Weld Galvanized Steel with Flux-Cored Wire
americanindustrialsupl and its partners may earn a commission if you purchase a product through one of our links.
Welding galvanized steel with flux core wire can be challenging especially if you are not familiar with the flux core method. Galvanized steel is coated with a layer of zinc that protects it from corrosion, but also creates problems when welding. The zinc can vaporize and form toxic fumes, which can cause health issues and damage the weld quality. The zinc can also interfere with the fusion of the base metal and the filler metal, resulting in weak and brittle welds.
Fortunately, there is a way to weld galvanized steel effectively and safely using flux-cored wire. Flux-cored wire is a type of welding wire that has a hollow core filled with flux, which is a substance that shields the weld from contaminants and helps the metal flow better. Flux-cored wire welding has several advantages over traditional welding procedures, such as using less heat, being easier to manage, and producing stronger and cleaner welds.
MIG Welders
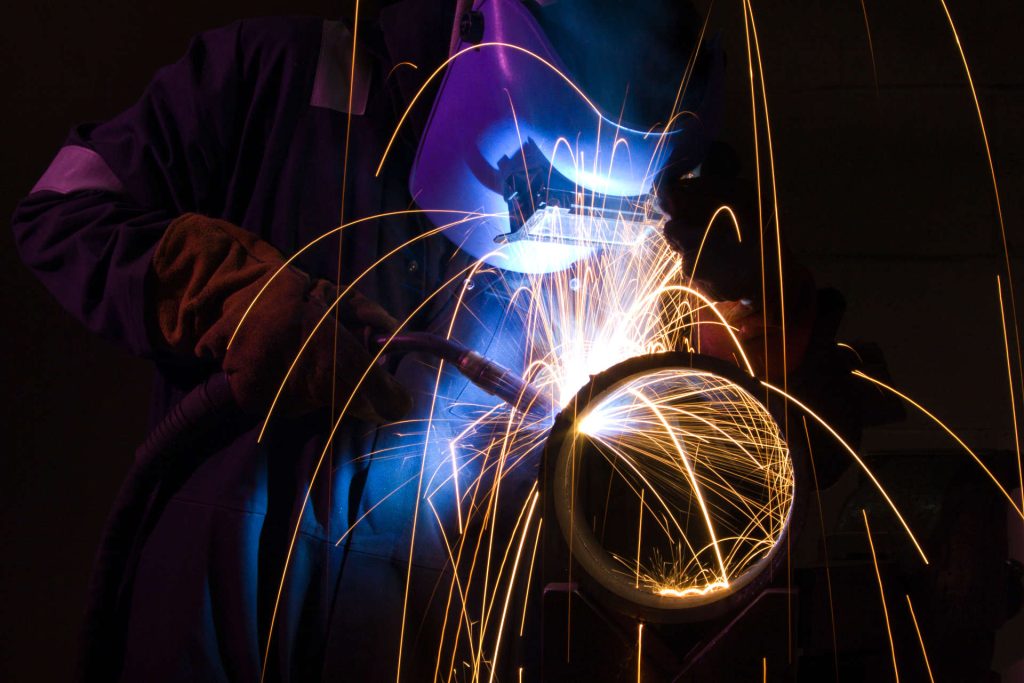
Below, we will look at how to weld galvanized steel with flux-cored wire, step by step and we will cover the following topics:
- The advantages of flux-cored wire welding over traditional welding procedures
- How to prepare galvanized steel for flux-cored wire welding
- How to set up your welder for flux-cored wire welding
- How to weld galvanized steel with flux-cored wire
- The safety precautions you should take when welding galvanized steel with flux-cored wire
By the end of this article, you will have a clear understanding of how to weld galvanized steel with flux-cored wire, and you will be able to apply this technique to your own projects.
Advantages of Flux-Cored Wire Welding Over Traditional Welding Procedures
Flux-cored wire welding is a versatile and efficient way of welding various metals, including galvanized steel. Here are some of the benefits of using flux-cored wire welding over traditional welding procedures:
Uses less heat:
Flux-cored wire welding uses less heat than other welding methods, such as stick or MIG welding. This means that there is less distortion and warping of the metal, and less risk of burning through thin or delicate parts. Less heat also means less zinc vaporization, which reduces the amount of toxic fumes and improves the weld quality.
Easier to manage:
Flux-cored wire welding is easier to manage than other welding methods, because you don’t need to use a separate gas cylinder or regulator. The flux in the wire provides the shielding gas for the weld, so you only need to feed the wire through your welder. This makes flux-cored wire welding more convenient and portable, as you don’t have to worry about running out of gas or carrying heavy equipment.
Produces stronger and cleaner welds:
Flux-cored wire welding produces stronger and cleaner welds than other welding methods, because the flux helps the metal flow better and prevents oxidation and contamination. The flux also forms a slag layer on top of the weld, which protects it from atmospheric exposure and can be easily chipped off after cooling. The result is a smooth and shiny weld that has good penetration and strength.
Preparing Galvanized Steel for Flux-Cored Wire Welding
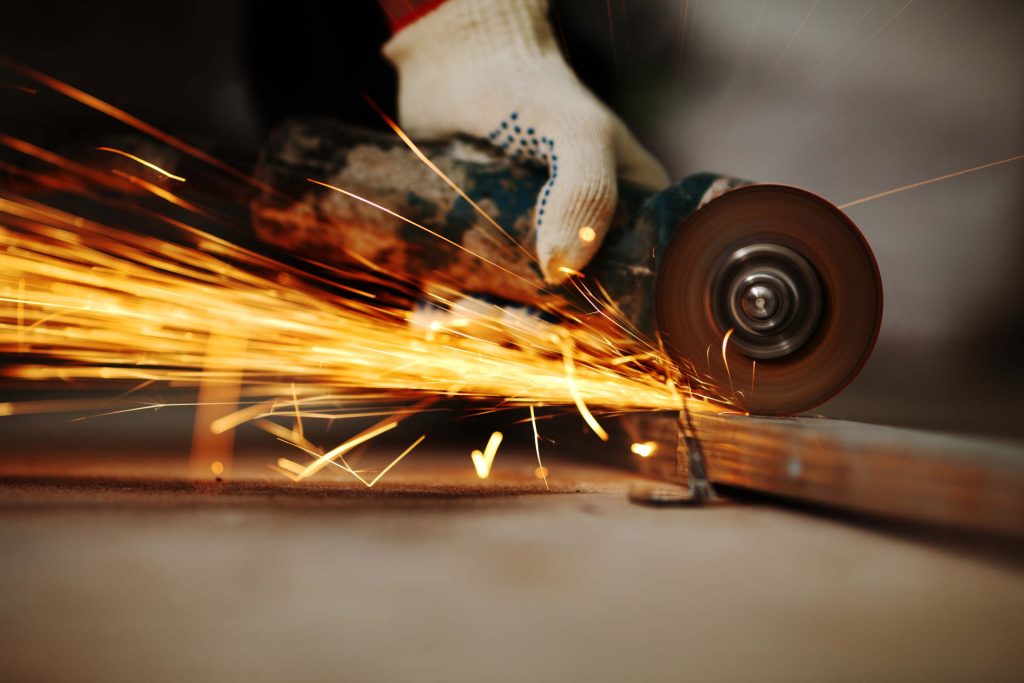
Before you start welding galvanized steel with flux-cored wire, you need to prepare the surface of the steel properly. This will ensure that you get a good weld that adheres well to the base metal and has no defects. Here are the steps you need to follow to prepare galvanized steel for flux-cored wire welding:
Cleaning the surface of the steel:
The first step is to clean the surface of the steel from any dirt, grease, oil, paint, or rust that might interfere with the welding process. You can use a wire brush, a grinder, or a sandpaper to remove any loose or flaky material from the surface. You should also wipe the surface with a solvent or a degreaser to remove any residue or moisture that might affect the weld quality.
Choosing the right flux-cored wire:
The next step is to choose the right flux-cored wire for galvanized steel. There are different types of flux-cored wires such as E71T-1C available on the market, each designed for specific applications and metals.
For galvanized steel, you should use a self-shielded flux-cored wire that has a high tensile strength and a low spatter rate. A self-shielded flux-cored wire does not require an external gas supply, as it generates its own shielding gas from the flux. This makes it ideal for outdoor or windy conditions, where gas-shielded wires might lose their effectiveness.
A high tensile strength means that the wire can withstand high stress and strain without breaking or cracking. A low spatter rate means that the wire produces less molten metal droplets that can fly off the weld and create a mess or a hazard. Some examples of self-shielded flux-cored wires that are suitable for galvanized steel are E71T-11, E71T-GS, and E71T-14.
Welding Galvanized Steel with Flux-Cored Wire
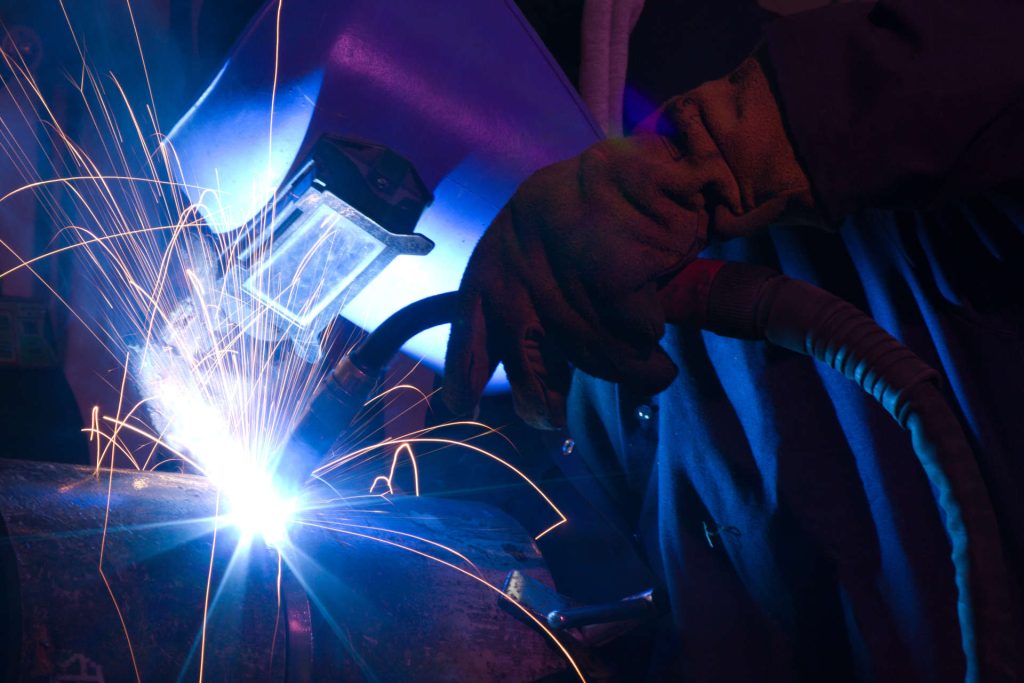
Once you have cleaned the surface of the steel and chosen the right flux-cored wire, you are ready to start welding galvanized steel with flux-cored wire. Here are the steps you need to follow to weld galvanized steel with flux-cored wire:
Setting up the welder:
The first step is to set up your welder for flux-cored wire welding. You should consult your welder’s manual for the specific instructions and settings for your model, but here are some general guidelines to follow:
Load the flux-cored wire into the welder and feed it through the gun. Make sure that the wire is compatible with your welder and that it is not tangled or kinked.
Set Polarity of your welder
Set the polarity of your welder according to the type of flux-cored wire you are using. Most self-shielded flux-cored wires require a DCEN (direct current electrode negative) polarity, which means that the electrode (wire) is connected to the negative terminal and the workpiece (steel) is connected to the positive terminal. This ensures that most of the heat is concentrated on the electrode, which helps melt the flux and create the shielding gas
Adjust the voltage and amperage
Check and modify the voltage and amperage of your welder according to the thickness and type of metal you are welding, and the diameter and type of wire you are using. You should start with a low voltage and amperage setting and gradually increase them until you get a smooth and stable arc. A good rule of thumb is to use 1 amp per 0.001 inch of wire diameter. For example, if you are using a 0.035 inch wire, you should start with 35 amps and adjust from there.
Coordinate the wire feed speed
Coordinate the wire feed speed of your welder according to the voltage and amperage settings you have chosen. The wire feed speed determines how fast the wire is fed through the gun and into the weld pool.
You should fine-tune the wire feed speed until you get a consistent and smooth arc that does not stutter or pop. A good rule of thumb is to use 100 inches per minute (ipm) of wire feed speed per 1 volt of voltage. For example, if you are using 20 volts, you should start with 2000 ipm and adjust from there.
Welding technique:
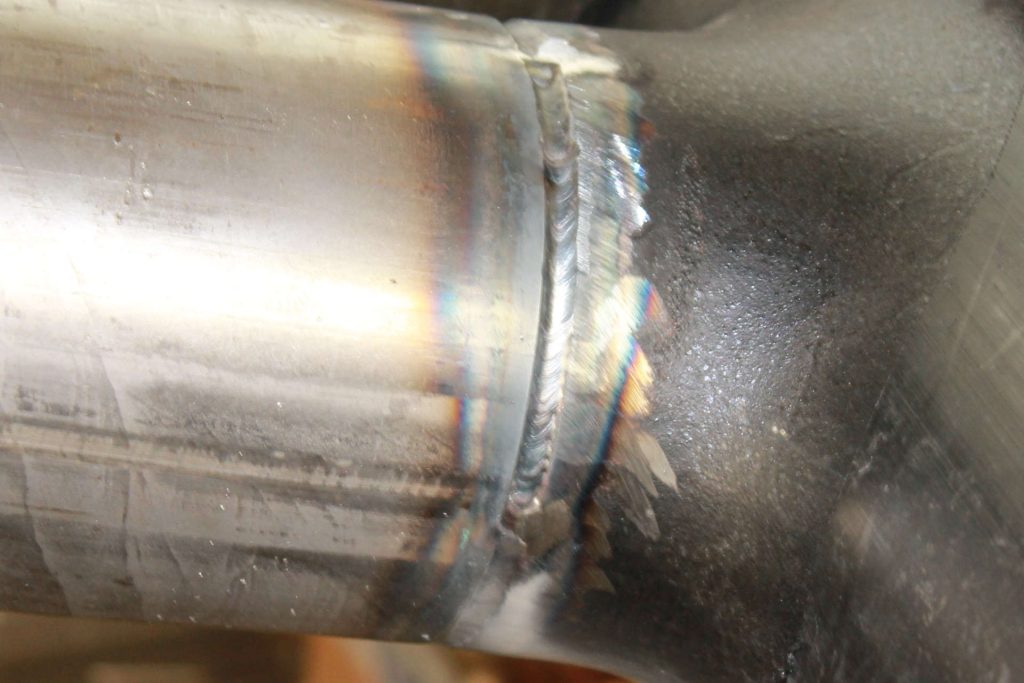
The second step is to use the proper welding technique for welding galvanized steel with flux-cored wire. It is advisable to adhere to the following to get the best weld possible:
- Hold the gun at a 10 to 15 degree angle from the vertical, with the tip pointing in the direction of travel. This will help create a good penetration and avoid undercutting or slag inclusion.
- Keep a steady travel speed that matches the melting rate of the wire. You should move fast enough to avoid excessive heat buildup and zinc vaporization, but slow enough to allow enough filler metal to fill the joint. A good rule of thumb is to move about one inch per second.
- Maintain a consistent arc length that is about one-eighth to one-quarter of an inch from the surface of the metal. This will help create a good fusion and avoid porosity or spatter.
- Use a drag or pull technique, where you move the gun away from the weld pool, rather than a push technique, where you move the gun towards the weld pool. This will help prevent slag from getting trapped in front of the weld pool and creating defects.
- Use a weaving or oscillating motion, where you move the gun slightly from side to side along the joint, rather than a straight motion, where you move the gun in a straight line along the joint. This will help create a wider and stronger weld bead that covers more surface area and fills any gaps or irregularities in the joint.
Safety Precautions:
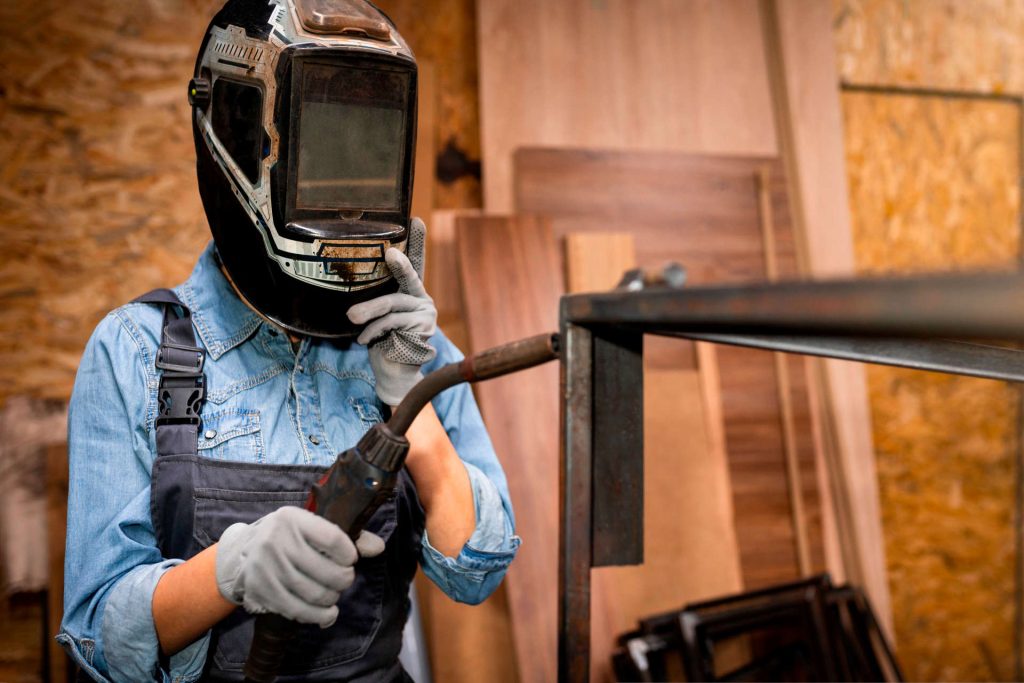
The third step is to take some safety precautions when welding galvanized steel with flux-cored wire. You should follow these tips to protect yourself and others from potential hazards:
- Wear proper personal protective equipment (PPE), such as gloves, goggles, helmet, apron, boots, etc., when welding galvanized steel with flux-cored wire. This will help prevent burns, sparks, spatter, slag, radiation, etc., from injuring you or damaging your clothes.
- Work in a well-ventilated area or use an exhaust fan or hood when welding galvanized steel with flux-cored wire. This will help disperse or remove any toxic fumes or gasses that might be generated by zinc vaporization or flux decomposition.
- Avoid inhaling or ingesting any fumes or dust that might be produced by welding galvanized steel with flux-cored wire. This can cause serious health problems, such as metal fume fever, zinc poisoning, respiratory irritation, etc. If you experience any symptoms, such as nausea, headache, fever, chills, coughing, etc., seek medical attention immediately.
- Keep flammable materials away from the welding area when welding galvanized steel with flux-cored wire. This will reduce the risk of fire or explosion caused by sparks or heat.
- Follow the manufacturer’s instructions and recommendations when using the flux-cored wire and the welder. This will ensure optimal performance and safety of the equipment and the materials.
Wrap Up: Weld Galvanized Steel with Flux-Cored Wire
Welding galvanized steel with flux-cored wire is a complex but rewarding process that can offer many advantages over traditional welding procedures. It can produce strong and durable welds with less heat and distortion. However, it also requires careful preparation and safety precautions to avoid damaging the steel or harming yourself or others.
If you follow the steps and tips that we have discussed above, you can successfully weld galvanized steel with flux-cored wire and achieve your desired results.
Videos
Resources
- University of Wollongong: Characterization of The Structure and Properties of Arc Welded Zinc Alloy Coated Sheet Steels
- University of Massachusetts Amherst: Welding, Cutting and Brazing SOP
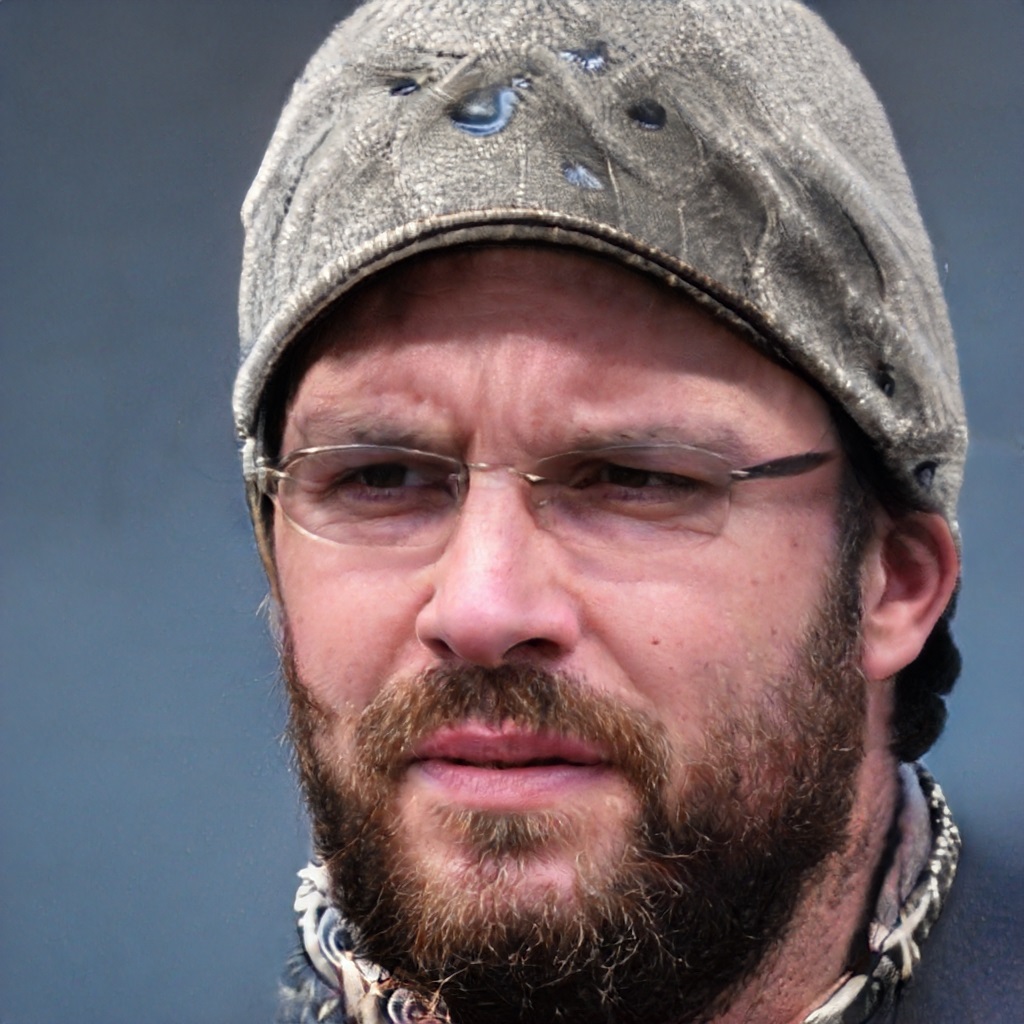
I’ve been involved in the welding industry for over twenty years. I trained in various engineering shops working on various projects from small fabrication and repairs through to industrial projects.I specialize in welding aluminum and food grade stainless steel and an now run an engineering shop fabricating equipment for the food industry.