A Comprehensive Guide to E71T-1C Flux Core Wire
americanindustrialsupl and its partners may earn a commission if you purchase a product through one of our links.
E71T-1C flux core wire is a type of welding consumable that consists of a metal tube filled with flux, which provides shielding and deoxidizing agents during the welding process. Flux core wire can be used for welding low-alloy and carbon steel in various applications, such as structural steel fabrication, shipbuilding, offshore construction, and heavy equipment repair.
One of the most commonly used flux core wires is E71T-1C, which is designed for all-position flux core welding (FCAW) applications with either pure CO2 or CO2-Argon mixed shielding gas. Generally it is a gas-shielded wire but self shielded variants are available and we shall look at the differences in terms of performance Below, we will explore the characteristics, diameter options, welding parameters, and performance of E71T-1C flux core wire in detail.
Flux Core Wire
Characteristics of E71T-1C Flux Core Wire
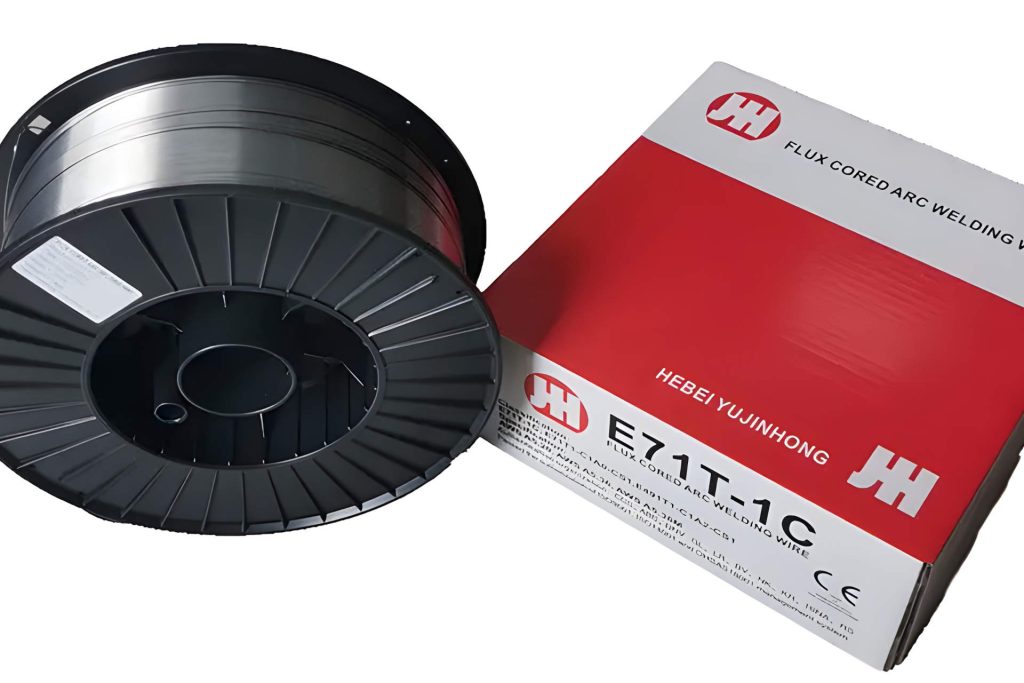
E71T-1C flux core wire has several advantages over other types of welding consumables, such as solid wire or stick electrodes. Some of the main characteristics of E71T-1C flux core wire are:
All-position Welding Capability
E71T-1C flux core wire can be used for welding in all positions, including flat, horizontal, vertical, and overhead. This is because the flux inside the wire creates a slag layer that supports the molten metal and prevents it from sagging or falling out of the weld pool. The slag also helps to protect the weld from atmospheric contamination and improves the weld quality.
Tensile Strength and Notch Toughness
E71T-1C flux core wire has a high tensile strength of 70 ksi (483 MPa) and a good notch toughness of 20 ft-lb (27 J) at -20°F (-29°C). This means that the welds made with E71T-1C flux core wire can withstand high stress and impact without cracking or breaking.
Spray Transfer and Low Spatter Loss
E71T-1C flux core wire produces a spray transfer mode, which is characterized by small droplets of molten metal that are propelled across the arc gap by the electric force. Spray transfer results in a smooth and stable arc with low spatter loss and high deposition rate. The spatter loss of E71T-1C flux core wire is typically less than 5%, which reduces the post-weld cleaning time and cost.
Bead Configuration and Slag Coverage
E71T-1C flux core wire produces a flat to slightly convex bead shape with good wetting and fusion. The bead has a uniform width and height with minimal undercutting or porosity. The slag coverage of E71T-1C flux core wire is complete and easily removable by chipping or brushing.
Suitable for Mild and High-strength Steel
E71T-1C flux core wire can be used for welding mild steel and high-strength steel with yield strength up to 80 ksi (552 MPa). The weld metal has a low hydrogen content and a good match with the base metal in terms of mechanical properties and chemical composition.
Level Wound and Deep Penetration Welding
E71T-1C flux core wire is level wound on spools or drums, which ensures smooth feeding and consistent performance. The wire has a fast freezing slag that allows deep penetration welding without burn-through or lack of fusion.
Diameter Options and Welding Parameters
E71T-1C flux core wire is available in different diameters ranging from 0.035 inch (0.9 mm) to 0.062 inch (1.6 mm). The diameter of the wire affects the current, voltage, travel speed, and stick-out length welding parameters,. The following table shows the recommended welding parameters for E71T-1C flux core wire according to the diameter and shielding gas:
Diameter | Shielding Gas | Current (A) | Voltage (V) | Travel Speed (ipm) | Stick-out Length (in) |
---|---|---|---|---|---|
0.035 | CO2 | 150 – 300 | 23 – 29 | 10 – 30 | 0.5 – 0.75 |
0.035 | CO2-Ar | 150 – 300 | 22 – 28 | 10 – 30 | 0.5 – 0.75 |
0.045 | CO2 | 200 – 400 | 24 – 32 | 10 – 35 | 0.75 – 1 |
0.045 | CO2-Ar | 200 – 400 | 23 – 31 | 10 – 35 | 0.75 – 1 |
0.052 | CO2 | 250 – 450 | 25 – 33 | 10 – 40 | 0.75 – 1 |
0.052 | CO2-Ar | 250 – 450 | 24 – 32 | 10 – 40 | 0.75 – 1 |
0.062 | CO2 | 300 – 500 | 26 – 34 | 10 – 45 | 0.75 – 1 |
0.062 | CO2-Ar | 300 – 500 | 25 – 33 | 10 – 45 | 0.75 – 1 |
Comparison Weld Between E71T-1 and ER70S-6
Difference between E71T-1C and E71T-1M Flux Core Wire
E71T-1C and E71T-1M are two variants of the same flux core wire that differ only in the type of shielding gas they are designed for. E71T-1C is compatible with either pure CO2 or CO2-Argon mixed shielding gas, while E71T-1M is compatible only with CO2-Argon mixed shielding gas. The difference between the two flux core wires lies in the following aspects:
Shielding Gas Variations
E71T-1C flux core wire can be used with pure CO2 or CO2-Argon mixed shielding gas, depending on the welding application and preference. Pure CO2 provides deeper penetration and higher deposition rate, but also generates more spatter and requires higher voltage. CO2-Argon mixed shielding gas provides smoother arc and better bead appearance, but also reduces penetration and deposition rate.
E71T-1M flux core wire can be used only with CO2-Argon mixed shielding gas, which is typically composed of 75% to 80% Argon and the rest CO2. The mixed shielding gas enhances the arc stability and reduces the spatter generation, resulting in a cleaner and more aesthetic weld.
Mechanical and Chemical Composition Requirements
E71T-1C and E71T-1M flux core wires have different mechanical and chemical composition requirements according to the American Welding Society (AWS) specifications. The following table shows the comparison between the two flux core wires:
Specification | E71T-1C | E71T-1M |
---|---|---|
AWS Classification | A5.20/A5.20M | A5.36/A5.36M |
Tensile Strength | ≥70 ksi (≥483 MPa) | ≥70 ksi (≥483 MPa) |
Yield Strength | ≥58 ksi (≥400 MPa) | ≥58 ksi (≥400 MPa) |
Elongation | ≥22% | ≥22% |
Notch Toughness | ≥20 ft-lb (≥27 J) at -20°F (-29°C) | ≥20 ft-lb (≥27 J) at -20°F (-29°C) |
Carbon Content | ≤0.12% | ≤0.12% |
Manganese Content | ≤1.75% | ≤1.75% |
Silicon Content | ≤0.90% | ≤0.90% |
Nickel Content | ≤0.50% | ≤0.50% |
Chromium Content | ≤0.20% | ≤0.20% |
Molybdenum Content | ≤0.30% | ≤0.30% |
Vanadium Content | ≤0.08% | ≤0.08% |
Recommended Shielding Gases
The choice of shielding gas for E71T-1C and E71T-1M flux core wires depends on the welding application, performance, and cost factors. The following are some of the recommended shielding gases for each flux core wire:
E71T-1C Shielding Gas
E71T-1C flux core wire can be used with either 100% CO2 or CO2-Argon mixed shielding gas. The choice of shielding gas depends on the application, cost, and availability.
100% CO2 is cheaper and more readily available than mixed gas. It also provides deeper weld penetration and higher deposition rates. However, it also generates more spatter, which requires more cleaning time and consumables. It also produces a harsher arc that may cause more wear on the contact tip and nozzle.
CO2-Argon mixed gas is more expensive and less available than pure CO2. It provides a smoother arc, less spatter, better bead appearance, and less cleaning time. It also reduces the wear on the contact tip and nozzle. However, it also reduces the weld penetration and deposition rates.
The common ratios of CO2-Argon mixed gas for E71T-1C are 75% CO2 / 25% Argon or 80% CO2 / 20% Argon. The higher the percentage of Argon, the smoother the arc and the less spatter.
E71T-1M Shielding Gas
E71T-1M flux core wire is similar to E71T-1C but requires a mixed shielding gas of CO2 and Argon. It cannot be used with 100% CO2 because it may cause porosity and cracking in the weld.
The common ratio of CO2-Argon mixed gas for E71T-1M is 75% CO2 / 25% Argon. This ratio provides a balance between weld penetration, spatter, bead appearance, and arc stability.
Welding Performance with Different Shielding Gases
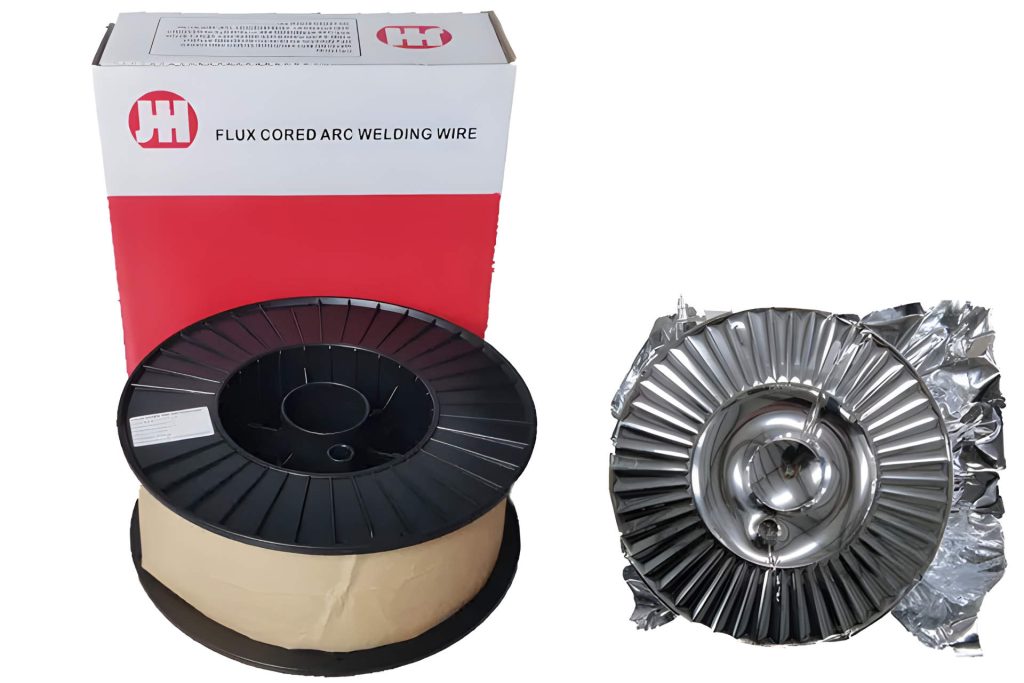
E71T-1C Performance
E71T-1C flux core wire has a good welding performance with both pure CO2 and CO2-Argon mixed gas. However, there are some differences in the weld characteristics depending on the shielding gas used.
With pure CO2, E71T-1C produces deeper weld penetration and higher deposition rates than with mixed gas. This is beneficial for welding thicker materials or filling gaps. However, it also generates more spatter, which requires more cleaning time and consumables. It also produces a harsher arc that may cause more wear on the contact tip and nozzle.
With CO2-Argon mixed gas, E71T-1C produces a smoother arc, less spatter, better bead appearance, and less cleaning time than with pure CO2. This is beneficial for welding thinner materials or improving the weld quality. However, it also reduces the weld penetration and deposition rates than with pure CO2. This may require more passes or higher currents to achieve the desired weld strength.
E71T-1M Performance
E71T-1M flux core wire has a specific welding performance with mixed shielding gas of CO2 and Argon. It cannot be used with pure CO2 because it may cause porosity and cracking in the weld.
With mixed gas of 75% CO2 / 25% Argon, E71T-1M produces a smooth arc, low spatter, good bead appearance, and high arc stability. It also provides good weld penetration and deposition rates for various steel gauges. It is suitable for all-position welding of carbon steel, mild steel, and low alloy steel materials.
Flux Core Wire
Effect of Pure CO2 on Weld Penetration and Spatter
E71T-1C Weld Penetration and Spatter
E71T-1C flux core wire can be used with pure CO2 as a shielding gas to achieve increased weld penetration and deposition rates. This is because pure CO2 provides more heat input to the weld pool than mixed gas.
However, pure CO2 also generates more spatter than mixed gas because of its higher ionization potential and lower thermal conductivity. Spatter is the molten metal that is ejected from the weld pool and solidifies on the base metal or the welding equipment. Spatter can affect the weld quality, appearance, and efficiency.
Spatter can be reduced by adjusting the welding parameters, such as current, voltage, wire feed speed, and stick-out. It can also be reduced by using anti-spatter agents or sprays on the base metal or the nozzle. However, spatter still requires more cleaning time and consumables than mixed gas.
E71T-1M Weld Penetration and Spatter
E71T-1M flux core wire cannot be used with pure CO2 as a shielding gas because it may cause porosity and cracking in the weld. This is because pure CO2 provides too much heat input to the weld pool and causes excessive hydrogen diffusion.
Porosity is the presence of gas pockets or bubbles in the weld metal that reduce its strength and ductility. Cracking is the formation of cracks in the weld metal or the heat-affected zone that reduce its integrity and durability.
E71T-1M flux core wire requires a mixed shielding gas of CO2 and Argon to achieve a balanced heat input and hydrogen control. However, not all mixed gases are suitable for E71T-1M. For example, an 88% Argon / 12% CO2 mix may cause lack of fusion and undercutting in the weld because of its low heat input and arc force.
Recommended Welding Positions
E71T-1C Welding Positions
E71T-1C flux core wire is suitable for all-position welding, which means it can be used for welding in flat, horizontal, vertical, and overhead positions. This is because E71T-1C has a rutile coating that provides good slag coverage and detachability.
Slag is the solidified flux that forms on top of the weld metal and protects it from atmospheric contamination. Slag coverage and detachability are important for all-position welding because they affect the weld quality and efficiency.
Slag coverage refers to how well the slag covers the weld metal and prevents oxidation and porosity. Slag detachability refers to how easily the slag can be removed from the weld metal after welding. Good slag coverage and detachability reduce the cleaning time and consumables.
E71T-1M Welding Positions
E71T-1M flux core wire is also suitable for all-position welding, which means it can be used for welding in flat, horizontal, vertical, and overhead positions. This is because E71T-1M has a similar rutile coating as E71T-1C that provides good slag coverage and detachability.
However, E71T-1M has some specific performance considerations for all-position welding because of its mixed shielding gas requirement. For example, E71T-1M may produce more spatter than E71T-1C when welding in vertical or overhead positions because of its higher arc force. It may also require more skill and technique to control the weld pool and avoid sagging or dripping.
Advantages and Disadvantages of Using Self-Shielded vs Gas-Shielded E71T-1 C Flux Core Wire
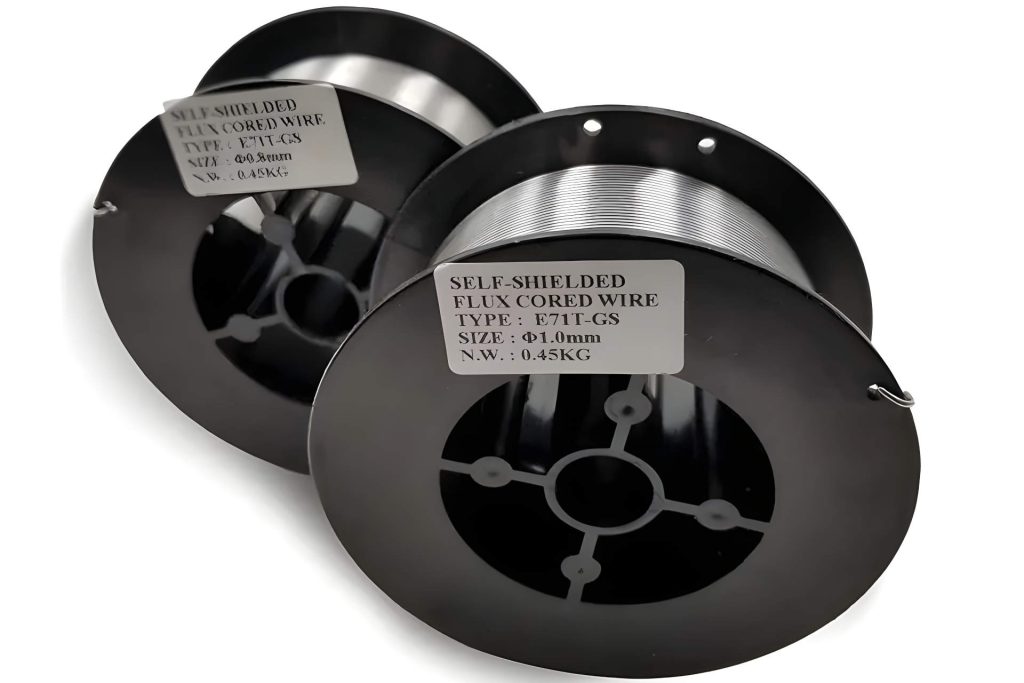
Advantages of using self-shielded E71T-1C flux core wire:
- Highly portable and ideal for outdoor welding applications, such as structural steel, shipbuilding, and bridge construction.
- Does not require an external shielding gas supply, making it more easily carried about.
- Can be used in windy conditions where gas shielding may be difficult.
- Can be used in areas where access is limited, such as inside pipes.
- Can be used on dirty or rusty materials.
Disadvantages of using self-shielded E71T-1C flux core wire:
- May produce more spatter and a less stable arc compared to gas-shielded wire.
- May require more cleanup after welding due to the slag produced during welding.
- May not provide as good arc quality and penetration as gas-shielded wire.
Advantages of using gas-shielded E71T-1C flux core wire:
- Provides good arc quality and lower spatter levels compared to self-shielded wire.
- Provides good penetration.
- Can be used for all-position welding.
- Can be used for flat and horizontal applications.
Disadvantages of using gas-shielded E71T-1C flux core wire:
- Requires an external shielding gas supply, which can be more difficult to carry around and set up.
- May not be as ideal for outdoor welding applications due to the need for shielding gas.
- May not be as ideal for use in windy conditions where gas shielding may be difficult.
- May not be as ideal for use in areas where access is limited, such as inside pipes.
Both self-shielded and gas-shielded E71T-1C flux core wire have advantages and disadvantages. Self-shielded wire is highly portable and can be used in dirty or rusty materials, but may produce more spatter and require more cleanup. Gas-shielded wire provides good arc quality and penetration, but requires an external shielding gas supply and may not be as ideal for outdoor welding applications or areas with limited access.
Final Thoughts
We have covered the most important consideration when looking to use to E71T-1M or E71T-1C as the most suitable flux core wire for a welding application and discussed its characteristics, such as tensile strength, impact toughness, and weldability, as well as its available diameters, ranging from 0.8 mm to 2.4 mm. We have also looked at the recommended welding parameters for different wire sizes and positions, and how to adjust them according to the base metal thickness and joint design. Moreover, we have compared E71T-1C with E71T-1M, a variant of the E71T-1C flux core wire, and highlighted their similarities and differences in terms of chemical composition, shielding gas requirements, and mechanical properties.
Unless using self -shielding variety, one of the most important aspects of using E71T-1C flux core wire is selecting the appropriate shielding gas and understanding its impact on welding performance. As we have shown, different gas mixtures can affect the arc stability, spatter generation, penetration depth, bead shape, and slag removal of the welds. Generally speaking, higher CO2 content results in deeper penetration and higher deposition rates, but also more spatter and slag. On the other hand, higher Ar content produces smoother and cleaner welds, but also lower penetration and deposition rates. Therefore, the choice of shielding gas depends on the specific welding conditions and quality requirements of each application.
Wrap Up: E71T-1 C Flux Core Wire and E71T-1 M Flux Core Wire
Both E71T-1C and E71T-1M flux core wires are versatile consumables that can be used for all-position welding of mild and low-alloy steels. They offer high productivity, excellent mechanical properties, and good crack resistance. However, they also have some limitations, such as sensitivity to moisture absorption, high fume emission, and limited applicability for out-of-position welding with larger wire diameters. Therefore, proper storage, handling, and welding practices are essential to ensure optimal results with these wires.
Flux Core Wire
Resources
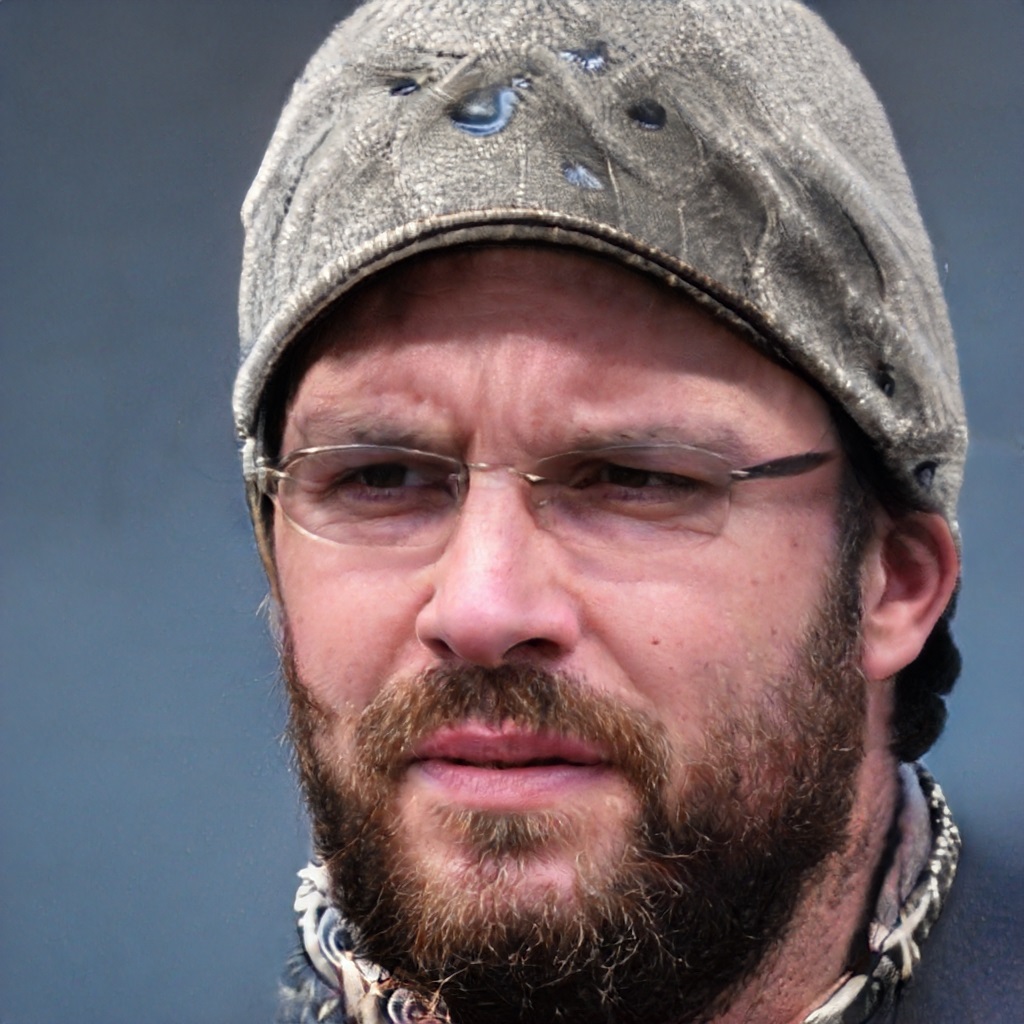
I’ve been involved in the welding industry for over twenty years. I trained in various engineering shops working on various projects from small fabrication and repairs through to industrial projects.I specialize in welding aluminum and food grade stainless steel and an now run an engineering shop fabricating equipment for the food industry.