Arc Machines New M217 Orbital Welder
Arc Machines (AMI). pioneers in the field of orbital welding have just released their newest orbital welding system, the M217. This welder follows on from their previous models, the M107 and M207 with the later and the M205 being deprecated.
This new workhorse is offered as a compact unit creating ease of portability for on-site applications while maintaining the functionality of the M217. The M217P replaces the M205.35% -smaller footprint and 27% lighter than the M217 -One-hand carry handle -10″ color touch-screen display -100% duty cycle, 5-150 amps -Manual or auto schedule generation, S³, Pulsed, Non-Pulsed, Step -Storage for 1000+ weld schedules and up to 99 levels per schedule plus Weld Data Recording -217P is designed to work with all AMI’s orbital fusion weld heads capable of welding tube
With a reputation for producing some of the most robust and reliable welder on the market, the M217 moves the bar higher with advances in the welding system controllers and the automated display interface on the machine. In addition further design improvements mean a much lighter welder yet, despite these advances and changes customers of previous models will immediately be familiar with the machine. As Arc Machines say:
Existing M205 customers will find that the enhanced 217P is 9% lighter; includes the advanced features of the M217, with a larger 10 inch touch screen and will retain the output connectors of the M205. Orders for the M217P weld system controller are being accepted now, with deliveries scheduled for mid-October 2016.
For those with the older M205 and M207 models Arc Machines are ending production of the M205 and M207 and you will only have up to the end of January 2017 to purchase new power supplies:
End of Sale for the M205 and M207 Power Supplies. As part of the evolution of our Fusion weld system controller product family, we will be ending the sale of the M205 and M207 power supplies. -M205 and M207 orders will be accepted until January 31, 2017. -Service, spare parts and consumables for the M205 and M207 power supplies, produced after 2016, will be supported through December 2026.
M217 Orbital Welder In Action
Long time partner and major customer of Arc Machines, Critical Systems Inc, have been putting the M217 WDR through its paces.
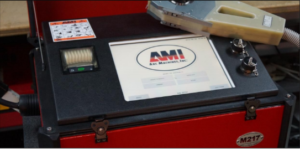
Hooking up the M217 is simple. Facility requirements are the same as the M207, except the fittings for the purge gas lines are compression style, instead of flared. The unit is switched on with its main breaker, in the same location as the M207. Power-up takes about 50 seconds, and displays the M217 home screen when complete (Figure 5). The look is all business, with buttons for the four main functions in the center. Navigating through the various screens and operations is very intuitive, and after some initial assistance from the owner’s manual, anyone experienced with the M207 will have no trouble operating the M217. One function worth mentioning here is the M217’s auto-generated recipe capability. The user enters four parameters (tube diam., wall thickness, tube material, and the model of weld head) and the M217 pulls all the remaining schedule specifics from an on-board library containing AMI’s best practices. Select the type of weld you want to perform from the four choices (Auto-pulsed, Auto-step, Auto-tack, and S³) and the M217 creates and loads the new recipe — a far cry from the labor intensive and error prone process of the M207. Should a user wish to customize specifics or fine tune a weld, simply touching the schedule field relating to a particular parameter brings up a menu, and allows on-the-fly editing.
Another clearly observable improvement over the M207 is in how smoothly the M217 runs the various weld head motors. During all CSI’s testing, rotor operation was quieter, smoother, and homing more accurate. The M217 also performs a two-step speed calibration that checks both the low and high speeds of the weld head. We suspected this would contribute to a more precise speed control. As a test, using auto-generated recipe times and the M217’s speed calibration, we ran a number of different cycles against a stop watch. All times were correct, as closely as could be visually confirmed. Operations are performed from the Weld screen. Individual displays provide constant feedback as the weld is occurring. Monitoring of the actual tungsten position as the rotor turns, the output current versus programmed current, weld step countdowns, purge pressure for both lines, and more, are all viewable in easy-to-read, real-time from this screen.
The next most obvious question is what are the quality of weld produced like. Although even poor welders failing can often be mitigated by a skilled welder, it is so much easier if the welder itself works well and can produce a quality weld. Arc Machines have a long standing reputation for making machines what work well in the field And here, according to Critical System’s report, the new M217 continues in this vain with fantastic bead uniformity and excellent penetration:
So how does the M217 weld? Using a variety of AMI heads, from the 9-500 to the 9-7500, as well as the 8-2000 and 8-4000, CSI made welds on SS tube diameters from 0.25” to 6.0”, and wall thickness’s from 0.035” to 0.120”. Using the M217’s autogenerated four level weld schedules, results were mostly excellent, with a few examples benefiting from small primary amp adjustments to the AMI library values. Bead uniformity, fish-scale, penetration, and color were as good as the best we had ever seen from a M207, and often better.
Another advanced feature examined during weld testing was the capability to perform Single Slope Single Pass (S³) welds. S³ welding is a more precise type of weld than the current industry standard four-level fusion welds. The four-level weld schedule lowers the weld current every 90º of rotation in an attempt to keep the heat in the work piece constant. But the heat buildup actually occurs in a linear fashion, not in steps, and can result in what is called the ‘Christmas tree effect’ as the weld bead narrows and widens. By reducing the weld current in a linear fashion designed to match the heat build-up, S³ welds should be extremely consistent from start to finish. Test coupons using this type of schedule on the M217 looked even better than the four level ones, and might easily become the industry standard as more organizations become familiar with this technique.
All in all it would appear tht Arc Machines have produced another excellent welder and have enhanced their reputation for bringing high quality welding systems on to the market at competitive prices.
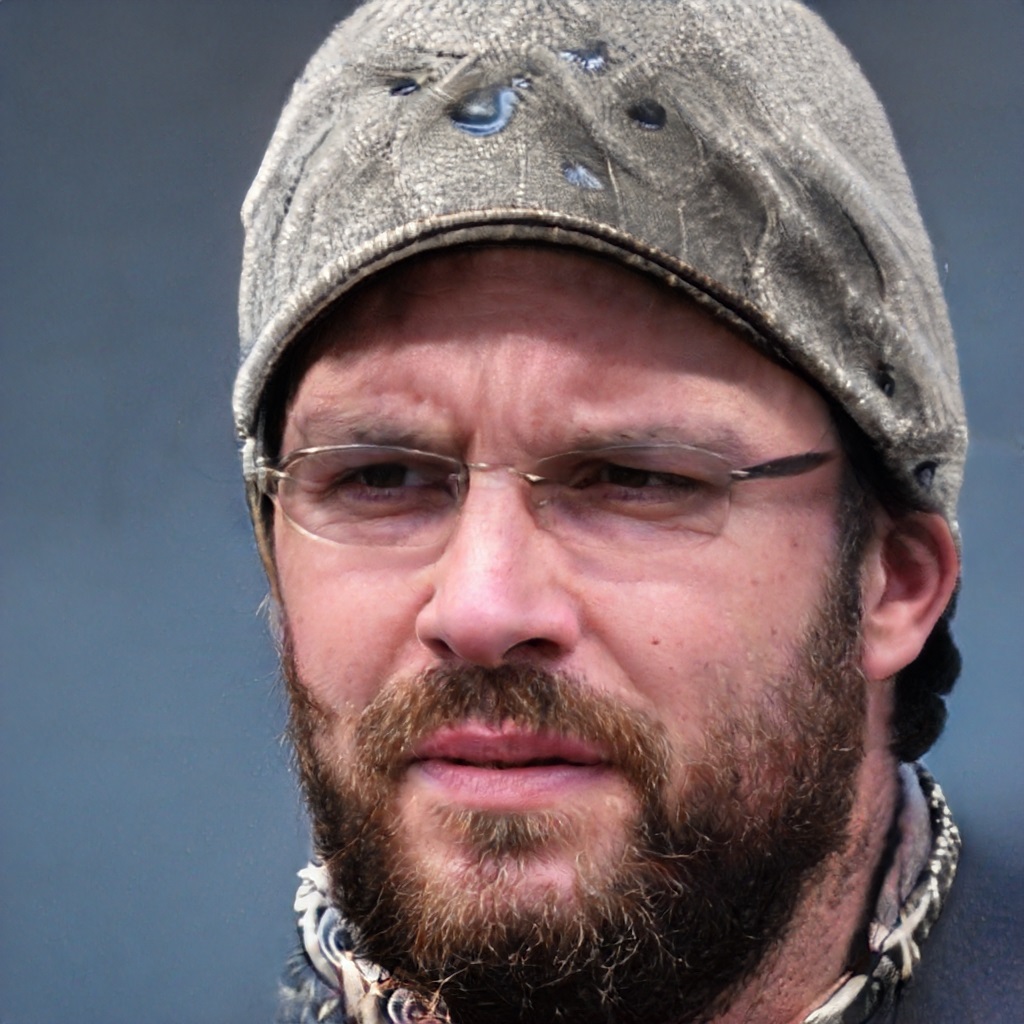
I’ve been involved in the welding industry for over twenty years. I trained in various engineering shops working on various projects from small fabrication and repairs through to industrial projects.I specialize in welding aluminum and food grade stainless steel and an now run an engineering shop fabricating equipment for the food industry.