What is the Right Shielding Gas for Welding Aluminum?
What is the Right Shielding Gas for Welding Aluminum? Controlling aluminium welds entails a variety of elements, including selecting the proper filler metal and shielding gas composition, as well as ensuring your power supply is properly set up to ensure quality welds as the end result.
Inert Shielding Gases
When deciding what is the right shielding gas for welding aluminum, we need first to consider the properties of the available gas options.
The two most commonly used inert (noble) shielding gases used to weld aluminum are Argon (Ar) and Helium (He). Argon or a combination of argon and helium are used to almost the exclusion of all other gases when welding using gas metal arc welding GMAW (MIG), or gas tungsten arc welding GTAW (TIG), processes. These processes are more commonly known as MIG and TIG.
The reason inert gases are used is because the weld is unaffected by these gases since they are inactive. All of these things are designed to keep the weld from being contaminated by oxygen and water.
Argon
Argon shielding gas is commonly employed in numerous welding procedures. The argon welding gas protects the new weld from the surrounding environment since it is a shielding gas. The welds are more smooth and long-lasting as a result of this.
One of the principle properties of argon is the absence of any interaction between argon and other elements. The inert gas serves a tremendous benefit in protecting the environment when welding.
Argon is delivered right through the tip of the welder, enveloping the arc and so reducing the influence of moisture and other factors that otherwise may make the weld weak, uneven or form spores in it. Sometimes the gas ca be spread over the rear of the weld as well to better shield it from the surroundings. This is the rationale why is welding done in an argon environment. Argon gas is commonly utilised in TIG and MIG welding.
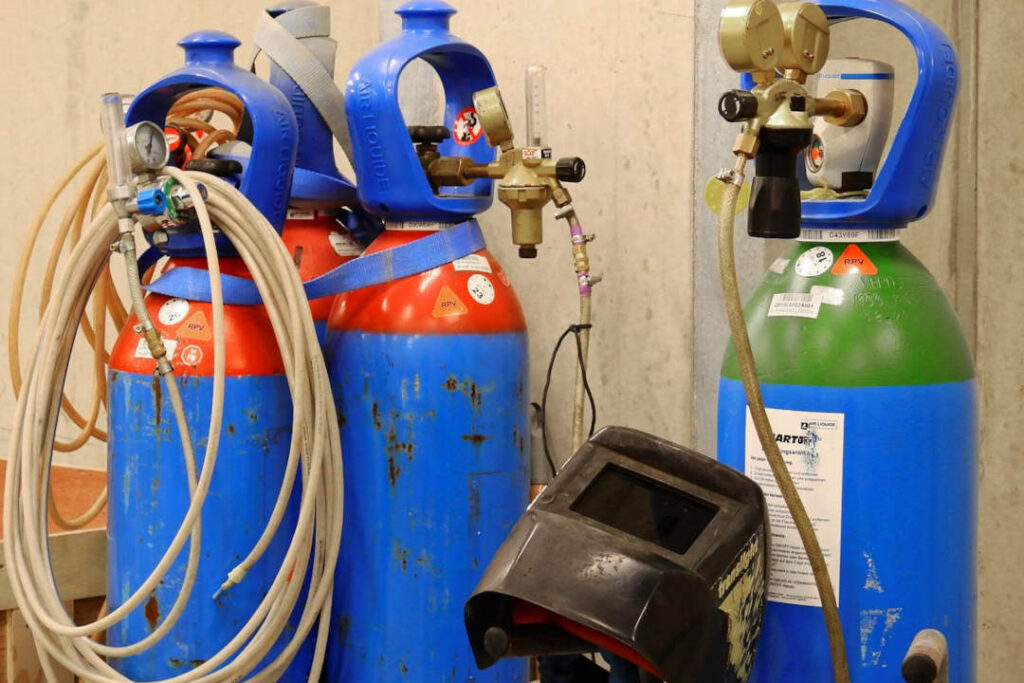
Helium
Helium Properties Helium is an inert gas, which means it doesn’t undergo any chemical changes when exposed to other chemicals. That feature is highly useful in the realm of welding shielding gases. The consistency of helium’s performance means that scientists can predict its effect on a wide range of welding tasks.
The gas displays strong thermal conductivity, that’s why it’s often employed for weld applications in which considerable heat input is required for increased wetting of the weld bead.
Helium normally is blended with variable quantities of argon in shielding gas mixes to take use of both gases’ favourable qualities. When welding, for example, using helium as a shielding gas may assist achieve a wider penetration pattern. However, it cannot offer the cleaning effect that argon can.
Don’t Use Oxygen or Carbon Dioxide
When discussing gases , it is important to note that you should never employ a shielding gas combination that combines Carbon Dioxide or Oxygen, although tempting because of improved productivity gained by increased travel speeds. Niether of these gases is inert and as such using them will almost certainly result in the oxidation of the Aluminum, a consequence you do not want for your weld.
What is the Right Shielding Gas for Welding Aluminum : MIG
Although, today, argon is the most often used shielding gas in aluminium production, there are two alternatives in gas metal arc welding (GMAW), or MIG as it is more commonly known as. Welders can either go with 100 per cent argon or an argon/helium blend.
Over recent years though, there has been a considerable degree of variation in the cost of helium. This is has been down to periodic scarcity of supply of the gas, possibly rendering it relatively expensive for various welding applications. Therefore, the trend has been that, if it isn’t needed in an application, 100 percent argon is favoured instead. Flow rates of 20 to 30 cubic feet per hour are advised.
However it is not always the case that it will not be needed. Using 100 per cent argon has a somewhat limited penetration pattern meaning that on relatively thick work-pieces argon/helium mixes provide better penetration On the other hand a larger arc frosting/etching zone is created when using an argon helium mix.
Many welding shops have typically employed argon/helium mixtures in their work methods. Helium may account for 25% to 75% of the gas mix in a helium/argon mixture for MIG. The welder may impact the distribution of heat to the weld and, as a result, the form of the weld metal cross – sectional area and the welding speed by modifying the makeup of the shielding gas mix. By increasing output frequency to 200 Hz or more a narrower frosted/etched zone is produced.
An example of a MIG set up would be to use spray transfer MIG to weld an aluminium utilising 1/16-inch-diameter material 5356 filler and 100 percent argon. The penetration achieved is essentially the consequence of the waveform of the machine.
How MIG Welding Gas Effects Arc Transfer Type
The weld transfer type is also affected by shielding gas options. The following are the most fundamental gas-related transfer types:
Only pure Carbon Dioxide or a high proportion of Carbon Dioxide may be used for short-circuit transmission, although you wouldn’t use this if welding aluminum.
More than 75% Argon is required for a successful transfer.
Argon spray transfer may range from 75% to 100% for metals like aluminium, depending on the kind of substance.
MIG: Push or Pull Welding Direction
When MIG welding aluminium, the forehand push direction should always be employed. Because by using the push direction it ensures that the shielding gas completely covers the weld pool, which is not always the case when pulling.
Pushing provides deeper penetration and a narrower bead, while pushing creates a flattened, broader bead with a shallower depth.
Filler Wire Aluminium Welding
Anther important are when MIG welding aluminum is the choice of the filler wire and how this can directly affect which you use. The most common filler wire used are the 4XXX and 5XXX series.
Despite the fact that the 5xxx series filler wire is more vulnerable to lack of fusion than the 4XXX series wires, the 5XXX filler metals are the type that is most widely employ for most structural applications due to their mechanical qualities. As a result, being able to establish a wider width of penetration aids in combating fusion issues. Some welding gas providers have created proprietary gas blend that provide welders with comparable qualities without the use of helium.
A smaller arc etching zone, a deeper penetration profile, and less smut when using high-magnesium alloys are some of the qualities advertised by firms with proprietary blends. These are all properties that you obtain by utilising helium in conjunction with argon. In the sense of the finished look, these are the types of features a welder working on polished aluminum is likely searching for. The issue then arises, whether the advantages of employing helium or a bespoke mix worth the higher gas cost?
The wire feed systems employed with “trim” or voltage control, which alters arc length, may modify the size of the frosted zone to some degree.
What is the Right Shielding Gas for Welding Aluminum : TIG
TIG welding uses a tungsten electrode to create the arc, which is carried by the welder. The other hand adds filler metal to the weld puddle (except when machine or robotic applications). TIG welding has a number of advantages, including more control over the welding process and a tendency to be very clean. TIG welding is directly comparable to gas or oxy-acetylene welding in terms of the process itself..
With TIG, the main gas used to weld aluminum is 100 per cert argon. Helium/argon blends may be utilised for applications that demand large thermal transfer, although such applications aren’t particularly prevalent.
A further advantage of using helium mix is that travel speeds may be increased with the use of gas mixtures, which are commonly 25 percent helium and 75 percent argon. This means that greater productivity can be achieved which may out-weigh the increase gas costs.
Porosity, a common problem in aluminium welding, may be combated by helium mixes. The maximum amount of hydrogen can be absorbed by molten aluminium. Helium mixes also have the ability to minimise any quantifiable porosity levels.
For many, the depth of penetration is just as important. This is because there are situations when a broader penetration profile aids the weld process, such as when operators are doing double-sided groove welds or fillet welds.
With TIG your power source setting is more important than the gas mix. TIG is an inverter-based welding process with changeable frequency output, enhanced balance control, and a separate amplitude control Often adjusting thee setting can result in increasing or decreasing the breadth of the frosting zone.
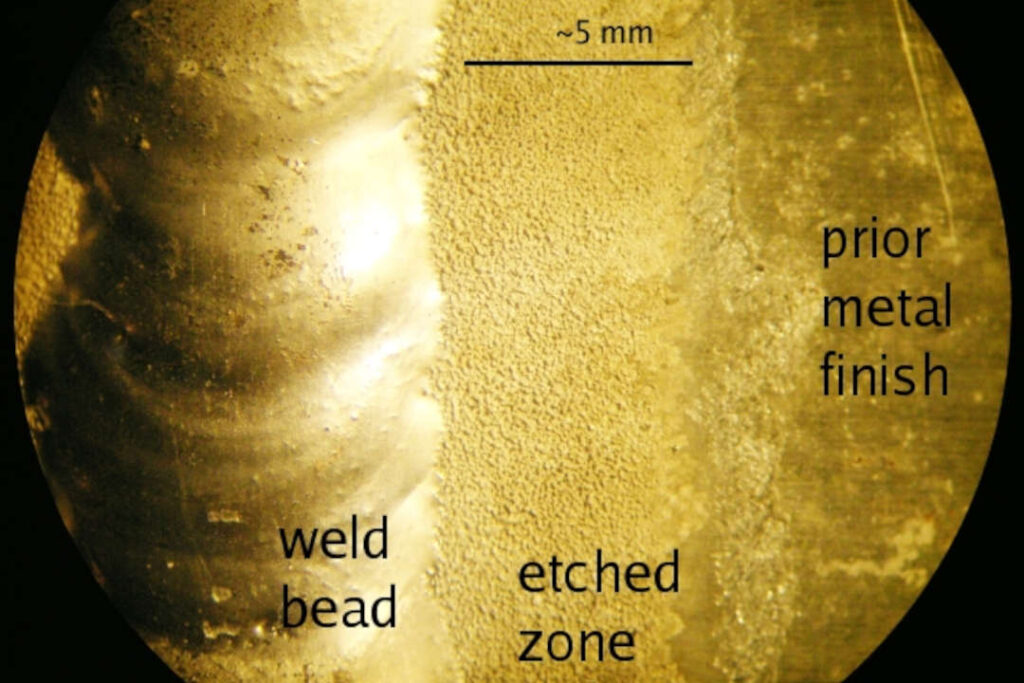
You may fine-tune the width of the arc coming off the tungsten on a TIG machine using frequency adjustment, which can reduce the arc etching zone. The frequency may reach 400 Hz depending on the equipment.
There isn’t nearly the same arc frosting zone control on the MIG side since it’s vital to maintain the voltage in a range that offers you the greatest feed and weld bead qualities, but it is still feasible to make a tighter arc by adjusting the voltage regulation.
The arc cone has less of a chance to spread out if you retain a tighter arc by altering the voltage levels. If you have a longer arc or a greater voltage, you will automatically have a larger arc cone. When you’ve reached the maximum or lower limits of your machine control, shielding gas mixtures may assist you create better welds. Some occupations just need them!
TIG: Push or Pull Welding Direction
When TIG welding aluminum, as with MIG, the push method is the preferred for TIG welding.
What is the Right Shielding Gas for Welding Aluminum? Additional Considerations
There are a number of other things to consider when considering what is the Right Shielding Gas for Welding Aluminum. These have to be balance with other welding considerations.
How thick is the metal you are welding?
If you’re looking to weld something extremely thin, you’ll want to lean toward TIG welding. MIG welding is less controlled so you’d typically want to use MIG welding for thicker metals.
The thicker the material the greater the penetration required which will impact on the gas and welding process choice.
Are you looking to achieve a finished appearance without grinding?
If your weld requires needs to be presentable without post-weld operations, you’ll need a welding technique that allows for a smoother weld and no spatter like TIG welding. When welding items are hidden or if the weld bead is allowed to be raised and somewhat rough then MIG welding will be perfectly adequate.
Do you need to produce liquid or gas tight welds?
It is difficult to produce leak-free welds with a MIG because the weld is cold briefly after the arc is struck before the metal starts to fuse. TIG is a better fit for gas or liquid-tight welds.
How much time do you have to finish the project?
If you’ve got a deadline to hit, your friend will be MIG welding as it can weld thick and thin metals and lays down filler metal much more quickly. MIG is typically the best choice for longer, continuous welds.
Welding Fume
A lot of welding fume (the white smoke that you see) is produced by aluminium alloys, compared to many other materials. In MIG, this is much more prevalent. When using TIG on aluminium, it is less noticeable. In MIG, metal is transferred across the arc, causing this. As a result of this, a significant amount of material is evaporating and forming the visible gas. In TIG, less material is vaporised since the filler wire does not become as hot.
Problems with Etching Zones
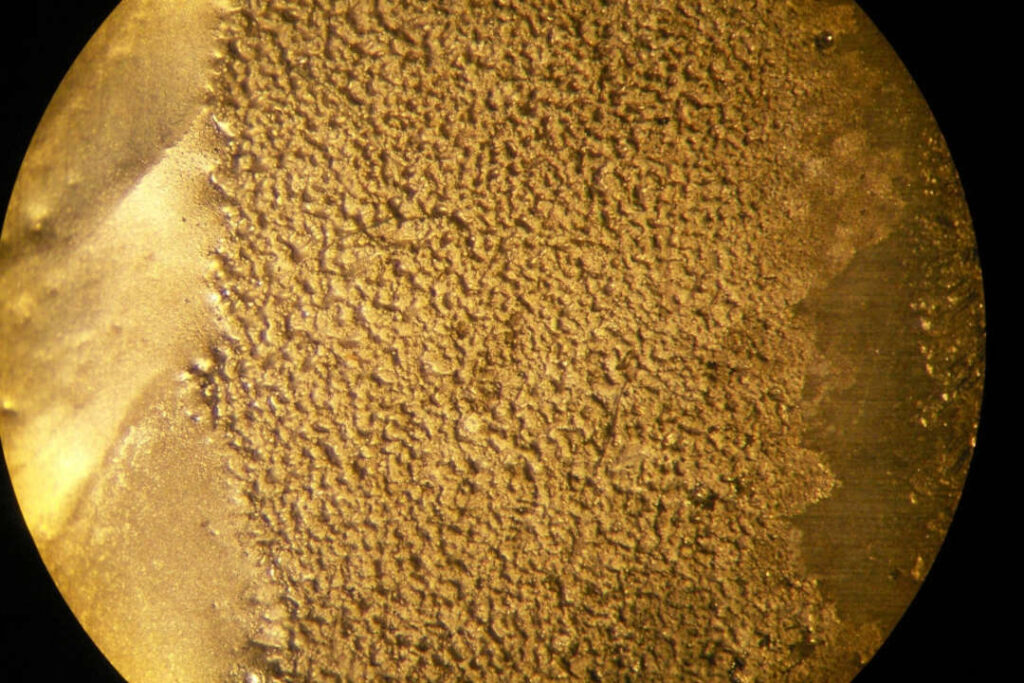
When using either aluminium MIG or TIG both processes entail the breaking up the aluminium oxide layer that natively develops on the metal to help in weld penetration. They appear to resemble frosted lines and are located near to the weld on both sides of the joint. They are termed arc etching zones.
For welders that seek for as little finishing work as possible after welding, this isn’t desirable, thus they often opt for a specialised shielding gas mix.
Etching zones, however, can also be mitigated with the correct machine management. The arc etching zone can be adjusted, to a certain degree, at the machine controls of current weld power sources.
Adjustable frequency output, extended balance control, and independent amplitude control on inverter-based welders may enable you alter the diameter of your TIG etch zone.
Summary: What is the Right Shielding Gas for Welding Aluminum
So, what is the Right Shielding Gas for Welding Aluminum? As we have discussed above it depends on numerous factors. The principle one though is the type of welding process to be used.
If using MIG you are likely to be using pure argon with flow rates of 20 to 30 cubic feet per hour. However you can also use an argon/helium blend if you require deeper penetration in the weld.
The advice is similar with TIG although you are more likely to be able to use a argon/helium blend as etching zone can be more easily controlled by manipulation of the power source.
The main problem with argon/helium blends is potential frosting which is much more of an issue with MIG.
The right shielding gas to use when welding mild steel or the correct shielding gas when welding stainless steel.
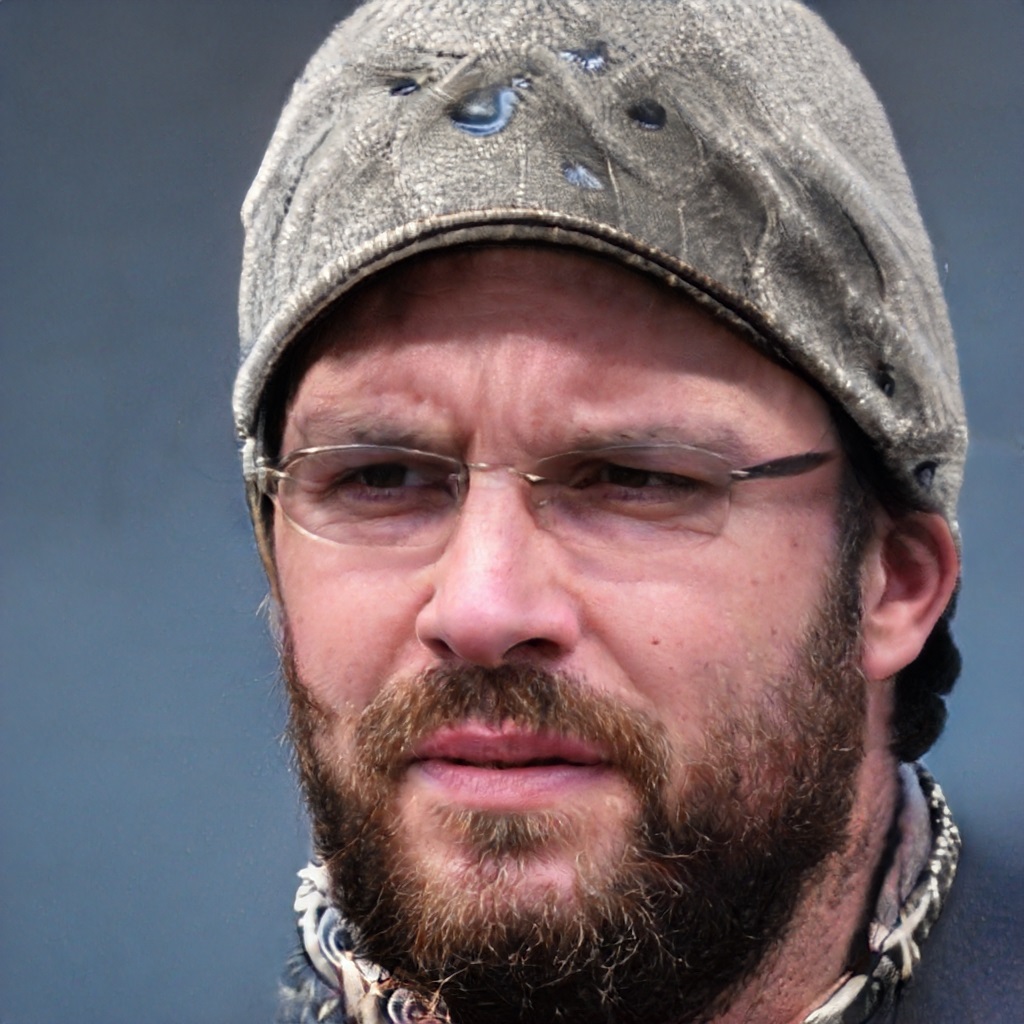
I’ve been involved in the welding industry for over twenty years. I trained in various engineering shops working on various projects from small fabrication and repairs through to industrial projects.I specialize in welding aluminum and food grade stainless steel and an now run an engineering shop fabricating equipment for the food industry.