Flux Core Wire for Welding Aluminum – Exploding the Myth
In simple terms you can’t use flux core welding method with aluminum so flux core wire for welding aluminum doesn’t exist and you will waste a lot of effort trying to find or weld aluminum using the flux core method.
It is easy to see why this myth perpetuates. The flux core method holds a lot of attractions, particularly to the hobbyist welder who doesn’t want to use gas. Flux core wire has a hollow core filled with flux, which is a material that protects the weld from contamination and helps create a strong bond between the metals.
For mild steel, stainless and some alloys it works well but when comes to aluminum, the properties of the metal prevent the welds from being successful. Below, we will look at the reasons as to why aluminum is not suitable for flux core welding and suggest some alternatives you can use instead.
The Myth of Flux Core Wire for Welding Aluminum
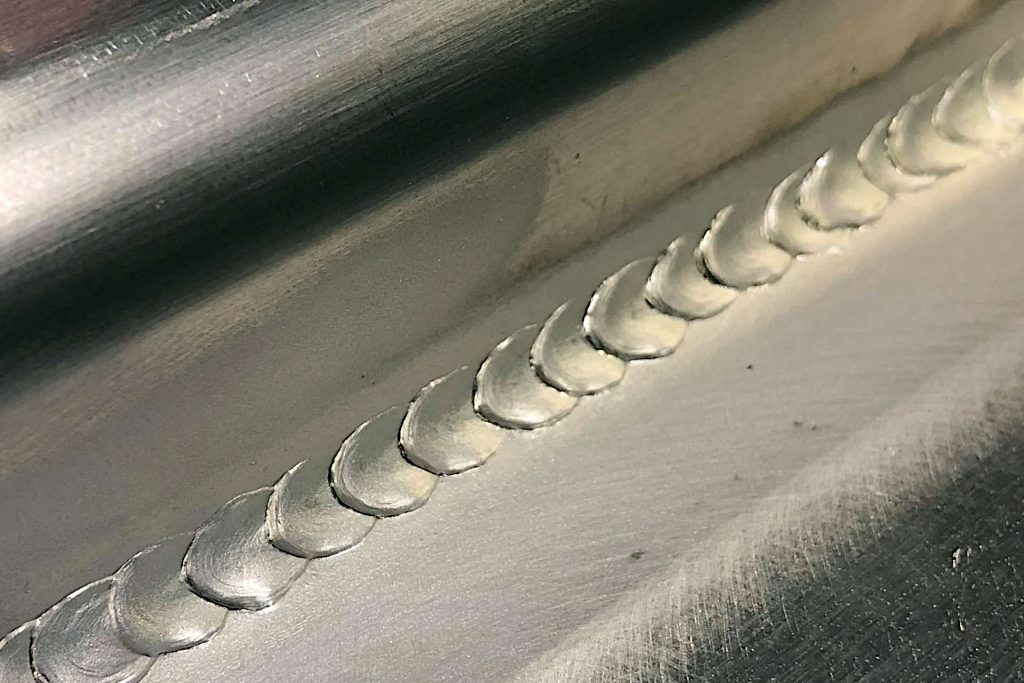
One of the reasons why flux core wire is popular for welding steel is that it does not require a shielding gas, which is an inert gas that prevents the weld from oxidizing and weakening.
Shielding gas can be expensive and cumbersome to use, especially for small welding projects. However, when you are welding aluminum, flux core wire is not a viable option.
There are several reasons as to why there is no flux core wire available for aluminum on the market. The principal reason is the nature of aluminum as a metal prevents the flux core method from achieving robust welds.
The leading cause of this is aluminum’s high thermal conductivity, which means it transfers heat very quickly. Consequently, it makes it challenging to maintain a stable arc and a consistent temperature with flux core wire, which can result in poor weld quality and porosity.
Porosity is when minute holes form in the weld due to trapped pockets of gas or contaminants, which can compromise the strength and appearance of the weld. Furthermore, flux core wire can introduce unwanted elements into the weld pool, such as hydrogen, which can cause cracking and embrittlement in aluminum.
Alternatives to Flux Core Wire for Welding Aluminum
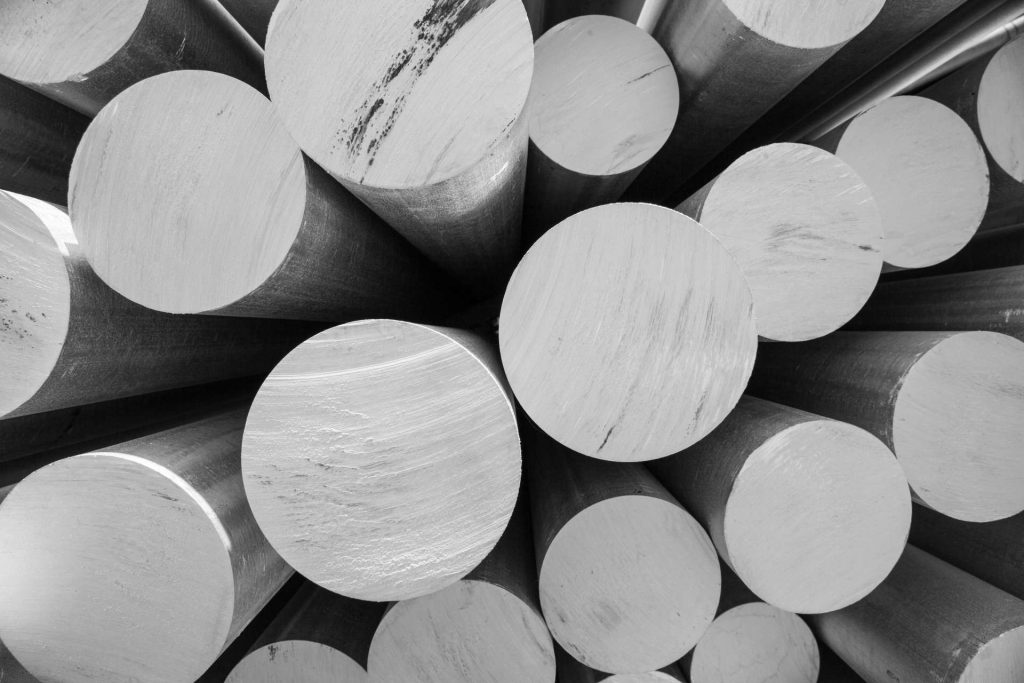
If you want to weld aluminum without using flux core wire, you have three main options: solid aluminum wire (MIG), TIG, or brazing rods.
Using Solid Aluminum Wire
Solid aluminum wire is a type of wire that is made of pure aluminum or an alloy of aluminum and other metals. Unlike flux core wire, solid aluminum wire requires a shielding gas, such as argon or helium, to protect the weld from oxidation.
Solid aluminum wire can produce high-quality welds on aluminum, but it also has some drawbacks:
- You need a welder that can handle aluminum, which usually means a MIG (metal inert gas) welder with a spool gun attachment. A spool gun is a device that feeds the wire directly from the gun to the weld pool, which prevents the wire from tangling or jamming in the feed mechanism. A MIG welder with a spool gun can be expensive and bulky to use, especially for small or intricate welding projects.
- You need to thoroughly clean the aluminum’s surface before welding, as any dirt or oxide layer can interfere with the weld quality.
- Finally you have to carefully adjust your welder’s settings, such as the voltage, amperage, wire speed, and gas flow rate, to match the type and thickness of the aluminum you are welding.
Using TIG Welding
Tungsten Inert Gas (TIG) welding is a popular/common method for welding aluminum material. It uses a non-consumable tungsten electrode and a separate filler rod to create the weld. TIG welding provides precise control and produces high-quality welds, making it a preferred choice for aluminum welding.
- Firstly correctly clean the surface, then preheat. Preheating should be regarded as depending on the type of aluminum. The temperature should be between 150°F and 250°F, depending on the thickness of the aluminum.
- Attach a heatsink to prevent the aluminum from overheating and warping during welding. Clamp the heatsink to the workpiece near the weld area.
- Set the balance control. A 60% cleaning and 40% penetration setting is usually a good place to start from.
- Set the polarity to AC and the correct amperage, usually 1 amp per 0.001 inch of aluminum thickness.
Using Brazing Rods
Brazing rods are another option for welding aluminum without using flux core wire. Brazing rods are metal rods that have a lower melting point than aluminum and contain a flux coating that helps them adhere to the metal surface.
Brazing rods do not require a shielding gas or a special welder to use; you can simply heat them with a propane torch and apply them to the joint between the aluminum pieces. Brazing rods can be useful for repairing or joining thin or irregular-shaped pieces of aluminum, but they also have some limitations.
- First, brazing rods do not create a fusion weld, which means they do not melt and mix with the base metal. Instead, they create a mechanical bond that relies on the strength of the filler metal and the surface contact between the metals. The result is that brazing rods cannot fill large gaps or cracks in the metal and may not be as strong or durable as fusion welds.
- Second, brazing rods may not match the color or appearance of the aluminum you are welding, which can affect the aesthetics of your project.
Final Thoughts: Flux Core Wire for Welding Aluminum – Exploding the Myth
In conclusion, flux core wire for welding aluminum is a myth that does not exist in reality. Flux core wire is not suitable for welding aluminum due to its high thermal conductivity, porosity problems, and compatibility issues with flux elements.
If you want to weld aluminum without using flux core wire, you can either use solid aluminum wire with a shielding gas and a MIG welder with a spool gun or use brazing rods with a propane torch. Both options have their advantages and disadvantages depending on your budget, equipment availability, project size and complexity, and desired weld quality and appearance.
Resources
- Universal Technical Institute: How To Weld Aluminum: The Beginner’s Guide
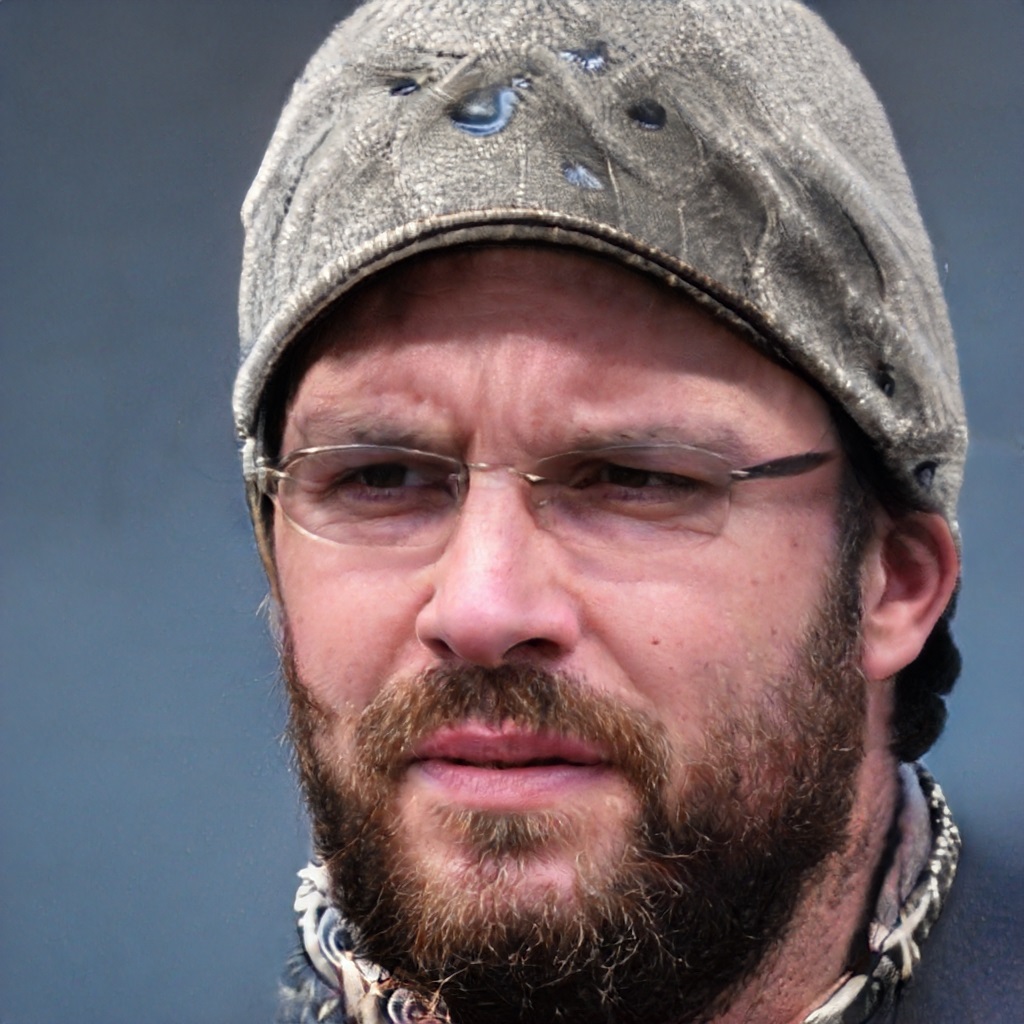
I’ve been involved in the welding industry for over twenty years. I trained in various engineering shops working on various projects from small fabrication and repairs through to industrial projects.I specialize in welding aluminum and food grade stainless steel and an now run an engineering shop fabricating equipment for the food industry.