Fusing Metal – An Introduction to Welding
americanindustrialsupl and its partners may earn a commission if you purchase a product through one of our links.
Fusing Metal – welding is the process in which two pieces of metal are fused together using heat and or pressure.
Welding is therefore a fabrication process that is a crucial part of the manufacturing operations and, as with any manufacturing processes, the welding procedure used to fabricate a part or structure is dependent on various factors. These factors and the decisions made relating to them can impact on the eventual quality of the end product.
Welding is commonly employed in construction, shipbuilding, automobile fabrication, aircraft manufacturing, machine building, pipe fitting, and many other disciplines.
Fusing Metal: Different Welding Processes
Welders use a variety of welding processes to join metal parts together. In some cases, a welder may join metal parts together by heating the parts to a temperature at which a portion of the metal parts melts and forms a molten weld pool. The molten weld pool cools to form a weld joint. The weld joint may have mechanical properties that differ in one or more ways from the properties of the surrounding metal parts.
There are around thirty different types of welding process that used, some much more common than others. The main commonly used type of welding is arc welding and uses an electric arc between two electrodes. Arc welding is often performed using shielded metal arc welding, gas metal arc welding or gas tungsten arc welding.
The main differentiation between these Arc processes being the use of the arc. Tungsten inert gas welding uses a tungsten electrode and a shielding gas such as argon or helium. Gas metal arc welding , also known as metal-inert gas welding, uses a non-consumable electrode and a shielding gas. MIG welding has become increasingly popular because it produces high-quality joints without requiring post-weld cleaning.
Gas Tungsten Arc Welding (TIG)
Gas tungsten arc welding, also known as Tungsten Inert Gas (TIG) welding, is a type of arc welding where a filler material such as wire, rod, or powder is fed into the arc zone. Gas tungsten arc welding has been widely used for joining aluminum, steel, stainless steel, and other metals. It is also used for welding plastic pipes and fittings.
Shielded Metal Arc Welding (SMAW)
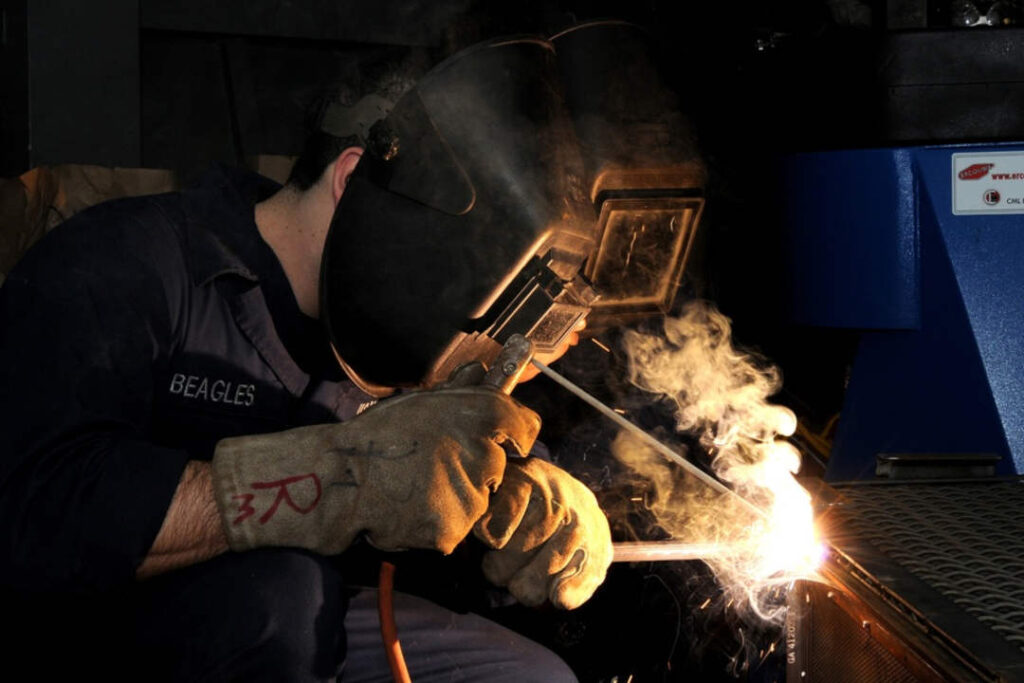
Shielded metal arc welding (SMAW), also know as manual metal arc or MMA, or generally know at stick welding, is a continuous stream of filler metal flowing out of the welding gun during welding. This allows the filler metal to be deposited onto both sides of the workpiece. A shield blocks the heat generated by the arc from reaching the surface of the workpiece. Shielded metal arc welding is typically used for welding mild steels, stainless steels, and low alloy steels. For a more detailed understanding of stick welding click here.
Gas Metal Arc Welding (MIG)
Metal Inert Gas welding is a relatively new type of welding technology. MIG welding was developed in the 1960’s by General Electric Company. Since then, this method of welding has gained popularity due to its ability to produce high-strength, defect free welds.
You can read more in-depth about MIG welding here.
Other Arc Welding Processes
Other processes include flux-cored arc welding, gas tungsten arc welding, plasma arc welding, submerged arc welding, pulsed arc welding, and resistance welding.
As mentioned above these processes vary in how arcs are created, the type of shielding gas used, and the type of electrode used.
Different processes have advantages and disadvantages, which influence which process is best suited for a given application. A thorough understanding of these trade-offs can help guide engineers in selecting the best welding procedure for a given application.
Many processes produce high-quality welds. Certain processes, such as the submerged arc welding process, can produce welds that are stronger than the base materials.
[amazon_auto_links id=”6652″]
Choosing the Right Welding Procedure
More often than not the choice of procedure is fairly straightforward However, as with design, materials and process selection, welding procedure selection can be exercise in trade-offs. These trade-offs involve anticipated cost of the part, aesthetic and economic considerations, and process-control requirements.
Determining which welding procedure is best for a given application involves first determining what welding process is best.
However, even though certain welding processes can produce exceptional results, some of these processes take longer to complete than others. The welding process chosen for an application should balance the requirements of weld quality, strength and durability, and production speed.
Shielding Gas
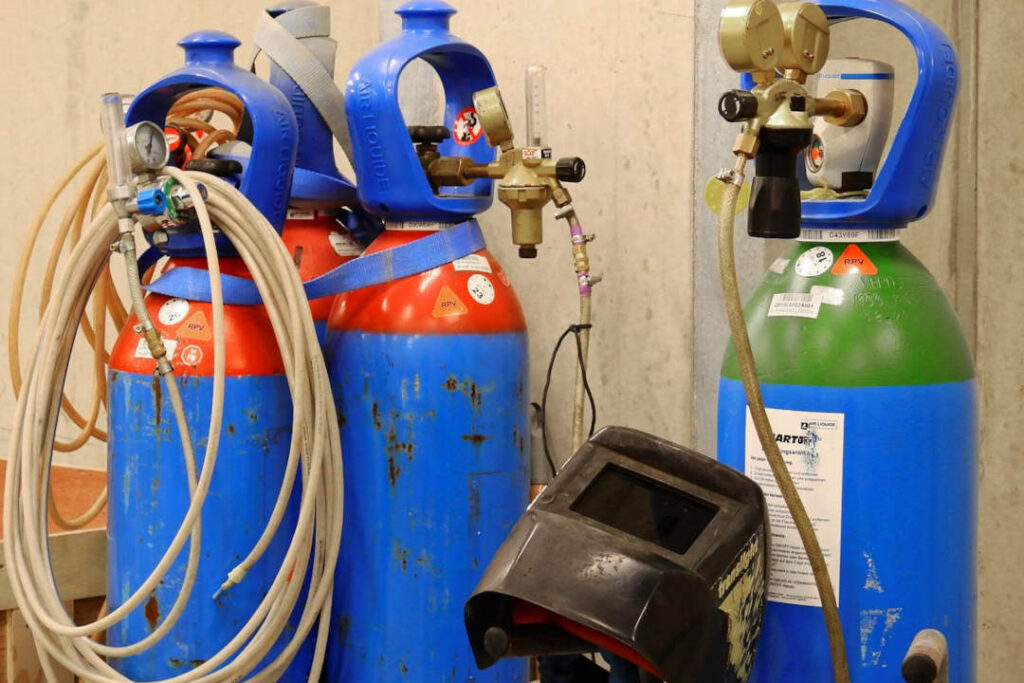
Welding processes vary in the type of shielding gas used. Most welding processes use a shielding gas to shield the weld from contaminants, such as oxygen and nitrogen. Shielding gases used in welding processes include carbon dioxide, argon, helium, and nitrogen.
The choice of shielding gas depends on a variety of factors. These include the weld’s characteristics, such as its thickness, its structural requirements, and the type of base material. It also depends on the welding process used, such as the type of shielding gas and electrode.
The shielding gas type also affects weld quality and the integrity of the weld’s metallurgical properties, including tensile strength, ductility, and toughness.
The shielding gas type also affects the weld’s micro-structure. The weld’s micro-structure is the texture, size, and properties of the weld’s constituent grains. The weld’s microstructure affects the weld’s strength, ductility, and toughness.
Finally, the shielding gas type affects weld cost. Some shielding gases are more expensive than others. Some processes, such as gas metal arc welding, can use a variety of shielding gases. However, certain welding processes, such as submerged arc welding, require a specific type of shielding gas.
Understanding The Materials You Are Welding
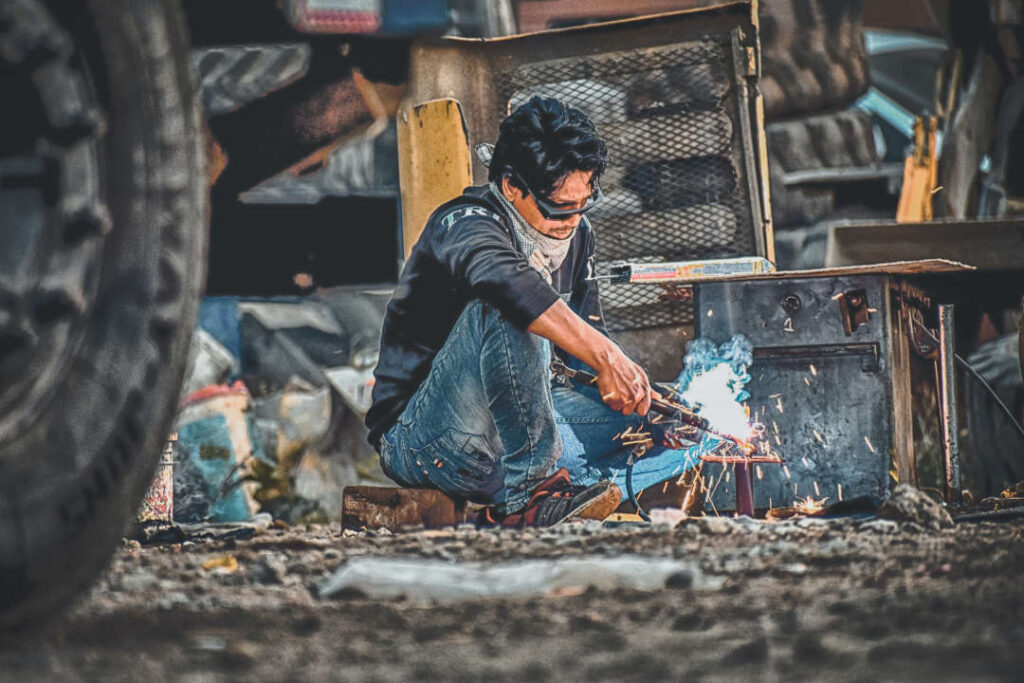
The welding process chosen for an application should balance the requirements of the base material’s composition, the shielding gas type and cost, and the weld’s micro-structure.
The welding process decided upon should take into account the requirements of the welding electrode type, cost, and weld quality. Welding electrodes come in a variety of types and compositions. The welding electrode type chosen depends on a variety of factors, including weld type, base material, weld strength requirements, and weld aesthetics.
The type of electrode also affects weld cost. Certain welding electrodes are more expensive than others. The eventual process chosen for an application should therefor take account of the requirements of the welding electrode type, cost, and weld quality. Thus the determined upon welding process should consider the requirements of the weld’s aesthetic requirements, cost, and weld quality.
All welding processes vary in how much heat they generate. They also vary in how heat from the weld affects the base material. Some processes, such as gas metal arc welding, create weld layers that shrink during cooling. These processes produce welds that leave minimal distortion. Other welding processes, such as submerged arc welding, create weld layers that expand during cooling. These processes produce welds that leave significant distortion.
Selecting the best welding procedure for an application involves understanding the benefits and limitations of different welding processes. Different welding processes produce different weld qualities. However, each welding process has strengths and weaknesses. Welders are skilled at using the welding processes at their disposal to produce high-quality welds. Welder expertise, combined with an understanding of the benefits and limitations of different welding processes, can help engineers select the best welding process for a given application.
[amazon_auto_links id=”6660″]
Resources
- New England Institute of Technology: What is Welding?
- Western Technical College: Basic Welding
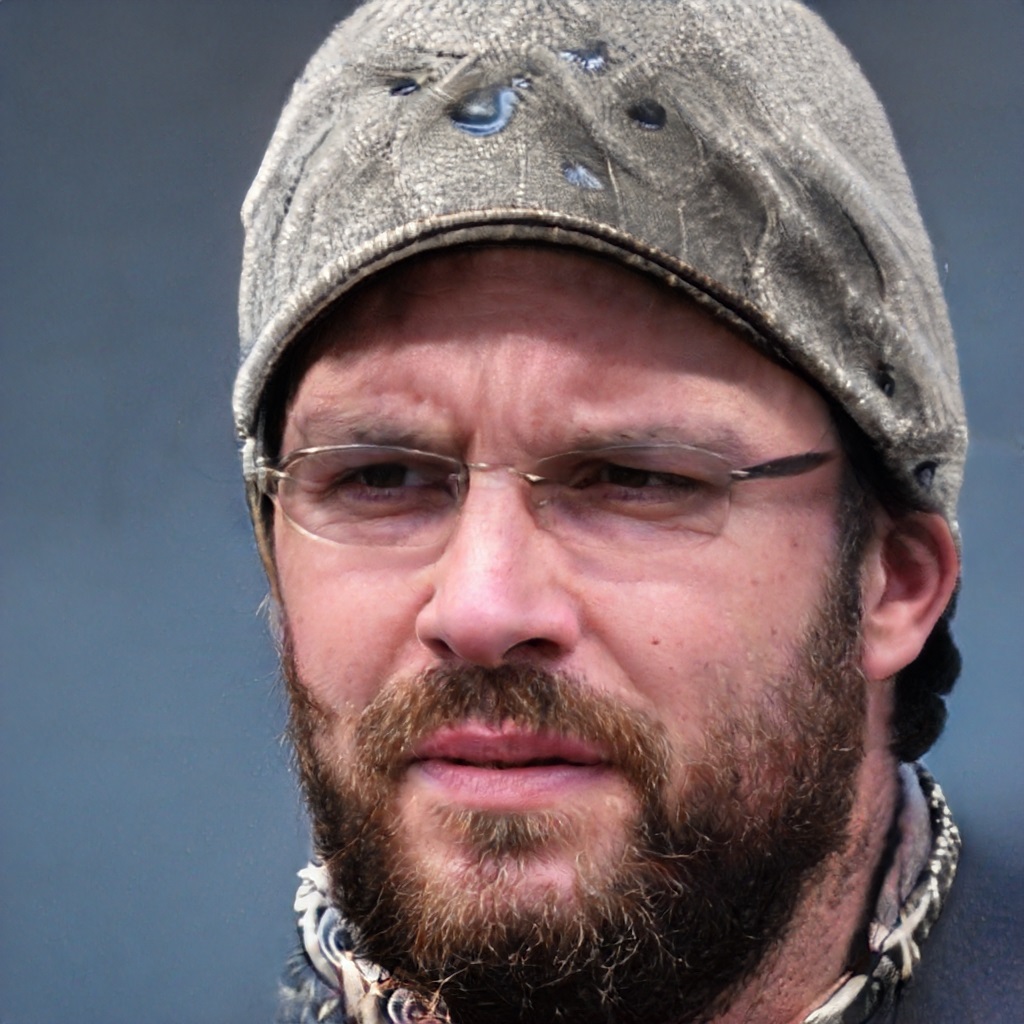
I’ve been involved in the welding industry for over twenty years. I trained in various engineering shops working on various projects from small fabrication and repairs through to industrial projects.I specialize in welding aluminum and food grade stainless steel and an now run an engineering shop fabricating equipment for the food industry.