Advantages and Disadvantages of Using Flux Core Welding for Titanium
americanindustrialsupl and its partners may earn a commission if you purchase a product through one of our links.
Flux core welding for titanium has some advantages and disadvantages that welders should consider before choosing this method for their welding process.
Below we will discuss the pros and cons of flux core welding for titanium and how they affect the welding process’s quality, efficiency, and safety. By going through this article, you should better understand this welding technique’s benefits and drawbacks and whether it suits your welding needs.
Flux Core Wire
The Nature of Flux-Core Welding Titanium
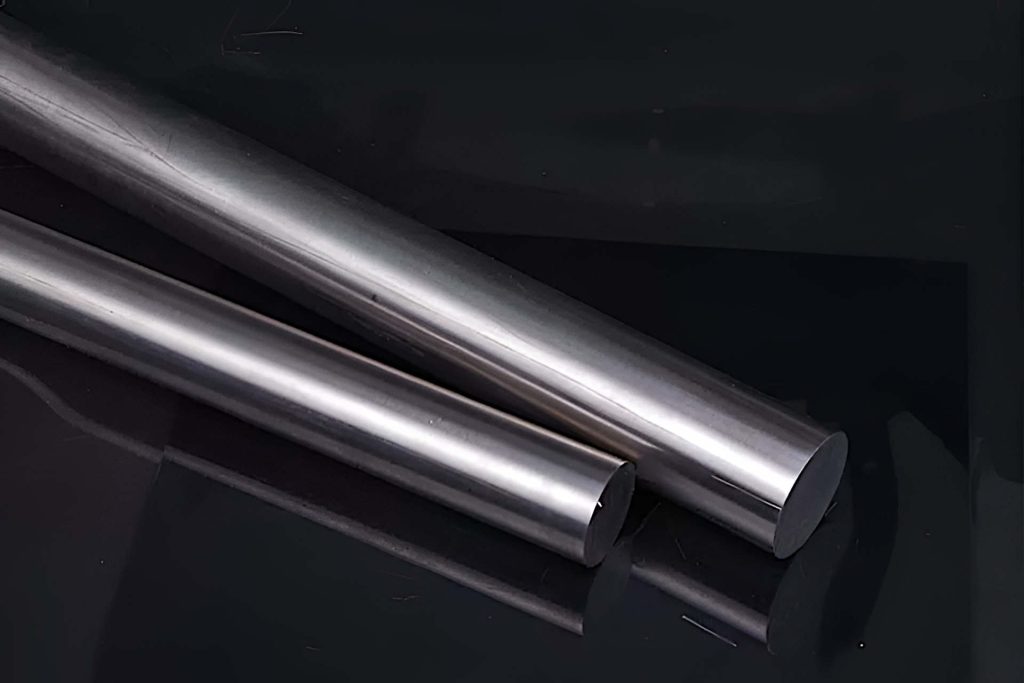
Flux-core welding is an arc welding process that uses a tubular wire with a flux-filled core. The flux protects the weld pool from atmospheric contamination and provides additional alloying elements. Titanium, which is a strong and lightweight metal with high corrosion resistance is a. welders should be aware of before choosing this method.
Table summarizing the main advantages and disadvantages of using flux core welding for titanium:
Advantages | Disadvantages |
---|---|
Increased Deposition Rate | Limited positional weldability |
Improved Penetration and Weld Quality | Increased Heat Input and Potential Distortion |
Enhanced Weld Bead Appearance | Possibility of Hydrogen Embrittlement |
Higher Resistance to Porosity | Requirement for post-weld cleaning and inspection |
Can Be Used in Outdoor or Windy Conditions | Complexity and cost of flux agents and equipment |
Suitable for Welding Thicker Sections of Titanium | Not recommended for welding thin titanium sections |
Note: The table includes only the main advantages and disadvantages mentioned
Advantages of Using Flux Core Welding for Titanium
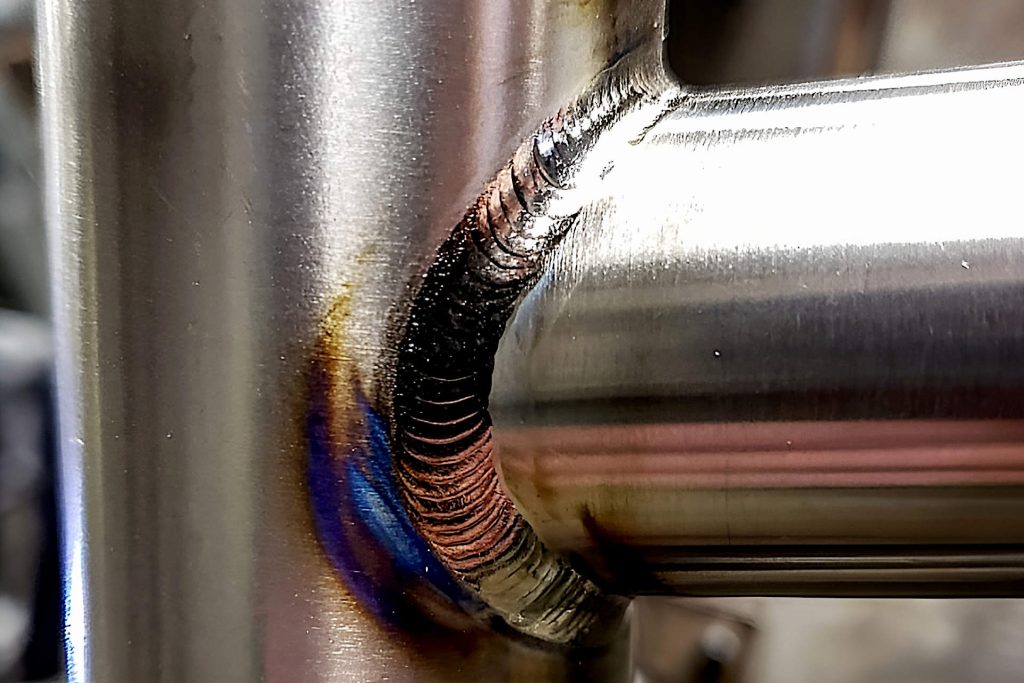
Increased Deposition Rate
One of the main advantages of using flux core welding for titanium is that it allows for a higher deposition rate than other welding methods. Deposition rate refers to the amount of filler metal that is deposited in the weld per unit of time.
A higher deposition rate means faster welding and less heat input, which reduces distortion and residual stress in the weldment. Flux core welding can achieve deposition rates of up to 12 pounds per hour, compared to 5 pounds per hour for gas tungsten arc welding (GTAW) or 8 pounds per hour for gas metal arc welding (GMAW).
Improved Penetration and Weld Quality
Another benefit of flux core welding for titanium is that it provides better penetration and weld quality than other processes. Penetration is the depth of fusion into the base metal, which affects the strength and integrity of the weld. Weld quality refers to the absence of defects such as porosity, cracking, or lack of fusion.
Flux core welding can produce deep penetration and high-quality welds because the flux protects the molten metal from atmospheric contamination and stabilizes the arc. The flux also forms a slag layer that covers the weld bead and prevents oxidation and nitriding of the titanium.
Enhanced Weld Bead Appearance
Another advantage of using flux core welding for titanium is enhancing the weld bead appearance. In skilled hands, flux core welding can produce a smoother and more uniform weld bead. (Weld bead appearance is the visual aspect of the weld, which can indicate its quality and performance).
A good weld bead should be smooth, uniform, and free of spatter or slag. Flux core welding can create a smooth and uniform weld bead because the flux controls the shape and size of the molten pool and reduces the spatter. The slag layer also helps to smooth out any irregularities or ripples on the weld surface.
Higher Resistance to Porosity
One of the challenges of welding titanium is to prevent porosity, which is the formation of gas pockets creating voids or holes in the weld metal. Flux core welding for titanium generally offers higher resistance to porosity than other techniques.
Porosity can weaken the weld and cause corrosion or cracking. Flux core welding can prevent porosity by shielding the molten metal from oxygen, nitrogen, and hydrogen, which are the primary sources of gas formation in titanium welding. The flux also searches for residual gas from the weld pool and releases it through the slag layer.
Can Be Used in Outdoor or Windy Conditions
Flux core welding for titanium is more versatile than solid wire welding because it can be used in outdoor or windy conditions where other processes may fail. Flux core welding does not necessarily require an external shielding gas (although gas-shielded flux core wire aris available), which can be blown away by wind or draft, causing porosity or loss of arc stability.
In most circumstances, the flux provides adequate protection for the weld pool and arc from any environmental interference. Flux core welding can also tolerate some degree of dirt, rust, or oil on the base metal, which may be present in outdoor applications.
Suitable for Welding Thicker Sections of Titanium
A sixth benefit of using flux core welding for titanium is that it is suitable for welding thicker titanium sections than other methods. Titanium has a high thermal conductivity and a low coefficient of thermal expansion, which means it conducts heat quickly and does not expand or contract much when heated or cooled.
Because of these properties, it can make it difficult to weld thick sections of titanium with conventional welding processes, as they may cause excessive heat input, distortion, or cracking. Flux core welding can overcome this challenge by providing a high deposition rate, deep penetration, and low heat input, which enable faster welding and less distortion of thick titanium sections.
Additional Advantages of Using Flux Core Welding for Titanium
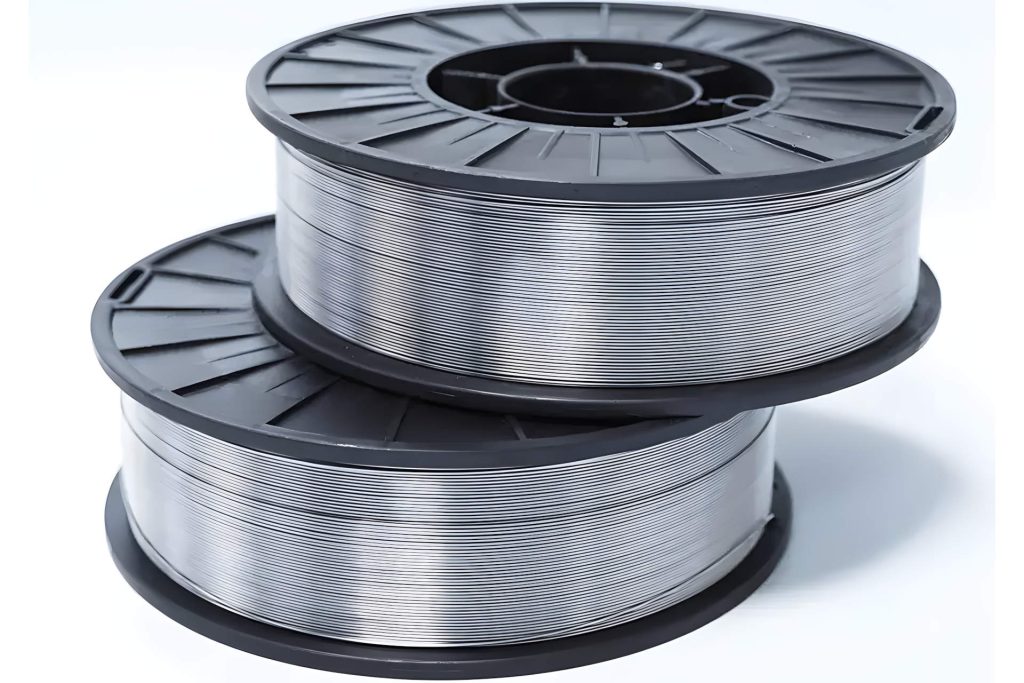
Here is a table summarizing the additional advantages of using flux core welding for titanium:
Additional Advantages | Description |
---|---|
No shielding gas required | Unless you are using gas-shielded flux core wire there will be no need to transport and manage awkward gas bottles. |
Wide range of flux core wires to choose from | There are several flux core wires that can be used for welding titanium, many of mild steel flux core wires can be used but the specific type of wire may depend on the welding machine, such as the Lincoln Electric FC90, being used |
Increased filler metal efficiency | Flux core welding allows for higher filler metal deposition efficiency, minimizing material waste. |
Increased travel speed | Flux core welding enables faster travel speeds, improving productivity in welding titanium. |
Improved gap-bridging capability | Flux core welding has better gap-bridging ability, accommodating small gaps or fit-up irregularities. |
Enhanced operator comfort | Flux core welding produces less fumes and smoke, creating a more comfortable working environment. |
Versatility with different titanium alloys | Flux core welding can be used with various titanium alloys, making it suitable for diverse applications. |
The table includes the additional advantages mentioned Of course other advantages may exist but dependent more on individual use cases.
Disadvantages of Using Flux Core Welding for Titanium`
Although flux core welding has a number of advantages for welding titanium, some drawbacks also need to be considered. Here are some of the disadvantages of using flux core welding for titanium:
Limited positional weldability:
Flux core welding relies on gravity to feed the flux into the weld pool. The result is that it makes out-of-position welding more complicated. It means that the welder has to work in a flat or horizontal position or use special techniques to prevent the flux from falling out.
Titanium, however, often requires welding in different positions, such as vertical or overhead, to achieve the desired shape and strength. Flux core welding is not well suited for these situations and may result in poor-quality welds.
Increased Heat Input and Potential Distortion:
Flux core welding generates more heat than other welding methods, such as gas tungsten arc welding (GTAW) or gas metal arc welding (GMAW). The increased heat can cause problems for titanium, which has a low thermal conductivity and a high coefficient of thermal expansion. Excessive heat input can lead to distortion, cracking, or warping of the titanium parts, especially if they are thin or complex.
Possibility of Hydrogen Embrittlement:
Flux core welding introduces hydrogen into the weld metal, which can cause embrittlement and reduced ductility of titanium. Hydrogen embrittlement is a phenomenon where hydrogen atoms diffuse into the metal lattice and create internal stresses that weaken the material. Titanium is particularly susceptible to hydrogen embrittlement, and can lose up to 50% of its tensile strength if exposed to high levels of hydrogen.
Requirement for Post-Weld Cleaning and Inspection:
Flux core welding produces slag and spatter that need to be removed after welding. This can be a tedious and time-consuming process, especially for intricate or large titanium parts. Moreover, flux core welding may leave behind traces of flux that can corrode or contaminate the titanium surface. Therefore, flux core welded titanium parts require thorough cleaning and inspection to ensure their quality and integrity.
Complexity and Cost of Flux Agents and Equipment:
Flux core welding involves using special flux agents designed to protect the weld metal from oxidation and contamination. These flux agents have to be carefully selected and stored, as they can degrade over time or react with moisture. Flux core welding also requires more sophisticated equipment than other welding methods, such as wire feeders, power sources, and shielding gas systems. These factors add to the complexity and cost of flux core welding for titanium.
Additional Advantages of Using Flux Core Welding for Titanium:
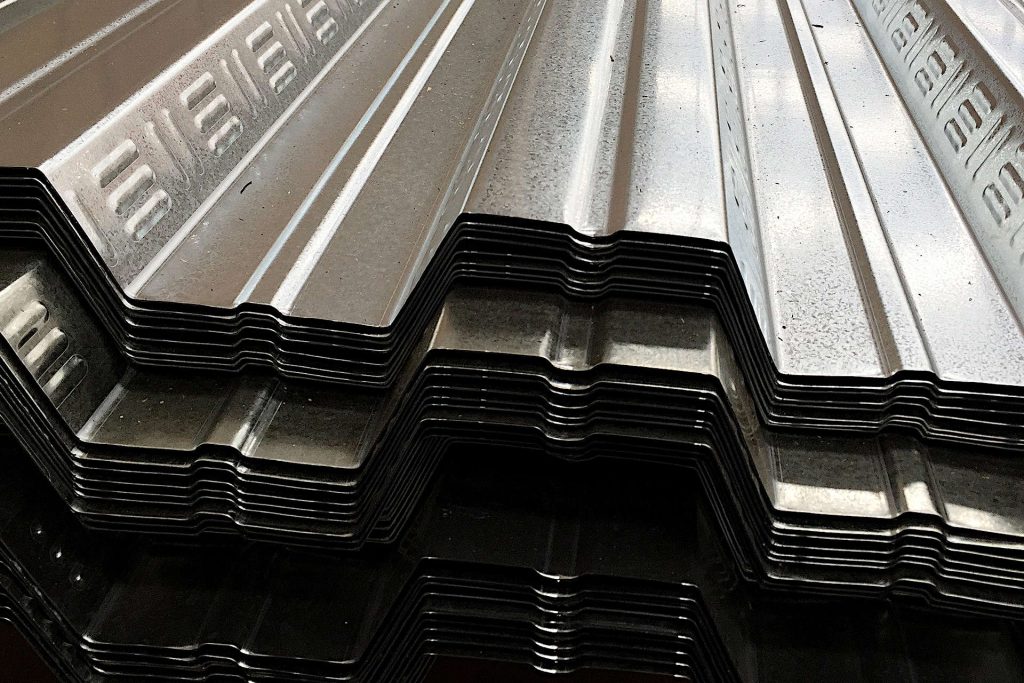
Flux core welding is not a good choice for welding thin titanium sections, such as sheets or tubes. The high heat input and large weld pool can cause excessive melting and distortion of the thin material, resulting in poor weld quality and appearance. Furthermore, flux core welding can create large gaps or holes in the thin sections, compromising their strength and performance.
Other Disadvantages of Using Flux Core Welding for Titanium
Other possible disadvantages of using flux core welding for titanium:
Additional Disadvantages | Description |
---|---|
Difficulties in welder training | Flux core welding for titanium may require specialized training and experience due to its specific techniques and parameters. |
Limited availability of flux core titanium wires | Compared to other welding processes, the availability of flux core titanium wires may be more limited, making it challenging to find suitable consumables. |
Higher equipment costs | The equipment required for flux core welding, including wire feeders and power sources, can be more expensive compared to some other welding methods. |
Increased post-weld cleaning and inspection requirements | Flux core welding often necessitates thorough cleaning and inspection of the welds due to the presence of slag and potential flux residue. |
Limited suitability for thin sections with complex geometry | Flux core welding may not be suitable for welding thin titanium sections with intricate shapes or complex geometry, as it can lead to excessive heat input and poor weld quality. |
The table includes the additional disadvantages but as with advantages there are many other possible disadvantages that will depend upon the specific welding project.
Final Thoughts: Advantages and Disadvantages of Using Flux Core Welding for Titanium
The use of flux core welding for titanium offers both advantages and disadvantages. Considering the specific requirements and constraints before selecting this welding method for titanium projects is essential. Let’s summarize the key points discussed:
- Flux core welding provides advantages such as increased deposition rate, improved penetration and weld quality, enhanced weld bead appearance, higher resistance to porosity, and suitability for welding thicker titanium sections.
- However, it also has its limitations, including limited positional weldability, increased heat input and potential distortion, the possibility of hydrogen embrittlement, the requirement for post-weld cleaning and inspection, and the complexity and cost of flux agents and equipment.
Before deciding to use flux core welding for titanium, it is crucial to evaluate the project’s needs carefully. Consider factors such as the weld position required, the desired quality of the weld, the thickness of the titanium, and the budget constraints. Consulting with welding professionals can provide valuable insights and help make an informed decision regarding the most suitable welding method for the specific application.
Remember, the success of any welding project relies on choosing the right method based on the project’s unique requirements. By weighing the advantages and disadvantages, you can ensure optimal results and achieve your desired welding outcomes.
Flux Core Wire
Commonly Asked Questions
What is flux core welding for titanium?
Flux core welding for titanium is a welding process that utilizes a flux core wire filled with flux agents to shield the weld pool from atmospheric contaminants. The flux core wire is made up of a titanium alloy with a flux compound, which releases a protective gas when heated, creating a shield around the weld. This shielding gas prevents oxidation and helps in creating a strong and durable titanium weld.
What types of flux agents are used in flux core welding?
There are different types of flux agents used in flux core welding for titanium. Some common flux agents include:
- Titanium-based flux agents: Titanium-based flux agents are designed specifically for titanium welding. They provide excellent protection against oxidation and help in achieving high-quality welds.
- Calcium-based flux agents: These are commonly used for welding titanium alloys. They provide reasonable protection against contaminations and help reduce harmful oxides’ formation.
- Aluminum-based flux agents: These are suitable for welding certain titanium alloys. They provide adequate protection against contamination and ensure good weld appearance.
The choice of flux agent depends on the specific requirements of the welding project and the type of titanium being welded.
Can flux core welding be used for all titanium applications?
Flux core welding can be used for a wide range of titanium applications. However, its suitability depends on various factors such as the thickness of the titanium, the desired weld quality, and the welding position. Flux core welding is particularly well-suited for welding thicker sections of titanium and in outdoor or windy conditions.
For thin titanium sections or applications that require precise and intricate welds, other welding methods, such as TIG (Tungsten Inert Gas) welding, may be more appropriate. It is essential to consider the project’s specific requirements and consult with welding experts to determine the most suitable welding method for each application.
Videos
Resources
- Chirieleison, Gregory Michael: The Effect of Flux Ingredients on Flux-Cored Arc Welding of Titanium
- Dom Bergeron: Welding Titanium
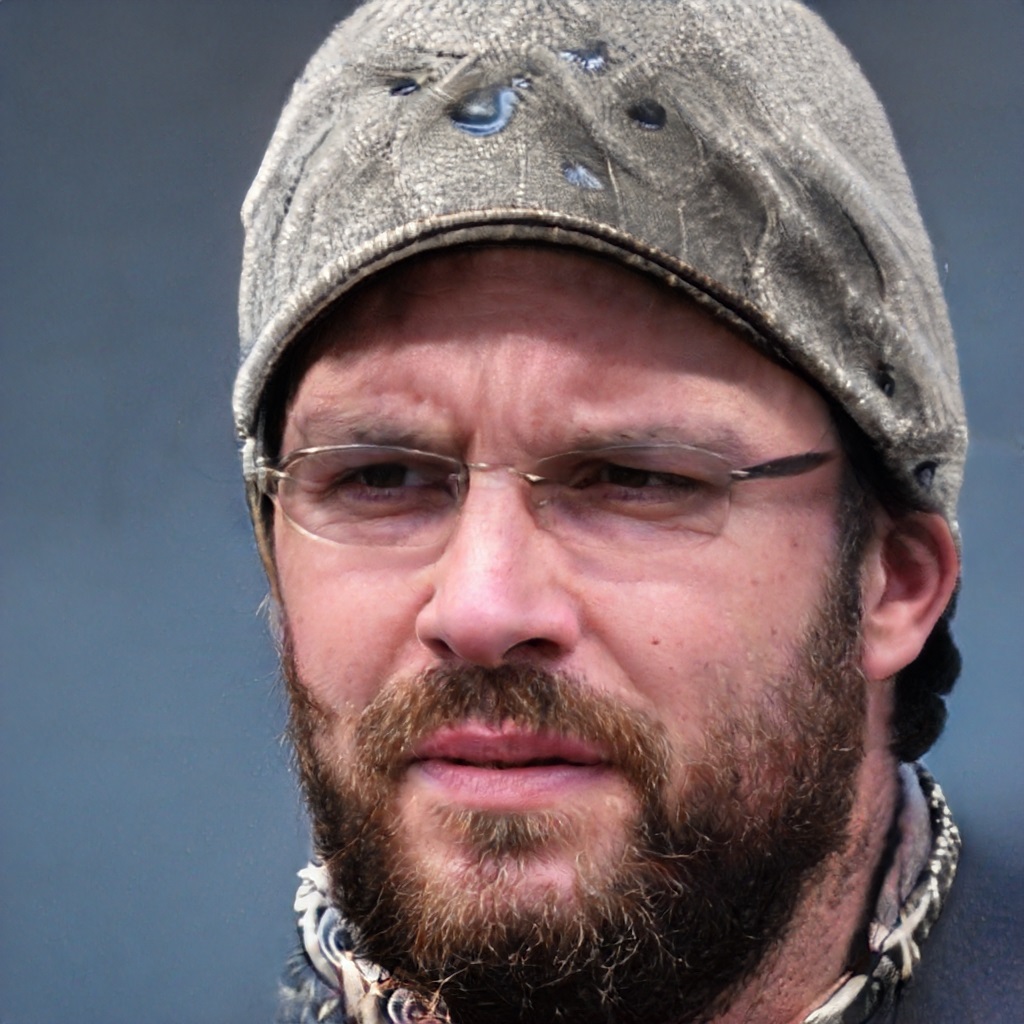
I’ve been involved in the welding industry for over twenty years. I trained in various engineering shops working on various projects from small fabrication and repairs through to industrial projects.I specialize in welding aluminum and food grade stainless steel and an now run an engineering shop fabricating equipment for the food industry.