feeding. It may also produce more slag than other wires.
- Hobart H222106-R19: This wire is strong, durable, and smooth. It produces clean welds with minimal spatter and distortion. It is also compatible with most MIG welders and has a good shelf life. However, some users may find it too stiff or hard, difficult to feed or bend during welding. It may also require more heat than other wires to achieve proper fusion.
- Blue Demon E71TGS: This wire is fast, efficient, and economical. It produces high-quality welds with excellent slag removal and bead appearance. It is also easy to store and transport due to its lightweight spools. However, some users may find it too thin or fine, prone to burning through or popping during welding. It may also have less consistency than other wires in terms of diameter or quality.
- Forney 42300: This wire is flexible, adaptable, and forgiving. It produces decent welds with good adhesion and corrosion resistance on various materials. It is also suitable for outdoor windy conditions due to its self-shielding properties. However, some users may find it too dirty or smoky, producing excessive spatter or slag during welding. It may also have lower strength than other wires in terms of tensile or impact resistance.
Properties and uses of 030 flux core wire: Welding Positions
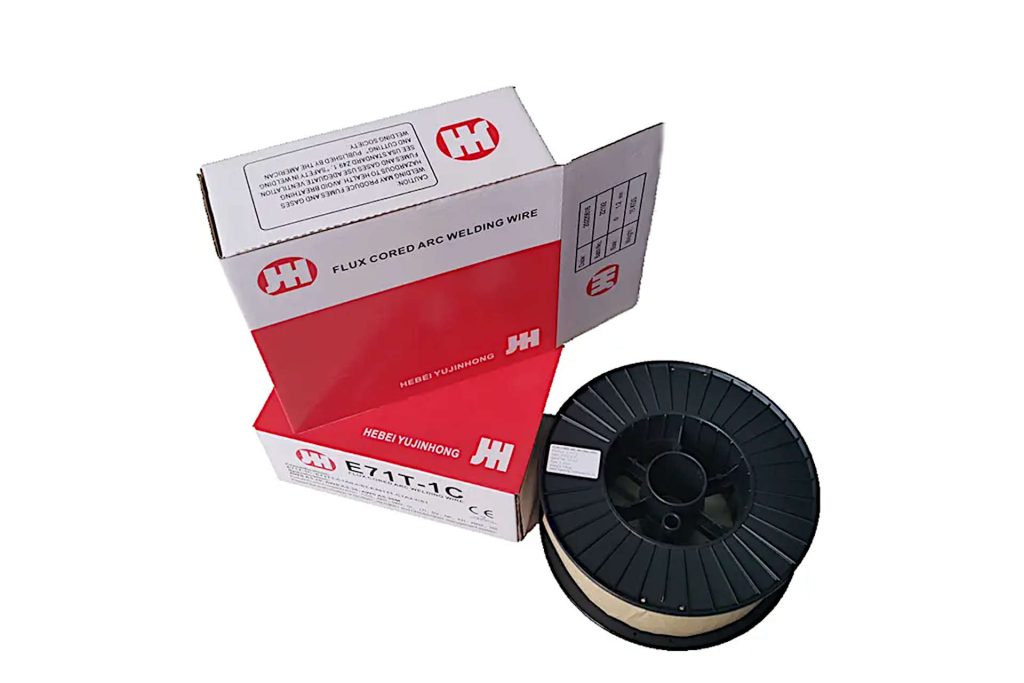
As 030 flux core wire is a type of welding wire that does not necessarily require an external shielding gas to protect the weld from contamination, it makes it highly flexible for use in various scenarios and different positions and environments, especially outdoors or in windy conditions.
All-position welding
All-position welding means that you can weld in any direction or angle, such as horizontal, vertical, flat, or overhead. This gives you more flexibility and productivity in different welding scenarios, such as repairing pipes, tanks, or structures.
030 flux core wire is designed for all-position welding because it has a fast-freezing slag that supports the weld puddle and prevents it from sagging or dropping. It also has a smooth arc transfer and low spatter that make it easy to control and manipulate.
To weld in all positions with 030 flux core wire, you need to adjust your torch angle and travel speed according to the position. For example, when welding horizontally, you should hold the torch at a 10-15 degree angle from the vertical and move it steadily from left to right. When welding vertically, you should keep the torch at a 5-10 degree angle from the horizontal and move it upward or downward, depending on the joint type.
Flat position welding
Flat position welding means that you are joining two flat pieces of metal that are parallel to the ground. This is the easiest and most common position for welding because it offers the most stability and visibility.
030 flux core wire is suitable for flat position welding because it has a high deposition rate and penetration that allow you to fill the joint quickly and efficiently. It also has a low tendency to undercut or burn through the base metal, which can cause defects and weaken the weld.
To weld in the flat position with 030 flux core wire, you need to maintain a consistent torch angle and travel speed throughout the weld. You should hold the torch at a 15-20 degree angle from the vertical and move it along the joint at a moderate speed. You should also avoid weaving or oscillating the torch too much, as this can cause excessive spatter and slag.
Vertical position welding
Vertical position welding means that you are joining two pieces of metal that are perpendicular to the ground. This is a more challenging position for welding because it requires more skill and technique to prevent gravity from affecting the weld.
030 flux core wire is capable of vertical position welding because it has a fast-freezing slag that supports the weld puddle and prevents it from falling or dripping. It also has a stable arc that can overcome the downward pull of gravity and create a uniform weld bead.
To weld in the vertical position with 030 flux core wire, you need to consider some factors such as joint type, direction of travel, torch angle, and travel speed. For example, when welding a vertical groove joint, you should start from the bottom and move upward (uphill) to create a narrower and stronger weld.
When welding a vertical fillet joint, you should start from the top and move downward (downhill) to create a wider and smoother weld. You should also hold the torch at a 5-10 degree angle from the horizontal and move it slowly along the joint.
Overhead position welding
Overhead position welding means that you are joining two pieces of metal that are above your head. Overhead is the most difficult position for welding because it poses more risks and challenges, such as spatter, slag, heat, and visibility.
030 flux core wire can perform overhead position welding because it has a fast-freezing slag that supports the weld puddle and prevents it from dropping on your face or body. It also has a low heat input that reduces distortion and warping of the base metal.
To weld in the overhead position with 030 flux core wire, you should use lower amperage (such as 90-120 amps) to reduce spatter and heat. You should hold the torch from the vertical at a 5-10 degree angle and move it quickly along the joint.
030 Flux Core Wire
Videos
References
- IOP Conference Series: Materials Science and Engineering: Influence of The Wire Diameter and Particle Fraction of Fe-Al2 O3/zr O2 Flux-Cored Wires Processed by Wire Arc Spraying on The Abrasive Wear Properties of The Coating
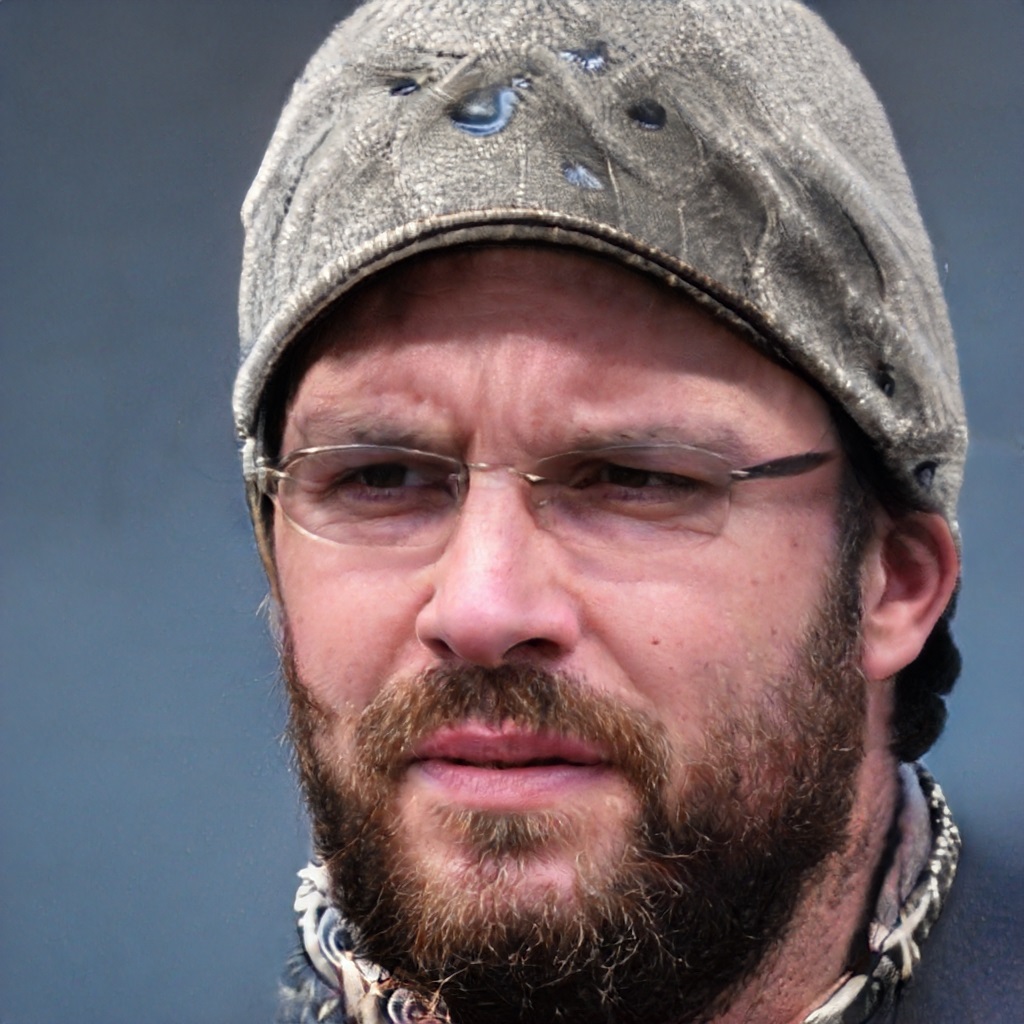
I’ve been involved in the welding industry for over twenty years. I trained in various engineering shops working on various projects from small fabrication and repairs through to industrial projects.I specialize in welding aluminum and food grade stainless steel and an now run an engineering shop fabricating equipment for the food industry.