Welding Galvanized Steel: What You Need to Know
americanindustrialsupl and its partners may earn a commission if you purchase a product through one of our links.
You’re in a clients workshop, ready to start his project. You walk across to the material stack and immediately realize, from the distinctive, shiny coating on the steel, it’s galvanized. Welding galvanized steel, Is a task that demands specific skills and knowledge. As a welder, understanding the nuances of working with galvanized steel is crucial. Not only does it affect the welding process itself, but it also impacts safety measures and the quality of your final welds.
Key Takeaways
- Remove Zinc Coating: Essential for clean and strong welds.
- Welding Process Selection: Choose the right method (TIG, MIG, Stick) based on the project’s specifics.
- Health Risks: Be aware of risks from inhaling zinc oxide fumes.
- Safety Measures: Use proper ventilation and protective equipment to ensure safety.
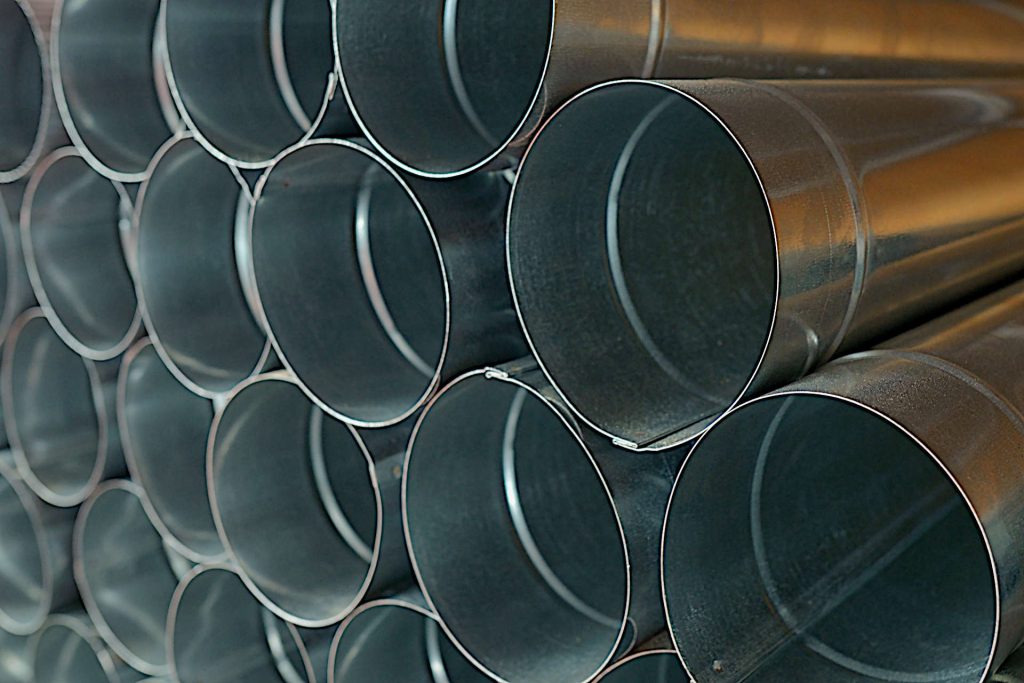
Below, we will look in depth at the differences of welding galvanized steel from other material. We’ll explore the processes and techniques necessary for effective welding, the safety precautions to keep in mind, and the particular challenges you’ll face. You’ll also discover best practices for different welding methods, ensuring your work is both safe and of the highest quality. Whether you’re a seasoned professional or just starting out, this guide will equip you with the knowledge needed to master this unique aspect of welding.
Galvanized Coating and How it Affects The Welding Process
When you’re welding, the type of coating on your steel isn’t just a minor detail — it’s a game-changer. Galvanized steel, coated with a protective layer of zinc, presents unique challenges in welding. Here’s how this coating impacts the welding process and what you need to know to tackle it effectively.
What is Galvanized Coating on Steel?
Galvanized coating is essentially a zinc coating applied to steel to prevent rust. There are a few common methods to apply this coating:
- Electroplating: A thin layer of zinc is electrically bonded to the steel.
- Hot-dipping: Steel is dipped in molten zinc, creating a thicker coating.
- Thermal spraying: Zinc is sprayed onto the steel surface.
Each method affects the welding process differently, primarily due to the thickness and composition of the zinc layer.
What is Galvanized Coating Made From?
As mentioned, the primary component of the galvanized coating is zinc. This metal offers excellent corrosion resistance, which is why it’s widely used. However, zinc’s properties also introduce certain complexities when welding.
How Does Galvanized Coating Affect Weld Penetration?
The presence of a zinc coating impacts weld penetration in several ways:
- Melting Point: Zinc’s lower melting point compared to steel means it vaporizes quickly during welding, potentially affecting penetration.
- Weld Pool Fluidity: Zinc can increase the fluidity of the weld pool, which might lead to issues like poor penetration and increased spatter.
How Does It Affect Post-Weld Processes?
After welding galvanized steel, several additional steps are often required:
- Cleaning: Zinc oxide residues need to be cleaned off the weld area.
- Inspection: Check for issues like porosity or weak welds due to zinc interference.
- Re-coating: Often, the welded area needs a new protective coating, such as paint or a zinc-rich primer, to restore corrosion resistance.
Factor | Impact on Welding Process |
---|---|
Zinc Melting Point | Causes rapid vaporization |
Weld Pool Fluidity | Increases spatter, affects penetration |
Post-Weld Cleaning | Necessary to remove zinc oxide residues |
Post-Weld Inspection | Critical for identifying weld defects |
Re-coating | Required to restore corrosion resistance |
Knowledge of these aspects of welding galvanized steel is essential for successful welds. By knowing what to expect and how to adapt your techniques, you can overcome the challenges posed by this unique material.
Which Welding Processes Can Be Used for Welding Galvanized Coated Steel
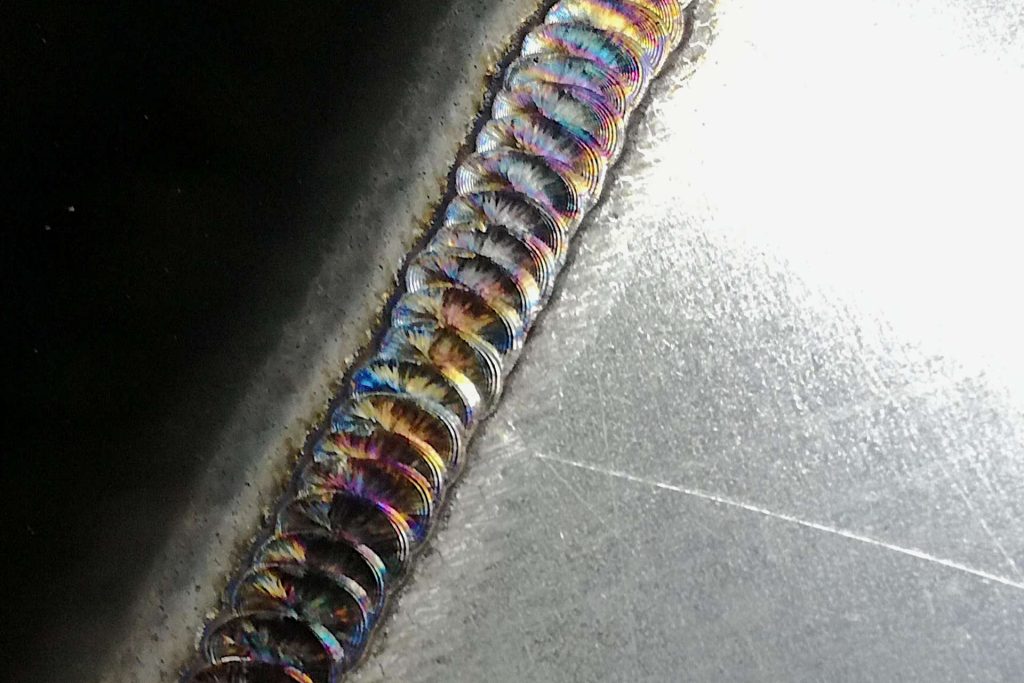
Choosing the right welding process for galvanized steel is critical. The zinc coating, while beneficial for corrosion resistance, introduces complexities in welding. Let’s explore the welding methods best suited for this material.
TIG Welding
TIG (Tungsten Inert Gas) welding (GTAW), known for its precision, is a good choice for galvanized steel, especially for thinner materials. TIG allows for controlled heat input, minimizing the burning away of zinc and reducing the risk of zinc oxide fumes. However, it requires a higher skill level and is slower compared to other methods.
MIG Welding
MIG (Metal Inert Gas) welding (GMAW) is versatile and faster. MIG can be used in two forms:
- Standard MIG Welding: Suitable for thicker galvanized steel. However, it can lead to higher zinc fume production.
- Flux Core MIG Welding: When welding galvanized steel with flux core method there you can avoid using external shielding gas and is effective in outdoor conditions. It’s more forgiving on thicker coatings of zinc.
Stick Welding
Stick welding (SMAW) is less commonly used for galvanized steel due to its higher heat input, which can burn off more zinc and produce greater amounts of fumes. Stick welding galvanized is best reserved for situations where other methods are not feasible.
Welding Process | Suitability for Galvanized Steel | Considerations |
---|---|---|
TIG | High | Precision, good for thin materials, less fumes |
MIG (Standard) | Moderate | Versatile, faster, more fumes |
MIG (Flux Core) | Good | Effective outdoors, less precision required |
Stick | Low | Higher heat input, more fumes |
When selecting a process, consider factors like the thickness of the steel, the environment you’ll be welding in, and your expertise with each method. By choosing the appropriate technique, you can minimize challenges and produce strong, reliable welds on galvanized steel.
Preparation for Welding Galvanized Steel
Proper preparation is key to successful welding, especially when dealing with galvanized steel. A common question arises: Do you need to remove galvanizing before welding? The short answer is yes, especially in the weld area, to ensure a strong and clean weld. Let’s break down the steps you need to take.
Cleaning and Surface Preparation Before Welding Process
- Remove Zinc Coating: It’s crucial to grind away the zinc coating in the area to be welded. This prevents zinc contamination in the weld pool, which can lead to porosity and weak welds.
- Tools: Use a grinding wheel, flap disc, or a file to remove the coating.
- Extent: Grind back to at least 1-2 inches around the welding area.
- Surface Cleaning: After removing the zinc coating, clean the bare steel to remove any remaining debris or residues.
- Tools: A wire brush, sandpaper, or a grinder works well for this.
- Solvents: Follow up with a solvent or degreaser to remove any oils or contaminants.
Chemical Removal of Galvanized Coating
Removing the galvanized coating from steel, particularly before welding, can also be achieved through chemical means. This method is often used when mechanical methods like grinding aren’t suitable. Let’s explore the use of various chemicals for this purpose:
Muriatic Acid
Muriatic acid, also known as hydrochloric acid, is effective in stripping zinc coatings. However, it must be handled with extreme care due to its corrosive nature.
- Safety Precautions: Wear protective gloves, goggles, and a respirator. Work in a well-ventilated area.
- Application: Dilute the acid with water (typically a 1:10 ratio of acid to water). Submerge the steel item in the solution until the bubbling stops, indicating the zinc has been removed.
- Neutralization: After removal, neutralize the acid with a baking soda solution and rinse the steel thoroughly with water.
Other Chemicals
Several commercial products are available for removing galvanized coatings. These are usually less aggressive than muriatic acid and are designed specifically for this purpose.
- Usage: Follow the manufacturer’s instructions for application, safety precautions, and disposal.
- Advantages: Often less hazardous and easier to use than muriatic acid.
Homemade Solution Using Vinegar
For a more accessible and less hazardous option, white vinegar can be used. It’s slower acting but safer for general use.
- Application: Soak a cloth in white vinegar and wrap it around the galvanized area. Alternatively, submerge small items in a container filled with vinegar.
- Duration: Leave it for several hours or overnight, depending on the thickness of the coating.
- Cleaning: After the coating has loosened or dissolved, clean the steel with a brush and rinse with water.
Each of these methods has its own pros and cons. Muriatic acid is fast-acting but hazardous, commercial removers are safer but may be costlier, and vinegar is safe and economical but slower. Your choice should be guided by the specific requirements of your project and your ability to handle these chemicals safely.
Removal of Oil or Grease from the Surface
- Degreasing: Apply a degreaser or oil-cutting cleaner to break down any surface oil or grease.
- Application: Use a clean cloth or spray to apply the degreaser.
- Scrubbing: A scrub brush or sponge can help in removing stubborn residues.
- Rinsing: Rinse the area thoroughly with warm water to remove any traces of the cleaner.
- Drying: Ensure the surface is completely dry before proceeding with welding.
Step | Action Required | Tools/Solvents |
---|---|---|
Zinc Coating Removal | Grind away zinc coating in weld area | Grinding wheel, flap disc |
Surface Cleaning | Clean bare steel surface | Wire brush, sandpaper |
Degreasing | Apply degreaser to remove oil/grease | Degreaser, scrub brush |
Rinsing | Rinse with warm water | – |
Drying | Dry the surface thoroughly | – |
If you spend the time properly preparing the galvanized steel before welding, you will ensure not only the quality of your welds but also your safety. The step-by-step approach we have just outlined should help you tackle the challenges of welding galvanized steel with confidence that you will achieve good strong welds free from contamination.
Health Risks Associated with Welding Galvanized Steel
Having looked at the preparation and possible welding process that can be used for welding galvanized steel we have to also consider additional health risks that arise from welding zinc coated material.
Welding galvanized steel requires an awareness of the health risks involved, particularly regarding the toxic fumes produced during the process.1 Understanding these risks and adopting appropriate safety measures is crucial for your health and well-being.
Toxic Fumes Emitted During Welding Process
When you weld galvanized steel, the heat causes the zinc coating to vaporize, releasing zinc oxide fumes. These fumes can pose significant health hazards.
- Effects of Inhalation: Breathing in zinc oxide fumes can lead to metal fume fever, a condition with flu-like symptoms such as fever, chills, nausea, and headache.
- Mitigation Methods: To reduce exposure, use proper ventilation, personal breathing filters, and powered air purifying systems.
Health Risks for Welding Personnel Exposed to Zinc Oxide Fumes
Exposure to zinc oxide fumes can have both immediate and long-term health effects.
- Symptoms of Metal Fume Fever: This includes coughing, fatigue, muscle aches, and fever, usually appearing several hours after exposure.
- Long-Term Effects: Prolonged exposure to high concentrations can lead to more serious conditions, including respiratory issues.
Health Risk | Symptoms/Effects | Preventive Measures |
---|---|---|
Inhalation of Zinc Oxide Fumes | Metal fume fever, respiratory issues | Proper ventilation, respirators |
Long-Term Exposure | Chronic respiratory problems | Regular health checks, safety protocols |
Safety Precautions and Personal Protective Equipment (PPE)
To safeguard against these risks, specific safety measures and PPE are recommended:
- Proper Ventilation: Essential to dilute and remove harmful fumes from the workspace.
- Systems: Local exhaust ventilation, fume extraction systems.
- Respiratory Protection: Use of appropriate respirators to filter out harmful particles.
- Types: Half-face mask cartridge filters, powered air purifying respirators (PAPRs).
- Regular Health Monitoring: Routine checks for any symptoms of metal fume fever or long-term respiratory issues.
Appreciating these health risks and adopting the right safety practices, will allow you to weld galvanized steel more safely and effectively. Remember, your health is as important as the quality of your welds.
Commonly Asked Questions
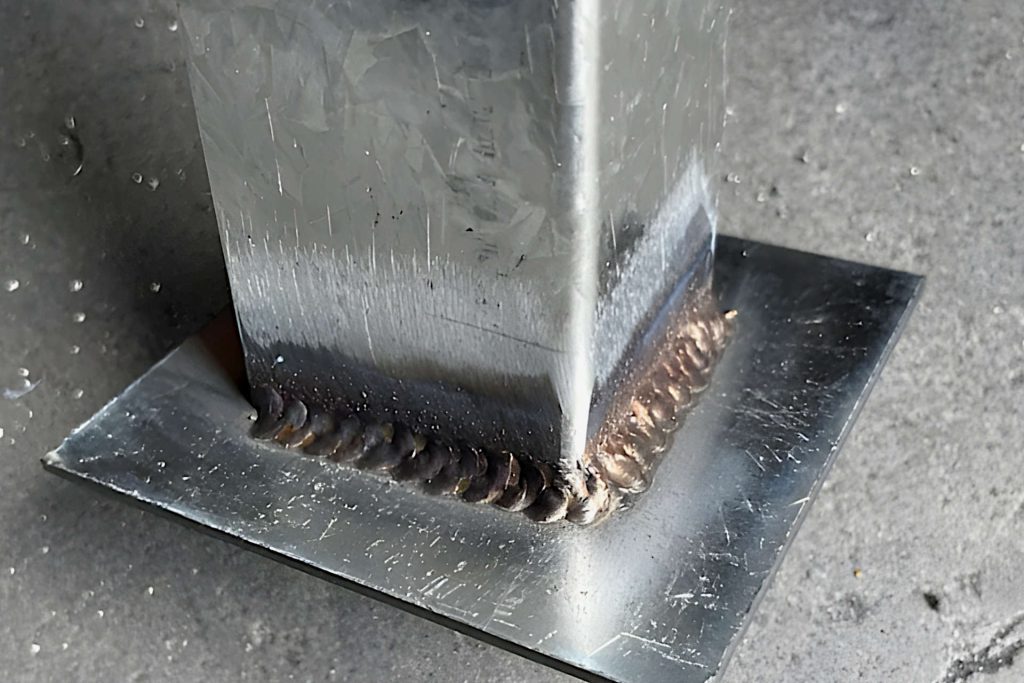
Can Welding Galvanized Steel Be Done Safely Indoors?
Yes, but with caution. Indoor welding of galvanized steel requires excellent ventilation to avoid the build-up of toxic fumes. Use local exhaust ventilation at the source and ensure the workspace is well-ventilated. Additionally, wearing appropriate respiratory protection is crucial.
What Are the Signs of a Good Weld on Galvanized Steel?
A good weld on galvanized steel should exhibit uniform penetration, consistent bead profile, and minimal spatter. It should be free from defects like porosity, cracks, or undercutting. The absence of excessive zinc oxide residues around the weld area also indicates proper technique was used.
How Does Welding Galvanized Steel Differ from Welding Regular Steel?
Welding galvanized steel differs primarily due to the zinc coating. This coating vaporizes at high temperatures, creating fumes and affecting weld quality. Special precautions like removing zinc coating in the weld area, using suitable welding techniques, and adopting enhanced safety measures are necessary.
Is There a Way to Restore Corrosion Resistance After Welding Galvanized Steel?
Yes. After welding, apply a zinc-rich paint or a galvanizing spray to the welded area. These products help restore the corrosion resistance of the material. Ensure the weld area is clean and free from contaminants before application.
How Do I Properly Dispose of or Recycle Zinc Residues and Used Protective Gear?
Dispose of zinc residues as hazardous waste according to local regulations. Used protective gear, like filters or respirators, should be discarded following the manufacturer’s guidelines and environmental standards. Never dispose of these items in general waste.
Can All Types of Galvanized Steel Be Welded Using the Same Techniques?
Not always. The welding technique may vary depending on the thickness of the zinc coating and the type of galvanized steel. Thicker coatings, often found in hot-dipped galvanized steel, require more extensive preparation and may pose greater challenges in welding compared to thinner, electroplated coatings.
Wrapping Up
As we conclude our consideration on welding galvanized steel, it’s important to emphasize that the insights and advice shared here are grounded in years of hands-on experience. Throughout my career, I’ve encountered numerous projects involving galvanized materials, each presenting its unique set of challenges and learning opportunities.
The key takeaways from our discussion should serve as a guide for both beginners and seasoned professionals:
- Preparation is Crucial: Proper preparation of the material, including the removal of the zinc coating and thorough cleaning, cannot be overstated. This step is vital for achieving strong and durable welds.
- Choose the Right Technique: Selecting the appropriate welding method based on the specifics of your project and the type of galvanized steel you’re working with can make all the difference in the quality of your welds.
- Safety First: Never underestimate the importance of safety, especially when dealing with the health risks associated with zinc oxide fumes. Adequate ventilation, the correct use of respiratory protection, and other safety measures are essential.
- Experience Counts: Finally, remember that practice and experience are invaluable. Each welding project is a learning experience, contributing to your skill and expertise, particularly when working with challenging materials like galvanized steel.
By applying these principles and continuously honing your skills, you can effectively navigate the complexities of welding galvanized steel, ensuring quality workmanship and safety in all your welding endeavors.
References
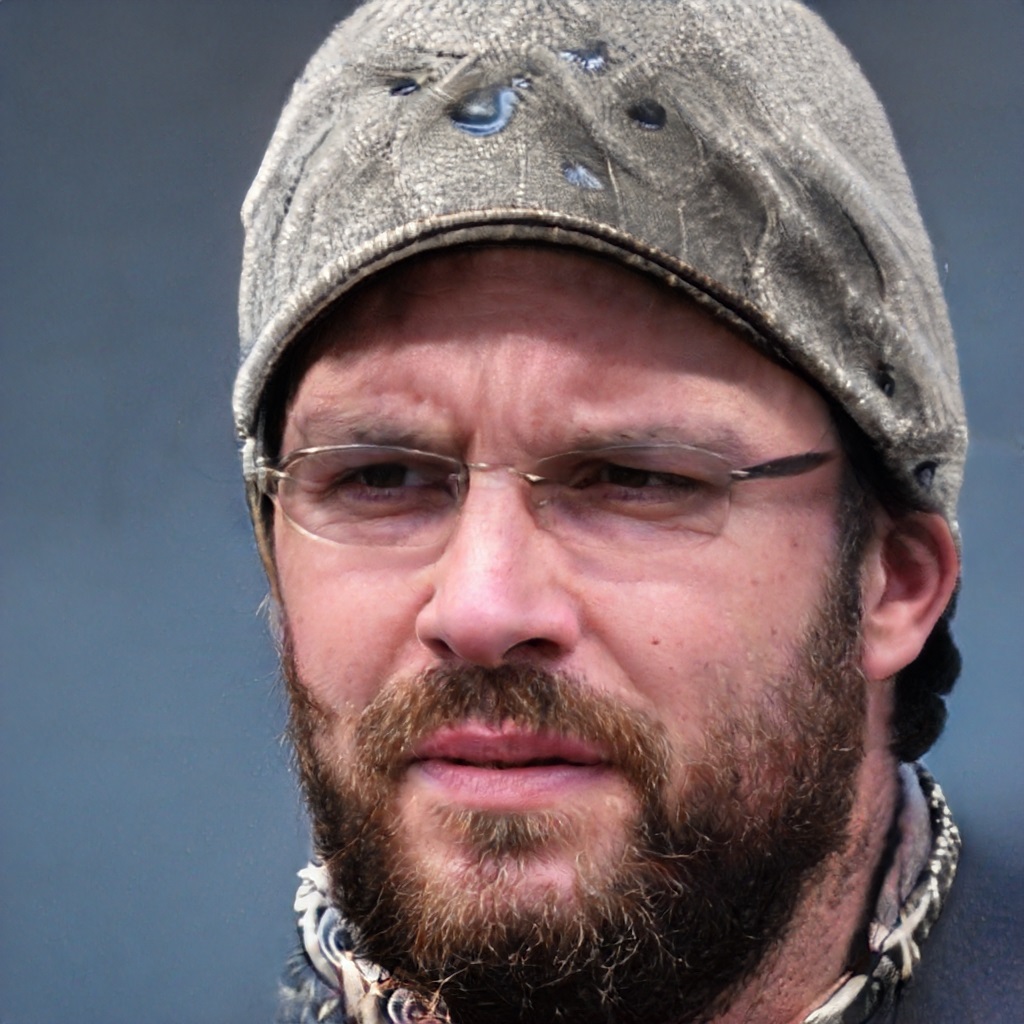
I’ve been involved in the welding industry for over twenty years. I trained in various engineering shops working on various projects from small fabrication and repairs through to industrial projects.I specialize in welding aluminum and food grade stainless steel and an now run an engineering shop fabricating equipment for the food industry.